Metsä Group Äänekoski - The next generation bioproduct mill
Metsä Group’s new bioproduct mill takes pulp production to a new level. In the mill, every single bit of the wood raw material and production side streams are utilized to achieve maximum material and energy efficiency.
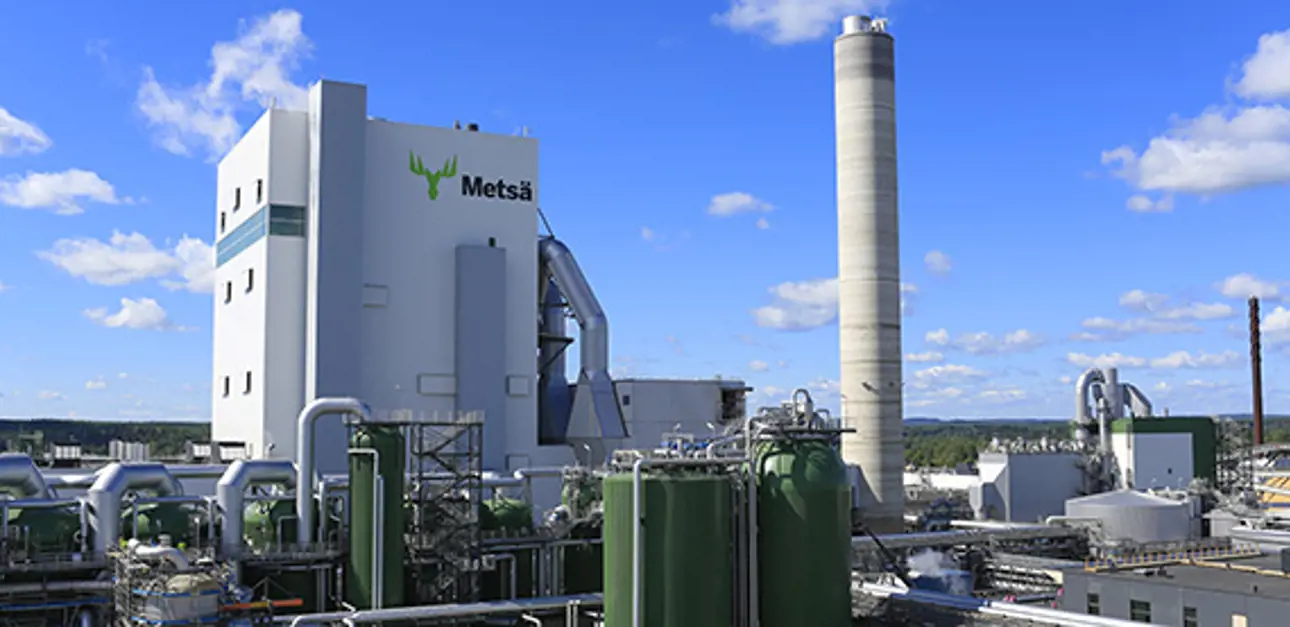
Äänekoski, a town of 19,000 people surrounded by lakes and vast softwood forests in Central Finland, is now home to Northern Europe's largest bioproduct mill. In April 2015, Metsä Group, a forest industry group focusing on tissue and cooking papers, paperboard, pulp and wood products, decided to replace their old pulp mill in the town with a modern, next generation bioproduct mill. At EUR 1.2 billion, Metsä Group's investment in Äänekoski is the largest investment in the history of the Finnish forest industry.
The old pulp mill had started production in 1985 and was therefore approaching the end of its operating life cycle. The choice was between a total renovation of the existing mill or then a new mill. The construction of the mill started in August 2015, and Valmet was chosen to supply some of the key technology islands to the new mill.
Timo Merikallio, Project Director from Metsä Group, and Camilla Wikström, SVP, Production, Pulp Business from Metsä Fibre
Metsä Group went through a traditional tendering process for the various key technology islands of the mill. "We have a long history of co-operating with Valmet at our pulp mills in Finland. Valmet has been a good and innovative partner for us. Valmet stood out from the competition by offering us the best technology within our budget, so it was a natural choice to partner with them when building the world-class bioproduct mill in Äänekoski," says Timo Merikallio, Project Director, Metsä Group.
The latest technology plays a key role
Metsä Group's decision to choose suppliers for the mill's key technologies was a deal for two. Valmet was chosen to deliver the recovery boiler, pulp drying line, gasification plant, lime kiln, sulfuric acid plant, and mill-wide automation system – all of it the latest technology and highly energy-efficient.
