A new star shines brightly on the Baltic Sea
When LNG-powered MyStar began her daily ferry route at the end of 2022, another star joined the constellation of ferries connecting Tallinn and Helsinki. MyStar is the second vessel in the Tallink fleet to select the Valmet DNA automation system for world-class operational efficiency, following her reference ship Megastar.
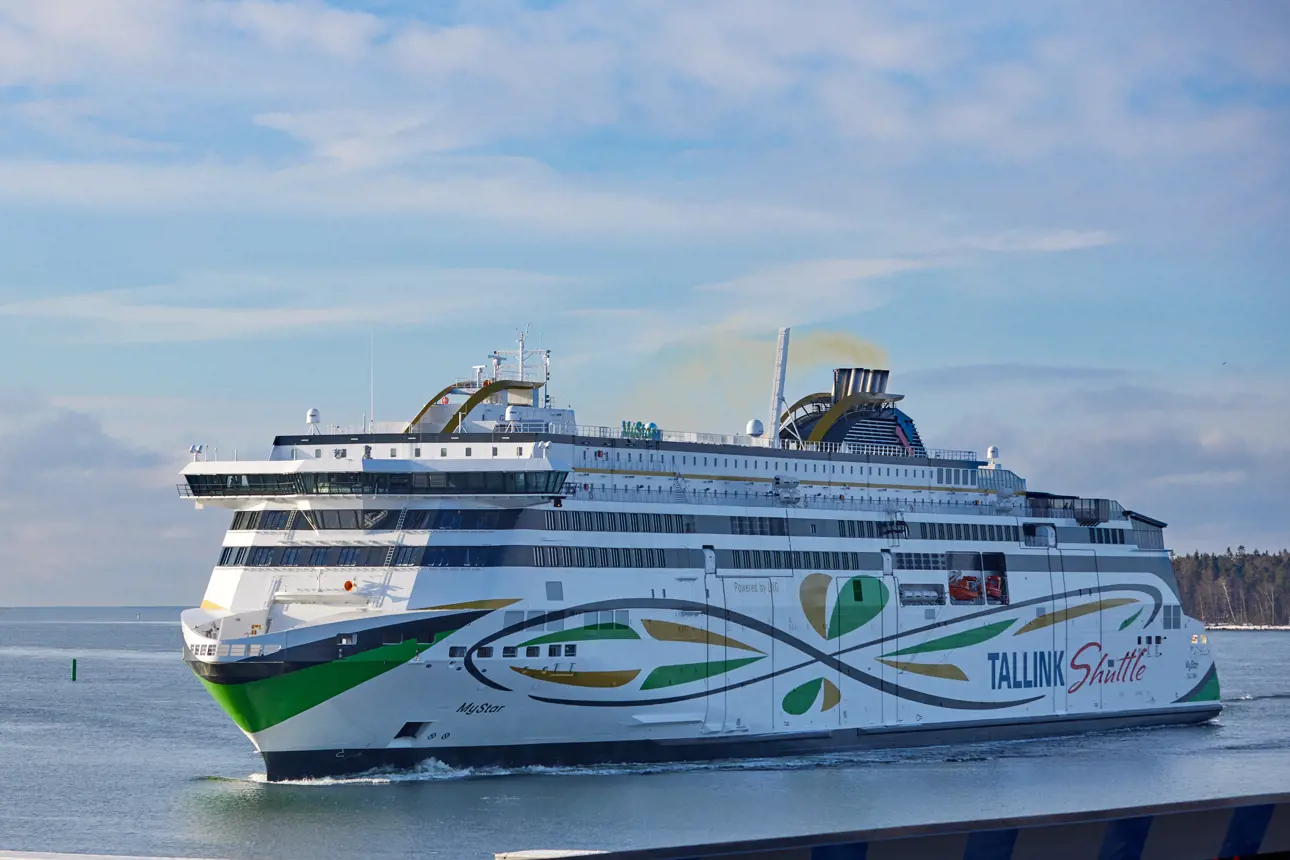
Tallink’s latest vessel is the greenest and most innovative vessel sailing the Baltic Sea. On December 7, 2022, shipyard Rauma Marine Constructions (RMC) handed MyStar over to Tallink, and the ferry’s first commercial voyage from Tallinn to Helsinki took place a week later on December 13. MyStar is a poster child for technologically advanced shipbuilding and world-class marine automation systems. These systems enable vessels to meet tightening environmental regulations, reach sustainability goals and enhance passenger comfort and safety.
