4-steps to resource efficiency: Quantify and discover the improvement potential for optimizing your production process
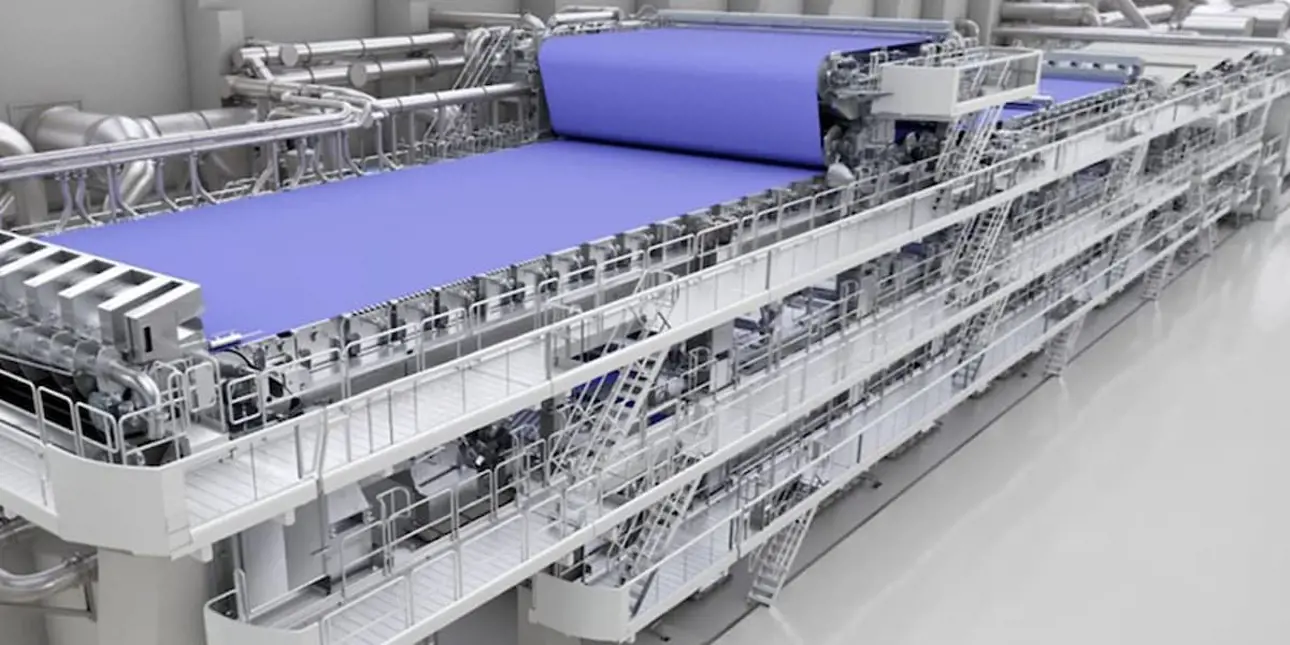
In our previous article about energy efficiency, we determined four steps with which our customers can improve their production line’s energy use. After completing benchmarking, the first of the four steps (see Figure 1 below), we have determined with the customer where their mill currently sits in terms of resource efficiency compared to the customer’s other mills or competitors. Let’s broaden those 4-steps to cover other resources besides just energy, as savings in water and raw materials or improvements in time and material efficiency all lead to better resource efficiency.
Figure 1. The 4-steps toward improved resource efficiency.
The 4-steps toward improved resource efficiency
1. The first step on this route is a specific benchmarking, Benchmarking provides you with goalsetting data for the next steps.
2. The second step is quantifying variabilities, which means identifying the variations of your entire production line. This enables you to discover the peak resource consumption sources, detailed improvement scope and potential.
3. The third step, optimization, offers tools for reducing variations and improving resource efficiency within the scope determined in the previous step.
4. The fourth and final step is investing in new technologies. Following these steps to resource efficiency, opens a new insight into new technology, revealing what you really need – and when.
These 4-steps provide you with a continuous development roadmap, from knowing where you are, what you can improve and how much, and by which actions. Improvement actions target the most crucial process sections to save energy, water and raw materials, improve the mill’s runnability and availability, and develop time and material efficiencies – all of which lead to better operational sustainability.
