Klabin's PUMA pulp project: largest private investment in Brazilian Paraná state
The construction of a large-scale pulp facility is not an easy task. A greenfield project includes tonnes of equipment and thousands of people, from the project design phase to groundbreaking works, erection, commissioning, and the final start-up process. The key is to successfully gather different stakeholders from multidisciplinary teams.
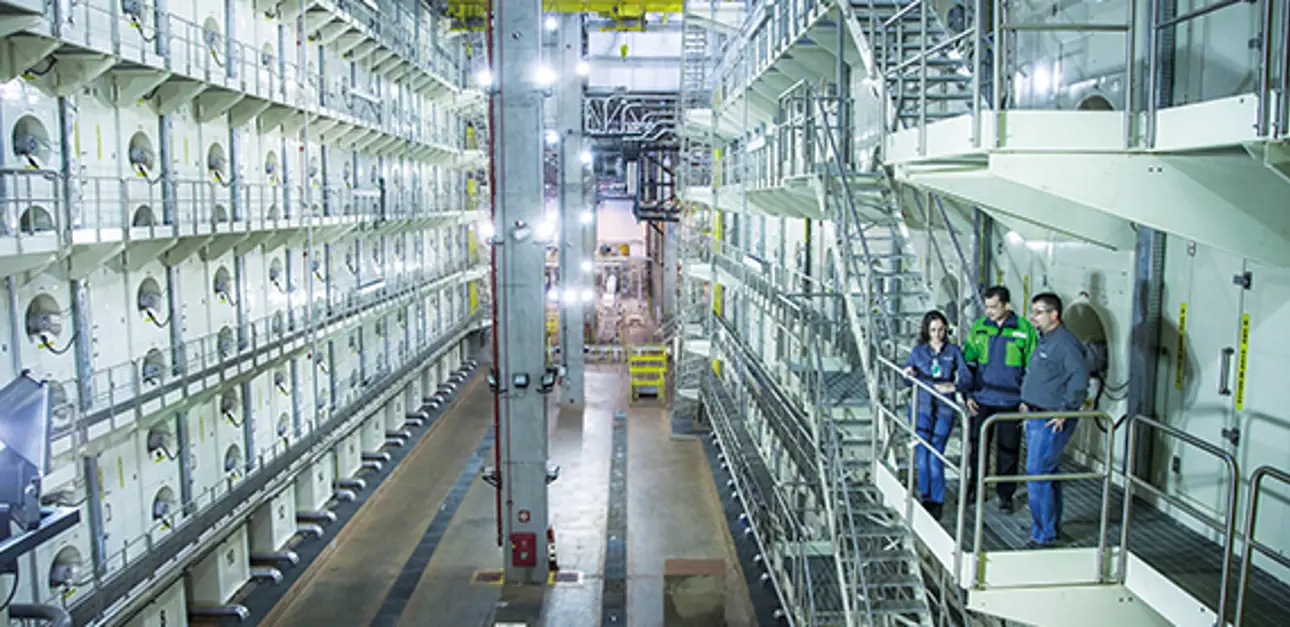
A combination of broad technological knowhow, innovation and a strong presence in Brazil made Valmet the best choice for supplying the pulp drying lines for one of the biggest pulp projects worldwide: Klabin’s PUMA pulp mill project, located in Ortigueira municipality, in the Brazilian Paraná state.
The R$ 8.5 billion (EUR 2.2 billion) Klabin PUMA new pulp mill investment started up in March 2016 and comprised world-class Valmet technology for pulp manufacturing. The overall project challenges and deadlines were successfully met, providing technology which is undoubtedly a game changer for Klabin’s business strategy. The PUMA project has achieved a simultaneous output of 1.1 million tonnes/year of bleached hardwood pulp and 400 thousand tonnes/year of bleached softwood and fluff pulp. The facility was designed to produce 270 MW of electricity, consuming 120 MW internally and exporting up to 150 MW to the Brazilian national grid, using 100% renewable fuels based on wood, tree bark and lignin.
