Dissolving pulp has a bright future at Sappi
Clothing made from wood is a growing trend. And dissolving wood pulp (DWP) is the key contributor to this development, since it can be made from all kinds of tree species.
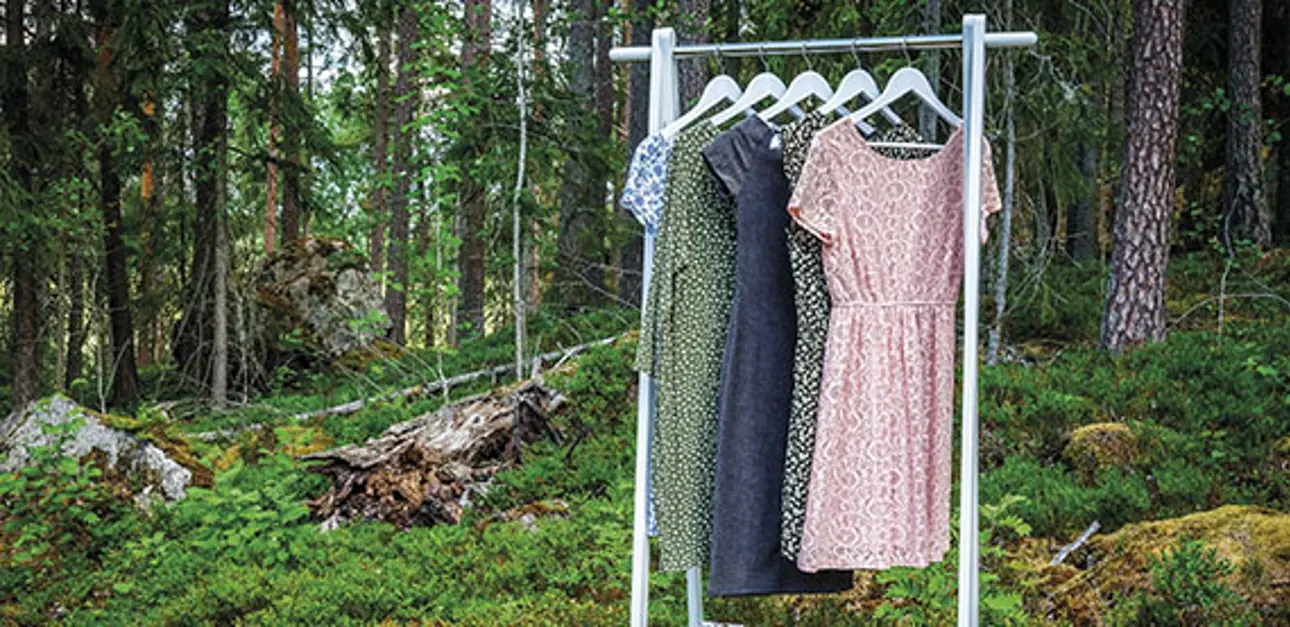
Sappi, the South Africa-headquartered pulp and paper producer, is the largest non-integrated producer of DWP in the world. The company currently produces 1.4 million metric tons a year, giving it a global market share of approximately 16 percent. We recently spoke with Tracy Wessels, General Manager Technical for DWP, about the company’s optimistic outlook on the sector and how they are positioning their new brand, Verve.
Why is Sappi so excited about DWP?
We are tightly linked to the growing textile value chain, which is showing positive growth in both organic market growth, and just as importantly, in substitution growth from less-sustainable textile fibers. Our capacity and our geographical production-site mix are well aligned to service this market growth, and we will certainly remain a key player within some of those market segments, notably viscose and lyocell. In addition, in South Africa we are sustainably supplied by our own commercial forest lands and we have robust and strict wood sourcing policies for our North American mill, which adds another level of sustainable advantage.
Today, environmental and ethical performance, as well as transparency within the textile value chain, are major focus areas, as brand owners are driving sustainable sourcing as a means of differentiation. We too are differentiating with the recent introduction of our new Verve brand of DWP, which is produced from sustainably sourced wood carrying with it a number of recognized certifications.
Regarding Verve, how are you allying with leading partners, and what benefits do they get?
Sappi has for many years worked with a strategic model to partner and collaborate with the leaders in the markets we supply, and Valmet is one of our long-term partners. We work closely with key customers to ensure optimum pulp performance compatibility with their specific processing equipment and conditions. Essentially, we “tailor” our production processes to ensure it is “fit-for-use weekend pulp,” with consistent pulp quality.
Moving forward, Verve is now extending these relationships outside our direct supply chain and engaging with key leaders in a number of disciplines, from analytics to supply chain understanding, as well as systems implementation for ease of doing business, through to NGO membership and collaboration with the aim of contributing positively to the entire value chain’s sustainability credentials. This not only due to the fact that wood based cellulosics are by their nature a more sustainable choice than other textile raw materials, but also by continuously improving the sustainability of this raw material.
Can you explain your term “weekend pulp”?
“Weekend pulp” is a term coined by one of our longstanding customers and is in reference to the consistency in pulp performance that Verve offers. The comment from our customer was that they prefer to run Sappi Verve pulp over the weekends, since they feel confident that they only need to provide minimal process support resources and have the assurance of stable performance. We think this term perfectly embodies our mission to provide top-quality, consistently performing products to our customers.
Valmet was the key technology supplier to the pilot demo plant at the Ngodwana Mill in South Africa. What progress have you made so far?
The aim was to explore and optimize the possible extraction of bio-renewable chemicals. The plant is close to industrial size and makes it possible to test new ideas and study the next-generation dissolving cooking process at close to mill scale. Everything in this project worked well from the start, based on a very good partnership with Valmet. We rapidly produced top-quality pulp and reached our targets. The learnings gained from the plant regarding extraction of hemicelluloses from the wood during prehydrolysis have been invaluable and given us the confidence to approve the scale up of our Xylex® technology for the production of xylitol and furfural. Therefore, we are currently building a Xylex® demonstration plant adjacent to the digester demo plant at Ngodwana.
Valmet’s scope of supply
To date, Valmet has delivered 15 dissolving pulp plants. For pulp production, Valmet is the only equipment supplier offering both continuous and batch cooking options. Valmet’s scope of supply covers every process stage in a pulp mill, starting from handling the incoming wood up to ready-made pulp bales, or rolls, and also including entire chemical and heat recovery plants as well as mill-wide automation systems.
Article published in Forward magazine 1/2019.
Related articles