Boosting production capacity at Estonian Cell
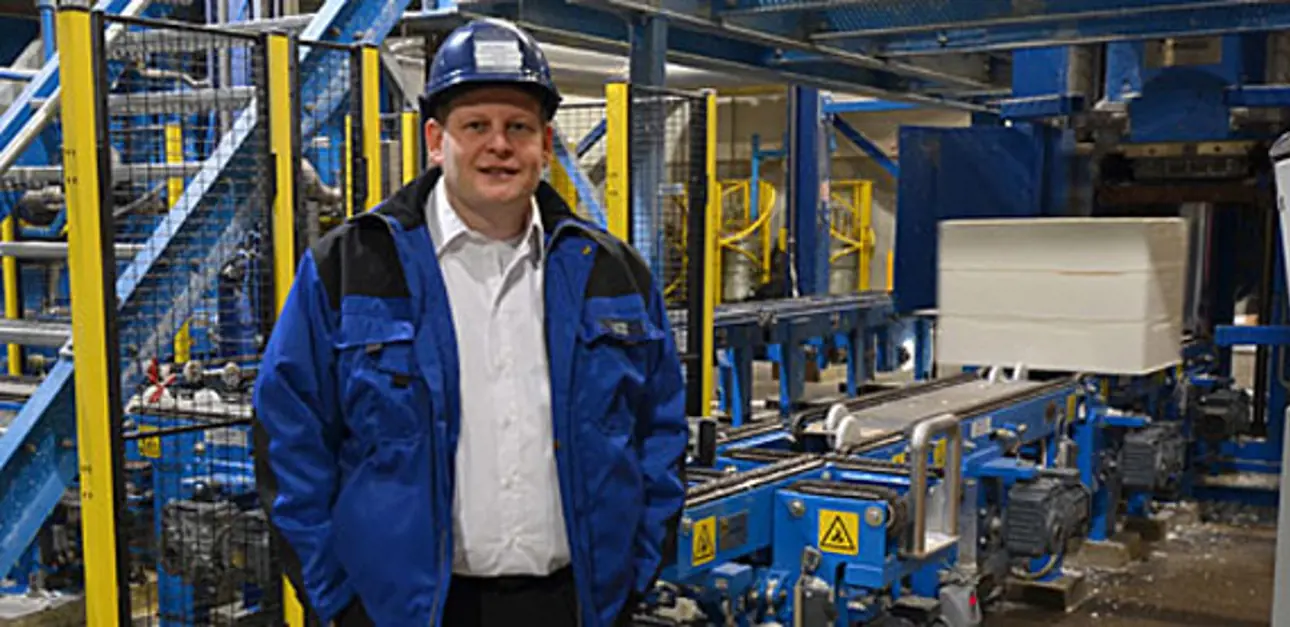
Lauri Raid, Mill Manager of Estonian Cell, is satisfied with the results of the slab press and partial baling line upgrade at the mill.
Estonian Cell, the only European pulp mill sourcing products solely from aspen, wanted to boost the capacity of its single baling line and improve availability in continuous shift production.
A new slab press and partial baling line upgrade from Valmet have now been integrated successfully into the existing line – a project that has played a major role in fulfilling Estonian Cell’s strategic investment plan to ensure the pulp mill’s financial sustainability.
Estonian Cell has become Europe’s largest producer of aspen BCTMP (Bleached Chemo Thermo Mechanical Pulp) since it opened in 2006. However, rapidly rising electricity costs and production bottlenecks adversely affected financial results, increasing the company’s cumulative net losses, particularly in 2012 and 2013. Estonian Cell responded with a bold strategic investment plan. This included the slab press investment and a new, innovative anaerobic effluent treatment phase that will reduce the mill’s electricity consumption by providing biogas for use in production.
One of the most important investments to improve the company’s financial results was the contract with Valmet to expand the baling line in order to significantly increase production volumes and reduce costs,“ says Lauri Raid, Mill Manager, CTO and board member of Estonian Cell.
Valmet's new slab press in operation.
Estonia is one of only a handful of countries that has over 50% forest cover. Around 8% of those forest resources are aspen. Estonian Cell produces high-quality grades of aspen BCTMP, which are used as additives to optimize aspects such as brightness, opacity and bulk, primarily in printing and writing papers.
The pulp mill, located in Kunda, 110 kilometres east of Estonia’s capital, Tallinn, was originally designed to produce 140,000 tons of aspen BCTMP annually in an eco-friendly, sulphur-free process with chlorine-free bleaching.
