Changing the global textile industry for the better
Jan 22, 2025
Circulose dissolving pulp in created by using cellulose from discarded textiles. This is then spun into new soft and breathable textile materials like viscose and lyocell. Big brands like Levi’s, Calvin Klein, H&M, and Tommy Hilfiger are already using it and Valmet supplied the technology for the first industrial-scale production line.
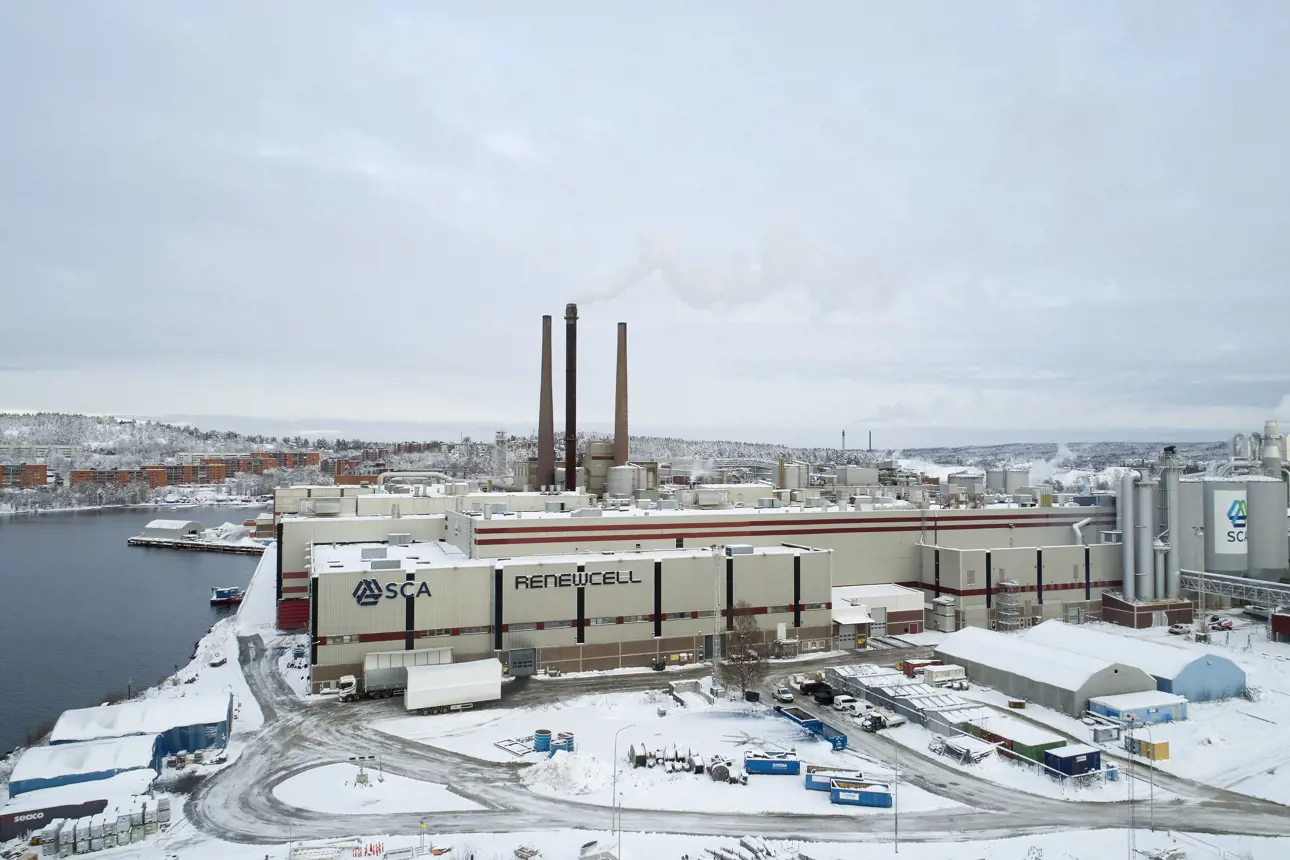
Swedish textile company Renewcell invented a groundbreaking process for recycling and reusing textile waste. The resulting product is a dissolving pulp called Circulose that is made from 100% textile waste. Textile producers and fashion brands such as Levi’s, Calvin Klein, H&M, Tommy Hilfiger and many others are now using Circulose to replace high environmental impact raw materials, like fossil oil and cotton, in their textiles. Henrik Dahlbom, the Project Director at Renewcell, explains some of the key benefits of Circulose.
“The textile industry has a significant impact on the environment and Renewcell is aiming to improve the environmental footprint of textiles. Cotton, for example, demands large quantities of water to grow and process, and it also uses pesticides and fertilizers that pollute the environment. Since our process depends only on recycled garments that we shred, we can sell a recyclable product that consumes much less water and chemicals over its many lifecycles.”
Professors with a recycling idea
The Renewcell company journey started at Sweden’s Royal Institute of Technology in Stockholm, where a couple of professors were working on recycling cotton from textiles. In the lab they succeeded in making a pulp from recycled cotton garments which responded well to bleaching for brightening it. Thereafter, in 2017, they built a pilot plant in Kristinehamn, Sweden, to scale up the output and make samples for the first customer trials. In parallel, they also did design testing for the bleaching process at Valmet’s Fiber Technology Center in Sundsvall.
