Smooth start-up with Valmet Training Simulator
Dec 11, 2018
When a new white liquor plant was installed at the CMPC Laja mill in Chile, simulator training and testing of the distributed control system (DCS) were essential parts of the project. They were key factors in achieving a fast, smooth start-up.
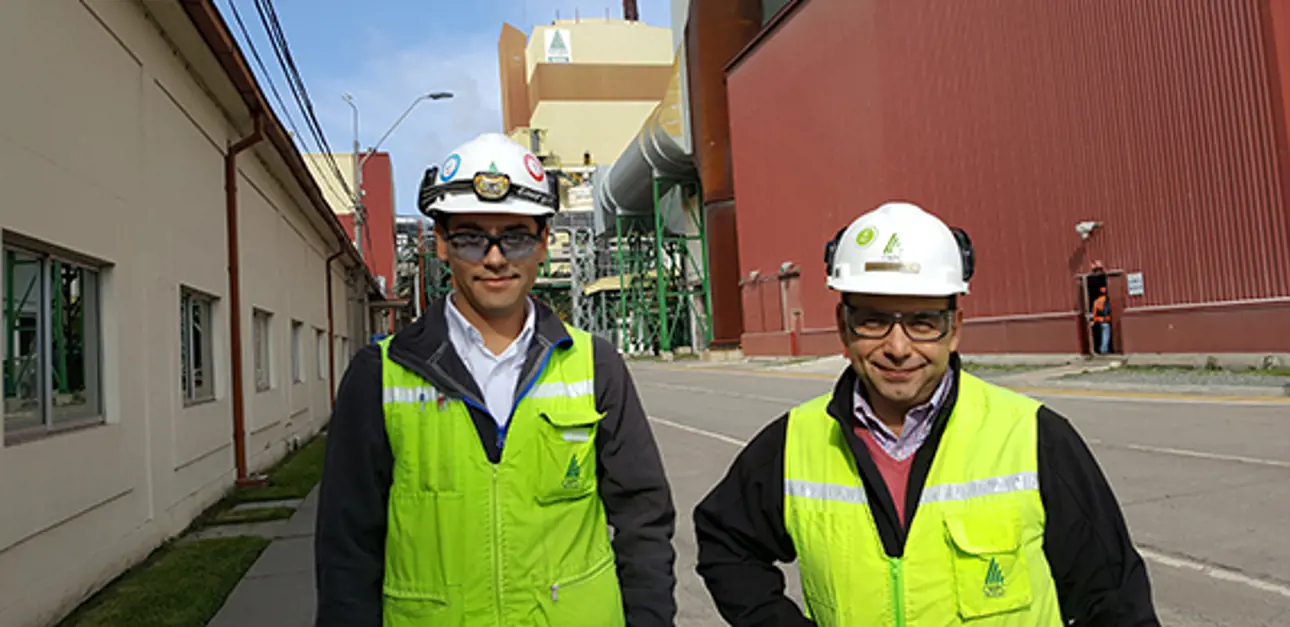
Due to environmental restrictions, the CMPC Laja mill needed to improve the environmental performance of its white liquor plant.
“We had a deadline of March 29, 2018 to improve the situation. The decision to build a new white liquor plant was taken in 2016, and the investment totaled EUR 120 million,” says Carlos Figueroa, Production Manager at the Laja mill.
Rapid, smooth start-up
On February 24, 2018, the new white liquor plant started up. There was a direct switch from the old plant to the new one, without any need for a shutdown.
“The fact that we didn’t need to stop and we instantly reached nominal production is hugely impressive. Thanks to the good co-operation with Valmet and the invaluable training – including the simulator – the start-up was very successful,” says Figueroa.
Classroom training
The technology in the white liquor plant was new to everyone, so there was a focus on training. A total of 18 people – operators, process engineers, shift managers and DCS engineers – took part in the classroom and simulator training, focusing on basic knowledge of the new equipment.
“The trainers were very skilled, and the training was at the right level,” says Pedro Peralta, Process Team Leader and the coordinator of the training.
A total of 18 people took part in the classroom and simulator training, focusing on basic knowledge of the new equipment.
Simulator tests and training – a key to success
A Valmet Training Simulator was included in the project. The simulator was first tested by Valmet and then verified in close collaboration with simulator engineers, DCS programmers and process engineers at the Laja mill. More than 50 issues related to the DCS applications were found during the simulator tests.
“It is a great advantage using the simulator during the DCS tests. The DCS programs and displays are much better tested than in projects without a simulator,” says Peralta.
A train-the-trainer course was held for Pedro Peralta and two others so that they could themselves conduct simulator training on site with all the operators. The simulator training was led by process specialists from Valmet. A simulator specialist participated to support the trainers. A number of pre-defined scenarios and exercises were developed, and all the operators had to run the exercises and related tests to pass the training.
“The simulator training was excellent. The simulation and scenarios were very realistic,” says Peralta. Mauricio Matamala, Simulator Systems Engineer at the Laja mill, gives his perspective: “There were initial tests of the simulator system early in the project. This was valuable for the rest of the project. The co-operation with the simulator engineers from Valmet was excellent.”
“The trainers were very skilled, and the training was at the right level.”
In-house simulator training to be continued
“The training has enabled our own trainers to run the simulator, and now they can create customized exercises so that others also can learn. The system administration by mill system engineers works very well,” says Matamala.
The simulator will continue to be used for training new staff. At the time of the interview, additional simulator training was being conducted for other mill personnel.
Stable production and high availability
With the new white liquor plant, CMPC has seen many improvements related to better quality, reduced environmental impact and higher availability. The white liquor quality is better, the amount of suspended solids in white liquor has improved, the active alkali is more stable, and the dryness of the lime mud is higher. CMPC were able to discontinue using a polymer that was previously required. The working environment has also improved, and the whole area is much cleaner.
“Thanks to the invaluable training, the white liquor plant today operates at a stable production with high availability,” concludes Figueroa.”
On February 24, 2018, the new white liquor plant started up. There was a direct switch from the old plant to the new one, without any need for a shutdown.
Contact person
Lars Almkvist
Director, Simulators and Process control, Pulp & Energy
lars.almkvist(at)valmet.com
+46 70 559 53 90