SCA shows the way - saving on installation time and costs
Svenska Cellulosa Aktiebolaget, headquartered in Stockholm, Sweden, operates its largest integrated plant in Europe in Mannheim, Germany. With Valmet (former Neles) technology, SCA increases system availability and saves installation time and costs at the same time.
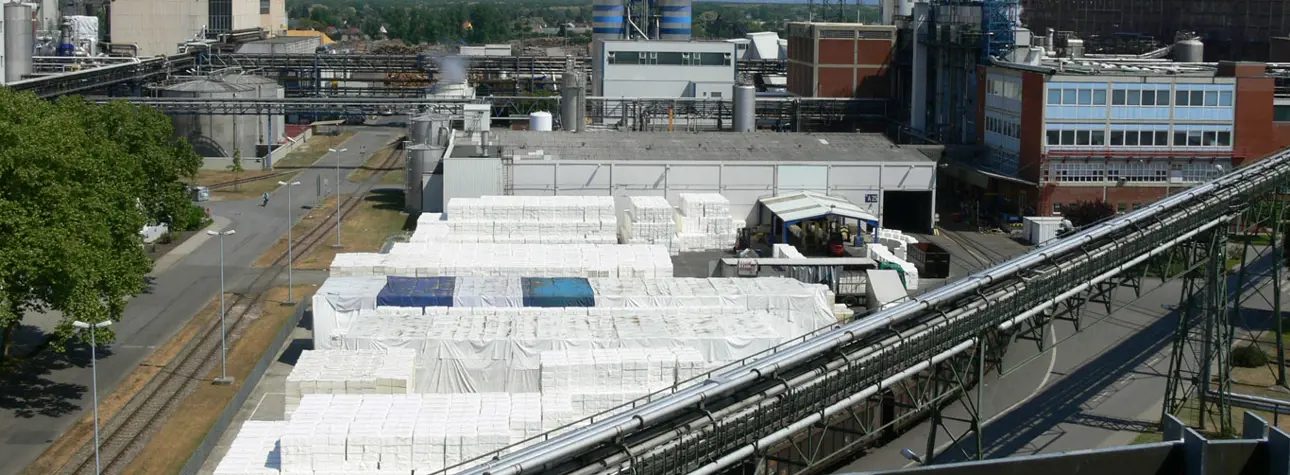
At SCA Mannheim, approximately 610 tonnes of pulp a year for use within the company as well as for external customers are produced using continuous and batch cooking technologies. The high production volume demands systems that are safe and reliable in every detail. These include in particular the Neles™ SwitchGuard™ for frequently switching on/off valves as well as the Neles DNA process automation system.
There are no comparable devices on the market, says Ulrich Volz about the advanced Neles™ SwitchGuard™ technology. Volz is responsible for Instrumentation & Control Systems in the pulp energy division at the Mannheim SCA plant. He has been familiar with the systems and their potentially weakest points for decades and has therefore relied on Neles valve and control technology for almost 30 years. The Neles™ SwitchGuard™ is unique. “Without this solution, we would still need to go through the labor-intensive and time-consuming process of selecting, fitting and then interlinking different components, such as solenoid valves, limit switches, throttles or boosters,” explains Volz.
SCA operates two pulp production lines in Mannheim. An annual output of 610 tonnes of pulp is used at the plant. SCA utilizes it to produce about 4 million packs of tissues as well as 1.3 million rolls of household towels and 2.4 million rolls of toilet paper daily. At these production volumes, it is not surprising that system shutdowns are only acceptable at precisely planned intervals. It goes without saying that required maintenance work needs to be carried out as quickly as possible.
60 intelligent on/off valve controllers save time in installation
“A significantly simplified installation process was our main criterion for changing over to the Neles™SwitchGuard™ three years ago,” explains Volz. He adds, “The only alternative would be a conventional installation with a complex array of instruments. The great advantage of this valve controller is that it is so compact, we clearly save a lot of time during installation. SCA uses about 60 of the intelligent on/off valve controllers, 16 of them for the continuous digester only. The on/off applications are controlled by a 4–20 mA signal from the Neles DNA process control system. Position transmission is carried out using integrated limit switches or a 4–20 mA signal. “Because of the excellent results over the years, Neles is one of the main suppliers for our plant,” explains Volz. “Therefore, we also use Neles’s RA and RE series valves as well as its process automation system for controlling the entire plant.”