In 2019, larger-scale samples were sent to key customers and got a positive response. So, in 2020, the team decided to build the first industrial scale production line at Ortviken near Sundsvall and the first saleable Circulose product was shipped in October 2022, with high demand for the material.
Renewcell wanted a partner that complemented its own expert’s process insight with deep knowledge about equipment and best practices.
Valmet equipment and expertise
When selecting Valmet as the equipment supplier, Renewcell unquestionably wanted a partner that complemented its own expert’s process insight with deep knowledge about equipment and best practices. Among the specific capabilities they sought were world class technology and long experience of supplying equipment to the fiber processing industry, in combination with an excited curiosity about textile recycling and the new dissolving pulp's special behavior.
Renewcell’s Dahlbom says that everything has worked out very well, with excellent cooperation between Renewcell and Valmet. “Already from the start of the project we had good discussions with Valmet about solutions for the installation. We were always focused on finding ways forward and we appreciated the experienced team from Valmet helping us. We could also feel that they were curious about this new fiber and how we could work with the equipment, so there was a shared dedication to making this succeed. I think everyone who gets involved in this project realizes how important it is for the environment and the future,” he states.
Renewcell conducted several pilot and lab trials at Valmet’s fiber technology centers in Finland and Sweden. Ari Saario, VP for Strategy and R&D for the Pulp and Energy business line at Valmet explains about the cooperation: “Pilot trials play an essential role in reducing risks in technology development and upscaling, and I have to say that I’m really impressed with the fast start-up of Renewcell’s first-of-a-kind plant. It is also worth highlighting the importance of close connections in technology development we have had since the beginning of project and actually even earlier.”
There was a shared dedication to making this succeed.
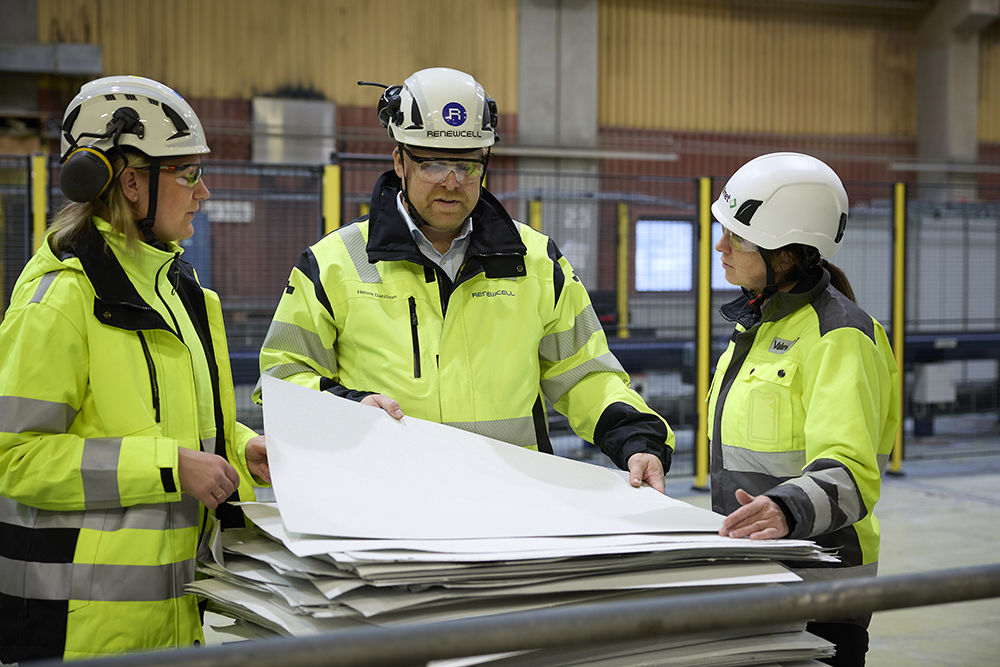
Henrik Dahlbom in the middle showing the cotton sheets. From the left: Sofia Bylund Valmet, Henrik Dahlbom Renewcell, Åsa Arencrantz Valmet.
Circulose now moving into the market
Circulose is a high-cellulose-content dissolving pulp which can be used to make viscose, lyocell, modal, acetate and other types of regenerated fibers, which are sometimes called man-made cellulosic fibers (MMCF). These fibers are then spun into yarns or woven or knitted into fabrics and finally cut and sewn into new high-quality textile products.
The big difference with Circulose compared to traditional textile raw materials is that no new cotton, oil or wood is consumed. The recycled clothes, as well as other recycled textile waste streams, are shredded and processed into a dissolving pulp solution which is then bleached and dried. From there it is delivered to customers, the fiber producers, in cotton sheets.
Joint solutions overcome challenges
Since the Renewcell line at Ortviken was built in an existing building, flexibility with the layout was very important. The small Renewcell project team had many discussions with Valmet about “how should we do it with this machinery” and “what kind of equipment do we need over there.” Valmet’s ability to advise on many of these questions was highly appreciated.
“Since this is a totally new process,” explains Dahlbom, “we didn’t have a lot of people to ask about how to do it. We had to invent a lot of things ourselves, sometimes with Valmet’s help, to be able to move forward. In addition, we had global issues such as the pandemic and war that also affected the project. But now we are moving well and ramping up production further, with a product that our customers can use and that meets their high-level quality specifications.”