All the pieces coming together for fossil free pulp production
Jan 23, 2023
Construction of the Metsä Fibre Kemi bioproduct mill is in full swing, with 3,500 people working at the site to start up a mill that is world class in energy, environmental, and material efficiency. The completely fossil fuel free new mill is scheduled to start up in the third quarter of 2023.
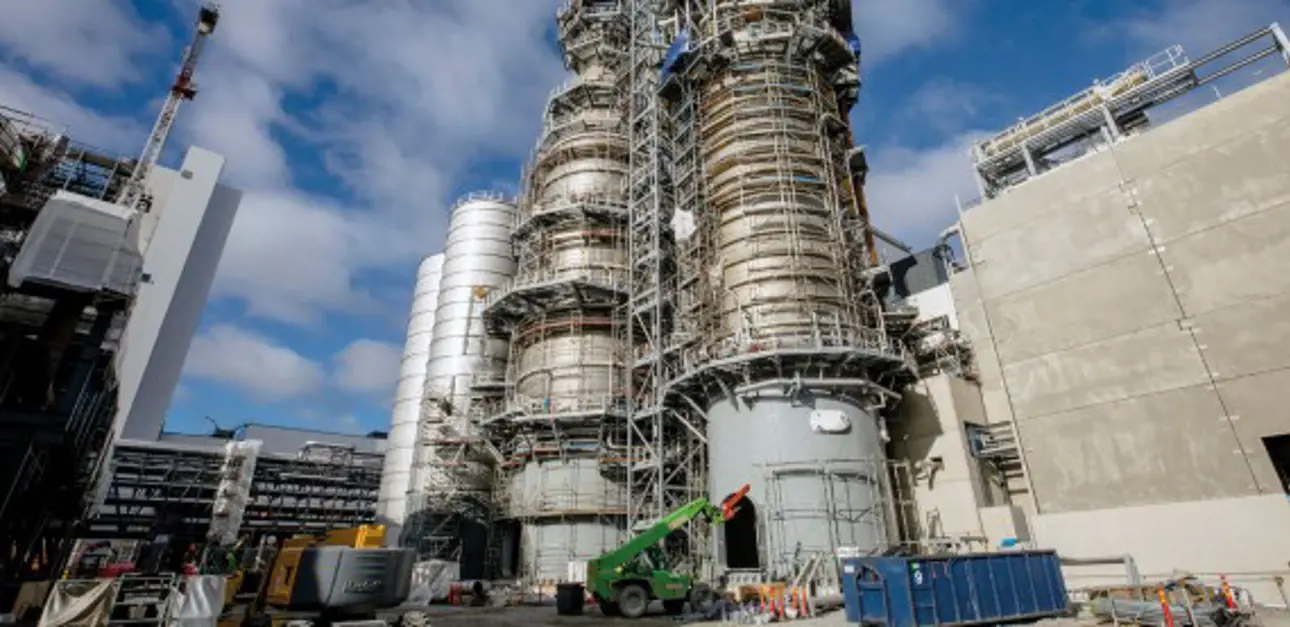
Metsä Fibre, part of Metsä Group, is making a significant investment in the Finnish forest industry by building a new bioproduct mill in Kemi, Northern Finland. The new bioproduct mill will have an annual production capacity of 1.5 million tonnes of softwood and hardwood pulp. It will also produce various other bioproducts.
In June 2022, large evaporation components were transported to the site.
Strategic project for Metsä Group of great local importance
“This project is of great strategic importance for Metsä Group. We’re fulfilling our strategy of sustainability and profitable growth. With renewable wood-based bioproducts, we’re enabling the replacement of fossil materials. This is also a significant investment in the Kemi region, securing employment not only for our own mill personnel but across the value chain,” says Metsä Fibre’s CEO Ismo Nousiainen.
Featuring the latest technology and automation
Sami Riekkola, Valmet’s Pulp and Energy Business Line President talks about the latest technology at the mill. “Valmet delivers the full production process from wood handling to baling, flow control solutions, and an automation system for the whole mill. These solutions represent leading sustainability performance with minimized emissions and the efficient use of side streams. For example, the sulfuric acid used in the mill processes is produced using the mill’s odorous gases, and the lime kiln uses gasified residue biomass as fuel. For effective dust removal and low emissions, the mill will have dry ESP (electrostatic precipitators) for the recovery boiler and both dry and wet ESPs for the lime kiln.”
The solutions delivered represent leading sustainability performance with minimized emissions and with the efficient utilization of side streams.
“High environmental and energy efficiency are key targets for our mill. The mill is built using the best available techniques (BAT), meeting and even exceeding the EU BREF requirements. The mill won’t use fossil fuels at all, and it will produce two terawatt hours (TWh) of renewable electricity per year. Sulfuric acid production from the mill’s own non-condensable gases is an excellent example of the modern technique, which goes beyond the industry requirements,” says Metsä Fibre’s Project Director Jari-Pekka Johansson.
The sulfuric acid production from mill’s own non-condensable gases goes beyond the industry standards.
“Automation plays a key role in the mill’s overall efficiency. With the help of Valmet’s automation system, we can run the new mill in a balanced way, control the process and ensure it runs flawlessly with high quality, cost-effectiveness and environmental efficiency,” says Tomi Seppä, Vice President, Production, for the Metsä Fibre Kemi bioproduct mill.
