Toward a virtualized mill environment at LD Celulose
Dec 21, 2021
The automation system of LD Celulose’s new dissolving pulp mill in Indianópolis, Brazil stands out with its innovativeness. The Valmet DNA Automation System is built on the latest virtualization technology, allowing a completely new way to operate the mill.
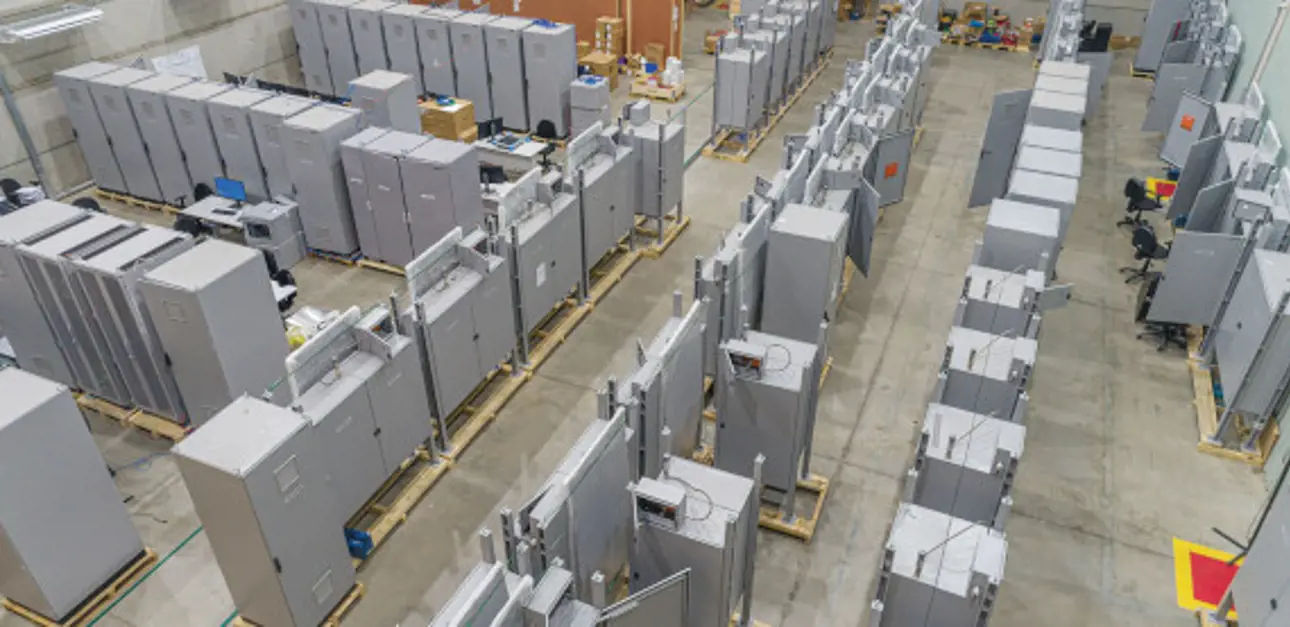
LD Celulose, a joint venture of Lenzing and Duratex, is building a new 500,000 tonne/year dissolving pulp mill in Indianópolis (MG), Brazil. Valmet is delivering key technologies and automation solutions for the project, which is expected to start up in the first half of 2022.
The factory acceptance test (FAT) of the automation system for the new pulp mill was finalized in Valmet’s premises in Sorocaba in October 2021. The automation system has more than 230 cabinets, and a total of 55 specialists was involved in implementing the project.
The factory acceptance test (FAT) of the automation system for the new pulp mill was finalized in October 2021. The automation system has more than 230 cabinets.
Developing a virtualized mill environment
In planning the new mill, LD Cellulose wanted to take advantage of Valmet’s expertise in automation and decided to go for an innovative virtualized mill environment. In practice, this means all the Valmet DNA automation system’s Windows nodes are virtualized into two redundant high-availability clusters. This allows the number of physical computers to be significantly reduced into several servers, enabling the use of redundancy, diagnostics, lifecycle management and cybersecurity features that come automatically with the virtualization technology. “In this project, we could achieve a level of technology that is rare in the automation sector but is less so in the IT area,” explains Jacson Santi, automation and instrumentation specialist at LD Celulose. “The biggest distinguishing feature is the virtualization of all the machines and systems that are involved in the mill operation.”
