Turning up the volume of CTMP production at SCA Ortviken
The demand for newsprint and magazine paper in the world has decreased. To adapt to this change, SCA decided to shut down the production of newsprint and LWC at their Ortviken mill and focus on producing CTMP pulp instead.
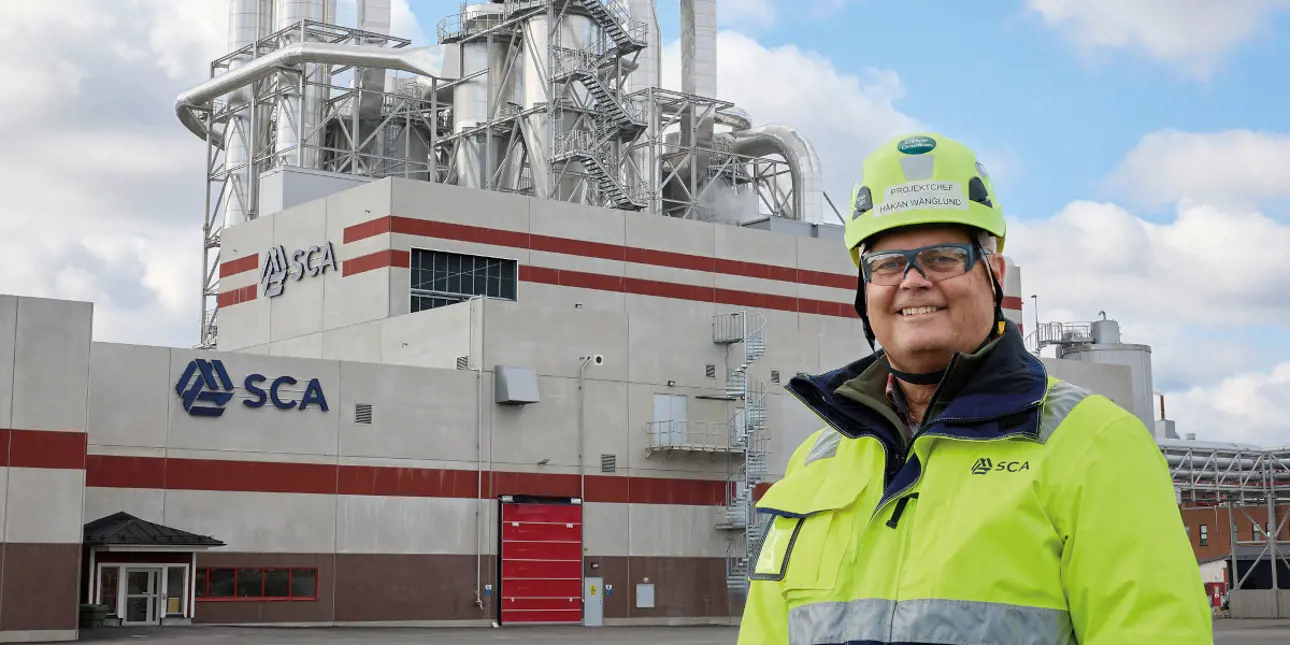
Håkan Wänglund, General Project Manager at SCA Ortviken, in front of the new flash drying and baling building.
SCA has many years’ experience of producing CTMP, and they know the technology and the customers well. They started the Ortviken conversion project in 2021.
We wanted a reliable supplier we could trust.
“We divided this project into four parts: wood handling, the CTMP plant, dewatering-drying-baling, and the fourth part, common systems, which ties the other three together,” says Håkan Wänglund, General Project Manager at SCA Ortviken. “We wanted a reliable supplier we could trust, and we also wanted to contribute as much as we could dare to healthy competition in the industry. Valmet was a possible supplier for the CTMP and dewatering-drying-baling projects. A large part of the CTMP section consists of existing Valmet machines, so it made sense to ask Valmet how we could rebuild the plant.”
A good response from CTMP customers
The planned CTMP production capacity at Ortviken is 300,000 tonnes, which is triple the company’s current capacity at their Östrand mill.
The compact layout in the CTMP plant.
