Severe service control
Jun 24, 2024
Many services are severe services. High-pressure drop applications are always considered severe service. Selecting a reputable and proven technology and brand is extremely important to the long-term reliability required in these types of applications.
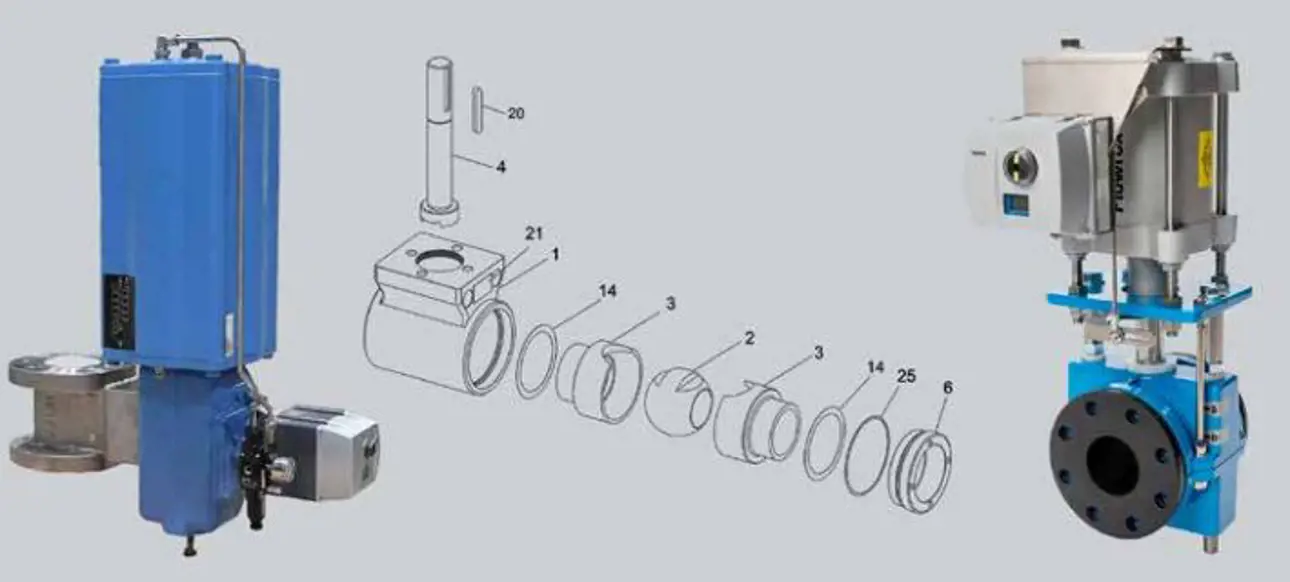
Figure 1: The image on the far left shows a ceramic control valve. The middle image illustrates the ceramic ball with internal ceramic lining protecting inlet and exiting pathways and a blade shaft for rubber and precise positioning. The image on the far right is a slurry pinch valve that utilizes a heavy-duty rubber sleeve, completely isolating all metal components from abrasive and erosive mediums
However, other severe service control valves may not be high-pressure but can be considered severe service control because the valves require abrasion or erosion resistance. With abrasive mediums, there are typically two directions to survive abrasive conditions. One is to make internal components harder, and the other is to make internal surfaces softer, so particles bounce off the wear surfaces.
Ceramic control valves and rubberized pinch valves are two types of valves that have high survivability in abrasive mediums. Ceramic valves offer several desirable features that increase valve performance and lifetime. First and foremost, the ceramic valve should not only have a ceramic ball; the inlet and outlet ports should be lined to protect the flow pattern. Otherwise, the ball could direct the flow pattern into the downstream side of the valve body. If the body is not protected by a ceramic lining, the abrasive flow would
likely wear through even if the metal surfaces had Stellite coating. Partially stabilized zirconium (PSZ) performs better when wide thermal swings may be present. PSZ ceramics can withstand temperatures from -50˚C (-40˚F) to 200˚C (390˚F); whereas unstabilized ceramics may break or shatter with wide thermal swings.
Metal Matrix Compounds (MMC) are a combination of metal and ceramic or both strength and abrasion. An MMC body adds the strength of steel and the abrasion resistance of ceramic. This can be highly advantageous in extreme scaling conditions. For maximum strengthand controllability, the ball and stem engagement of the valve stem should have
a blade style to maximize tightness and provide backlash-free control. Low Cv trims in sizes 1” valves may be helpful in low flow accurate control. In extreme scaling conditions, a stainless steel metal matrix body will provide added protection for the valve body. Ceramic valves are applied to the following common applications:
- Lime Mud Control
- Kaolin, China Clay Control
- Carbonate Handling
- Gypsum Handling
- Cement Production
- Metal Slurries
- Autoclaves
- Catalyst Regeneration
- Desulphurization Units
- Pulp & Paper Recausticizing
There are similarities between the rubber-lined pinch control valve and the ceramic control valve. The rubber sleeve in a high-quality pinch valve can also withstand abrasive and erosive flows. Pinch valves have reduced port sleeves for each valve size specifically designed for process control and tailoring the percent open to provide the most accurate
flow control. Pinch valves have some limitations compared to ceramic valves. Ceramic valves are capable of a much higher temperature than pinch valves.
For example, a pinch valve with a high temperature styrene butadiene rubber sleeve (SBRT) has a minimum temperature of -50˚C (-40˚F) and a maximum of 110˚C (230˚F), whereas the ceramic valve has a maximum temperature of 200˚C (390˚F). Therefore, when the process medium exceeds 110˚C (230˚F), the ceramic valve would be the best choice. A rule of thumb with pinch valves is that 50% of the inlet pressure is the maximum delta P allowed across the control valve is 50% of the inlet pressure. In higher pressure drop applications exceeding 50% of the inlet pressure, the ceramic valve may be the best valve for that application.