Fluff and softwood market pulp as end products
The Valmet scope of supply included two drying machines, baling and roll finishing lines. “This project was different in many ways. At same time, it included one of the biggest and highest capacity machines in the world, with 9.5 meters of width and a capacity of 3,500 tonnes per day, side by side with the first drying machine designed to produce both fluff and softwood market pulp in South America. The same machine can produce rolls and bales, depending on the product that the customer requires,” explains Paulo Aguiar, Valmet’s Director of Pulp Drying technology. The supply also included two winders and fully automated roll handling with plastic wrapping to handle fluff production with special care.
Tests on Valmet pilot machine for optimum sheet formation
“Fluff is a product that requires high quality and additional physical properties than those measured in normal market pulp. Klabin has invested in research and development to ensure that we would have the best product available since we were entering a new market and looking forward to achieving differentiation in quality,” Klabin’s Technology and Pulp Business Unit Director Francisco Razzolini states. “At same time, we wanted to have a flexible machine, to produce a high capacity of softwood market pulp, without sacrificing the fluff quality. We worked with Valmet in their pilot machine located in Sweden to determine the optimum design in the sheet formation that would allow the best for both products,” he adds.
The product development didn’t stop in the forming section. The machine was also equipped with caliper control that assures parallel jumbo rolls, which is crucial for good operation of the winders. It may seem simple to achieve on a paper machine, but in a drying machine where the grammage is 10 times higher than paper, it is not an easy task. “We have developed the project to produce fluff with low defibration energy properties, one of the most valued parameters in the market,” comments Sadi Oliveira, Klabin Ortigueira’s Industrial Director. “The line is also fully automated, with minimal operator interference. This applies to everything from jumbo roll transportation to the packaging lines, prioritizing the safety in our operations,” he adds.
Committed to the environment
The PUMA project was developed using the best available technology focused on the reduction of environmental impacts, as well as the use of raw materials from planted and certified forests, socioeconomic development of nearby communities, health and occupational safety and innovation, among other aspects.
Concerning environmental aspects, a dedicated team surveyed the pre-established conditions and monitored the environmental impacts in the region of the new plant during the construction phase, testing and start-up. The atmospheric conditions, noise generated, fauna, and water quality were all fully monitored to mitigate any possible impacts on nearby communities during all stages of the construction.
The environmental investment included the installation of a Solid Waste Treatment Plant, which aims to separate traditional reusable materials (fibers, sludges, grits, dregs) from other industrial waste, promoting its use in composites, minimizing the needs for industrial landfill.
For the construction phase, a structure was set up for the use of labor in the region, with the application of training courses and prioritizing of the use of the regional workforce whenever the professionals sought were available. “In the civil construction phase, about 80% of the construction workers were from the State of Paraná, and even in the electromechanical assembly phase, which demanded very highly-skilled professionals, local workers accounted for 50% of the workforce,” Klabin’s Project Manager João Antonio Gomes Braga says.
Committed to the municipality
The PUMA pulp project was the highest private-sector investment ever made in Paraná, including infrastructure and recoverable taxes, and construction was completed in 25 months and remained well within the initial budget.
The overall construction phase generated R$ 700 million (EUR 184 million) in taxes. The facility is expected to pay R$ 300 million (EUR 79 million) in taxes annually, generating a great deal of value to local communities. “The new pulp mill and forestry operations generated 1,400 new jobs. Around 40,000 workers went through the works,” Francisco Razzolini says.
Social responsibility
In order to determine its social investments, in 2012 Klabin conducted a social diagnosis of the municipalities of Ortigueira, Imbaú and Telêmaco Borba, which represented the PUMA pulp mill’s direct area of influence. Through a broad participatory process that involved many different stakeholders in urban and rural areas, Klabin developed the Puma Project’s Social and Environmental Action Plan, which comprised various initiatives in the areas of health, education, culture, recreation, the environment, family farming, etc.
A long-term partnership
The partnership between Valmet and Klabin is not limited to the project. Klabin has outsourced the drying machine maintenance to Valmet during the first three years of operation. A team of 17 people work inside the mill, aiming to maximize availability and machine efficiency. These people can also count on Valmet’s specialists for remote access.