Win-win service at Grupa LOTOS refinery
The best service solution is the one that fits the customer’s needs best. At the Grupa LOTOS Refinery, in Gdansk, Poland, our full-fledged customer service is a reality. It features a business focused service agreement, a maintenance presence near the customer and looking after the refinery’s valves and operation.
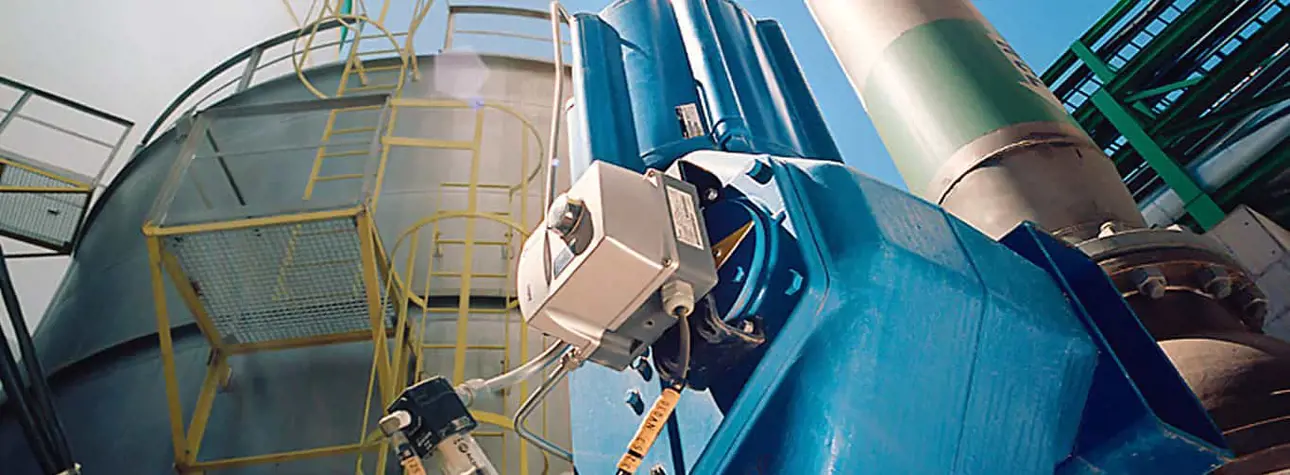
- Highlights
- Grupa LOTOS was looking for a way to optimize valve performance and to maintain peak performance over time.
- We provided the refinery with valve services under a service agreement as well as carries responsibility of and owns contractual stock.
- Key benefits for the customer include strong support in day to day activities in addition to quick response at reasonable cost.
“Valmet Flow Control business line (former Neles) has set a high standard in terms of flexibility and customer approach. We are very pleased that we have such a good relationship and I hope that they will continue to play a bigger supply role in the future with us,” says Grzegorz Bledowski, Technical Director at Grupa LOTOS, about the service that we are providing to the daily work at the refinery.
Grupa LOTOS is one of the biggest refining companies in Poland. The refinery in Gdansk belongs to Europe’s most state-of-the-art refineries and has a leading position in the Solomon benchmarking.
The company has worked with Valmet Flow Control business line (former Neles) for a very long time, and our products have been installed in its units since the refinery started. Some of the valves have been operating for over 30 years and still work very well. Currently over 20% of the control and safety valves. These valves are used in the safety systems and as control valves in difficult conditions. “For me as a customer, it is also important that a supplier has a very strong local office and is able to offer support. Valmet's local office is not only a marketing office, but almost an engineering facility as well, and they provide us with very strong support in our day to day activities. It is important for me to know that the response I get from them is helpful, quick and at reasonable cost,” Bledowski points out.
According to the fully tailored service agreement, the refinery utilizes a local workforce certified by Valmet and services are carried out under supervision. “This is important; not only does it mean we can limit costs, not the most important factor, but we do have to take into account the fact that, in the case of an emergency, we don’t have to wait for support from Finland. We can do something within a few hours. That’s why we have to keep on site sufficient and proper spare parts and we have to be able to repair everything, to find a solution based on local capabilities,” Bledowski continues. “For example, if we have a problem with the units at the plant, with the application, the medium, pressure, dust or rust, together we can find a good solution to the problem. I prefer to have the problem solved once and for all, not to continuously repair. And Valmet Flow Control provides exactly this service and support via their Polish branch office.”
All parties win
As part of the new strategy, responsibility and ownership of contractual stock has been shifted from Grupa LOTOS to Valmet. Bledowski puts in: “It’s a win-win agreement. During negotiations, Valmet demonstrated a very positive attitude and flexibility. Our internal service company, Grupa LOTOS Service can also learn from it and improve their know-how and in turn they can learn from our experiences, so both companies get something out it.”
The text is based on an article published in Valve World magazine January / February 2014.
Text originally published in 2014, and slightly updated in April 2022, due to the company name change to Valmet.
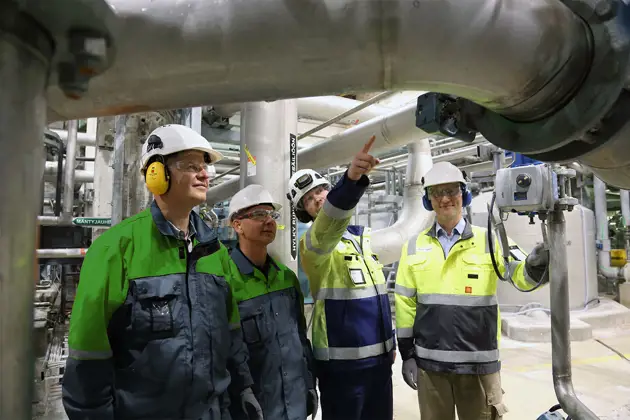
Subscribe to our newsletter
Subscribe now to flow control newsletter and receive the latest insights directly to your email.
SubscribeRead more customer success stories