APRIL/SSYMB Rizhao greenfield mill: One year of successful operation
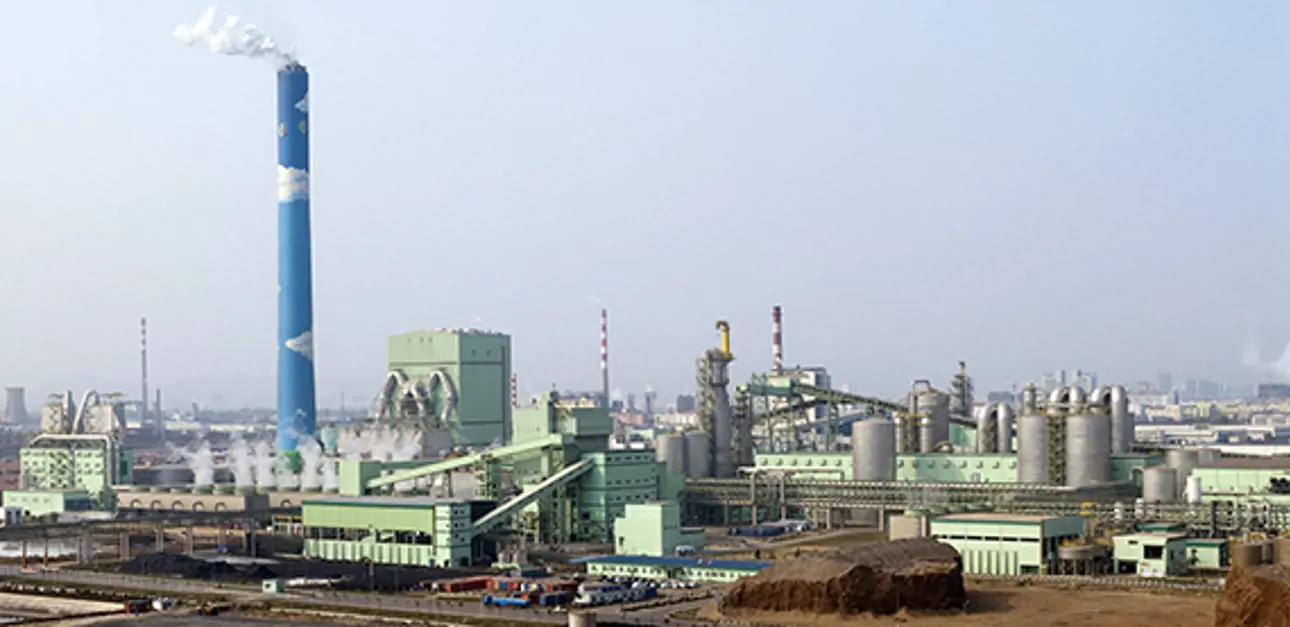
APRIL SSYMB Rizhao mill, the world's largest pulp mill situated in the heart of Rizhao city, has completed one full year of operation and produced over one million adt bleached pulp. On June 30, 2010, the mill produced it’s first pulp sheet. The mill has a state of the art ecofriendly and odorless production.
The start-up the greenfield kraft pulp line and chemical recovery process at the APRIL/SSYMB Rizhao mill in Shandong Province, China, went very quickly as can be seen from production achievement during one full year of operation. Everything is running according to plan, great accomplishment for this mega-sized kraft pulp mill.
The mill is a joint venture between APRIL (Asia Pacific Resources International) and local government
Valmet’s scope of supply included all main processes for kraft pulp production and chemical recovery. The delivery also included supervision services for erection and start-up, as well as training of mill staff.
A mega-sized kraft pulp mill
The pulping line is larger than any other line delivered anywhere else so far. This marks the beginning of a new era in mill design for the best possible economies of scale.
The Rizhao mill is designed for very low energy, water and chemical consumption. Compared to any other pulp mill built in recent times, it have the lowest impact on the environment. The target is to eliminate solid waste from the mill.
Most advanced technology for lowest environment impact “We selected Valmet to supply the fiber line from chips to bale, evaporation and recovery boiler because of past good experience in dealing with their equipment and management.
The mill has invested in the best available technologies to eliminate smell and reduce the color of effluent, and minimize solid waste. This mill is the new benchmark in size and performance for the pulping industry,” says APRIL COO A. J. Devanesan.
Pulping process
Acacia and eucalyptus wood are the raw material for pulp production. The chips are stored in five GentleStore circular chip storage systems, each designed for a capacity of 190,000 m3.
The fiber line comprises equipment and processes for cooking, pulp screening, brownstock washing, oxygen delignification and bleaching. The selected technology features continuous CompactCooking, Delta screening and TwinRoll wash presses installed for each stage of pulp washing.
An ECF sequence O-DHT–EOP–D-D/P was selected for pulp delignification and bleaching. The new CompactCooking method produces pulp with higher yield, better bleachability and lower energy consumption than other cooking methods.
![]() |
![]() |
|
GentleStore circular chip storage systems |
Continuous CompactCooking | |
![]() |
![]() |
|
Delta screening | TwinRoll wash presses |
Pulp drying
Pulp drying is carried out using Valmet’s energy-saving DryWay concept. The process at the APRIL/SSYMB mill consists of two parallel drying lines. The trim width of the drying machines is eight meters.
The delivery encompasses all necessary process systems from re-screening, drying and cutting through to ready-made bales. The drying machine wet end features Valmet’s twin-wire DryWay concept furnished with two shoe presses. This enables high web dryness prior to the airborne dryer and thereby remarkable energy savings.
After pulp drying and cutting, the sheets are baled in three baling lines installed for both lines. Valmet’s Robobaling technology is used for pulp baling. Both baling systems share two unitizers from where the bale units are transported to storage.
![]() |
![]() |
|
DryWay concept | DryWay dryer | |
![]() |
![]() |
|
Baling lines | Baling storage |
Chemical recovery Black liquor from the pulping system is evaporated in Valmet’s EVAPS plant including two parallel evaporation lines, each dimensioned for evaporation of 1,000 tons of water per hour. The liquor at approximately 80% dry solids content is burned in Valmet’s RECOX boiler.
Designed for a maximum capacity of 7,000 tons of dry solids per day, it is the world’s largest recovery boiler ever built. Strong and weak odorous gases are burnt in the recovery boiler. During June, the boiler was run for few days with 7,550 tDS/d - the record firing capacity in the world.
APRIL is the largest tree planter in the world. It is also the largest hardwood market pulp supplier in Asia and the second largest globally. The company produces paper under the brand name PaperOne, which is sold as a premium product in over 60 countries.
![]() |
![]() |
|
Evaporation lines | RECOX boiler |