Reaching new heights in efficiency and stability
Dec 5, 2024
Sun Paper’s Beihai mill reaches new levels of production with the start-up of new bleached chemi-thermomechanical pulp (BCTMP) and bleached hardwood kraft pulp (BHKP) lines, and a Valmet Recovery Boiler.

Sun Paper and Valmet have continuously deepened their cooperation for more than 25 years. Their partnership has evolved from more than ten paper machine production lines for high-grade fine paper, coated paper, and cartonboard to pulping production lines for dissolving pulp, bleached chemi-thermomechanical pulp, and chemical pulp.
“Sun Paper’s collaboration with Valmet began in 1999 with the launch of the Sun cartonboard PM 17, and Valmet’s technology has since significantly contributed to the group’s sustainable development,” says Ying Guangdong, Chief Engineer and Deputy General Manager of Shandong Sun Paper Co., Ltd.
In 2021, the Beihai mill started up a BCTMP line and a BHKP line, both supplied by Valmet. Valmet’s flow control technology supports both lines, with a total of 2,659 Valmet valves applied to key positions. Meticulous preparation and close cooperation with Valmet ensured the success of both start-ups, and there is a Valmet Recovery Boiler at the heart of the mill, which is central to its energy system.
Highly efficient BHKP production
At the end of 2021, the Beihai mill’s BHKP line successfully commenced operations. The chemical pulp produced by the new line is currently utilized in their PM 1, BM 2, PM 3, and tissue paper machines. It boasts a daily production capacity of 2,650 air-dried tonnes of BHKP, making it Sun Paper’s highest-capacity chemical pulp line to date.
The Beihai mill’s BHKP line is Sun Paper’s highest-capacity chemical pulp line to date
“From commissioning to successful start-up, pulp production was achieved in just 10 days,” says Dai Zhongying, Director of Chemical Pulp Production, Guangxi Sun Paper Co., Ltd.
The BHKP line utilizes Valmet’s Continuous Cooking G3 dual-tower low-temperature digesting technology.
![]() |
![]() |
The chemical pulp line features the fifth-generation Valmet TwinRoll Presses. |
“The APC allows precise adjustments of key parameters, including alkali use, steam addition, and liquid ratio," says Dr. Li Zhi. |
![]() |
![]() |
“From commissioning to successful start-up, pulp production was achieved in just 10 days,” says Dai Zhongying, pictured with Eva Engelfeldt, Senior Sales Manager Pulp & Energy, Pulp Sales, Valmet. |
The bleaching tower. |
Superior chemical pulp quality
The BHKP line utilizes Valmet’s Continuous Cooking G3 dual-tower low-temperature digesting technology, as well as fifth-generation Valmet TwinRoll Presses, with six units in the screening section and four in the bleaching section. It also incorporates a Valmet Advanced Process Control (APC) digesting section system for the real-time monitoring, adjustment, and optimization of the production process. “The APC allows precise adjustments of key parameters, including alkali use, steam addition, and liquid ratio. It maintains the stability of operating parameters, which is crucial for ensuring the consistency of the digesting process,” says Dr. Li Zhi, Deputy Director of Chemical Pulp Production at Guangxi Sun Paper Co., Ltd.
"Valmet’s technology has significantly contributed to the group’s sustainable development,” says Ying Guangdong, Chief Engineer and Deputy General Manager of Shandong Sun Paper Co., Ltd.
Record start-up for BCTMP line
The Sun Paper Beihai mill also started up a BCTMP line in 2021, and with a daily capacity of 1,850 air-dried tonnes, it is the largest single BCTMP line in China up to now.
“The most critical success factor lies in sincere cooperation between both parties,” says Wang Dong, Director of BCTMP Production at Guangxi Sun Paper Co., Ltd. “Valmet coordinated the onsite installation and commissioning remarkably quickly: The TwinRoll press set a record for the fastest installation, and the high-consistency refiner was successfully started up just two weeks after its arrival.”