Deep dive into the mill’s resource efficiency
Specific benchmarking gave us a narrow sample of the customer’s current production status. With quantifying, it’s time to take a deeper dive into the production process and analyze the main current issues with the mill’s resource efficiency, and how they can be tackled and improved. This means determining the operating window around which the customer is currently hovering and evaluating the individual production sub-processes against resource efficiency.
This quantifying analysis is completely tailor-made according to the customer’s needs and own ideas. “Every board and paper mill is its own production line’s best expert” is what we determined in our previous article, and that hasn’t changed. It’s essential to include the customer in these next steps and determine the analysis focus and scope together.
Valmet’s modern state-of-the-art digital tools such as advanced data analytics fit extremely well into this quantifying process. They can play a major role when visualizing and specifying the key characteristics of the customer’s production process and highlighting its scope for improvement. Illustrative production and process data visualizations based on these digital tools are also very useful methods when justifying the quantifying process’s results.
The final deep-dive analysis scope can include stock preparation, the forming and press section, and vacuum, air, and steam and condensate systems. Alternatively, it can include the complete mill if clear focus areas are not identified, or if everything needs equal attention. Valmet’s expertise and analysis solution offering covers all our customers’ production processes.
Ways to find improvement potential
It is possible to evaluate resource efficiency during this deeper analysis with both remote and on-site work, depending for example on the customer’s instrumentation and data collection level and remote connectivity opportunities. From the scoped process sections, Valmet’s experts will find improvement actions by:
- Comparing current resource use with Valmet’s professional and accurate dimensioning and simulation tools.
- Evaluating the current instrumentation, automation and data collection levels and their potential for improvement.
- Auditing current operating efficiency and condition with onsite measurements and spe-cialist analysis.
- Assessing currently used resource efficiency KPIs, their relevance, follow-up and im-pact.
- Examining the status of production personnel’s expertise and understanding how their work affects resource efficiency.
Based on Valmet’s comprehensive quantifying analysis, the potential for improvement and rec-ommendations are found and presented to the customer with clear explanations and savings calculations. The target is to find actions, from simple process optimization (low-hanging fruit) all the way to medium-sized and larger process modifications and investment suggestions using the latest Valmet resource-efficient technologies.
- Low-hanging fruit can for instance be simple process parameter changes that can be completed immediately without additional resources, money or time.
- Medium-sized actions can for instance be process connection modifications, equipment mainte-nance services and overhauls, and small equipment modernizations. These actions take some additional resources, time and money.
- Finally, investments are the tools for the customer to get the absolute maximum resource efficiency from their production line. For example, completely new technology installa-tions, old equipment modernizations and rebuild concepts can be designed and evaluat-ed with the customer to support these investment decisions.
When improving resource efficiency, payback times tend to be very attractive. A typical annual saving potential, depending on the production capacity and unit costs, can be:
As these things are linked. For example, we need to consider that when reducing water use, savings can be created from
- A reduced need for pumping
- A reduced need for heating
- A reduced need for process water biocide treatment
- A reduced need for wastewater treatment
- A reduced risk of water scarcity production issues in some areas
- A reduced risk of environmental legislation related production issues in some areas
- A reduced risk of sustainability-related reputational issues
A development roadmap defines the optimization steps
After we have quantified the process and discovered its potential for improvement, it’s time to optimize it.
All the discovered improvement actions need careful evaluation of whether their implementation is feasible and in which order they should be done: In the paper and board making process - everything affects everything. A development roadmap can be used to set all the actions in the correct order and remind us what is done and when. This ensures that the highest improvement potential is utilized first, and that improvement actions won’t conflict with each other. It should also be remembered that resource efficiency development isn’t just a one-off project but a continuous improvement process that needs to be reviewed and iterated again and again.
Valmet’s service agreements, underlying digital tools and optimizers are the key service elements in executing these optimizations. All this is supported remotely by Valmet’s Performance Center (VPC) to ensure smooth implementation of all improvement actions. These key elements are easy to tailor according to individual customer needs and are made to be just fit for purpose.
All this is part of Valmet’s everyday work with proven success, various reference cases and satisfied customer stories. We are committed to moving our customers’ performance forward together and bringing this continuous development into real-life actions to improve paper and board making resource efficiency and sustainability.