Valmet celebrates the delivery of over 100 White Liquor Oxidation systems
Jan 22, 2025
The modern pulp mills are excellent examples of circular economy thinking – where all resources are recycled and reused, waste streams are minimized, and the processes’ water and chemical loops are closed as much as possible.
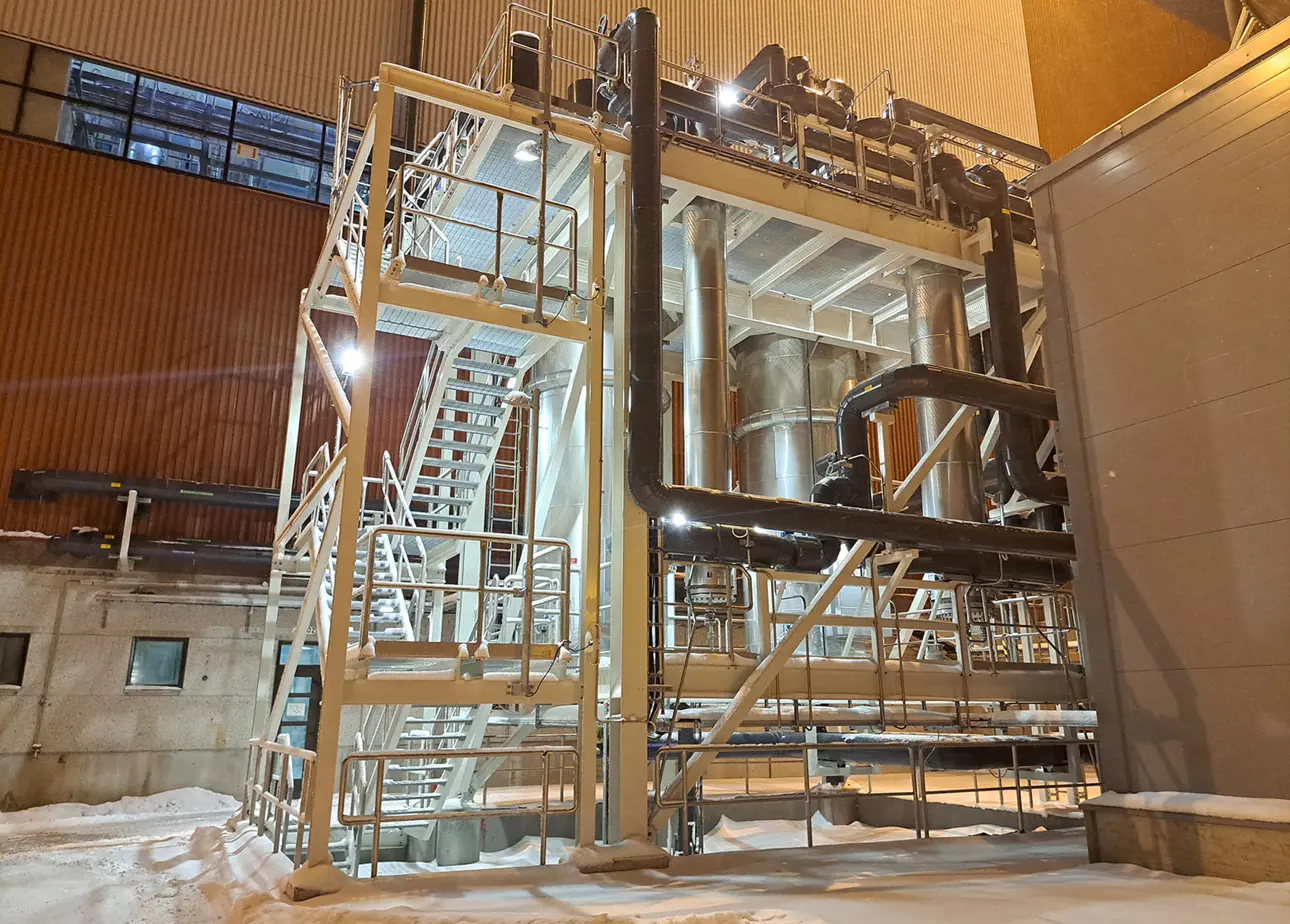
One of the innovations to improve the reuse and reduction of chemical usage is the White Liquor Oxidation.