The Sun Paper Beihai mill's BCTMP line is the largest single BCTMP line in China
Sun Paper’s Behai BCTMP line currently supplies pulp to their cartonboard paper machine, which has an annual capacity of one million tonnes. “The excellent bulk and tensile strength of our pulp meet the paper machine’s high-quality requirements, enabling the production of superior paper metrics with minimal fiber use,” says Wang Dong confidently.
![]() |
![]() |
The BCTMP line. |
Valmet OptiFiner RF-5 Low-Consistency Refiner. |
![]() |
![]() |
Wu Zhuang (left), Duty Supervisor of the BCTMP line at Guangxi Sun Paper Co., Ltd, and Qin Haichao (right), BCTMP Process Technology Manager at Valmet, posing in front of the finished pulp on the BCTMP line. |
“The excellent bulk and tensile strength of our pulp meet the paper machine’s high-quality requirements, enabling the production of superior paper metrics with minimal fiber use,” says Wang Dong, pictured with Haichao Qin, Technology Manager, Services, Pulp & Energy Solutions, China, Valmet. |
Excellent operational stability
Valmet’s two-stage bleaching process in the Sun Paper Beihai BCTMP line, which involves medium-consistency bleaching followed by washing and high-consistency bleaching, has proven exceptionally effective at enhancing brightness. Key technologies and equipment in the line include Valmet TwinRoll Presses, Valmet RGP-82 CD high-consistency refiners, and Valmet OptiFiner RF-5 low-consistency refiners.
Valmet’s flow control technology supports both lines, with a total of 2,659 Valmet valves applied to key positions.
Making continuous strides forward
The close cooperation between Sun Paper and Valmet is steadily propelling Sun Paper’s Beihai mill forward, laying a solid foundation for a greener, more efficient, and harmonious future. “We’ve made significant strides in ESG (Environmental, Social, and Governance) initiatives. On the environmental front, we’re not only committed to continuous improvement but have also successfully achieved ongoing reductions in COD emissions and a steady decrease in the use of fossil fuels,” concludes Ying Guangdong.
Text Dana Zhu and Silvia Xi
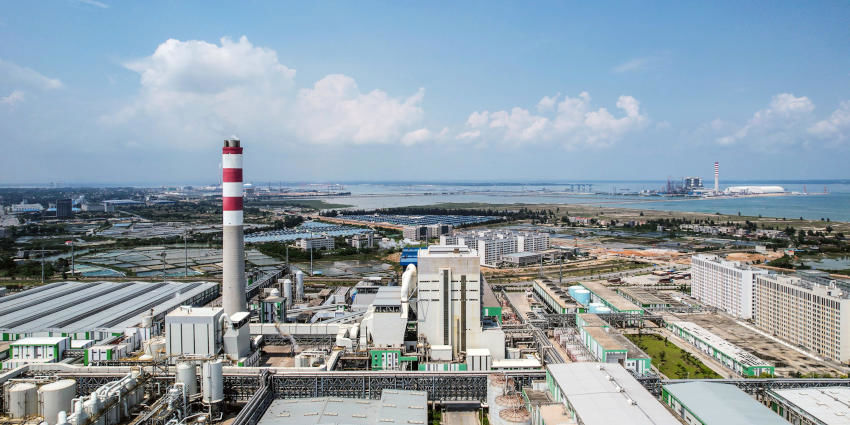
Exceptional recovery boiler performance
The Beihai mill depends significantly on biomass energy, which generates 85 percent of its total steam supply. The Valmet Recovery Boiler commissioned at the end of 2021 is central to the mill’s energy system. With its cutting-edge design and efficient energy utilization, the boiler can generate up to 720 tonnes of high-pressure steam per hour.
“The recovery boiler consistently demonstrates stable production operations and maintains reliable environmental performance,” says Dai Zhongying.
“Valmet has enabled us to significantly reduce our water, electricity, and steam consumption,” adds Ying Guangdong.