Valmet’s holistic approach from chip to board for linerboard producers brings success
There are many advantages of having one supplier covering everything from wood handling to final board. Valmet’s holistic approach – from chip to board – helps companies worldwide to produce linerboard that is profitable and sustainable.
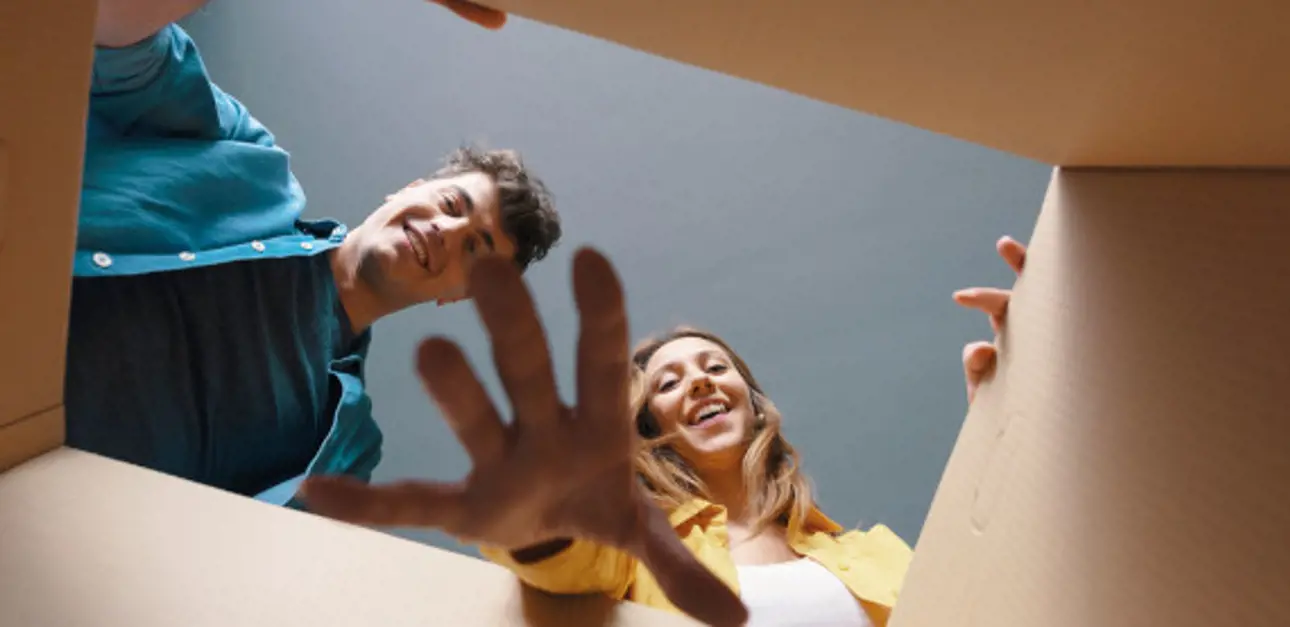
"Sustainability is becoming more important than ever. Sustainable packaging with lower wood and power consumption, and a decreased carbon footprint are keys to success. At the same time, the requirements for the quality of the products are increasing,” says Matti Lares, Senior Paper Technology Manager at Valmet.
"Today, we’re helping companies worldwide to produce linerboard that is profitable and sustainable. This includes assisting customers to develop new linerboard grades based on new raw materials," says Matti Lares, Senior Paper Technology Manager at Valmet.
There is great potential for companies that develop and produce high-quality fiber-based packaging. Some are investing in greenfield mills for board production, while others are searching for ways to make their existing board production more profitable and sustainable. Lares explains how Valmet can make a big difference:
“Today, we’re helping companies worldwide to produce linerboard that is profitable and sustainable. This includes assisting customers to develop new linerboard grades based on new raw materials. We provide proven solutions, and service and cutting-edge expertise all the way from chips to board, so that our customers can produce the linerboard of the future.”
