CMPC Guaíba pulp mill becomes totally odorless
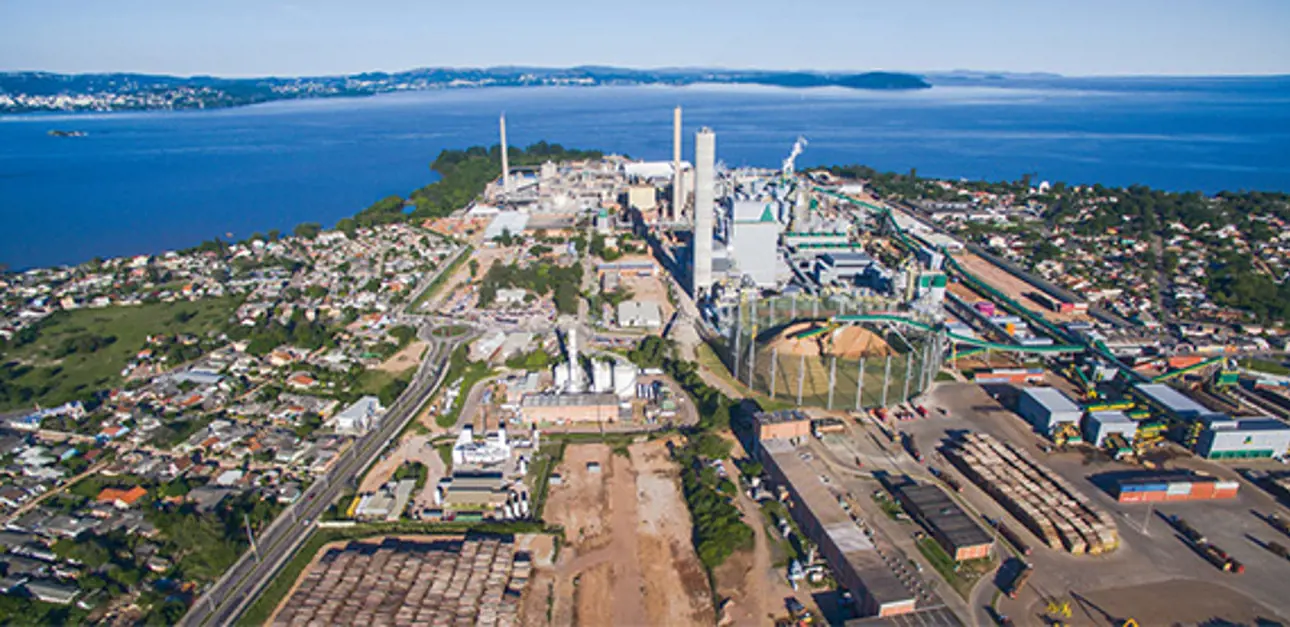
CMPC Riograndense Ltda’s Guaíba pulp mill in Brazil no longer emits any hazardous or malodorous gases into the environment. They are efficiently controlled and destroyed by Valmet’s non-condensable gas (NCG) treatment system – probably the most comprehensive one in the world.
Between 2013 and 2015, CMPC expanded its Guaíba pulp mill located close to Porto Alegre in Rio Grande do Sul State, Brazil. Valmet supplied all the main technologies for a new 1.3 million ton pulp production line 2, including solutions for treating concentrated non-condensable gases (CNCG) and diluted non-condensable gases (DNCG).
No venting and zero smells. These were the guidelines for the design of an integrated NCG system for pulp lines 1 and 2. As the mill is located close to a city with over 1.2 million inhabitants, CMPC wanted to take their well-being into account and minimize mill emissions.
“Only by deploying a secure NCG system can we honor the promise of zero odors made to the environmental authorities and avoid complaints from the community,” says Daniel Sidoruk, Recovery and Utilities Area Coordinator at CMPC Guaíba. “As Valmet supplied the digester, evaporation plant, recovery boiler and white liquor plant that emit NCG, it seemed very consistent to use the same technology provider to integrate such a complex NCG system.”
Sidoruk lists Valmet’s strengths as being able to provide proven technology, compliance with contractual terms, excellent technical support in Brazil as well as the long, successful relationship with CMPC.
Over 100 odor sources controlled by one system
Valmet’s integrated NCG system covers both pulp mill lines. This leaves no ‘grey area’ between them. The effect of every process decision on the whole system can be evaluated, and there is only one operating philosophy. In addition, having the same type of CNCG burner in both recovery boilers means fewer spare parts, easier maintenance and operation – and one team for the job.
“Controlling a complex NCG handling system that collects odorous gases from over 100 NCG sources is a challenge. In Valmet’s mill-wide ODOCON system, all odorous gas sources have been connected to the NCG handling system to achieve the target of an odorless pulp mill,” points out Eevi Smolander, Product Manager, Biotech and Environmental Systems, Valmet.
Typically in a pulp mill, there are two combustion places for destroying CNCG gases. The primary combustion place is a dedicated CNCG burner in the recovery boiler, while the back-up burner can be a burner in the lime kiln, a power boiler or a standby flare burner.
“At Guaíba, there are six combustion locations for CNCG to ensure that odorous gases will not be emitted into the atmosphere under any circumstances. When switching the CNCG from one burner to another, there is no venting of odorous gases. This is done by bottling up the CNCG in the piping while waiting for the back-up burner to be ready to receive the CNCG. Valmet’s automation solution plays a major role in controlling the system,” Smolander explains.
System availability is maximized with tailored process solutions. And special attention has been paid to the switchover situation, resulting in a completely new operating concept.
The back-up burners at Guaíba are continuously in a hot standby mode to ensure faster switchover. This means that support fuel is continuously burned in all the CNCG burning locations, and the burners are ready to receive gases without separate startup. Long odorous gas pipes are kept hot by a constant steam flow through the piping up to the burners, which is important for the smooth switchover and high availability, too. CNCG can be combusted also during power blackouts.
No emissions, high availability
The integrated NCG system at Guaíba is working very well. Valmet carried out some system fine-tuning during the November 2015 outage to remove even the slightest chances of any NCG emissions escaping into the atmosphere.
“We consider the project to be victorious, and it has brought environmental gains to our company,” Daniel Sidoruk says. “There was a lot of uncertainty about the proper functioning of this system due to its high degree of complexity, but now this has been debunked. We are sure that the solution implemented in November will suit our needs, and we will be a totally odorless mill. The system has met our expectations.”
In Valmet’s mill-wide ODOCON
system, all odorous gas sources
have been connected to the NCG
handling system to achieve the
target of an odorless pulp mill.
What about the system availability?
“It can be said that the system availability is practically 100%. There is always a system ready to handle NCG and prevent gases from being emitted into the atmosphere,” Sidoruk concludes.
Text: Marjaana Lehtinen
This article was originally published in Valmet's Customer Magazine Forward 1/2016.