The crew is comfortable using the Valmet DNA automation system for their tasks after only a few months of operations. They are pleased with the thorough training they received from Valmet in Finland before the ship was handed over. Plus, the system’s highly intuitive visual graphic displays make their work easy.
The benefits of using large wall displays
Chief Engineer Veljo Kattago of MyStar explained how the crew is using the Valmet DNA automation system. “What’s new on board this vessel are two very large displays on the wall that make monitoring much easier for us. On earlier vessels, we had multiple small displays. Valmet is good at designing large displays to show everything needed at a glance. For example, the entire power management system can be displayed, and it is easy to change the mimic to monitor another part of the vessel’s operations.”
When the power management system starts, it is easy to see what is happening from the mimic. The main power system is shown on the large display screens. “If you want to see more information, you can then look into the details on the smaller popup mimics, such as the main engine parameters. You can also switch mimics and place the detailed view on the large screen,” he explains.
Valmet is good at designing large displays to show everything needed at a glance.
“Normally, we keep the two main overview mimics open all the time. We can easily see when the main engine is starting. It’s clear to see from the mimics that everything is under control. This is important,” he stresses.
He goes on to say that it is also easy to use the Trend and Event Archive (TEA) to check parameters and get more information to run the vessel. “Valmet’s team comes to fine-tune the system whenever we have any requests. Because both vessels – MyStar and Megastar – have the Valmet system, it has been very easy for the crew to use it,” Veljo says.
Excellent training and support
Andreas Suvorov, MyStar’s Electrical Engineer, was trained on the system for about seven months at the RMC shipyard. He continued his training later in Tallinn. “Valmet DNA is a new system for me. I’ve only been using it now for the past two months since MyStar began commercial operations. It provides a lot of data that you need for various purposes. You continuously learn more as you use the system,” he says.
Roman Vladimirov, 3rd Engineer, is most pleased with the system’s vast history databank. “If something unexpected happens, I can go back to the Trend and Event Archive. I can see all the systems and compare data to find out what went wrong or why there has been a change. It’s important to learn from the past,” he says.
“The automation system also allows me to easily select the parameters most relevant for the tasks I’m working on, such as temperature or pressure. It is easy to click on the graphics to see if the temperature is rising, for example,” Roman continues. When the vessel is in port, he stays busy with the automation system as the engines are turned off and then on again.
Roman is pleased with the training support he has received from Valmet. He also spent nearly a half year in Rauma being trained to use the system by the Valmet team. “Juha Vainio from Valmet took care of the commissioning. It was really good to work with him during the project,” Roman says.
Hindrik Usin, Chief Officer, works on MyStar’s bridge. He’s pleased with the graphical automation system mimics.
“It is easy for me to follow the status of the ballast water process from here. Right now, I want to secure stability. So, I will discharge about 120 tons of ballast water. We took water on board yesterday but now no longer need it. Using the Valmet automation system, I can just open the valve and check that the status is green, or good to go.”
Hindrik selects the operation mode for deep ballasting. “When the system is ready, I push ‘Start.’ The system shows me exactly what the treatment unit is doing and when I can start the ballasting pump,” he explains.
He goes on to mention that the bridge also can use the remote control functionality. If the engine room crew would like to perform the ballasting, they would have to request remote access. “But right now, we’re the kings,” he says, as he continues monitoring the operations.
Matti Nurminen, Valmet’s Lead Engineer, is the main designer of the MyStar automation system. He masterminded the power management system (PMS) and all electricity generation and distribution. In his opinion, designing and delivering the entire system went quite smoothly and according to plan.
“When MyStar stays in Tallinn each night, it is plugged into a charging station and the generators are switched off. So, it is not necessary for a technician to be there overnight,” Matti says.
Second vessel in a fleet
Being selected a second time for a Tallink LNG-powered vessel was solid proof that Valmet’s system has been highly appreciated on the first vessel.
Valmet’s delivery scope for MyStar included Valmet DNA Integrated Automation with its information management system, the Power Management System and Emergency Shutdown system.
The project was successfully carried out by both the professional project teams at Tallink, RMC and Valmet.
Now a new star has been born that complies with the latest environmental regulations and sustainability goals with its green technology and advanced automation system. Additionally, the vessel has raised the Baltic standards when it comes to passenger comfort and safety – along with providing a stellar user experience.
For more information:
Heikki Tanner
heikki.tanner@valmet.com
+358405570780