Successful press section rebuild at Fibre Excellence SAS Provence in France
Jan 10, 2025
A press section rebuild has successfully started up on April 2nd 2024 at Fibre Excellence SAS Provence mill in Tarascon, France. The rebuild was a part of a modernization plan, which included 180 million euros of investments over four years, to upgrade the plant to the highest industrial and environmental standards.
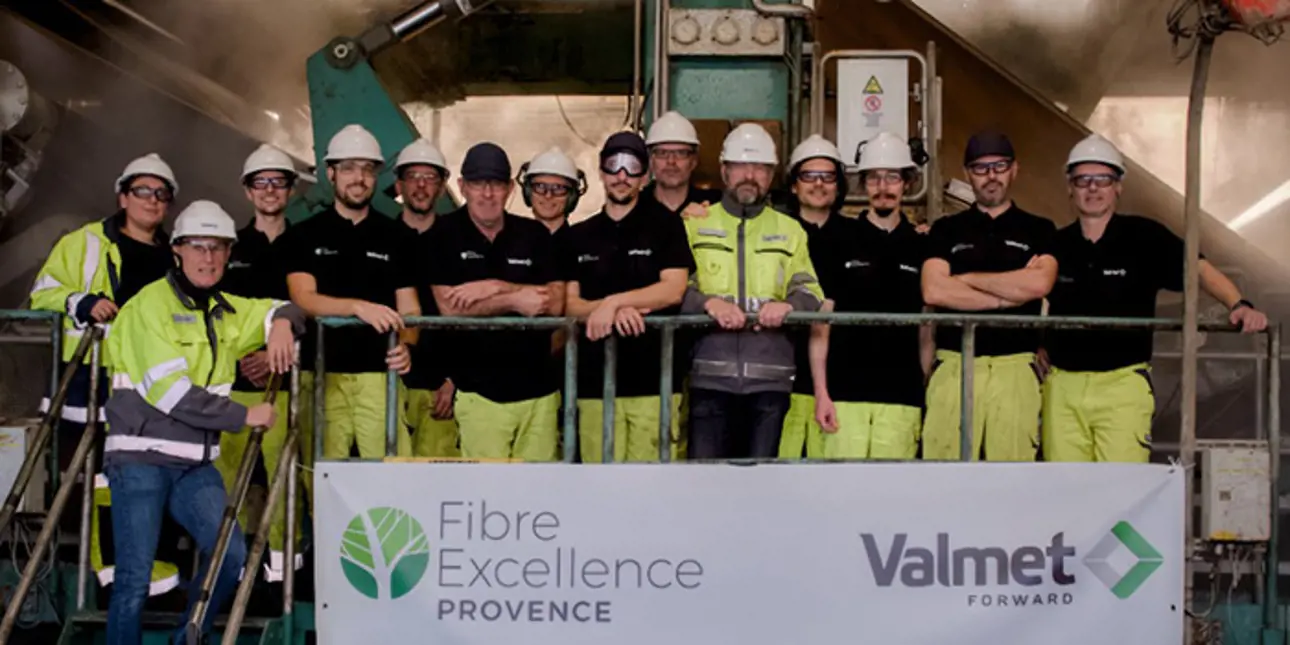
Valmet’s delivery for press section rebuild included new top feltings, patented Valmet Pressurized Felt Conditioning System, felts and a new lump breaker roll. Spare parts, mechanical erection of supplied equipment, and site advisory services were also included.
“In 2020, we initiated a partnership aimed at debottlenecking the pulp dryer. The rebuild of the press section was a decisive step in this process. The performance achieved has exceeded our common objectives,” said Yannick Duperrier, Senior Mill Sales Manager at Valmet.
Jussi Hyvönen, Sales Manager, Pulp Drying at Valmet, explained the benefits of the new press section: “The machine is designed for unbleached softwood kraft pulp (UKP). With this investment, the dryness out of press section increases and machine runnability improves. The new parts have a design capacity of 900 air-dried tons per day, to be prepared for future capacity increases.”
Smooth startup and excellent results through seamless cooperation
The installation of the new press section at Fibre Excellence SAS Provence mill was completed on schedule, thanks to careful planning and effective teamwork. The successful implementation of the new Pressurized Felt Conditioning System further highlighted the team’s adaptability. The project met its targets, and the pulp drying line is no longer a bottleneck in production.
Denis Houdault, Product Sales Manager, Fabrics at Valmet, shared the challenge and successes: “Installing the first top felt through two nips was quite challenging. However, tail threading was completed swiftly, and with a few adjustments, we achieved high dryness levels after the press section.”
“During the start up, it was obvious that the dryness had improved, as we noticed considerable changes in the draws between the presses. We also observed during the tail threading that the web was a lot stronger after the third press,” said Cédric Barrat, Pulp Dryer Superintendent at Fibre Excellence SAS Provence. “We learned how to operate the new felt conditioning system, and in the end, it turned out to be pretty simple and effective design.”
Petteri Kivirauma, Project Manager at Valmet, concluded: “With good planning and the dedication of Valmet professionals and contractors, the installation and annual service overhaul were completed on schedule. The startup proceeded smoothly, thanks to the cooperation of the mill’s production personnel.”
Time to celebrate
In the beginning of December 2024, a coffee and cake event was arranged at the customer site to celebrate the successful press section rebuild. This event provided an excellent opportunity for the teams to come together, enjoy some sweets, and share the success of the common project. The atmosphere was filled with joy, making it a memorable for all participants.
Valmet Pressurized Felt Conditioning System challenging industry standards
The Pressurized Felt Conditioning system is a unique solution designed to replace conventional vacuum pump-based systems. By blowing low-pressurized air through the press section, it effectively dewaters the press felts. The system offers easy adjustments to meet various dewatering requirements, providing full-range control over air pressures and volumes for maximum flexibility.
Combining efficiency, sustainability, and cost-effectiveness, the Pressurized Felt Conditioning System is an ideal choice for modern pulp mills. It significantly reduces electrical power consumption by up to 50 % compared to typical vacuum-based systems and achieves 100 % savings in water consumption.
The system features lower investment costs, and achieves significant savings in process systems parts and installation costs. Additionally, the blowers take up less space than vacuum pumps, and they can be freely located in the machine hall, with the possibility to connect several felts to the same blowing unit.
The press section rebuild at Fibre Excellence SAS Provence wasn’t just an engineering exercise; it was a commitment to sustainability and operational excellence. By challenging industry standards and embracing innovation, this pulp mill can create a greener, more efficient future — one rebuild at a time.
Information about the customer Fibre Excellence Provence SAS
Fibre Excellence PROVENCE mill produces around 250,000 tons of pulp per year, which is processed into many everyday products: hygiene products, packaging, filter paper, etc. It employs over 250 people and generates over 5,000 indirect jobs in the region, particularly in industry and in the forestry sector. The mill therefore injects an additional 100 million euros into the local economy every year. Located in Tarascon since 1951, the mill has been continually modernized to meet changing regulatory standards and improve its industrial processes.