Valmet Methanol Purification - Unleashing the green value of methanol
Methanol is a pulp mill byproduct with great potential. Its better use may help a pulp mill lower the fuel costs, lower the carbon footprint and increase production.
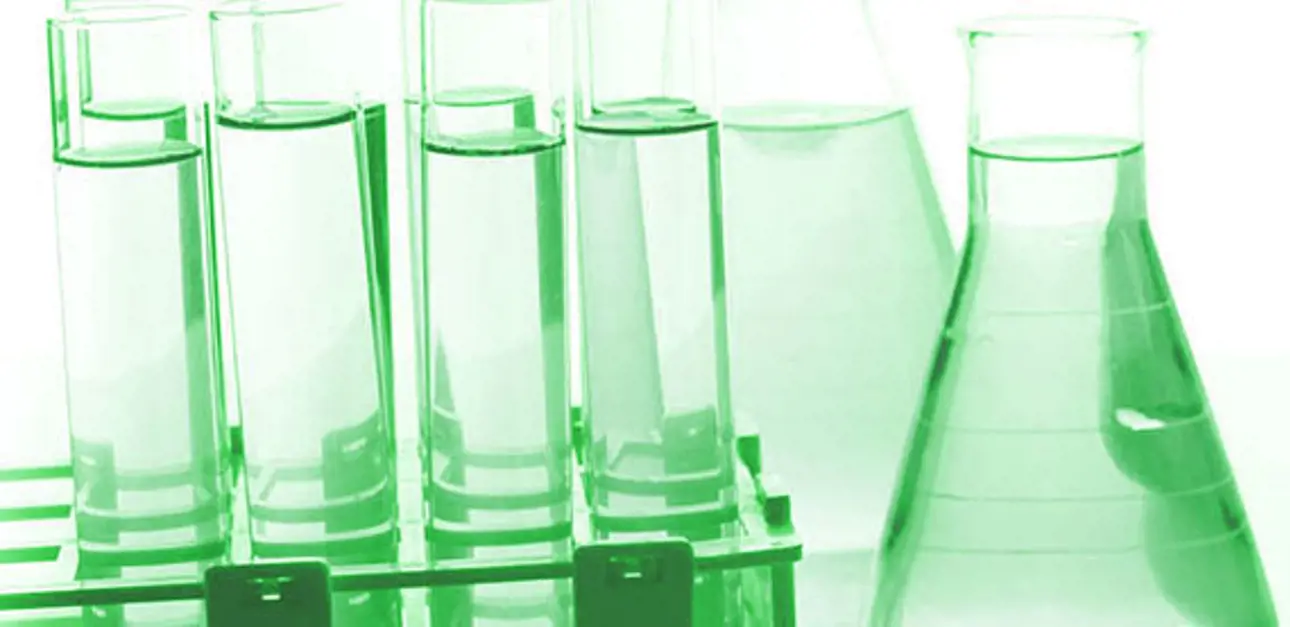
Commercially available methanol is primarily made from natural gas and is therefore not carbon neutral. But pulp mill methanol is a green fuel that can be used instead of natural gas or oil. A mill produces some 10 to 15 kg of methanol per tonne of air-dry pulp (ADT), and this is enough to make many modern pulp mills operate without any fossil fuel at all. Instead, they use liquid methanol that is produced and stored in the mill.
New purification technology
But today, using pulp mill methanol can be something of a challenge. It is concentrated in gaseous form in the evaporation plant, and after some heat recovery steps and the reduction of the moisture content, the gas is sent to either incineration, typically to the lime kiln or to the recovery boiler, or to a liquid methanol system. The methanol is heavily contaminated and has a very strong odor. Handling is therefore difficult, and combustion results in emissions of NOx and SO2. The methanol can also vary in water content and quality, and this has resulted in lime kiln capacity issues.
To take the pulp mills forward, Valmet and several industry partners have developed a new purification technology. Today, it’s possible to upgrade existing methanol systems so pulp mills can produce purified methanol – bio-methanol.
Higher profits and a lower carbon footprint
“The benefits of purifying methanol can come from using it as a fuel at the mill, selling the purified methanol or debottlenecking the recovery boiler. A pulp mill with a production of 400,000 tonnes of pulp per year produces approximately 15 tonnes of methanol per day, and for a mill like this, the combined benefits could reach several million dollars a year,” says Anders Rothelius, Manager, Evaporation Applications and Technology at Valmet.
Anders Rothelius, Manager for Evaporation Applications and Technology at Valmet
Using purified methanol instead of the normal quality brings benefits like better combustion, lower emissions and higher availability. And if 15 tonnes of methanol per day are used as fuel instead of oil, the mill saves USD 0.9 million/year or more, lowering its carbon footprint.
The benefits will be greater for mills with access to a market for bio-methanol. Fossil methanol sells at around USD 500/tonne, but since there is no established market for bio-methanol, it is difficult to predict its value. Selling 15 tonnes of purified methanol/day at the price of fossil methanol produces annual revenue of USD 2.6 million. And it’s likely that the bio-methanol will command a premium.
Removing methanol from the recovery boiler fuel mix can also enable increased pulp production. If the recovery boiler is the limiting factor, the mill will be able to produce one extra tonne of pulp for every tonne of methanol that is removed. If extra pulp brings USD 250/tonne, including other costs, 15 additional tonnes of pulp per day will increase profits by approximately USD 1.3 million/year.
A methanol upgrade
Liquid methanol systems can now be upgraded with a purification step. And if the resulting bio-methanol is distilled, it becomes so pure that it can be used in chemical processes. This makes it possible for pulp mills to displace fossil-based methanol for the production of chlorine dioxide, an important bleaching chemical. “The methanol purification plant that was built during the development project was operated at a pulp mill for almost 4,000 hours without problems. The design was later completed and is now proven for commercial applications. The development of the technology was made possible with the help of several industry partners, and we’re now ready to help pulp mills use this technology to bring their performance forward,” Rothelius concludes. |
|
The methanol purification technology was developed and proven together with several industrial partners in an industrial environment
|
Existing methanol plants in pulp mills can be upgraded with a purification step located upstream from the methanol plant. The resulting purified methanol is a high-quality fuel that can be used at the mill or sold.
Purified and distilled methanol is clean enough to be used in other chemical processes like chlorine dioxide production. This will displace fossil methanol use for this purpose at the mill.
Text Andreas Liedberg
Related articles