Valmet simulators assist effective and safe management at LD Celulose’s new pulp mill
Projected to be one of the largest dissolving pulp mills in the world, producing 500,000 tonnes of pulp per year, LD Celulose S.A. is a joint venture between Lenzing and Dexco. To ensure the equipment’s safety and performance and the quality of operator training from the outset of operations, the company relied on solutions from Valmet, the leader in technology, automation and services for the pulp, paper and energy industries.
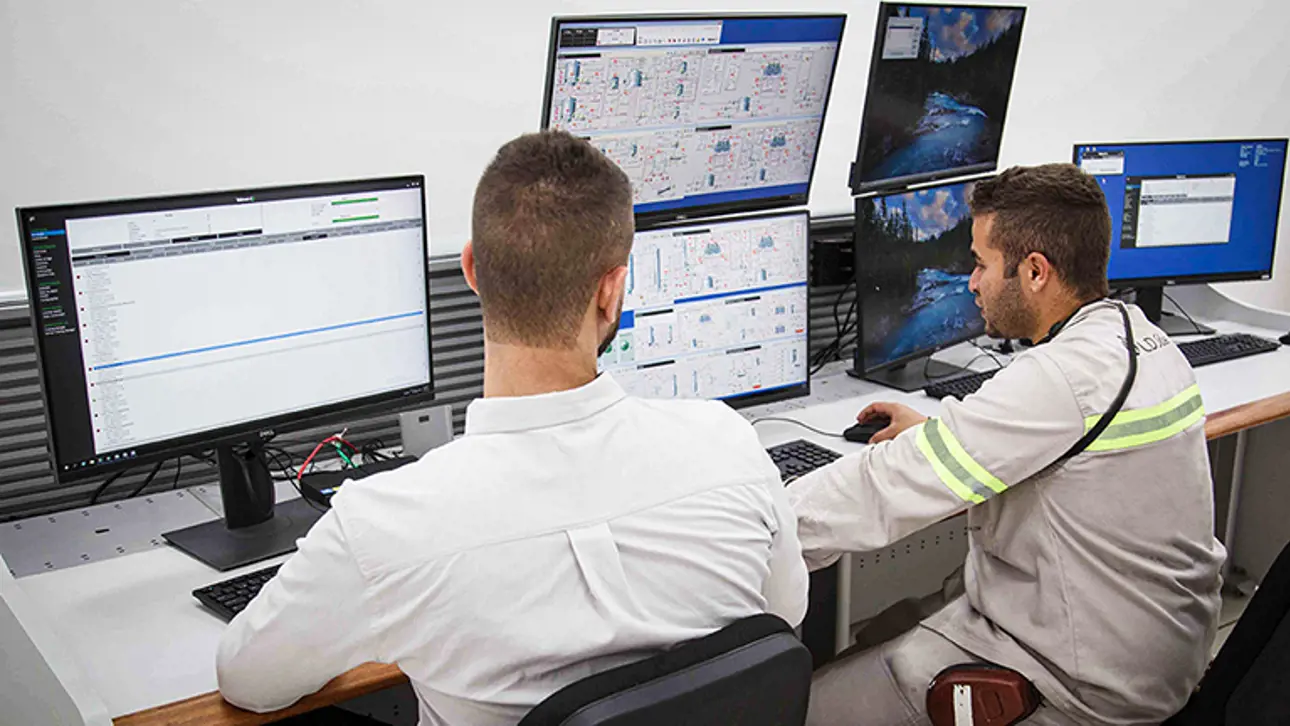
Valmet has delivered all the simulators to support the control system tests and operator training at LD Celulose’s new mill in Indianópolis, Brazil. The Valmet Training Simulator is utilized in all process islands, from start to finish of production, with a total of 14 process areas. An innovative feature of the project is that the wood handling area is the first in Brazil to receive an Operator Training Simulator (OTS). Another highlight is the presence of simulators in areas like water treatment, water treatment for boilers, wastewater treatment and turbo generators, which are usually little explored in the OTS. These investments demonstrate LD Celulose’s commitment to the quest for more efficient processes, optimized for and focusing on the safety and excellence of its operating team.
In the first step, the simulators are used to test and validate the logics implemented in the Distributed Control System (DCS) and Advanced Process Controls (APC), a process known as joint FAT. Subsequently, the set (simulator and control system) is employed as a tool in the operators’ training. Among the several benefits associated with the use of simulators is the possibility to pre-tune process controllers, whose previous definition of control parameters contributed to obtaining stabler initial conditions during the real process’s commissioning stage.
Due to pandemic restrictions, the tests were performed remotely with the support of teams in Brazil, Sweden and Finland.
The Valmet Training Simulator is an essential tool for occasional production adjustments and operational experiments because it facilitates communication between systems and is a more automated and efficient solution. “With it, we can virtually reproduce the equipment’s dynamic behavior in every situation and operating scenario with high fidelity. This way, all the machines and systems involving the mill’s operations are virtualized,” concludes Rafael Ferreira, simulator engineer, the local coordinator of the OTS project. Innovation makes it possible to train the operator team before or after the start-up, performing eventual production adjustments and operational experiments in addition to capacitating new professionals who may join the team in the future, guaranteeing more efficiency and agility in long-term production.