At the heart of a new hardwood kraft pulp line
To secure fiber supply and the viability of their board machine, Tamil Nadu Paper Limited decided to integrate the mill with pulp production. They selected Continuous Cooking G3 and TwinRoll Press technology from Valmet, which has proven its benefits through strong bleached hardwood kraft pulp and reduced energy, water and chemical needs.
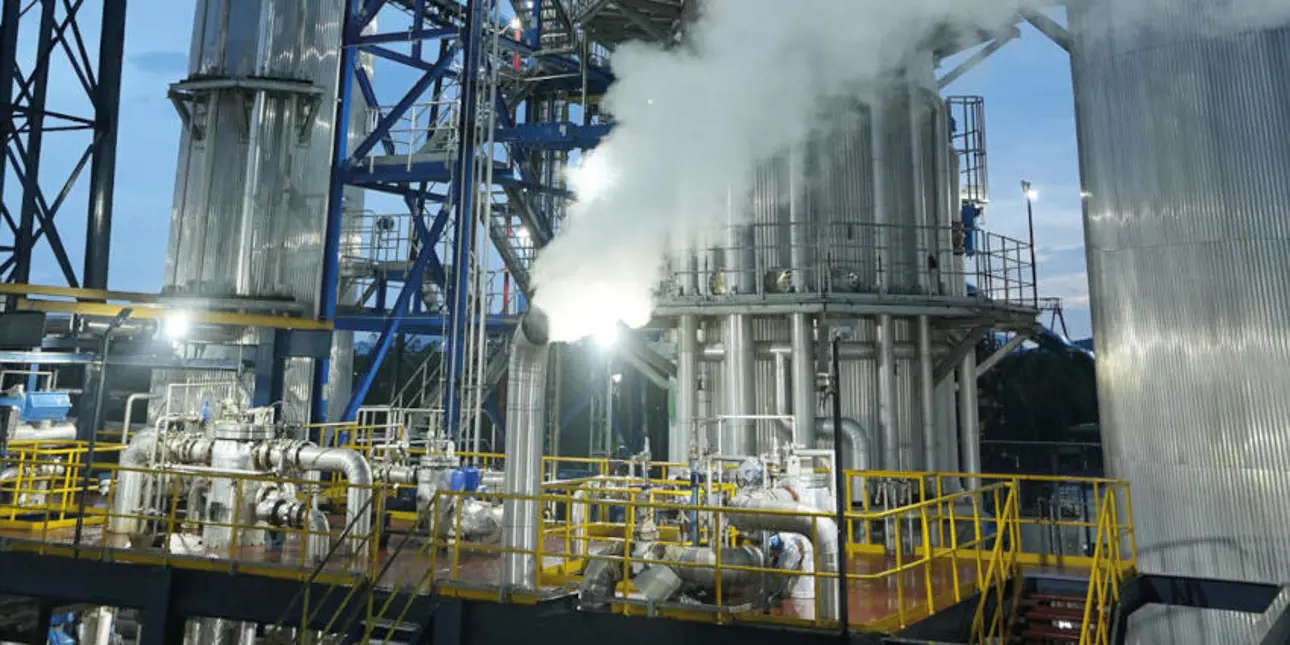
The Tamil Nadu Paper Limited (TNPL) pulp and paper mill in Mondipatti, Trichy District, India has a modern board machine making 200,000 tonnes/p.a. of multilayer paperboard. It began operating in 2016. Since the machine started up, it has been fully dependent on purchased pulp for papermaking fibers. With the pricing of purchased pulp often fluctuating and availability not always completely reliable, TNPL felt these risks were impacting the long-term outlook for the paper machine’s operation.
To secure both the fiber supply and the future viability of their board machine, TNPL started exploring the possibility of integrating the mill with pulp production. The idea was to take advantage of the highly organized pulpwood plantations that the company had wisely been developing over many years to help ensure its fiber supplies.
The Valmet TwinRoll press technology has reduced energy, water and chemical demand.
High performance and pulp quality with Valmet Continuous Cooking G3
TNPL decided to install a modern bleached hardwood pulp line, and they selected Valmet Continuous Cooking G3 technology after a thorough techno-commercial evaluation of bids from global pulp and paper technology suppliers.
“Based on our thorough evaluation, Valmet won the order because it was clear that their solutions met all our key objectives, including environmental compliance, technological competence, high energy cost-effectiveness and the greenest technologies,” explains the late Mr. Seenivasan R, Executive Director (FAC) of Mill Operations at TNPL. “We are pleased to say Valmet has fulfilled all our requirements.”
The plant was commissioned in January 2022 with support from Valmet’s experienced team. TNPL says it is satisfied with the overall performance of the Valmet Continuous Cooking G3 and pulp quality achieved for use in its premium aura brand packaging board grades.
The TNPL team greatly appreciated Valmet’s professional support.
Added value from high-efficiency presses and long experience in pulp washing
“The Valmet technology that TNPL has installed gives it many advantages, including consistently excellent pulp quality and yield,” says Mr. S. Nandagopal, General Manager (Projects) at TNPL. “Significant cost and sustainability benefits have also been realized in terms of low energy, water and chemical consumption, and a reduced overall environmental impact.”
“The lower energy, water and chemical demand benefits TNPL is getting are the direct result of the the Valmet TwinRoll press technology performance,” explains Mr. S. Nandagopal. In addition, Valmet’s long experience and expertise with the critical pulp washing operation have also been a big advantage.
It was a very good experience to work together remotely on this project, and it’s remarkable how successful it was.
Finally, TNPL has appreciated the pulp line’s compact design, as well as the high level of service and Valmet’s commitment to project implementation.
Successful project execution despite pandemic
A major difficulty faced during this project was the Covid-19 pandemic, which was managed very well thanks to close cooperation between Valmet and TNPL. Project execution took place during a period that included two waves of Covid-19 in India. The pandemic meant travel restrictions were in effect during the start-up phase. The team needed to be creative to work around these difficulties.
Using remote technology to access the mill’s DCS, Valmet’s Nordic team and their counterparts from both TNPL and Valmet’s team in India collaborated closely to achieve smooth start-up and commissioning. The day after the start of the hardwood line, the high-quality pulp was used to manufacture the mill’s premium paperboard grades. The line reached its expected maximum capacity within four months of the start-up.
“During the Covid-19 pandemic, remote communication via Teams helped us keep in close touch as we were executing the project,” says Mr. R. Kandhavel, Assistant General Manager for Instrumentation. “With a major project like this, many separate layers and systems need to be coordinated, and I’m happy to say we met the challenge in spite of Covid-19. It was a very good experience to work together remotely on this project, and it’s remarkable how successful it was.”
Professional support and close collaboration
Mr. Bhanu Prasad, Chief General Manager of the TNPL Board Plant, is also very pleased with the project and the overall cooperation with Valmet in achieving its objectives.
Mr. Bhanu Prasad, Chief General Manager Board Plant at TNPL.
“Valmet gave us their full support during the project execution, even during the peaks of Covid-19, and all the deliveries were on time. Despite the travel restrictions on their overseas experts, Valmet empowered their local supervisors to support TNPL with remote support services so that the experts could also participate. Valmet’s overall project execution performance was excellent and very professional.”
![]() |
![]() |
The late Mr. Seenivasan R, Executive Director (FAC) of Mill Operations at TNPL. |
Mr. S. Nandagopal, General Manager (Projects) at TNPL. |
Text Hugh O’Brian Photos Kartikaya Nagar