Sulfuric acid production in mega mills – integration and mill chemical balance
Non-condensable gases (NCG) are formed during cooking and evaporation processes in chemical pulping. NCG contain reduced Sulfur and causes pungent smell in the mill’s surroundings. Once released to the atmosphere, Sulfur oxidizes and contributes to the large-scale acidification of soil, which negatively affects vegetation and biodiversity.
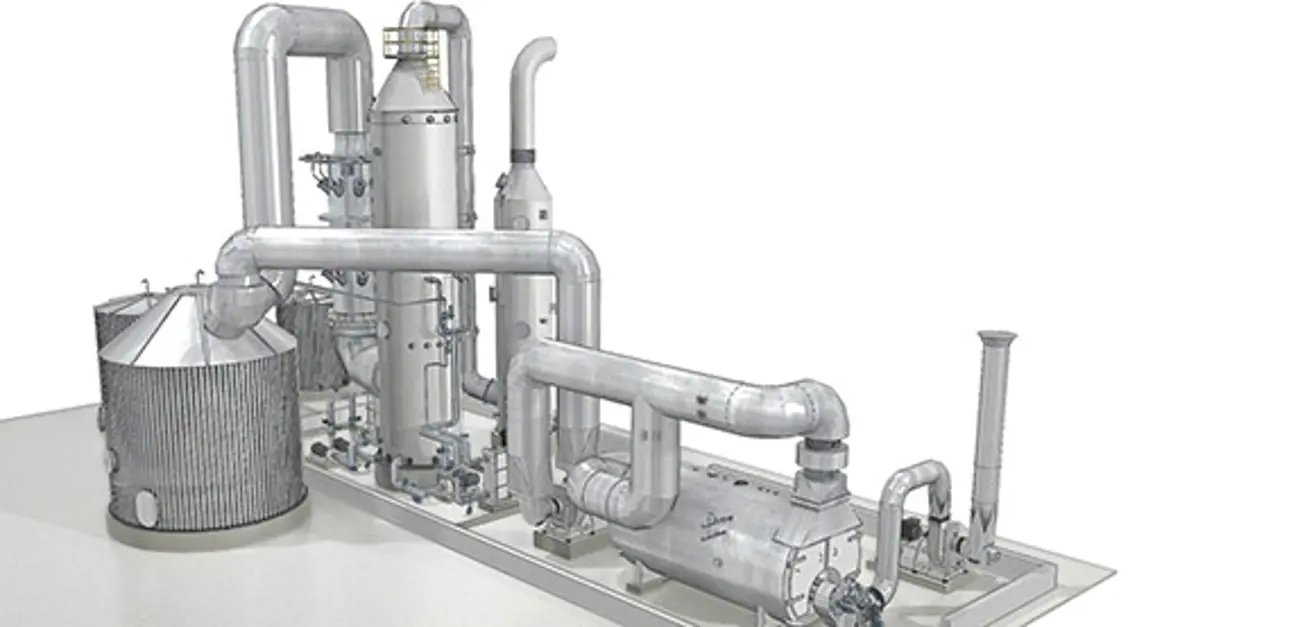
Traditionally, NCG are carefully collected and incinerated either in the recovery boiler/power boiler/lime kiln or a separate NCG boiler. In many cases oxidized sulfur in flue gas is not recovered and thus it increases the emission levels of the mill.
Working together with Metsä Group Valmet developed a new solution for sulfur control in the pulp mill processes. With decades of experience on solving mill chemical balance issues, Valmet’s team designed the solution to use NCG as main source to produce sulfuric acid, and the produced acid can be used in pulp mill processes. The solution is suitable for all types of chemical pulp mills.
The internally produced sulfuric acid can replace purchased acid at several locations within the mill. Valmet acid plant delivery, technological and operational experience suggest that this plant is a must process for any mill that is from moderately sized to mega mills. Valmet’s Sulfuric acid plant technology is one step closer to achieving the realization of future biorefinery concepts.
The first sulfuric acid plant of this type was started up in 2017 and has been continuously operating at Metsä Group’s Äänekoski Bioproduct mill, Finland. In 2020 Valmet made a pre-agreement with Metsä Group to deliver a similar solution for the planned Kemi Bioproduct mill.
Drivers for development
Active chemicals containing sulfur (S) and sodium (Na) as main elements play a vital role at chemical pulp mills. At any given mill process, Na/S exists as combination of different chemical forms. Efficiency of a pulp mill is defined by the amount of pulp it produces by maintaining active chemical recycling process.