The number of employees working with construction and installation at the site is at its peak more than three thousand. To succeed, systematic way to operate, synchronized schedule management and good communication with all parties is needed.
Keys for success in a mega project
The project’s initial planning started years ago – after the Äänekoski bioproduct mill was started up. The first concrete steps were taken in 2020 with preparatory works on site, pre-engineering and the environmental permit. The final investment decision was made in February 2021, when the construction works in Kemi also started.
“This project’s scope is extensive. In addition to the bioproduct mill itself, we’ve already built a new railway to the mill area, a new warehouse for the deep sea port, and a new 110 kV high voltage transmission line to the national grid,” Johansson describes the scope of the works in Kemi.
“High environmental and energy efficiency are key targets for our mill. Sulfuric acid production from the mill’s own non-condensable gases is an excellent example of the modern technique, which goes beyond the industry requirements,” tells Metsä Fibre’s Project Director Jari-Pekka Johansson.
Executing a project of this magnitude is itself a challenge, and these exceptional times have added their own flavor.
“To succeed in such a project, we need a systematic way to operate, synchronized schedule management and good communication with all parties. With more than three thousand people working onsite, representing about a dozen nationalities, we need clear practices. The global Covid-19 pandemic and the Russian invasion of Ukraine have affected everything, including the Kemi bioproduct mill project, but we’ve taken corrective actions and have been able to mitigate all their effects. This is thanks to professional people and companies like Valmet working with us in the project,” says Johansson.
“Work on a site like this is always intense. Despite the challenging circumstances, Metsä Fibre has arranged the site facilities very well, including the offices, canteens and the offer of onsite Covid vaccinations,” says Valmet’s site manager Antti Ahola (left) pictured with Juulia Liimatainen, Valmet’s project Director.
Valmet’s site manager Antti Ahola has a lot of experience of working in large projects all over the world. He gives Metsä Fibre credit for the arrangements at the site. “Work on a site like this is always intense. Despite the challenging circumstances, Metsä Fibre has arranged the site facilities very well, including the offices, canteens and the offer of onsite Covid vaccinations. Together, we also worked on some special arrangements to get all the components to the site on time.”
Several key milestones successfully reached
The project is proceeding at full speed, and many major milestones have been reached in recent months.
“All in all, we had about 30 special transportations of large components from the Ajos deep sea port to the Kemi city port and on through the town. To transport the large cooking and evaporation elements, some lampposts and traffic lights had to be temporarily removed, and they’ve now been restored,” Ahola adds.
The large components requiring special transport were moved from the port of Ajos to the mill site during October and November 2021 and May and June 2022. The largest components were the 15-metre wide, 510-tonne evaporator units. The longest component was the approximately 65-metre-long reactor tower.
Valmet’s Project Director Juulia Liimatainen lists a few of the ongoing activities. “In addition to the equipment and piping installations, other preparatory activities are ongoing. The site operators’ training has started, and we are undertaking hydro and pressure tests. And we are of course very happy to have successfully completed the planned works for the Fiberline 1 rebuild at the existing mill’s September 2022 shutdown.”
The automation system’s factory acceptance tests were conducted in Kemi during the fall of 2022. After Valmet’s own system and application engineers had tested the system, Metsä Fibre’s personnel also tested it.
“Testing has gone very well, and the fact that we did it here in Kemi made it possible for most of our teams to take part in the testing. We also see this testing as a very important part of the learning process. Our process operators can familiarize themselves with the new mill’s production process through the testing,” says Seppä.
Approaching the final stretch
The new bioproduct mill will be started as planned in the third quarter of 2023.
Automation is in a very central role when thinking about the mill’s overall efficiency.
“Next, commissioning teams will mobilize to the site and start the preparations for the first cold commissioning activities. We’re all committed to our common goal of securing a smooth start-up and fast ramp-up,” Liimatainen summarizes the next steps from Valmet’s perspective.
“The next months will be busy, and we’ll continue to have many contractors and our own employees on the site. Securing the safety of everyone operating on the site continues to be very important,” Johansson concludes.
Text Lotta Forssell
Photos Nina Susi, Jarno Vuorinen, Metsä Group
Metsä Fibre Kemi bioproduct mill – a showcase of sustainable pulp production
Metsä Fibre’s Kemi bioproduct represents state-of-the-art technology with high raw material efficiency, low emissions, excellent energy efficiency and high side stream utilization.
Valmet’s technology for wood handling, cooking and fiberline, and chemical recovery enables a high fiber yield and cooking chemical circulation. As the lime kiln uses product gas made from bark, the mill is 100 percent fossil fuel free. Energy integration between cooking and evaporation reduces the mill’s steam consumption. With the aid of the high-power recovery boiler, the mill can produce 150 percent more electricity than it needs. The production of sulfuric acid from the mill’s non-condensable gases reduces emissions and improves side stream utilization. Air emissions are controlled by dry and wet electrostatic precipitators.
The mill’s production is optimized with Valmet’s automation solutions, including the Valmet DNA mill-wide automation system, advanced process controls (APC), analyzers and online measurements.
Valmet’s flow control solutions delivery to the Kemi bioproduct mill consists of 2,600 NelesTM ball, segment and butterfly valves for on-off and control applications, and 1,250 Neles NeldiscTM butterfly valves for manual on-off duty. Neles ND9000TM series valve controllers enable advanced performance follow-up and predictive maintenance planning.
Related videos:
Related articles