The continuous digester is equipped with 16 intelligent Neles™ SwitchGuard™ on/off control valves. They control, monitor and diagnose on/off valves from the Neles RA and RE series.
Super-fast switching, proven millions of times over
In addition to the plug-in solution of Neles™ SwitchGuard™, it also has a high capacity and excellent switching performance. The screens in the extraction zone tend to clog up easily in the continuous digester. This problem is eliminated by alternate switching of the valves at the digester, resulting in the screens staying clean. The principle is based on valves opening very fast. This does not only require high capacities, but, above all, excellent switching properties of the on/off valve controller.
Ulrich Volz points out: “We make optimal use of adjustable opening and closing time profiles. In this way, we achieve the exact valve switching times we need, and at the same time, we benefit from the minimized pressure impact in the pipes. The valve opens within one to two seconds, but it closes, as required, slowly, within five seconds.”These switching properties must remain constant, millions of times. Each individual Neles™ SwitchGuard™ switches every 1.5 minutes, 24 hours a day.
Monitor, diagnose and plan proactively
During operation, the Neles™ SwitchGuard™ analyzes the performance of the automatic on/off valves online and stores the diagnostic data for future needs. Thus, the valve state is constantly monitored and potential problems can be identified early on. Evaluation of the diagnostic data for proactive maintenance guarantees high process availability as well as high valve reliability. This aspect is very important for valves being used in integrated pulp production lines: the continuous pulp production process is the basis for tissue production at SCA Mannheim.
Despite many challenges, Ulrich Volz remains relaxed: “Should an error occur at the intelligent controller or the valve, employees in the control room are immediately alerted and receive an error message, so that a quick reaction on their part might still avoid shutdown.” All Neles™ SwitchGuard™ controllers are integrated into the Neles DNA process control system, which is an open platform and connects all company areas, from field level to plant management.
Leading the way in environmental protection and sustainability
Svenska Cellulosa Aktiebolaget (SCA) is a listed international consumer goods and paper products company. The company develops, produces and markets hygiene products, packaging solutions, printing paper and wood-based materials – taking into consideration the principles of sustainability in all its activities. SCA employs approximately 43,000 employees worldwide and markets its products, among them Tempo and Zewa as well as global brands TENA and Tork, in more than 100 countries. Annual sales for 2011 totaled EUR 11.7 billion.
Plant photos courtesy of SCA.
Author: Frank Hasenbach-Bauer
This is an English summary of the text originally published in Industriearmaturen, 2/2012. Also published in Results automation 2/2012 and Results valves 2/2012.
Text originally published in 2012, and slightly updated in April 2022, due to the company name change to Valmet.
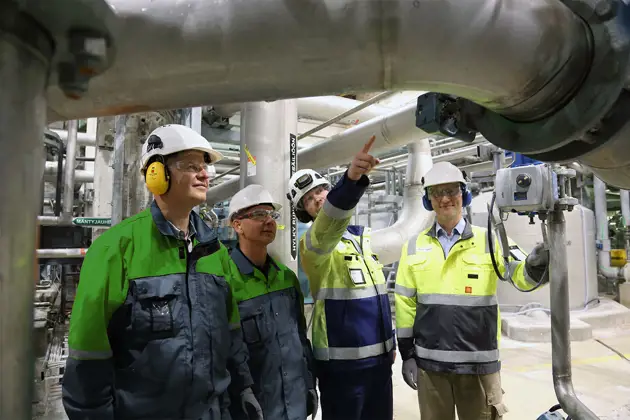
Subscribe to our newsletter
Subscribe now to flow control newsletter and receive the latest insights directly to your email.
SubscribeRead more pulp and paper stories