Taking the guesswork out of properly sizing an assembly
The cause of the valve-related problems encountered in industrial applications often lies in an inadequate selection of valves in terms of their sizes. Modern software for intelligent valve sizing incorporates the manufacturers’ laboratory data and experience-based algorithms to come to the aid and eliminate possible valve misbehavior.
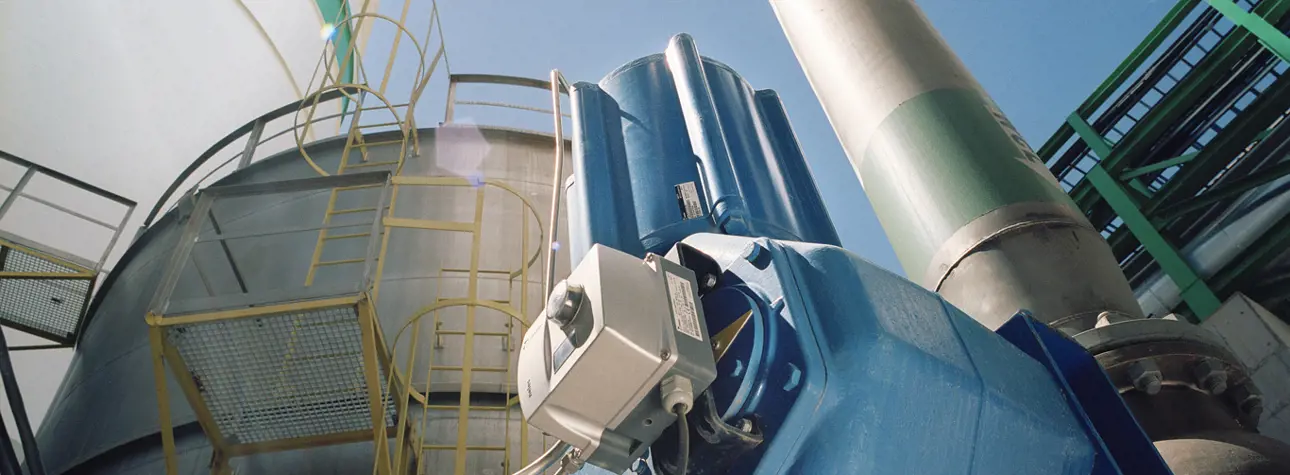
How real-world data make modern valve sizing & selection tools more efficient. Some have said, “experience is the best teacher.” This adage not only applies to life in general, but also in the quest for the most effective process for the sizing and selection of valves for industrial applications.
- Valve sizing and selection
- The software can be beneficial to different types of end-users, including processing plant end users, service providers, contractors and engineering firms and consultative sales representatives.
- Control valve selection elements that every processor should consider, among others, include flow velocity and erosion, noise and cavitation, and actuator load factor.
Unfortunately, even today, valve sizing and selection is not typically experienced based. Instead, the sizing and selection process all too often relies on standard equations and rules of thumb, which are applied to valve performance data collected in the manufacturer’s laboratory. The laboratory data is very accurate in itself. However, the rules of thumb make very broad assumptions about flow conditions that will be present in the actual system.
Often, this assumptive process is good enough and the valves selected will be durable and adequate to their purpose. On the other hand, when valves misbehave and the result is poor process control, reduced output, component degradation due to noise, vibration and cavitation, and unscheduled downtime, the root cause of the problem is likely an inadequate selection process due to the over-reliance on generalized rules of thumb.
This problem can be fixed. Over several decades, valve manufacturers have collected performance data on tens of thousands of valves in the field under actual line conditions. In the early days, this research involved going to the installation and measuring relevant conditions. Within the past decade, microprocessor- based data collectors embedded in valve controllers have geometrically expanded the amount of data available for process system modeling. Users who take the time to accurately model their processing line conditions can now rely on more accurate equations so that they can select and size valves, actuators and trim with a substantially higher degree of resolution.
Expert sizing software compresses what used to take days into hours and minutes and yields sizing and selection information for critical valve applications that can frequently deliver a huge payback in terms of improved process safety and productivity.Steven Hocurscak, Business Manager, (former) Neles & Mapag
Of course, modeling line conditions and applying line-specific equations to a range of possible valve choices until the best fit is obtained can be very time consuming. This is where expert sizing and selection software comes in. This software incorporates the manufacturers’ laboratory data and experienced based sizing algorithms. The software has the intelligence to guide users through a semi-automated line modeling and component selection procedure during which various flow performance outcomes are observed as various valves and components are swapped in and out of the system. This results in the best possible combination of valves, actuators and trim for the process loop in question. Expert sizing software compresses what used to take days into hours and minutes and yields sizing and selection information for critical valve applications that can frequently deliver a huge payback in terms of improved process safety and productivity.
Many variations
Several manufacturers have offered expert sizing and selection software and refined their selection processes and algorithms over many successive years—sometimes decades. While they all, to some degree, make selection and sizing easier, they also have unique differences in terms of the operator interface, library of valve types, models, actuators and trim components available, and the variety of analyses that can be performed. Some users who want to compare components from different manufacturers may find this tool frustrating, since vendors can only include their own products in the library, and they don’t have access to all of the competitor options and performance data.
