Ensuring a smooth pulp drying process
The Vulindela project is an overall expansion project at the Sappi Saiccor mill in South Africa. It will increase the mill’s total output by 110,000 tonnes of dissolving pulp per annum while reducing its environmental footprint. As part of this project, Valmet helped Sappi overcome a bottleneck in their baling line.
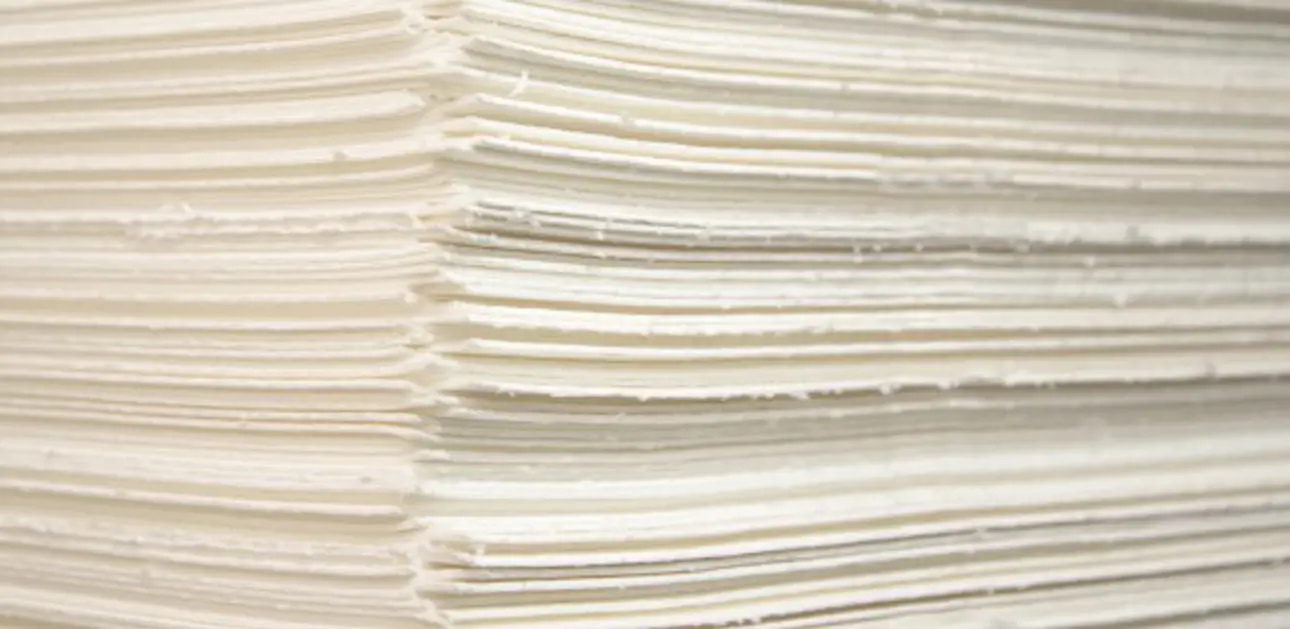
The Saiccor C4 pulp dryer is a legacy Valmet machine which makes specialized cellulose pulp for aftermarket use. The mill exports the pulp in either bale or reel form to various customers.
Valmet rebuilt the sheet cutter and installed the new baling line during the annual shutdown.
As part of the mill’s Vulindela expansion project, Sappi had identified that their existing C4 baling line was creating a bottleneck in their pulp drying line. To overcome this challenge, Valmet was chosen to deliver a second modern baling line alongside the existing baling line.
New baling line and rebuild of sheet cutter roll pair
The project included the installation of a new baling line and the rebuild of the aging sheet cutter roll pair. As part of the rebuild, the sheet cutter was replaced with a double blade knife cutter, while the existing water heating system was retained for use with the new cutter rolls. The rebuild also included the replacement of the feed rollers and pull rollers on the cutter layboy. The new baling line includes conveyors, a bale press, inkjet marker, wrapper applyer, wrapper folder, rotating unit, bale stacker, wire tyers and a unitizer.
Final installation during annual shutdown
The new line was built alongside the existing baling line, and much of the base equipment was installed before the actual shutdown. This was successfully installed during the older line’s normal production.
The new baling line.
The final installation of equipment and the start-up were accomplished during the annual shutdown of the C4 machine line, which lasted approximately two weeks. During the installation, Valmet provided four on-site installation specialists, and Sappi provided a team from a locally sourced rigging company. The project site leader was from East Asia, while the Valmet site engineers were from Sweden.
Strong focus on safety
The Sappi and Valmet teams met regularly to keep the project on track and ensure that all installation work and preparation were carried out safely. To meet Sappi’s strict safety requirements, the entire new line is enclosed in a safety zone. Access to the safety zone is PLC controlled, including not only physical barriers and safety fences but passive electronic safety beam sensors.
Good training ensured the operators quickly became comfortable with the new line.
Training to ensure smooth operation
The Sappi crew started their training early in the shutdown to ensure each operator could understand the process and get used to the layout and the new touch screen operation. This enabled them to quickly become comfortable with operating the new line.
“The cooperation between Sappi and Valmet ensured the project was successfully completed,” says Sappi Project Director Wayne Weston.
As planned, the new baling line’s capacity is higher than that of the C 4 pulp drying line, so the baling line is no longer a bottleneck.
“The cooperation between Sappi and Valmet ensured the project was successfully completed even though the Covid-19 pandemic presented unexpected challenges and required new methods and processes,” says Sappi Project Director Wayne Weston.
Text Kevin McQueen
PHOTOS Patrik Tjärnström