Wash press upgrade leads to improved performance at Navigator Aveiro pulp mill
Operating a pulp mill at its maximum capacity requires continuous work. At Navigator Aveiro mill, it is regularly discussed how to optimize the process and the equipment further. One of the latest improvements is a wash press upgrade, that quickly after the start up led to improved consistency and lower Chemical Oxygen Demand (COD) in the washing line.
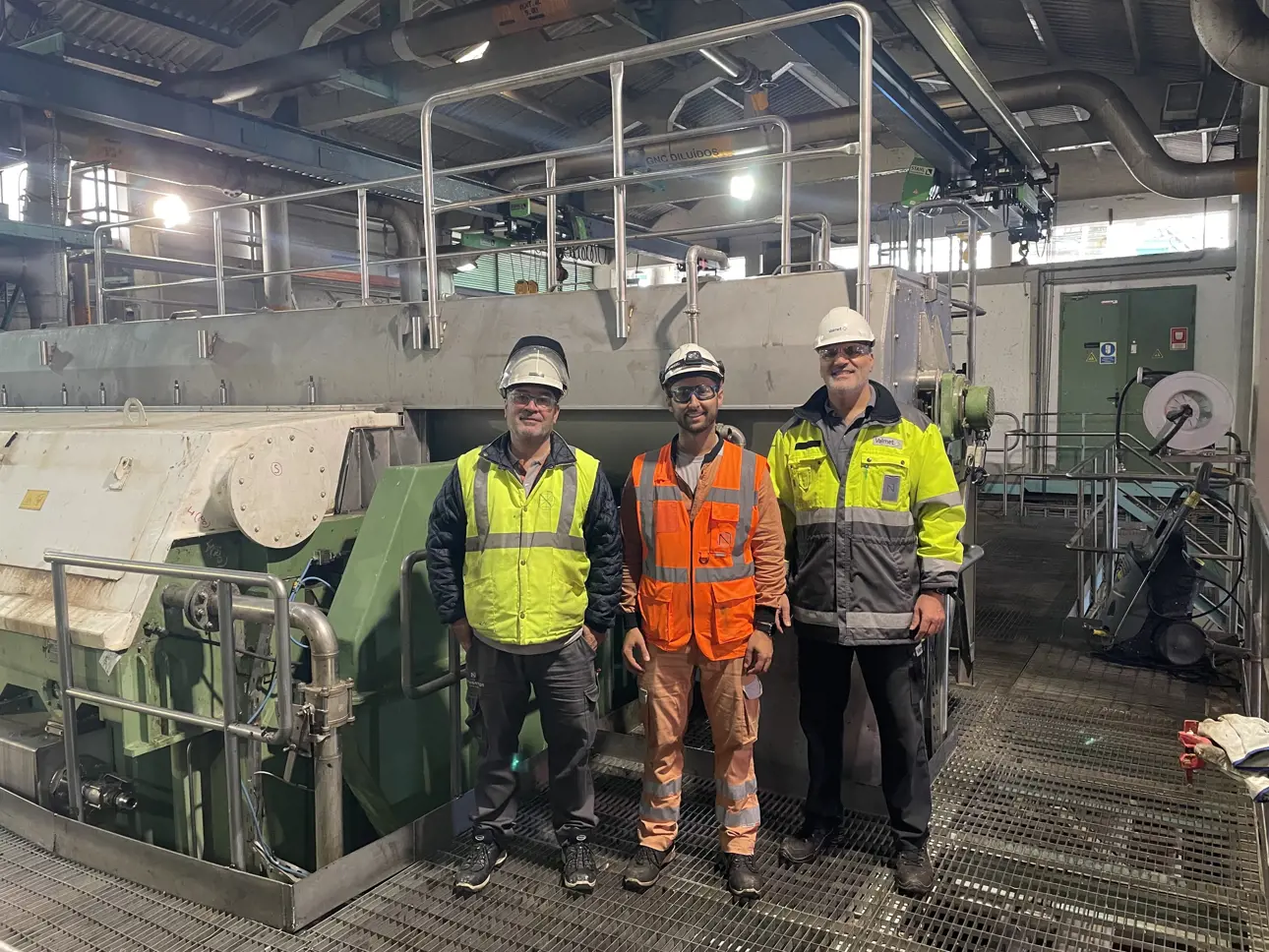
From left to right: Rui Pedro ( Production Manager), Tiago Teixeira (Project Responsible), Rui Vinhas (Valmet Mill Sales Manager)
Navigator Aveiro pulp mill is located in Cacia, Portugal. The mill was inaugurated in 1953, and four years later in 1957 it achieved a major breakthrough as it was the first mill in the world to produce high-quality kraft pulp from eucalyptus. Valmet is the original equipment manufacturer of several process islands at the Aveiro mill, and over the years the companies’ relationship has developed into a mutually valued partnership.
Continuous development through process optimizing and investments
Some of the equipment at the Aveiro mill dates back to the 1950’s, but thanks to Navigator’s determination to keep up with the newest technology, numerous significant modifications have been carried out over the years.
“Life at Aveiro mill is about continuous development. We are seeking to optimize our process to reach the maximum capacity of the mill, and naturally it also requires upgrading or replacing equipment that has reached the end of their lifecycle. By investing in modern technology, we also contribute to the safety and sustainability of our mill,” says Rui Pedro Pereira, Production Manager at Aveiro mill.
One of Navigator’s latest investments is the wash press upgrade carried out during the mill’s annual shutdown in October 2022.
“We started to have problems such as low consistency and high COD with our washing line, that also led to increased maintenance need and operational costs. After trying to solve the challenge ourselves without succeeding, we turned to our suppliers for support. Out of the several options we found Valmet’s proposal the best and decided to go for a comprehensive modification of the wash press P0,” Pereira says.
Unique second-hand solution enabled the replacement of both rolls
Valmet’s delivery included several upgrades that were installed for the first press after screen room, P0: Two new rolls with Valmet Anti Rewet, Valmet Adjustable doctor with a new doctor beam, Valmet Air Seal L, new inlet box Valmet Inlet N, and a new Valmet HP cleaning system.
“I’m very happy for the possibility to continue our long-term co-operation with Navigator Aveiro. Modifications of this scale never come in ready-made packages from the shelf, and I appreciate the customer’s willingness to discuss also the out-of-the-box solutions,” says Rui Manuel Vinhas, Mill Sales Manager at Valmet.
“In this case, we suggested utilizing a second-hand roll to be able to replace both rolls at the same time. I’m happy the customer liked our proposal, and we were able to give new life to a roll removed from a closed mill. After a thorough refurbishment it works as new. Compared to the option of replacing just one roll at a time, the results of the modification could be seen immediately,” he continues.
Good performance leads to repeated order
The challenges Aveiro mill previously had with the washing line’s performance are now behind.
“The good performance of this press has led to an improved performance of the entire washing line. In this particular position the consistency is good and COD very low – contributing also to decreased maintenance and operational costs, which is always good”, Pereira says.
So, are you satisfied with the modification and Valmet’s work?
“Well, we are already discussing similar upgrades to the two other presses in our washing line. I guess that means we are satisfied,” he concludes.