Until recently, most expert sizing software focused on control valve applications. This makes sense because control valves are most critical for assuring optimum process performance, end-product quality, and productivity. However, over the years, releases of expert software have added new analytical capabilities and valve types. For example, new calculation modules have been introduced that enable the selection of intelligent automated on/off valves and emergency valves. An on/off calculation tool allows the selection of metal- and soft-seated on/off valves with advanced actuator sizing, including adjustable safety factor and torque key figures. By using the tool, users can select the actuator more quickly and accurately in the engineering phase. They can also use the mass calculation tools to select a number of interrelated package components simultaneously. For ESD (Emergency Safety Device) valve sizing, safety requirements (such as an actuator-sizing safety factor or a complete valve assembly safety integrity level) can be evaluated using special tools within the software program. The SIL (Safety Integrity Level) module for final element PFD (Probability of Failure on Demand) calculation allows both 1oo1 and 1oo1D (D standing for diagnostics) final-element calculation that takes into account the use of a valve, an actuator, and a partial-stroke test device. In addition, one-to-several pneumatic components can be taken into account in the calculation.
How it works
Successful control valve sizing and selection depends on knowing the actual process conditions in the system in which the valve is to be installed.
This information is rarely available first hand. The more assumptions one has to make on flow conditions, the less accurate control valve sizing is going to be. Fortunately, when a few flow conditions are known accurately, an algorithm can be found that can model the behavior of a given control valve for the whole flow range. Expert sizing software leads the user through a sequence of data input steps, which allows for the calculation of this algorithm. Expert software predicts the performance of the control valve package as a part of the system before installation. By comparing the predicted performance of different valves, users can quickly arrive at the most appropriate control valve package to ensure the desired process performance. This procedure allows users to avoid oversizing of valves and undersizing of actuators, reducing valve acquisition and maintenance costs while optimizing process control.
For example, the selection of a control valve is divided into two parts. First, the mechanical selection in which suitable valve style, materials and pressure rating are selected to guarantee safe and reliable performance according to good engineering practices and local laws and regulations. This selection should be made using bulletins and technical information specific for each valve type. Then comes sizing, which is an iterative process resulting in the selection of valve package components that meet process control objectives while preventing unwanted phenomena such as excessive noise or liquid cavitation. After the valve size has been determined, other valve package components can be fine-tuned to optimize the installed performance of the valve to phase out such undesirable control characteristics as hunting, excessive slow, or fast response and poor accuracy. One way this is done is by adjusting controller response patterns to compensate non-linearities detected in the valve’s installed flow characteristic curve. Expert sizing software presents the user with a broad range of mathematical correction and compensation tools to linearize control valve performance as much as possible.
Control valve selection points every processor should consider
Optimal Travel: When a valve is sized correctly, the range of operation will correspond well to the control range of the valve. Travel at normal flow should fall within 50 to 70 percent opening angle. Travel at maximum flow should fall below 90 percent. Travel for minimum flows should be above 20 percent open to avoid erosion of the trim.
1/2 The pipeline size rule: Because rotary valves typically have more Cv than rising stem valves, it’s not uncommon to have a control valve smaller than the pipe size. To avoid valve damage caused by piping stresses, the valve size should not be less than half of the diameter of the pipeline. When the valve size that best fits the flow conditions is smaller than half of the pipeline, consider reduced capacity trim rather than a smaller valve.
Installed Gain Curve: The installed gain curve indicates how the control valve will perform under the given process conditions. A high gain means small changes in valve position will produce large changes in flow, therefore causing the process to overshoot. Low gain means large changes in valve position will produce small changes in flow, causing the process to behave sluggishly. A constant gain line at 1.0 within the control range would be ideal. For best results, gain should be between 0.5 to 3.0, and the ratio of maximum to minimum gain should be ≤ 2.0.
Flow velocity & erosion: Erosion damage is closely tied to the velocity of the media. This damage is typically seen first on your valve trim, but can also affect the body and downstream piping. The erosion damage is only amplified with the presence of particulate (erosive media), or flashing conditions.
Maintaining a proper velocity, especially when the media is erosive or flashing, is important for extending your valve life.
- Try to maintain opening angles greater than 20 percent open on all flow conditions.
- On clean service maintain velocities lower than 37 ft/sec (32 ft/sec for butterfly valves).
- If media is erosive or flashing, moving to a larger valve should be considered as the added surface area will help minimize erosion
Noise: Aerodynamic noise (noise generated from gases or steam) is strongly related to exit velocity of the media. The concern is mechanical damage of the valve assembly with aerodynamic noise, damage of valve, actuator, or accessory components from intense vibration. Government regulations typically limit noise to 85 dBA if a person will be near the noise source for eight hours or more, however it’s unrealistic to think every valve will perform to that noise level. Keep noise levels below 110 dBA to prevent mechanical damage to your assembly.
Hydrodynamic noise is used to predict cavitation intensity. Manufacturers often have different opinions about cavitation, however it’s also accepted that if you want to eliminate damage you must lower noise down to an acceptable level (which in turn means lowering the intensity of the cavitation). For specific noise recommendations please review your specific valve sizing software for noise levels applicable to your specific size valve.
