Valmet Belt Dryer – efficiently turning biomass into fuel
The Valmet Belt Dryer is a low-temperature dryer for biomasses like bark, woodchips, sawdust, bagasse and agricultural waste. Its proven technology ensures high end material dryness and utilizes waste heat from the mill, keeping energy costs low.
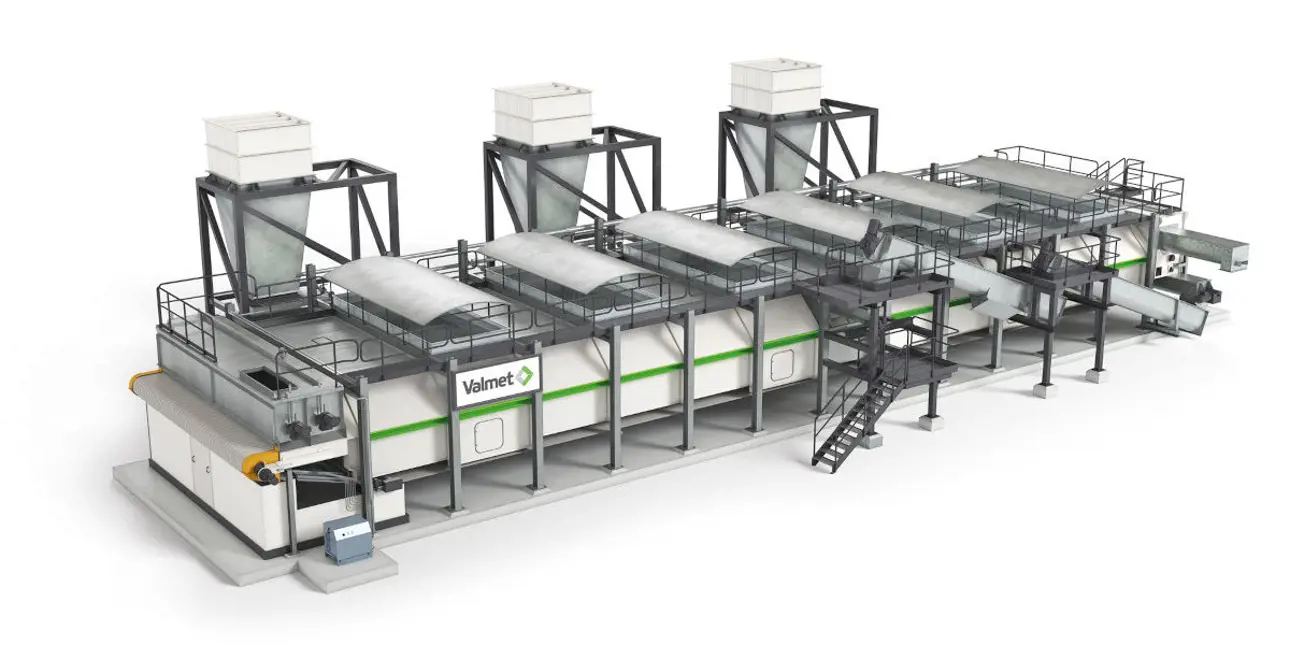
The dryer is designed to remove water efficiently by evaporating moisture from wet biomass. After drying, the resulting waste materials can be used as biomass fuel. This can be utilized in a wide range of applications, the most common of which is gasification for lime kilns. Dried biomass can also be used as fuel in wood powder firing plants for lime kilns, as well as fuel for power boilers and other combustion applications. It can also be used in biomass conversion processes like white pellet and steam-treated pellet production.
Modular and flexible design
The dryer’s structure is modular, giving it dimensioning flexibility. This means it can easily be adapted for different applications and ambient conditions around the world. Most parts can be fitted into containers for easy and cost-effective transportation and quick onsite assembly. The design has also proven to be easy to maintain and operate.
The Valmet Belt Dryer features low electrical consumption because it utilizes waste heat from other processes.
The dryer’s flexible construction allows it to be set up as single-layer or double-layer types. In a single-layer type, the biomass passes through the dryer only once. It is used as a fuel pre-dryer for applications in which the end moisture should exceed 20 percent. In a double-layer type, the biomass passes through the dryer twice for applications in which the end moisture should be below 20 percent.
Even material end moisture
The double-layer type provides several notable benefits. For example, it lowers the total heat and power consumption required for drying, and it delivers uniform residual moisture levels.
The Valmet Belt Dryer delivers high uptime, is easy to operate and produces even-moisture biomass.
The dryer can evaporate up to 30 tonnes of water per hour and enables the continuous dehydration of residual moisture below 5 percent. Thanks to the even distribution of the material, its controlled airflow and unique material recirculation, the dryer guarantees uniform residual moisture in the dried biomass it produces.
“The dryer has high uptime: It’s easy to operate and produces biomass with an even moisture content. In addition, the possibility to combine several low-temperature heat sources makes it flexible in various processes,” says Ari Havu, R&D Product Portfolio & Strategy Manager at Valmet.
Ari Havu, R&D Product Portfolio & Strategy Manager, Valmet.
No primary energy required
Several different energy sources like warm water, low-pressure steam and hot flue gas recovery systems can be used to obtain sufficient heat to operate the dryer. The heat from one or more sources is transferred to a hot water loop, which is then used to generate hot air in the dryer. A hot water loop can be used when the ambient temperature is always above +0 °C. When the ambient temperature is below -0 °C, ethylene-glycol dilution or propylene-glycol dilution is used.
The Valmet Belt Dryer features low heat consumption because it operates at low temperatures.
Sustainable and cost-effective
This robustly designed high-efficiency dryer features low heat consumption because it operates at low temperatures. This type of drying is non-destructive and does not change the properties or quality of the biomass as is the case with high-temperature drying. The dryer also features low electricity consumption because it uses waste heat from other processes, and no primary energy is required.
The dryer is also designed to keep maintenance and operating costs low. Wear parts have been kept to a minimum, and several parts of the dryer have features that prolong the equipment’s lifetime. For example, the conveying screw has a lining, and the dryer is mounted on conveying rolls, both of which reduce friction and wear. Operation is fully automatic, and material is recirculated to optimize heat and power consumption. Thanks to its efficient operation, the dryer’s environmental impact is kept to a minimum, and its availability is high.
“Integrating the dryer as part of the main process and heat recovery systems is important to Valmet customers when optimizing heat use and the plant’s overall efficiency. An integration combines several Valmet technologies, and it’s a real value-adding service for our customers,” Havu concludes.
The dryer efficiently turns biomass into fuel, and it plays an important role in the green transition.
Text Kerstin Eriksson PHOTOS Lars Berggren, Ari Havu
Keep the desired conductivity with a Valmet Dryer Belt
“A few years ago, we combined our belt dryer manufacturing expertise with our industrial fabric experience and launched the Valmet Dryer Belt. Today, we have a solid installed base of dryer belts in a continuously growing customer network,” says Raul Almeida, Global Product Manager for dryer belts at Valmet. Valmet’s dryer belt technology ensures that the end material has high dryness, and is easy to maintain and handle.
The Valmet Dryer Belt is a product specifically designed for dryers operating in wood, pelletizing and biomass plants that dry and convert the material for energy use. The belt has a herringbone pattern with antistatic properties and a strong stainless-steel seam. It tolerates temperatures up to 140 °C. Valmet can produce and deliver belts in widths of up to 12 meters and in lengths of up to 140 meters.
Valmet works as a licensee of the Swiss company W. Kunz dryTec AG, leader in the agro industrial dehydration market that commercialises its products under the brand name Swiss Combi with a 50-year experience.
Related articles