“The increased production has brought us new customers. Although we have not yet reached the intended quality and capacity for all products because we’re still fine-tuning the facility, we’re gradually getting approved as a supplier. We still run CTMP production at the Östrand mill for support with the qualities we have yet to achieve. Our new product, called “More,” has been launched for our customers. It is a high-quality pulp, and we’ve received a positive response so far,” says Wänglund.
A challenging installation
SCA utilized an existing building for the CTMP plant, which limited their options with the layout. For example, the impregnation screw had to be inclined to fit below the traverse beam. The construction of the dewatering, drying and baling parts was easier because it was a greenfield installation with plenty of working space. The CTMP plant also included the installation of the first flash dryer ever built according to Valmet’s own concept – the Valmet Fiber Flash Dryer.
I’m absolutely convinced that we will achieve our goals in this project.
“All projects have their challenges, but if someone had asked me in advance what risks I foresaw, I would never have guessed that we would have a pandemic for two years, a war in Ukraine, or a ship getting stuck in the Suez Canal and causing chaos worldwide. You must remember this when evaluating our successes. However, we’ve been lucky to have a decommissioned mill facility from which we’ve been able to source spare parts. We were able to reuse equipment and at the same time move forward with the installation,” says Wänglund.
Dewatering presses are proven technology and an important part of the Valmet Fiber Flash Dryer concept, in combination with fluffers, slab presses and the flash dryer.
HT-CTMP for energy-efficient production
The production line is designed to reduce energy consumption in several ways. One example is the high-temperature chemi-thermomechanical pulp (HT-CTMP) process that it uses – the impregnation stage softens the fiber, which means that less energy input is required in the refiners. And in the Valmet Fiber Flash Dryer system, the drying air is recirculated, and energy is also recovered from the cyclones and scrubber, making it very energy-efficient. The refiner segments are currently being tested to identify the optimal parameters to achieve the right quality of pulp and ensure lower specific energy consumption.
“We can easily measure our facility’s steam and electricity use. We have frequency converters on many pumps to keep energy consumption down, but in the case of the largest motor, the quality parameters control the energy consumption. During the project, Valmet suggested a new way to use low-pressure steam and thereby reduce the proportion of medium-pressure steam consumption. As an environmentally conscious company, it was an easy decision for us. Energy efficiency is extremely important to SCA,” says Wänglund.
Energy is recovered from the Valmet Fiber Flash Dryer system, which makes it very energy-efficient.
Finding solutions and moving ahead
“As we’re in the start-up phase right now, we’ve obviously not had the opportunity to measure all the qualities and how efficient the facility is over time, but I’m absolutely convinced that we will achieve our goals in this project. I think we had a good working atmosphere, and I feel that it is a mindset at Valmet to try to find solutions for moving ahead. There were never any deadlocks because of different opinions. I really appreciate that kind of mindset. If you consider all the challenges we had, I think this was a very successful project overall,” Wänglund concludes.
Text Kerstin Eriksson Photos Torbjörn Bergkvist
The first pulp bale
A milestone in the project was of course when the line was started up, the first pulp went through the entire system and the very first bale was produced.
“If I were to name a highlight of the project, I would choose one occasion in particular. That’s when we managed to run pulp through the system for the first time and receive the first bale. I remember when we were waiting for the right dry matter to be reached. We had a camera on the dry matter meter that slowly ticked upwards. At 48%, we transferred the pulp to the dryer and it went very well already on the first try. I saw the incredible joy in the staff on site, it was great. I was happy as well. We have saved that first bale, it is like a receipt that we have now tied the knot,” says Wänglund.
CTMP pulp
SCA Ortviken manufactures a CTMP pulp that has many different uses. For example, it can be used in the intermediate layers in cardboard to make it stiff, bulky and strong, and it is also suitable for book paper and for hygiene products where good absorbency is required.
The pulp can be made from pure spruce, a mixture of spruce and birch or pure birch. With spruce, the fibers come from partially self-hewn roundwood spruce together with sawmill chips from, for example, the Tunadal sawmill. Because it can combine materials with different properties, the Ortviken mill has the flexibility to produce pulp that yields very good strength, bulk and low shives content.
Related articles