Valve Performance Monitoring service maximizes plant reliability at Mercer Stendal
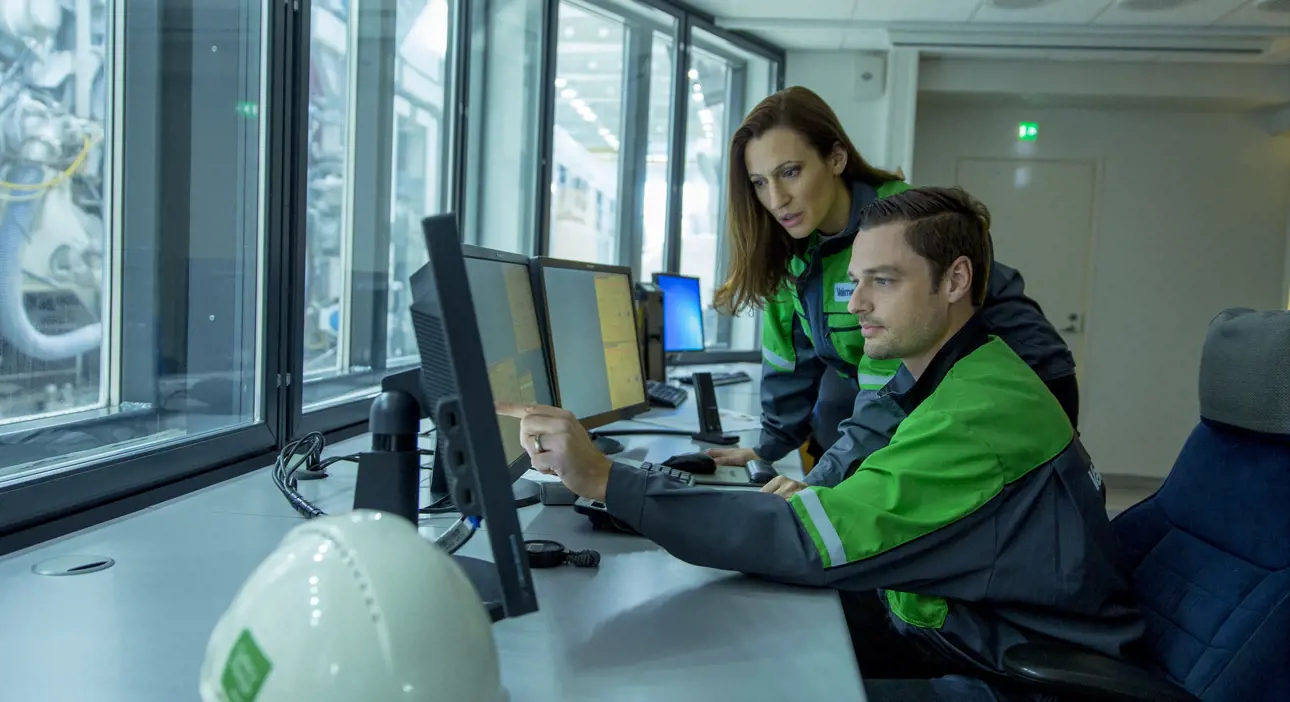
Valmet Valve Performance Monitoring (VPM) is a digital service designed to ensure plant availability and reliability by predicting and preventing valve-related issues. The service is built to detect valves which have some degradation in the performance, to provide expert recommendations and offer service support to solve potential malfunctions.
Almost one year ago, a VPM service agreement was signed with Mercer Stendal’s pulp mill in Germany. The 5-year Valve Performance Monitoring (VPM) agreement covers monitoring of the most critical 500 valves, 24/7 online valve monitoring and the delivery of four expert diagnostics reports per year. The diagnostic findings are followed with interactive tickets in the Work Flow Hub platform to ensure every issue is treated and solved. All the information, such as dashboards and reports, are available and updated at the customer’s cloud collaboration space Valmet Customer Portal, which is a part of the Valmet Industrial Internet (VII) platform for valves.
Long-term partnership
Mercer’s pulp mill in Arneburg uses Valmet’s technologies broadly, from automation to flow control solutions. Mercer Stendal is running the plant with Valmet DNA, and they have an installed base of 1000 Neles™ valves. This new agreement is a continuation of the modernization of their plant.
“We have a long relationship with Mercer Stendal. They rely on our products and the previous Neles™ NDX™ replacement project was very successful, proving that we are a reliable and sustainable partner to work with. Now, they want to better utilize the data coming out of their valve positioners. Valmet is doing the online 24/7 valve monitoring, interacts continuously with the customer and every three months we combine the findings into a diagnostics report. The findings and expert-recommended actions are then discussed with the customer until a conclusion is reached. To enhance resource efficiency, VPM service ensures a more targeted approach to maintenance, while outsourcing the monitoring and analysis tasks”, says Christian Beig, Sales Manager, Valmet Flow control business line.
Proactive maintenance ensures reliability
The main objective for Mercer Stendal is to switch from a reactive mode to a proactive mode in valve maintenance. By taking a reliable proactive approach and predicting progressive failures, both plant uptime and the availability of their valves are increased. With Valmet’s VPM service, Mercer Stendal will receive continuous expert service recommendations for valves, actuators and positioners and the right service support to solve all issues found. The service also helps to find the exact valves that need to be serviced during the next shutdown. Furthermore, they can focus only on the critical valves and save time and money.
“Over the past six months, we have worked together with the customer on going through the findings of what occured after implementing the service recommendations. We have seen this led to a positive impact on plant production and improved product quality. In addition, the service enables better process optimization, as the fine-tuning and stabilization of the valves leads to energy savings. There’s a growing trend to move towards digitalization also within the process industry globally. A proactive maintenance approach and utilization of valve data and diagnostics can save a lot of customer’s valuable time and money. Our expert service helps them move forward on their digitalization journey. I’m happy to see that our customers’ value our knowledge and capabilities to offer these kind of services,” says Boris Volavicius, Digitalization Sales Director, MRO and Services business unit, Flow Control, Valmet.
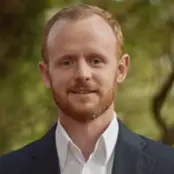
Boris Volavicius
Digitalization sales director,
Valmet flow control business line
Read more
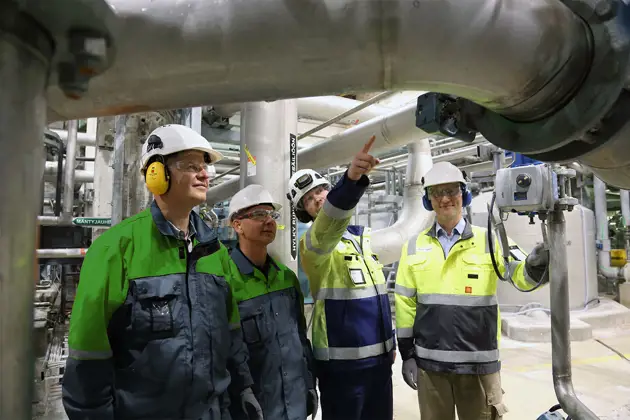
Subscribe to our newsletter
Subscribe now to flow control newsletter and receive the latest insights directly to your email.
Subscribe