Valmet Fiber Flash Dryer – A flexible and energy-efficient new concept
The demand for CTMP lines in recent years has driven Valmet to further develop its flash drying technology. The result is a flexible and energy-efficient system that can be scaled to the optimal size, using the best heat source at each pulp mill.
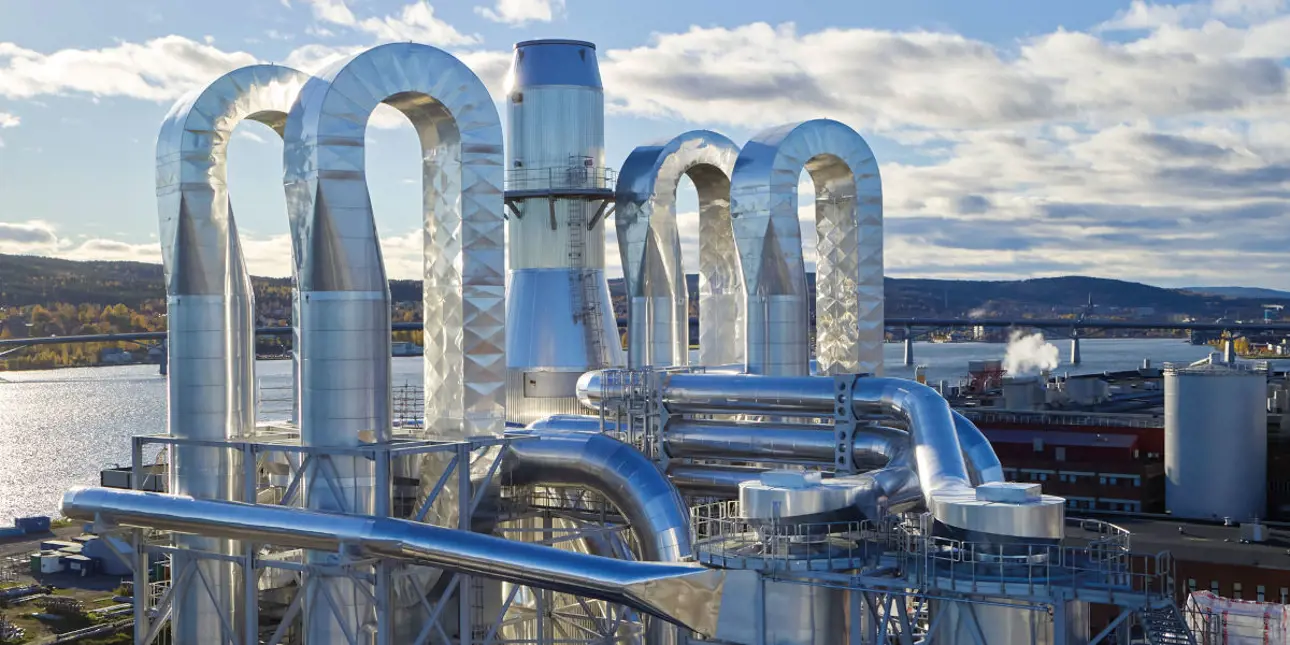
The Valmet Fiber Flash Dryer is designed for any process or pulp quality, even applications with recycled fiber and annual fibers. It’s very reliable, easy to operate and has a low total ownership cost. Valmet can deliver complete CTMP systems, seamlessly integrated from woodyard to board or bale.
A very flexible drying system
The new system’s design is very flexible, and the footprint can easily be adapted to existing buildings and machinery. In addition, most of the system can be built outdoors, even in areas with extreme weather, and the dryer sections and cyclones can also be tailored to fit applications and needs best.
The total energy efficiency of the Valmet Fiber Flash Dryer is more than 91 percent.
Henrik Bergström, Chief Process Engineer, Valmet.
The dryer will typically use heat sourced from steam/air heat exchangers, either alone or in combination with gas burners – for example, duct-mounted gas burners that use natural gas or propane. However, the actual choice of heat source will depend on factors such as the required temperature, what’s available on site and the prices of different energy sources. Meanwhile, the choice of heat exchanger will depend on the available steam quality and type: whether it’s high-pressure steam, white water steam or steam from hot filtrate.
Easy to operate and affordable to own
With the Valmet Fiber Flash Dryer system, pulp mills benefit from automatic and problem-free operation. Their operators only need to work with a few parameters, and the start and dryness controls are automatic, with advanced process control. The system therefore offers high long-term availability and requires minimal maintenance and resources, with a low total ownership cost.
High capacity and energy efficiency
In a drying process, the quality of the pulp and the system’s heat economy greatly depend on the efficiency of pulp shredding in the dewatering stage and good fluffing before the flash dryer. With the Valmet Fiber Flash Dryer, energy is recovered from the cyclones and scrubbers and from the recirculation of the drying air, which minimizes the system’s energy consumption, giving it a total energy efficiency of more than 91 percent.
The Valmet Fiber Flash Dryer has a capacity of up to 1,000 air-dried metric tonnes per day and per dryer unit, and the first flash drying system built and delivered with this new concept is now up and running at SCA’s Ortviken mill in Sweden.
“We believe in this energy-efficient technology, and we intend to develop it further. What really makes our new Valmet Fiber Flash Dryer concept stand out from the market’s other systems is the combination of our proven dewatering press, fluffer and slab press, and the new flash dryer. With the Ortviken CTMP project, we’ve verified the concept, and it’s great to see it operational now,” says Henrik Bergström, Chief Process Engineer at Valmet.
The Valmet Fiber Flash Dryer system.
TEXT Kerstin Eriksson
PHOTOS Torbjörn Bergkvist
The first system with the new concept started up
The first project was a conversion of the SCA Ortviken mill in Sweden from newsprint and LWC to CTMP production. Together, Valmet and SCA developed a concept to produce CTMP at the best possible operating expense. The system, heated by steam, consists of two dryers and one scrubber with a capacity of 2 x 475 air-dried tonnes per day. The installation was handed over to SCA in March 2023.
The Valmet Fiber Flash Dryer process
Flash drying can be described as almost instantaneous evaporation. Small particles and single fibers with a large exposed surface area meet a hot air stream in the drying stages. The fibers are carried by the hot air through the system, and they remain in the drying zone for less than 30 seconds. Since the evaporation from the wet surfaces in the air stream takes place at the wet bulb temperature of the air, the evaporation occurs at approximately 50°C. Thanks to this low drying temperature, the brightness of the pulp is unaffected during the drying process. The pulp has approx. 48-percent dryness when it enters the drying system and approx. 88-percent dryness when it exits.