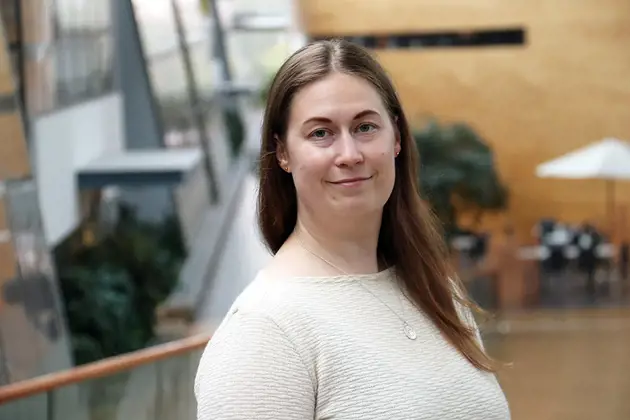
“This is actually a solution that has been around already for several decades, but the latest performance and sustainability drivers have increased the interest for this again. We have now passed the milestone of delivering hundred references globally. Our oldest references are air-based systems from the mid-1980s and latest ones are oxygen based systems to Arauco Sucuriu in Brazil, our biggest reference, and JK Paper India, our smallest one,” tells Jasmina Leppänen, Valmet’s Mill Wide NCG Systems’ Product Sales Manager.
“The main use for oxidized white liquor is to use it for pH control in the oxygen delignification plant, bleach plant, or effluent plant, thus replacing external alkali usage with mill’s own white liquor. By not using NaOH as alkali source we can increase internal circulation, reduce operational costs, and also reduce the need for make-up chemicals,” explains Yann Chapellière, R&D Engineer for Valmet’s Mill Wide NCG Systems.
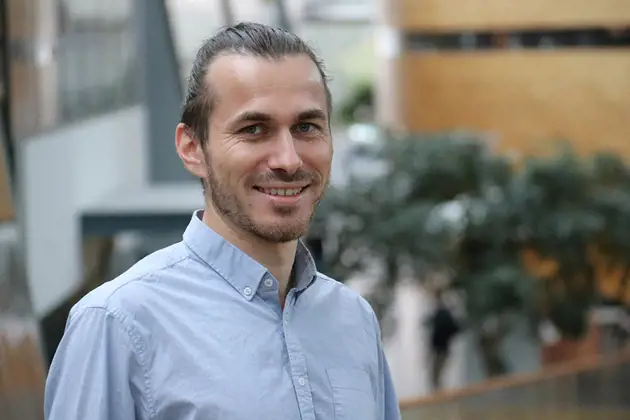
Alternative technologies for different needs
Valmet offers two well-proven and efficient alternatives. The atmospheric air-based oxidation system, Valmet WLOX AIR, is suitable for the production of partially oxidized white liquor for oxygen delignification. The pressurized oxygen-based system, Valmet WLOX O2, can produce fully oxidized white liquor and is thus suitable for more demanding utilization in for example bleaching stages or BCTMP plants.
The two-vessel pressurized oxygen based white liquor oxidation system (WLOX O2) has a small footprint and can be used for total oxidation.
“The original, more simple, atmospheric solution is still used, and the oxygen-based solution has been on the market since late 1990s. Our systems offer very good availability and easy maintenance. The oxygen-based system has smaller physical footprint and offers much higher sulfate (SO4) conversion rate. It has been great to see that the demand for this system has continued. We have delivered several projects where an existing pulp mill has been upgraded with this system,” Jasmina Leppänen summarizes.
“We have followed-up our installations and have seen very good results in practice. For example, there have been no reports of fouling problems and during our latest start-up our oxidation results were beyond satisfactory for a plant delivered to a pulp mill in Finland. To find the correct solution for each mill, the mill process and chemical cycle needs to be carefully analyzed,” Yann Chapellière complements.
Related articles