Common applications for pinch control valves include:
- Lime Mud Control
- Titanium Dioxide Control
- Mining Applications:
o Flotation
o Thickener underflow
o Hydrocyclones & Magnetic Separation
o Grinding & Screening - Kaolin, China Clay Control
- Calcium Carbonate Handling
- Gypsum Handling
- Cement Production
- Metal Slurries
- Pulp & Paper Recausticizing
Both ceramic ball control valves and pinch valves are excellent in handling extremely
abrasive and erosive flows. A pinch valve has the advantage when the valve needs repair; all it requires is replacing the rubber sleeve for the valve to be back in service. The cost of the rubber sleeve is only a fraction of the cost of a new ceramic ball and inlet and outlet liners. However, each customer must determine what they feel is best for their process.
Cavitation and flashing control
All control valves should be sized for process conditions. Sizing programs consider the entered process conditions and calculate the best valve and percent opening to accomplish accurate flow control.
Sizing programs detect if incipient or critical cavitation will occur, predict noise levels, and calculate the velocity through the control valve. If the sizing reports higher than recommended manufacturer’s levels, alarms will be displayed. If that occurs, selecting a different size valve or even an alternative valve design may be the solution.
If cavitation is detected, there are special rotary control cavitation control devices that can be deployed. Cavitation occurs when the pressure drop through the valve becomes high enough. When the medium passes over the vena contracta (smallest opening through the valve during control), the medium turns to steam because it dips below its vapor pressure. When the pressure recovers after passing the vena contracta, millions of bubbles implode or collapse causing cavitation. Cavitation is extremely damaging to all types of valves and shortens the lifetime of a valve’s internals.
Newer technologies in rotary control valves employ a tortuous flow path over several stages to reduce the overall pressure drop so that it never dips below the liquid’s vapor pressure.
Intelligent positioners offer significant cost and energy
Intelligent positioners have been in existence for many years and the information to end users is often underutilized. More advanced designs reduce air consumption considerably and can save users approximately 90% per year per valve in produced or wasted air consumption. These savings can be significant when there are several thousand positioners in a large processing complex. The greatest advantage of an intelligent positioner is the ability to predict changes in the control valve. These changes may be only minor fatigue, or they could be signaling catastrophic valve failure, which, when detected early, may save the processing unit thousands, if not hundreds of thousands, of
dollars annually.
Figure 2: The above illustrates Q-trim in a ball control valve. The attenuator plates cause a pressure staging, the result being the medium never dips below the medium’s vapor pressure; thus, the valve does not cavitate. This type of trim is also very effective with aerodynamic noise reduction. It can reduce noise levels in certain instances by 20-30 dBa. If the attenuator plates become clogged, the input signal to the valve positioner will tell the valve to open more (even up to 100% open) and the clogged attenuator plates will automatically flush clear debris and return to optimum flow control.
Some valuable features of an intelligent positioner to consider:
- Simple and fast installation and commissioning – autocalibration
- Local/remote operation
- Wide language support
- Expandable architecture
- Hare Protocol rev. 7 and Foundation Fieldbus
- Full suite of diagnostics on every unit
- Self-diagnostics
- Online diagnostics
- History trends
- Communication diagnostics
- Extended off-line test capabilities
- Worldwide support for hazardous area approvals
- Standard Local User Interface (LUI) accessible without opening the device cover
- Distributed Control System (DCS) asset management program
Ideally it is best to select a brand that has the full suite of diagnostic capabilities loaded onto each positioner and can seamlessly interface with third-party assets or performance management systems. The information is always there for the user to access when and whether they ever use the diagnostics. Some positioner manufacturers’ prices increase as new levels of diagnostic capabilities are added, while others load the full suite of capabilities on every positioner for the same price each time.
Figure 3: Neles NDX intelligent positioner offers a linkage-less design, a full suite of diagnostic capabilities, extremely low air consumption with 40 service centers worldwide, and global product support.
Conclusion
When dealing with abrasive slurries, it is rarely a good idea to try to utilize standard valves used typically in clean mediums. In slurries, they typically fail frequently and lead to excessive OPEX budgets. Choosing the right valve is paramount to reducing operating costs and limiting downtime. Time spent choosing the correct product will lead to lower operating costs and expenses, less downtime, and greater profitability.
Text by T. Loudin. For more information contact raimo.lavikainen@valmet.com.
Text originally published in Valve World Americas Journal, May 2024 issue.
Discover more
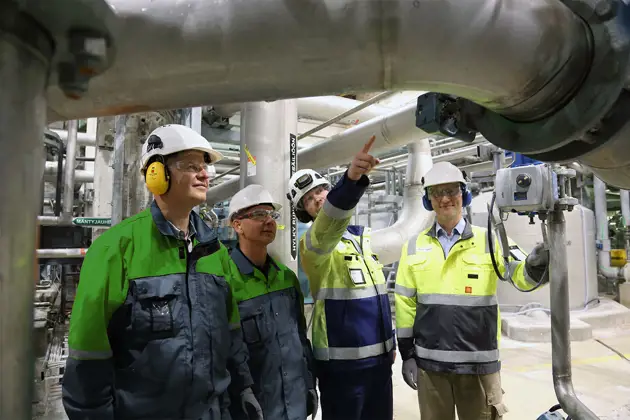
Subscribe to our newsletter
Subscribe now to flow control newsletter and receive the latest insights directly to your email.
Subscribe