Äänekoski recovery boiler supplied by Valmet is equipped with several high-power features
The gasification plant produces biogas from bark, which replaces fossil fuels in the lime kiln. The pulp drying machine includes several new features that improve efficiency and usability. The largest part of the delivery was the recovery boiler with new high-power features. The boiler has a capacity of 7,200 t/ds and has an electricity production capacity of 250 MW. As a result, the mill can produce up to 1.4 times more electricity than it uses.
"The mill is a prime example of a contemporary bioproduct mill. In addition to high quality northern softwood and hardwood pulp, it produces other bioproducts. Also, it doesn't use any fossil fuels and it supplements Finland's total share of renewable energy by more than 2 percentage points," says Bertel Karlstedt, President of the Energy and Pulp business at Valmet.
Mutual trust brings success
Metsä Group and Valmet agreed that the technology deliveries would be made using a tailored open book working model. It meant that Valmet and Metsä Group practically sat on the same side of the table. Metsä Group bought the equipment and made subcontracting agreements, and Valmet steered and managed the operations at the site.
"The project was the largest I have ever headed. It was big, international and divided into hundreds of smaller contractor agreements. Our co-operation with the open book project model worked well. Valmet's ability to meet our requirements during the project was on a good level," says Merikallio.
"Mutual understanding and joint project goals are essential. Metsä Group had really experienced project personnel. Even though we had some challenges during the project, at no point did they question our ability to solve them within the given schedule," says Jari-Pekka Johansson, Valmet's Äänekoski Project Director. "Trust on both sides is crucial to achieve our common goals."
Bertel Karlstedt, President of the Energy and Pulp business at Valmet, and Jari-Pekka Johansson, Project Director from Valmet
Dedication to safety
The total number of construction and project personnel at the site peaked at 13,500 people. Metsä Group had set high safety standards already in the bidding process.
"Valmet's commitment to safety was noticed at an early stage. It showed also during the project through the resources Valmet appointed to the site. The accidents during the project were typically slips and trips. Our lost time accident rate was below 14 per million working hours, which can be categorized as a good result in a project like Äänekoski," says Camilla Wikström who was the mill manager at the time of construction and has been recently appointed to SVP, Production, Pulp Business, Metsä Fibre.
The high level of automation, e.g. automatic tail threading, in the drying machine allows the operators to start the machine with hands free, bringing safe and reliable operation.
"Safety was well managed and resources were well placed. For example, at the very demanding recovery boiler construction site with a lot of contractors, Valmet managed to work without any serious injuries. The attitude towards safety issues is the most important thing. With the right attitude, most accidents can be prevented, and Valmet demonstrated their ability to steer and handle health, safety and environmental issues well," continues Merikallio.
Optimizing performance with Valmet's automation
Metsä Group chose Valmet to deliver the key process technology and the mill-wide process automation system and related analyzers. The Valmet DNA automation system is the backbone of the entire mill and includes a secure back-up system for mill operations. Valmet also supplied a comprehensive information management solution that provides real-time data for maintenance and quality control.
Äänekoski mill has mill-wide automation solution with Valmet DNA and analyzers.
"The mill is equipped with 1,500 sensors that measure bearing vibration. Our automation service agreement provides weekly status reports for Metsä Group's maintenance personnel. This enables repairs and replacements before any breakdowns occur. Äänekoski mill also uses maintenance pads for easy access to information and reporting on the shop floor," says Tuomo Marjomaa, Senior Project Manager at Valmet.
Start-up right on time
In August 2017, the Äänekoski bioproduct mill was started up a couple of minutes before the schedule set already two years earlier. The mill produces 1.3 million tonnes of pulp per year, along with other bioproducts such as tall oil and turpentine.
"I think success in this project was a result of good time management, the open book working model, our decision-making culture and interaction between people," Jari-Pekka Johansson sums up.
"Projects like ours always include unexpected issues and challenges. We also had some, but the way Valmet handled them only increased my trust in them. I feel very positive as the mill has performed well and the ramp-up is nearly completed," says Timo Merikallio. "Building these kinds of mills is always a different combination of technologies, and there isn't only one way of doing it. I enjoyed working with Valmet; their professionalism and well-managed sourcing organization impressed me."
The high level of automation, e.g. automatic tail threading, in the drying machine allows the operators to start the machine with hands free, bringing safe and reliable operation.
TEXT Antti Ratia
PHOTOS Antti Ratia, Metsä Group and Tomi Parkkonen