Top-level availability and world class energy efficiency in evaporation
The world’s number one most energy efficient evaporation plant could be the one at SCA Östrand in Sweden. Compared to a normal, modern pulp mill, this plant saves more than 100 000 tons of steam per year. This enables a nice income from sale of renewable electricity, but the new evaporation plant also enables full reuse of mill condensates and that brings large savings in fresh water.
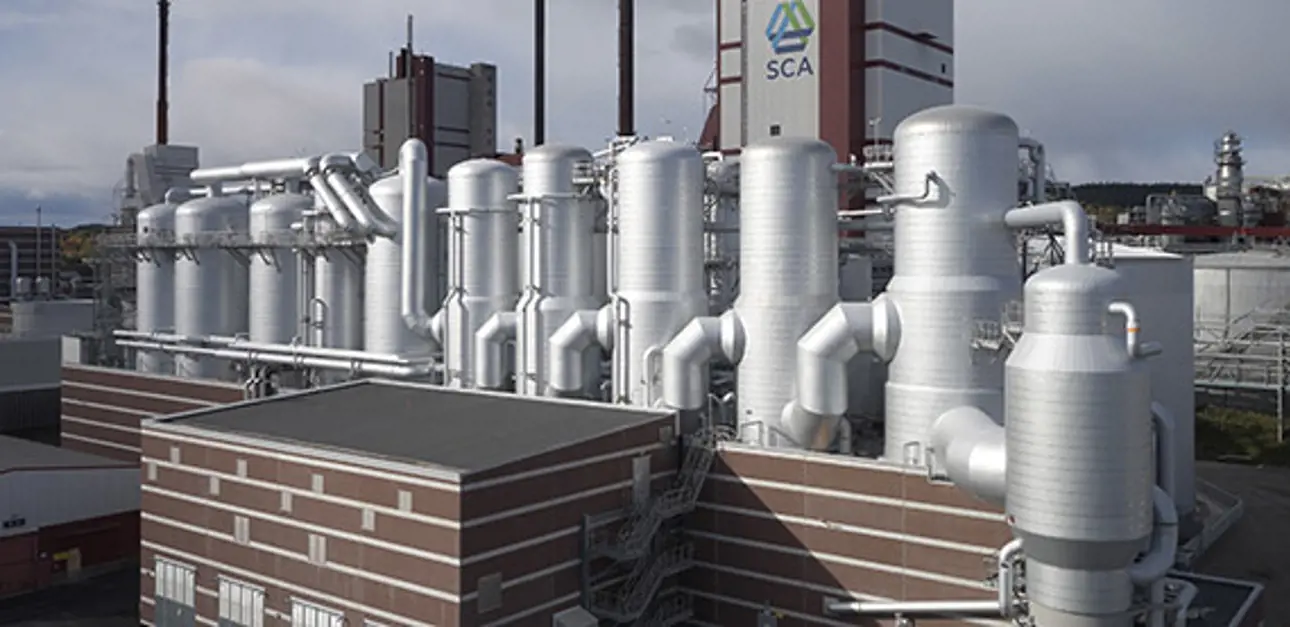
Project Helios
Project Helios was a large undertaking to increase the production of market pulp at the SCA Östrand mill. The goal was to increase production from 430 000 tons to 900 000 tons per year and the chosen strategy was to modernize the mill in carefully planned steps spread out over several years. Project Helios was completed in 2018 and SCA got a pulp mill that will create growth and employment in the region surrounding the mill for decades to come. A future development into a biorefinery plant is also in the plans.
SCA wanted the evaporation to add substantial value to the mill’s operation, and the teams from the mill and from Valmet therefore performed an extensive review to find the best possible energy configuration for the mill and to find the best design of the evaporation plant.
Since evaporation with condensate treatment is the biggest steam consumer in the mill, it’s the obvious target when improving the energy efficiency. A life cycle cost (LCC) analysis has proven to be one suitable method for finding the optimum solution, but to give an accurate indication, the analysis should include a wide array of design parameters.
But improving the energy efficiency can bring challenges. As evaporation becomes more energy efficient, less live steam will be needed and, if the total evaporation capacity and dry solids levels remains constant, scaling will most likely become an issue not only in the concentrator.
Condensates: A hidden treasure
Today’s condensate handling solution from Valmet enables full reuse of condensates in the mill. One of Valmet's design strategies is to use selected evaporators to segregate condensate into one larger flow of cleaner condensate and another, smaller, flow of foul condensate. The height and tube design of a Valmet evaporator makes it ideal for stripping of condensates.
Methanol
Methanol is normally collected in the stripper off gas and sent for liquefaction in a methanol plant. With new technology from Valmet, many existing methanol plants can be upgraded to produce purified methanol. This is a high-quality fuel that can help the mill lower the need for fossil fuels. With distillation, the purified methanol becomes clean enough for use in the ClO2 plant. This can bring serious savings in the form of lower costs for purchased chemicals.
Authors: Mathias Gourdon, Raymond Burelle, Andreas Liedberg, Outi Niittymäki, Randy Stern, and Anders Wernqvist
This article is a summary of a paper which will be presented at the International Chemical Recovery Conference ICRC in Brazil in 2021. The presentation will explain how to further improve the thermal efficiency and the environmental performance of kraft pulp mills, and how new systems and techniques have been developed within the evaporation plant. Additionally, the presentation covers how these new approaches were implemented in a project completed in 2018 for a new evaporator and condensate treatment system supplied by Valmet at the SCA Östrand market pulp mill.
Related articles