“It was defined from the start as a single line concept from a single source supplier, says Lauri Raid. “Achieving maximum capacity from that single line was vital. The original slab press was a prototype that did not meet our stability expectations. Trying to squeeze out extra tons compromised availability and production became increasingly unstable and costly.”
“The investment in a new slab press became even more critical considering the losses the company was making,” continued Lauri Raid. ”So, increasing capacity and gaining the related cost savings was the top priority. We wanted to tackle availability issues and equipment-related breakdowns and reduce maintenance costs. We also had three other objectives: improve the appearance of our bale wrappers, go from double to single wiring on bales and offer customers a big bale option.”
Estonian Cell began discussions with Valmet in 2010. The company’s expertise as a world-leading supplier of slab press and baling technology for the pulp and paper industry played a major role in being selected to supply the line upgrade. “Estonian Cell wants to be first with new and better solutions,“ emphasizes Lauri Raid, “We saw that Valmet has no competition in terms of baling lines.”
At the heart of the reconfigured line is Valmet’s Slab Press PFE, the latest version of the automatic bale-forming machine for flash dried pulp that has been supplied to over 70 pulp mills worldwide.
Lauri Raid explains that the new solution has solved previous precompaction issues: “Uneven delivery of pulp to the slab press had been a major problem. If you start to compact the bale too early, all the other problems start from there. Valmet’s double screw solution provides better, more even delivery of pulp to the press and was the best design for achieving higher capacity.”
In addition to the new slab press, the upgrade project at Estonian Cell also
included a partial rebuild of the baling line.
However, the challenge for Valmet was not simply to replace the slab press. “We wanted to retain some of the machinery from the old line and incorporate new machines,” comments Lauri Raid. “We also wanted the option to use both the old and new press to feed the same baling line – so the new press was to be installed alongside the old one.”
In 2011 Estonian Cell came under the sole ownership of the Austrian Heinzel Group. A year later Valmet got the go ahead to design, supply and erect a slab press and partial baling line to produce over 500 air dried tonnes of aspen BCTMP per day.
Estonian Cell’s Project Manager, Toomas Kask, outlined the practical challenges involved: “It is unusual to put a new slab press next to an existing one and mixing another manufacturer’s equipment into a working line is always a challenge, especially integrating the software for the old and new control systems.”
Valmet’s start-up team was on site at Estonian Cell for three weeks in the summer of 2013. The team’s tasks included the erection of the new 80-ton slab press, which was carried out according to plan while the existing line was in operation.
“The Valmet team was highly professional and cooperative. They were also very flexible. If unforeseen problems arose we were able to find solutions together,” says Toomas Kask. One of the more unusual new line elements installed by the Valmet team was a massive, upper pulp distribution screw for splitting pulp flow from the flash drier to the two presses. This 10-metre version is considerably longer than the 6-metre distribution screws Valmet has installed at other mills.
“Originally, we thought we would have to build a new cooling tower for the new press,“ explains Lauri Raid. “Valmet was the only supplier with experience of distribution screws and this solution has substantially reduced project costs.”
The new slab press has been operating since July 2013. Although the old press currently stands idle, reincorporating it in production remains an option for the future.
From the new slab press, bales are fed via a Valmet-supplied L-shaped conveyor system to link up with the existing bale press. New and original machinery is interspersed throughout the line. Additions include Valmet’s RoboApplier and RoboFolder machines to provide efficient bale wrapper application and folding. Valmet’s RoboHightyer increases bale options by producing “big bales” consisting of two non-wrapped standard bales for use in large industrial pulping applications.
Routine maintenance has become easier, according to Maintenance Manager, Olev Kaarlop: “I think the whole conception of the new press is much better in technical terms. It is a simpler design with fewer wear parts and much easier to deal with.”
Alari Rebane gives the operator’s perspective: “Production is much more stable and there are fewer problems to deal with. As the press works automatically, there is no need to make manual corrections as before. My working environment is better too, the press is a lot quieter and dust emissions have been considerably reduced.”
“All our targets are being achieved,” says a satisfied Lauri Raid. “Our bale wrappers look smarter, using single bales wires has cut wire costs and means less dewiring for customers, and we can now offer the big bale option. It’s too early to assess maintenance costs, but it looks promising. Production stability is good and we have met our internal availability targets.”
“Most importantly, our top priority has been achieved. Our target capacity has been easily reached in accordance with the performance guarantees. In fact, we recently beat our one-day capacity record by producing 557 tons and are well on course to meet our target of 165,000 tonnes for 2014,” concludes Lauri Raid.