A sustainable star in South Africa
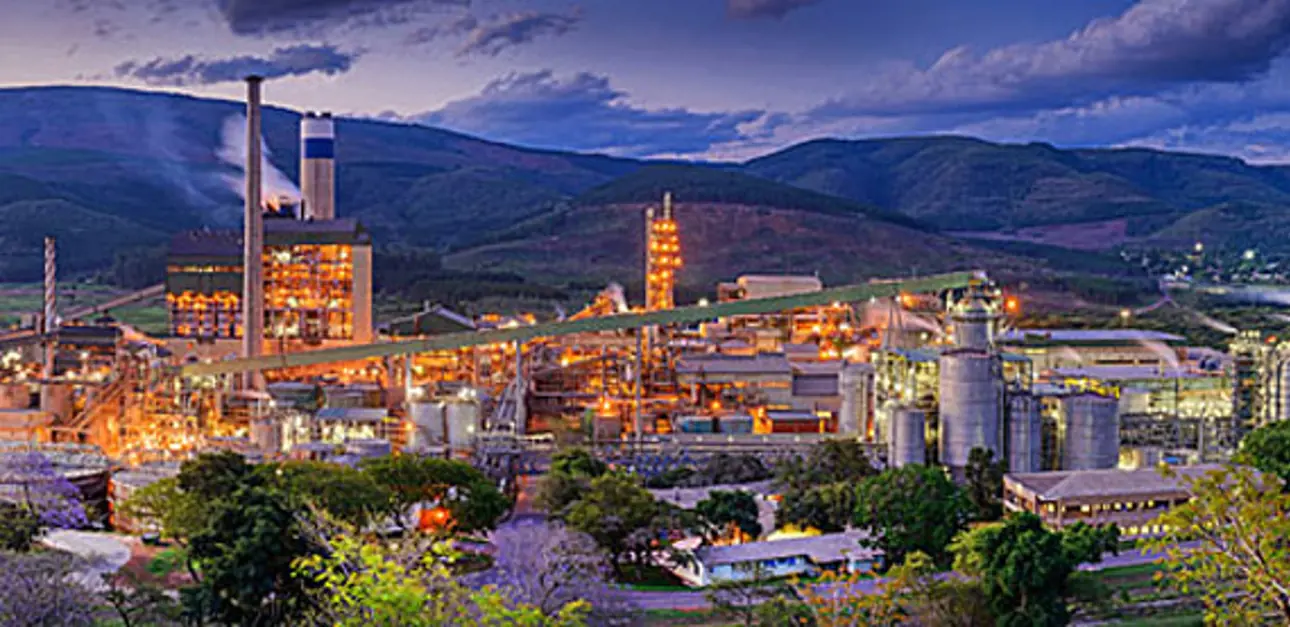
Sappi's Ngodwana mill is located approximately 50 km west of Nelspruit in Mpumalanga province, in South Africa. Due to the limited water supply in the vicinity of the mill, the environmental regulations have been very strict. Regular controls are done in terms of air emissions, water use, effluent discharge and solid waste management, as well as energy recovery. The new line is designed to minimize the use of fresh water and performs in the top 5% of integrated pulp and paper mills worldwide in this respect.
Challenges and innovative solutions
Innovative process and execution solutions were needed, and this project was both urgent and demanding. For example, the product from Ngodwana had to be interchangeable with sulfite pulp from Sappi’s Saiccor mill, and the fiber line had to be capable of producing elemental chlorine-free and totally chlorine-free dissolving pulp, as well as bleached hardwood kraft pulp.
“Today we have a flexible process where we can run a variety of sequences and qualities. If we need to, we can replace the first stage with acidic hydrolysis and the last with a peroxide stage in the bleach plant, for example, making the process totally chlorine-free,” says Hunphrey Landman, Technical Services Manager of Sappi Ngodwana.
Another challenge was the shortage of skilled construction personnel due to a number of large ongoing power station projects. This resulted in a multinational project management and construction team. In addition, the learning curve for operating staff was steep, as both batch cooking and prehydrolyzed kraft based on the Valmet Batch process were new technologies for the mill.
Quality parameters set in the cooking plant
The existing wood room has been upgraded with new conveyors and chippers to supply the new batch cooking plant with raw material. In a dissolving line, the cooking plant is vital, as it determines most of the quality parameters. In this case, a prehydrolysis stage was added to release hemicellulose from the wood. The energy balance has to be just right in order to minimize water consumption, and maximizing the use of waste heat is also important.
Reduced emissions and low water consumption
The washing is based on TwinRoll TRPE presses with two washing stages before the oxygen delignification stage and two after it. A press-based process is ideal for keeping water consumption low.
“We are very satisfied with the washing performance of the presses. The pulp is bright and clean, with the viscosity we are looking for. The presses require little maintenance and do not give us any trouble. We are also happy about the low water consumption, which was a prerequisite,” says Landman.
Washing in the bleach plant is also based on TwinRoll presses of the TRPE type and one TRPZ press ahead of the ZeTrac ozone stage. Bleaching with ozone instead of chlorine enables lets us recycle more of the dissolved material and reduces emissions from the bleaching plant.
The recovery system minimizes water consumption by using evaporation condensate instead of fresh water. The capacity of the recausticizing plant has increased to 5,500 m3 of strong white liquor a day, and the evaporation plant can now handle 550 tonnes of evaporated water per hour. The retrofit also included a condensate stripping system, which has increased the quality of the condensate.
The capacity of Ngodwana’s recovery boiler No. 2 has increased from 1,850 to 2,200 tonnes of dry matter per day and the two-stage ash leaching plant has cut sodium discharges into effluent.
The future looks bright
By choosing an efficient technology which allows flexibility, reduces the environmental impact to a minimum and still produces high-quality pulp, the future looks bright for the Ngodwana mill.
“As well as improving our environmental footprint, this project has improved the mill’s prospects. The GoCell project will reduce odors from the mill and the improved efficiency with the new equipment means that we will use less coal per year, which will reduce our CO2emissions by 120,000 tonnes. In addition, the overall emissions from the mill will decrease,” Landman concludes.
Dissolving pulp is Sappi’s speciality · In 2011, the project to expand and modernize the Ngodwana mill began, including the introduction of 210,000 tpa of dissolving wood pulp at the mill. Valmet received the order to supply the main equipment for the new cooking plant and fiber line and also equipment for the upgrade of wood handling, evaporation and recausticizing, as well as a new ash leaching system. · Sappi is today the world’s largest manufacturer of this specialized cellulose from two mills in Southern Africa: Ngodwana and Saiccor, and the Cloquet mill in North America. · The main part of Sappi’s dissolving wood pulp is sold as raw material for the manufacture of viscose staple fiber for clothing and textiles. |
Did you know that your clothes are made from wood-based raw materials?
Viscose, rayon and modal are all made from dissolving pulp and used in the manufacture of fashion and decorating textiles, which have a soft, natural feel and excellent breathing properties. Unlikemany synthetic raw materials, these fabrics are produced from a natural and renewable resource.