Optimized boardmaking with stronger pulp
Chip quality is the first parameter that has a direct effect on the final paper and board quality. With ImpBin, chip impregnation is done more homogenously than is the case with the other concepts on the market. It combines the dual benefits of lower wood cost with improved pulp quality, resulting in a much stronger virgin pulp. When added to Valmet’s new holistic refining concept for the fiberline and board machine’s stock preparation, customers achieve optimized and tailormade fiber properties for their final products. For example, ImpBin produces a longer average fiber length, and stronger final boards are thus obtained.
"Stronger pulp makes it possible to reduce the proportion of virgin pulp and replace it with recycled fibers, while preserving the strength of the board," explains Lars Sjödin, Technical Director of Valmet’s Fiber Business Unit.
“We’ve seen this in several customer cases, and it’s a real game changer. With Valmet’s stronger pulp, our customers can produce stronger board. They can also produce board with preserved strength but with a lower basis weight than before. Stronger pulp also makes it possible to reduce the proportion of virgin pulp and replace it with recycled fibers, while preserving the strength of the board. Our customers also achieve lower wood and power consumption, and a decreased carbon footprint,” Lars Sjödin, Technical Director of Valmet’s Fiber Business Unit, explains.
We take a holistic approach and assist our customers all the way from chip to board.
With advanced tools for board machines, Valmet can maximize the final strength properties of the fibers. A headbox with Aqua layering technology for more efficient dosing of strength additives, forming with Sleeve Roll technology for improved fiber-to-fiber bonding, and hard nip sizing for better surface starch response are three examples. Depending on the need and desired production level, Valmet can select the most suitable units to maximize strength development over the entire lifecycle of the board machine.
An end-to-end solutions provider
Not all companies producing corrugated packaging have the same challenges and goals, yet that doesn’t mean that they’re completely different. Many try to find answers to common questions such as: How can we lower our production costs from the raw material? How can we increase our production? How do we attain a lower basis weight for our packages? How can we achieve the desired tensile and tear strength? Everything is connected, and Valmet’s holistic approach – from chip to board – is a success factor for the customers.
Riikka Antikainen is a Senior Paper Technology Manager at Valmet. Despite specializing in board machines, Riikka emphasizes the importance of seeing the big picture:
“An improved fiberline results in a better end product. There are many advantages to having one supplier covering everything from wood handling to the final board. And we’re happy to say that Valmet is the only full-scope supplier on the market for pulp and board production, and the only one with mill-wide automation.”
Valmet Mill Wide Optimization is a Valmet Industrial Internet (VII) application, and a crucial part of Valmet’s holistic approach. Together with Advanced Process Controls (APC) such as Valmet Cooking Optimizer for digesters and Valmet’s Pulp to Paper Optimizer for board machines, the application ties everything together. It was developed to close the gap between process areas, and therefore makes it possible to adjust furnish properties according the requirements of the produced linerboard.
"The holistic optimization solution automatically stabilizes and optimizes the process variables from chip to board to obtain the most cost-competitive and energy-efficient liner board production. We can thus control and optimize the whole process, making linerboard according to our customers’ requirements,” says Antikainen.
Bright future for fiber-based packaging
Consumers’ expectations of smart and environmentally friendly packaging are increasing, and it is predicted that fiber-based renewable packaging has a very positive future. This is true for the food industry, consumer goods, and many other business areas.
At the same time, e-commerce is growing, and our ways of living and consuming are changing. The Covid-19 pandemic accelerated this change in our behaviors and preferences. So what do we think the future holds? Jan Laredius, the concept owner of the area of Pulp for Packaging Grades at Valmet, offers his thoughts:
"We can see that the future for fiber-based packaging looks very bright," says Jan Laredius, the concept owner of the area of Pulp for Packaging Grades at Valmet.
“First and foremost, we can see that the future for fiber-based packaging looks very bright. To be a winner, I think it’s important to have a proven track record in sustainability. Linerboard with a lower basis weight can be part of this. It’s feasible due to Valmet’s stronger pulp, and it means less wood consumption, more climate-smart transportations and a lower carbon footprint.”
“We take a holistic approach and assist our customers all the way from chip to board. This makes our offer stronger and is key to producing high-quality linerboard at minimal cost,” Laredius concludes.
Text Kristofer Sjöblom
Related articles