Digitalization driving the development of remote services
In recent years, advances in connectivity, big data and digitalization have often promised to bring significant benefits to industry. Now, with the Valmet Industrial Internet, we are using data to deliver a better kind of maintenance service, as well as performance optimization services.
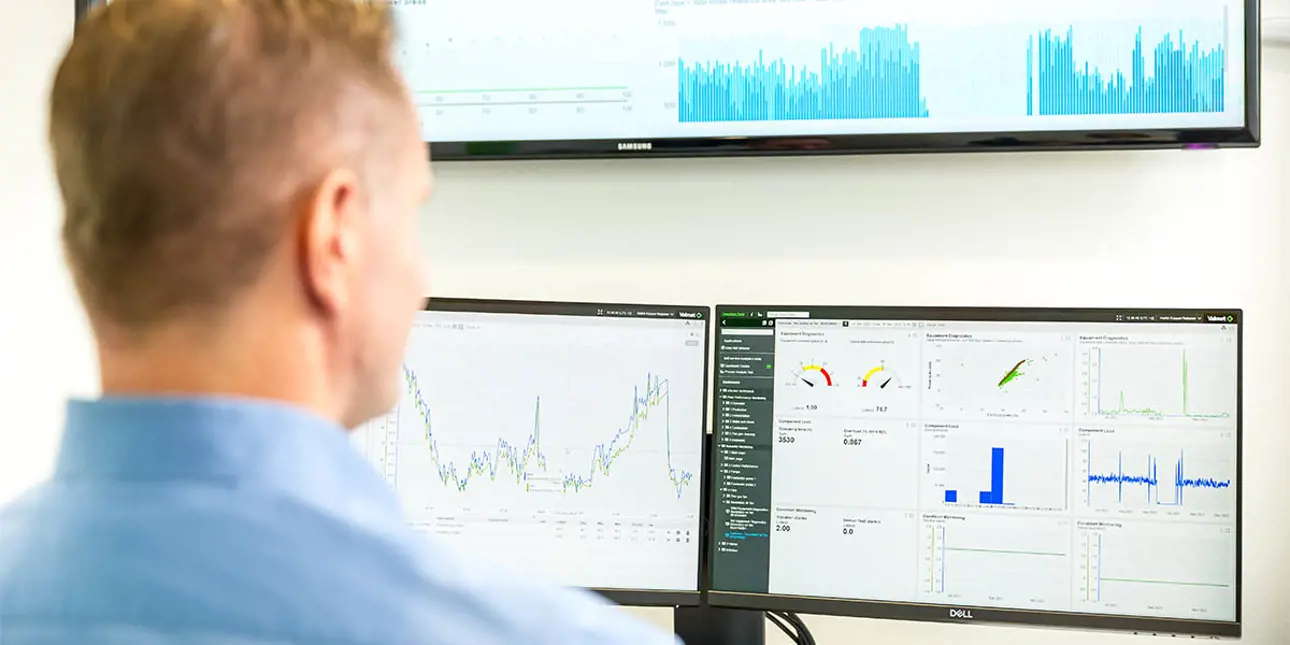
Mika Kari, Global Technology Manager, Valmet Industrial Internet, Board, Paper and Tissue Solutions, Services Business Line, tells us more. "With the Valmet Industrial Internet (VII), we can offer new types of remote monitoring and optimization services. This is something we can offer globally. We can gather data from the customer’s site and, using our expertise and analytics, we can turn that data into value. It’s a dialogue with data."
Approaching data with the spirit of expertise
Kari emphasizes that data by itself isn’t enough. Expertise in the production processes and installed equipment is essential.
"We have developed an advanced digitalization offering that enables us to efficiently and effectively utilize data gathered from installed equipment, which we then use to benefit our customers’ processes and businesses," Kari says. "Key elements of the VII include Industrial Internet applications, Valmet Performance Center, the Valmet Customer Portal, Intelligent machines and Automation, and a solution ecosystem with leading industry players. It’s important to note that the VII isn’t just about the technology – it’s the combination of human expertise and data analytics that provides the value. Our remote services always include remote support from Valmet Performance Center, which is our network of industry and data experts. These are Valmet’s own people and they have a deep understanding of machinery, processes and automation."
Valmet has an extensive range of VII solutions and applications for maintenance and optimization.
A better way to serve customers
"Because so much data is available, the trend is now to move from big data to smart data," says Kari. "There is always a cost for data, so you need to focus on what’s relevant. Unnecessary data isn’t worth collecting. That’s why Valmet has developed an extensive range of VII maintenance solutions and applications that are targeted at specific aspects of operations, including optimizing and maintaining production capacity, paper quality, energy efficiency and reliability."
Mika Kari, Global Technology Manager, Valmet Industrial Internet, Board, Paper and Tissue Solutions, Services Business Line.
"In practice, when we provide remote maintenance services, what happens is that we securely gather and analyze real-time data with Valmet Performance Center service. Our applications monitor the results constantly for deviations and, if they detect anything, they send an alarm to our Valmet Performance Center team. The team will then do a deeper analysis, diagnose the issue and identify best options for resolving it. Then they will get in touch with the customer. We have real people – real experts – to help them out."
Big benefits from remote maintenance
During the pandemic, when international travel was nearly impossible, Valmet was still able support customers around the world, resolving maintenance issues and even participating in startups. All through remote connections.
"Remote monitoring and diagnostics enable us to prevent waste,” says Kari. “Whether it’s wasted money, travel, time, energy, raw materials, natural resources or emissions. For example, problems in production can lead to poor performance. Now, with continuous monitoring, we can detect issues ahead of time and alert the customer. This kind of proactive, preventive maintenance prevents the issue from developing and helps avoid waste throughout the value chain."
"Because we can provide services remotely, we can also respond faster. The relevant expertise is always available through Valmet Performance Center, so we don’t need to send an expert to the customer’s site and the customer doesn’t need to wait."
New capabilities turn data into value
As digitalization is increasingly being accepted across industries, it’s pushing the development of maintenance forwards. "Valmet Industrial Internet gives us the capability to gather data from individual process areas or even from a whole plant," says Kari. "For example, our offering includes Valmet Machine Diagnostics, to monitor and optimize the performance of an entire paper, board or tissue line. We also have a Valmet Winder Diagnostics service, which specifically focuses on the winder section."
"Our Valmet Performance Center team can do optimization for a wide variety of process applications," says Kari, "and we can develop VII applications to meet customer’s specific needs. When we analyze data in the right way, then we can get insights that enable data-driven decisions. For example, we can determine whether a deviation is a chronic problem or a random incident. If we can identify the root cause, then you don’t have to fix the same thing repeatedly. We can also use data to support our customers’ investment decisions and recommend technical improvements. We’re turning data into value for our customers’ businesses."
Making real progress with maintenance
"The work we have put into developing these remote maintenance services is part of Valmet’s Beyond Circularity R&D program and ecosystem, which is a four-year program that’s partly funded by Business Finland," adds Kari. "So far, our customers have appreciated our ability to help them quickly and remotely, and we’ve been introducing remote training, which will become more important with younger generations. Valmet attended Technology Fair 2023 in Helsinki, Finland, where we won the Finnish Maintenance Society's innovation prize for our success with Valmet Industrial Internet, Remote Monitoring and Optimization. We are delighted with this! It shows that we’re really making progress."
Related articles