Valmet simulators increase efficiency and reduce operations risks in Klabin Puma II
Inside of a big and complex plant as Klabin Puma unit, in Ortigueira, state of Paraná, in Brazil, every care with operation is essential. That’s why an important item to ensure safety and equipment performance, as well as the quality of training of operators are the simulators, where operators can be trained in a virtual environment.
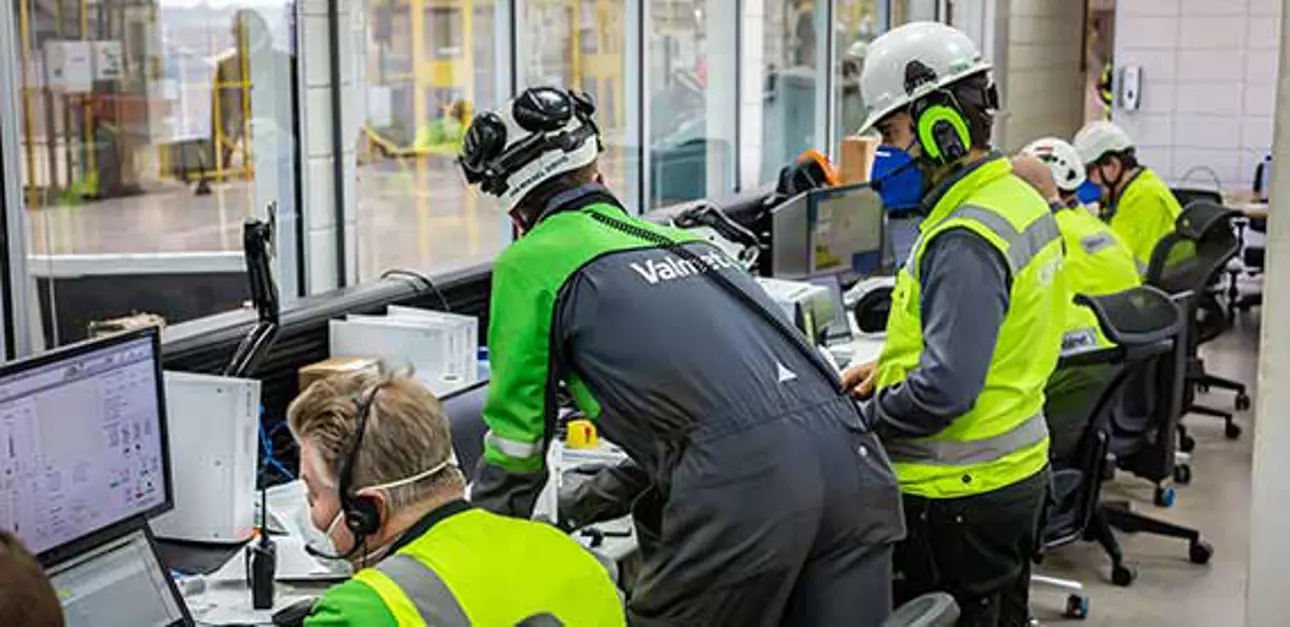
Valmet is responsible for delivering part of Klabin's Puma II project simulators. The Valmet Training Simulator is used in cooking, brown pulp washing, screening, refining areas and in the new Paper Machine 27 (PM 27). The simulators are used, at first, to carry out the tests and validation of the logics implemented in the Distributed Control System (DCS) and Advanced Process Controls (APC), a process known as joint-FAT. Then, the range (simulator and control system) is used as an essential tool in the operators' training – including approximately 170 hours of training on the simulator.
“The simulator is capable to reproduce the behavior of equipment on the plant, with all operating situations and scenarios virtually. This makes it possible to train the team of operators before the start-up of the mill or once the mill is in operation, qualifying new professionals,”, explains Rafael Ferreira, Valmet’s Sales Engineer, who coordinated the activities of this project.
“Furthermore, it is an essential tool for any production adjustments and operational experiments. Klabin will have the opportunity to innovate in its processes, simulate production situations before putting them into practice, bringing gains in productivity and efficiency,” he adds.
For Tiago Zan, Automation Engineer at Klabin, the OTS (Operator Training Simulator) represents a big step for the mill start-up and operator capabilities. “With the simulator trainings, the operators improve their performance and increase the adaptation for control system. This results in faster action and avoiding safety failures as well as quality or productivity losses. The learning curve is faster, and we further improved the training of people working in such important roles,” he points out.
The tests were done on site, at Puma II unit, and remotely, due to pandemic restrictions. “In the past, we would have the entire team working together at Puma”, says Rafael Ferreira. “In this case we had to reevaluate the plan and make adjustments, utilizing remote teams and global support.”
Valmet delivered key technology for the Klabin Puma II project
Eduardo Mai, Fiber Line Operator Leader at Klabin, said that his team could count on many expert employees, but were not familiarized with the new system. "This simulation system greatly helps the operator to create familiarity with the equipment. The Puma II simulator offers many possibilities of real situation scenarios that can happen. Here, the operator develops skills so that he can work on problems with greater agility.”
PM27: modeled process from start to the end by a simulator
The PM27 is the first paper machine in the world that has simulators from the beginning to the end of the production process in order to train and empower the operators. “Other plants do the simulation, normally, just until drying phase,” says Tiago Zan. “With this simulator developed by Valmet, we can do the whole modeling until jumbo rolls output. This is a significant gain for operators learning, who can simulate the entire paper production process," he adds.
Alan Paes, PM 27 operator leader at Klabin, assess the knowledge acquired during the simulations can help operators in day-to-day tasks when operating the system. “This helps on psychologic level, because the operator gets less nervous, since now he has knowhow and experience to deal with many different situations. He knows exactly what to expect of the machine and the better way to deal with possible variants,” he concludes.
Related articles