“The main goal is to maintain this partnership not only today until the mill’s start-up, but throughout the journey of the new LD Celulose plant," says Simone Almeida, applications manager at Valmet.
“Having Valmet as a partner is very positive. We’ve proven that the best technologies were adopted in the project. Thanks to the new features that come with the virtualization technology, we are able to analyze the entire plant from the control room. And all this with a very assertive interface,” says the maintenance manager at LD Celulose, Alan Alves.
Final acceptance test with remote connections
With the Covid-19 pandemic, one of the project’s challenges was to conduct the factory acceptance test that is typically conducted in Valmet units like Sorocaba and Finland remotely, with Valmet and LD Celulose teams participating from different locations. Sandro Silva, Valmet project manager, says: “We were all ready to welcome the Finnish and customer teams, but as safety comes first, we decided to do almost everything remotely. With quick planning, we were able to introduce some new tools and facilitate a high-quality acceptance test, with customer representatives joining from Brazil and Austria, and our Valmet team from Finland and Brazil. Even in these circumstances, we achieved all the goals we’d set.”
"Thanks to the new features that come with the virtualization technology, we are able to analyze the entire plant from the control room," says the maintenance manager at LD Celulose, Alan Alves.
Strong experience in green field projects
Another criterion for choosing Valmet as the major partner for the new mill was its expertise in greenfield projects in the pulp industry. “We had many meetings to introduce our solutions and highlight our capacity to execute projects. To support LD’s choice, we promoted a reference visit at a mill in Brazil’s South Region, where we could exchange experiences with the final user. LD Celulose seeks innovation, and we have solid references in this segment for the pulp and paper industries,” explains Simone Almeida, applications manager at Valmet.
“With quick planning, we were able to introduce some new tools and facilitate a high-quality acceptance test remotely," says Sandro Silva, Valmet project manager.
The biggest distinguishing feature is the virtualization of all the machines and systems that are involved in the factory operation.
Almeida adds that good project development during the in-house phase reinforces the partnership for the next phase on site, when the commissioning and start-up happens. “The main goal is to maintain this partnership not only today until the mill’s start-up, but throughout the journey of the new LD Celulose plant, offering our services and automation solutions, and following Valmet’s way to serve,” she concludes.
“The biggest distinguishing feature is the virtualization of all the machines and systems that are involved in the mill operation,” says Jacson Santi, automation and instrumentation specialist at LD Celulose.
Text Livia Bianco, Luiz Kozak
Photos Renato Galvão
The article was updated in November 2024 to include the scope delivered by Demuth, before that business was acquired by Valmet in 2024.
Scope of Valmet’s delivery
- Wood handling
- Fiberline
- Pulp drying and baling line
- Evaporation plant and ash crystallizer
- White liquor plant
- Mill-wide automation system and process analyzers
- Operator Training Simulator
- Valmet Performance Center connectivity
- Spare parts consignment agreement
- 5-year consumables agreement, including screen baskets, slitter parts, dryer machine clothing, filter bags and expert visits.
Executing a large project during challenging times
Delivering a project of this size and scope is always a major effort that involves thousands of people and work stages. When you add a global pandemic with major disruption in transcontinental transport and travel restrictions to the mix, the equation becomes even more challenging.
“We’ve implemented almost all of this project during the Covid-19 pandemic. Despite facing logistics challenges caused by Covid-19, the impacts on material flow haven’t impeded our progress. We’ve mitigated the impacts by rearranging the works. We’re also prepared to offer remote support for commissioning if it’s needed,” says Pekka Rikkinen, Project Director, Pulp and Energy, Valmet.
“This is a technically demanding project, and we’ve needed to pay special attention to planning and scheduling to succeed. With LD Celulose, we’ve implemented various Covid-19 mitigation actions, covering not only the site works, but also other areas such as accommodation and transportation,” explains Guilherme Mendonça, Project Manager, South America, Valmet.
“All this has meant we’ve also had to conduct many of our internal and customer meetings remotely. The key to the success has been that we’ve communicated openly and actively, and we’ve all been working together toward the same goal,” Rikkinen concludes.
Full Valmet mill
After the acquisition of Demuth our common reference LD Celulose dissolving pulp mill has become a full Valmet mill. Demuth has delivered two complete wood handling lines including roller debarkers, disc chippers, screening stations and storages for chips and biomass.