As a common practice, pulp mills are purging a sulfur rich stream e.g. recovery boiler ash and neutralized spent acid from the chlorine dioxide plant. Several pulp mills reduce their sodium intake by using oxidized white liquor at oxygen delignification to maintain pH. Recovery boiler ash mainly contains Na2SO4, which leads to that also a lot of sodium is lost, when the S-level is controlled. Due to the loss of sodium with the ESP ash sulfur-free sodium must be added to the system. Therefore normally sodium hydroxide is added to the process increasing the operating costs.
Environmental and economic forces have been reducing the ash purging and the consumption of fresh water. Additionally, the improved pulp washing has reduced the loss of chemicals with the pulp leaving the washers. Reduction of sodium loss from the washing process is more difficult to achieve since sodium is adsorbed on the fiber that leaves the closed liquor cycle. Although these methods are applied at some modern mills, they still face difficulties to control the sulfur.
One of the development trends in kraft pulping, is to create valuable side streams from the process. Such streams are in many cases created by a primary acidification with sulfuric acid. Examples being tall oil production and lignin extraction. Sulfur from these processes increases the sulfur load on mill recovery cycle and therefore internally produced sulfuric acid will close the mill chemical balance, and the acid can be used in ash leaching, tall oil production or chlorine dioxide production.
Sulfuric acid plant start-up and operation
The first Valmet Sulfuric Acid Plant at the Äänekoski Bioproduct mill consists of a CNCG incinerator, catalytic converter, condensing tower, and a bisulfite scrubber including product storage tanks. The production capacity of the plant is approximately 35 tons of sulfuric acid per day, and it can produce higher quantities depending on the incoming non-condensable gases sulfur content. This is the world's first larger scale sulfuric acid plant that is being operated at a pulp mill. This plant produces high quality sulfuric acid that can be used in any part of the mill.
Starting up new sulfuric acid plant at a pulp mills is challenging due to corrosive and hazardous nature of SO3 and H2SO4. Therefore, properties of these chemicals and the process conditions must be well understood already during the design phase of the plant. In addition, the process is required to be in coherence with all other mill processes, because of its versatile role at the pulp mill. The produced acid can be used in bleaching, chlorine dioxide production plant, tall oil production, pH control and waste water treatment plant. Internally produced sulfuric acid reduces the cost of externally purchased acid, increases the environmental advantages and helps in closing the mill chemical balances. Sulfuric acid plant is one step closer to achieving the realization of future biorefinery concepts.
Sulfuric acid plant at Metsä group Bioproduct mill, Äänekoski, Finland
Effect of the Sulfuric Acid Plant on mill chemical balance
In old and new pulp mills, sodium losses are higher than input to pulp mill chemical recovery cycle. Additional sodium required to make-up the losses and NaOH is used as make up in most of the cases. This is quite opposite in case of sulfur, i.e. incoming sulfur is higher than out going sulfur, due to this reason, excess sulfur is removed from the recovery process by purging recovery boiler’s ESP ash and this action increases environmental load. ESP ash mainly contains Na2SO4. Therefore, Na is removed when sulfur is removed. Every kg S/ADt surplus takes out 1,4 kg Na/Adt (=2,5 kg NaOH/Adt) and in most of the cases NaOH is costly make up. In order to avoid sodium losses due to sulfur purge, it is indeed beneficial to produce sulfuric acid with internal sources such as NCG and use at the pulp mill by substituting externally purchased acid.
The savings come from reduced NaOH costs, externally purchased acid costs, environmental benefits and one step closer to realization of closing pulp mill chemical cycle.
Conclusions
The production of sulfuric acid from pulp mill non-condensable gases enables the bioproduct mill to become nearly self-sufficient in sulfuric acid usage. Sulfuric acid plant brings significant environmental advantages, one of them was the amount of sulfate lead to the mill's effluent treatment plant has been reduced and the sulfate load in the nearby waterways was decreased drastically. The CNCG incineration plant can be used as a back-up boiler for producing process steam by incinerating CNCG, tall oil pitch and/or liquid methanol. This innovative plant can produce sulfuric acid and bisulfite simultaneously depending on the requirement.
Authors: Tero Juutilainen, Pilvi Uurinmäki, Asta Humalajoki, Guilhermo Magalhaes and Thomas Timmer
This article is a summary of a paper which will be presented at the International Chemical Recovery Conference ICRC in Brazil in 2021. The presentation will cover the production of sulfuric acid from NCG incineration, environmental advantages, financial gains, operational experience, and the strategies to close mill chemical balances with sulfuric acid plant as well as presenting further improvements for chemical balance management.
Related articles