Troubleshooting specific conditions
Well-developed expert sizing and selection software offers a broad set of tools that can be used to detect a wide range of problems that can occur in a process control loop. The following problem conditions, abstracted from an actual expert sizing software users’ guide, detail some of the most common of these:
1 Noise and cavitation
Problem: High-pressure drop over the valve, compared to upstream pressure, may result in cavitation causing material damages and noise. The predicted noise level depends on flow situation and also on the valve and valve size in question.
Solution: The main principle of reducing cavitation noise is to select a low-recovery, multi-stage, anti-cavitation valve.
2 High actuator load factor
Problem: Valve accuracy is limited, tuning of the positioner and the whole control loop is difficult and the response time for signal changes is long.
Solution: Select larger actuator or check if supply air pressure can be increased enough to enable use of selected actuator. Also, the seat, bearing and gland constructions can be changed to reduce the required torque.
3 High flow marginal
Problem: When required flowrate is considerably less than calculated valve fully open flow, the control accuracy is decreased and control range is narrow.
Solution: If the required flowrate is considerably less than calculated valve fully open flow, then selecting a smaller size valve, lower-capacity valve type, or reduced capacity trim will help. Sometimes this situation is the result of using an equal percentage inherent flow characteristic in systems where the pressure does not change as a function of the flowrate. In those cases, a linear or close to-linear inherent characteristic will help.
4 High flow velocity at inlet port
Problem: Seating area of valve trim may wear leading to decreased tightness. Other parts of the valve may be exposed to wear especially in erosive, corrosive and cavitating conditions.
Solution: Increasing the valve nominal size will decrease the inlet velocity. Sometimes it is necessary to also use reduced capacity trims in order to keep the valve opening at an acceptable level.
5 High flow velocity at outlet port
Problem: If the flow velocity is high, the seating area of valve trim may wear, leading to decreased tightness. Also, other parts of the valve may be exposed to wear especially in erosive, corrosive and cavitating conditions. In some valve types, high velocities may also cause dynamic forces with valve trim that lead to unstable operating conditions.
Solution: Increasing the valve nominal size will decrease the outlet velocity. Sometimes it is necessary to use reduced capacity trims in order to keep the valve opening within an acceptable level. Because of gas compressibility, increasing valve downstream pressure will decrease the valve outlet velocity. Valve downstream pressure can be increased with a fixed restriction, like a diffuser, installed downstream of the valve. The users’ guide to this particular expert sizing software goes on to address 22 additional conditions that may be detected by the software along with providing suggestions for alleviating the resulting problems, such as damaging noise levels, intense cavitation/flashing conditions, and poor installed characteristics (gain) performance, to name a few.
Who can use valve sizing software?
Expert sizing software is a serious control loop optimization tool that can, in the hands of knowledgeable users, harness laboratory data in combination with decades worth of field experience and powerful mathematical models to emulate control valve performance in very close simulations of the processing environment in which they will be installed. The software can be of use, in varying degrees, to many different types of end-users.
- Processing Plant End Users: Engineering departments may use this tool to better understand how various control valve packages perform in a variety of process loops.
- Service Providers: The software can be an invaluable tool for service providers called on to diagnose and fix chronic valve problems resulting in poor performance, excessive wear, and compromised safety.
- Contractors and Engineering Firms: Expert sizing and selection software is an essential tool for engineers who are faced with the task of making cost-effective decisions regarding hundreds or even thousands of valves specified for new processing installations.
- Consultive Sales Representatives: Not every end-user of valves will have sufficient staff hours available for learning and using expert sizing software. This does not mean, however, that they cannot take advantage of it. Vendors who are engaged in consultive selling frequently have extensive training in this important tool. To take advantage of all that one can learn from it, all a prospective customer needs to do is ask for their assistance.
Text by Steven Hocurscak. For additional information, please contact joonas.korhonen@valmet.com.
Published originally in FLOW CONTROL MAGAZINE • June 2013 as 'Experience matters'
The text has been updated in April 2022, due to the company name change to Valmet.
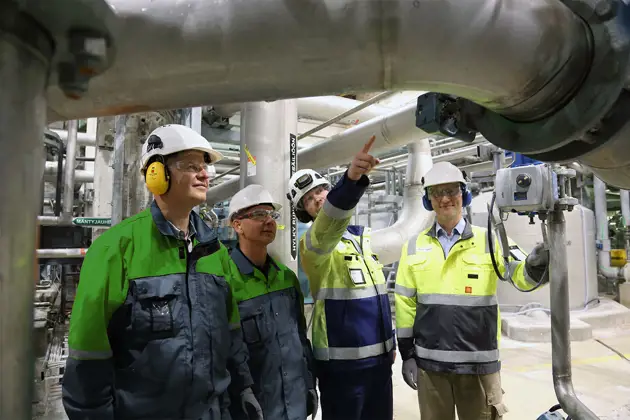
Subscribe to our newsletter
Subscribe now to flow control newsletter and receive the latest insights directly to your email.
Subscribe