The importance of advanced peristaltic pumps
There are two methods to make pumps last longer in abrasive mining operations. One is to harden internal metal components to survive longer than softer metals. The second way is to utilize rubber, which is softer. Sharp or abrasive minerals bounce off elastic rubber surfaces with little damage.
More advanced peristaltic pumps, such as a Flowrox peristaltic pump, have increased rubber hose lifetime and pumping availability and also significantly reduced operating costs. Since the 1930s, peristaltic pumps have utilized either two rollers or two metal bumps (shoes) to compress the rubber hose twice every 360-degree revolution. A new design utilizes a crankshaft and a single heavy-duty roller to compress the rubber hose. This is important because the life of a rubber hose is determined by how many times the hose is compressed per revolution. In dual shoe designs, the hose is compressed twice as frequently. The eccentric shaft single roller design will thus produce at least double the hose lifetime.
Filtration
Peristaltic pumps are ideal for thickener underflow, flocculant delivery, reagent delivery, filter feed and any application requiring a high solids content. In many cases, a mining operation will deliver 35% mineral slurry and 65% water to a pressure filter to separate the two fractions.
However, it may be in the mine’s best interest to significantly increase solids content to 60% mineral slurry and 40% water. Often, this is done with the thickener before delivery to the pressure filter. An increase to 60% solids will reduce the filtration retention time and increase filter performance, may help produce a dryer cake, and ultimately lead to more tonnage processed and a direct contribution to the bottom-line profitability of a mining operation. If the suction piping to a peristaltic pump becomes clogged, it is also possible to reverse the pumping direction and blow out the clog.
A thickener underflow Flowrox peristaltic pump can produce up to 80 percent solids for the pressure filter, reducing filter retention time, produce dryer cake and improve the mine’s overall profitability.
Pumping capacity
Unlike centrifugal pumps, peristaltic pumps do not lose pumping capacity when resistance and pressure increase. A peristaltic pump produces exactly the same flowrate per revolution and can be controlled extremely accurately simply by increasing or decreasing the pump’s rotational speed. In the pressure filter feed, the peristaltic pump can pack the filter chambers more tightly, producing uniform cake throughout each chamber.
Flocculants and reagents
Peristaltic pumps are ideal also in the delivery of flocculants and reagents to both the thickener and the flotation process. These chemicals are often shear-sensitive, and a pump that shears these chemicals is not ideal. A peristaltic pump is low-shear and does not agitate or damage the long polymer chains. The result is greater chemical effectiveness and lower consumption of expensive chemicals.
Extreme heat
The second most devastating variable for rubber hose peristaltic pumps is extreme heat. A single eccentric roller design peristaltic pump can pump at temperatures up to 203°F (95°C) at the pump’s full rated pumping capacity. However, a dual-shoe-designed peristaltic pump will have to limit its pumping speed to approximately one tenth of its rated capacity due to the heat the rubbing action creates, to avoid destroying the rubber hose prematurely. Most shoe design pumps require a massive amount of glycerin in the pump housing which creates both extra costs and work. A single eccentric rolling design generates virtually no heat and thus utilizes approximately one tenth of the glycerin simply to lubricate the rubber hose. With heat and dual compressions, an eccentric single roller design can produce up to two to five times longer hose life, and often, the pump can be one to two sizes smaller, while still improving hose lifetime compared to the shoe design.
Text by Todd Loudin. For more information about Flowrox pumps, contact markus.rossi@valmet.com
Text originally published in World Pumps magazine May/June 2024 issue.
Related readings
Discover the product pages
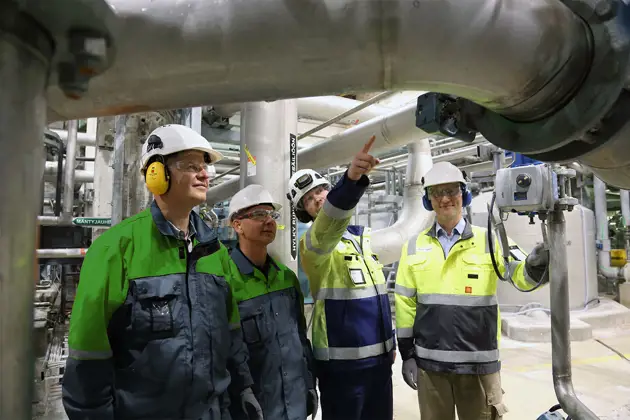
Subscribe to our newsletter
Subscribe now to flow control newsletter and receive the latest insights directly to your email.
Subscribe