Reliable future-proof investment of one of the world’s leading accelerator centers
Adapting to changing operating condition is crucial when it comes to the control of refrigeration plants for accelerators. To meet the application’s challenging requirements, the DESY research center trusts Valmet in its selection of intelligent valve controllers and automatic online monitoring system.
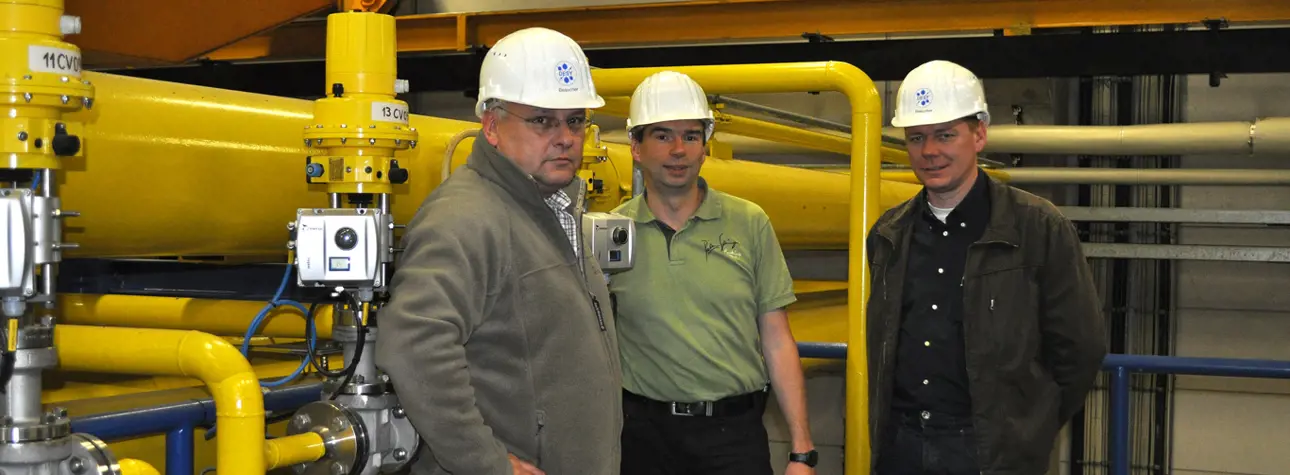
The research centre DESY is one of the world’s leading accelerator centres and is renowned for researching, developing, building and operating particle accelerators. For a long time the HERA ring accelerator was the institute’s flagship project. Its successors are the European XFEL and FLASH. For these two accelerators DESY had to refurbish and modernise the entire cooling system. Neles was commissioned as the general contractor for the complete rebuild of the valve controllers and the air pressure supply of the FLASH cooling system.
“The refrigeration plant operates 24/7, all year round. Therefore, we must ensure outstanding plant reliability.” Torsten Böckmann, Engineer, DESY
Now intelligent Neles™ ND9000 valve controllers regulate all field devices and the Neles FieldCare software optimises online monitoring of all functions. With this stateof-the-art technology DESY achieves the extremely high levels of plant safety and availability that are essential for operating accelerators of this type.
XFEL, FLASH, EPICS, CSS – these are commonly used terms at the research centre, and anyone who happens to overhear the conversations of DESY employees at work must think that they have landed in the future, if language is anything to go by. Here, it is all about particle physics and synchrotrons. Not always easy to understand for outsiders, but apart from fundamental research – how did the universe come into being? – elementary particle physics has brought about applications that we now use in our day-to-day life. This includes the World Wide Web, imaging techniques, radiology and tumour treatment in medicine as well as materials research that many industrial sectors benefit from.
DESY in Hamburg is one of the world’s leading accelerator centers for research
- Valmet installed about 150 intelligent valve controllers from the Neles ND9000 series on the valves of the DESY refrigeration plant.
- Neles™ ND9000 controllers ensure the optimal control of pressure, temperature, flow rate, fluid levels, as well as the rotational speed of the turbines.
- Neles™ FieldCare software optimizes the online monitoring of all functions.
- The linear and rotary valves have been in operation since the construction of the plant around 20 years ago.
Thousands of experiments necessitate extremely high availability
In future the refrigeration plant will serve the superconducting linear accelerator FLASH (Free-Electron Laser Hamburg), whose numerous tasks include serving as a test system for the future European XFEL (X-Ray Free Electron Laser) one of the most powerful sources of X-radiation worldwide. While DESY operates those plants, institutes from all over the world use them for their experiments. Torsten Böckmann knows the problems arising from the strong demand only too well. “Thousands of scientists register their experiments and book time slots for measurements. These slots are planned so strictly and tightly that measurements could not be completed in cases of system faults or, worse, failure. Therefore we rely on these extremely high levels of availability.”
The FLASH refrigeration plant consists of low- and high-pressure compressors, cleaner, line drier, oil removal system and cold box, where the actual cold is produced. “The modernised plant is designed to cool helium down to 2 Kelvin (-271.15° C), so that we attain superfluid helium 2, whose excellent thermal conductivity is required for the experiments,” explains Torsten Böckmann. “We have chosen Neles as our partner for carrying out the necessary modifications.” Neles was responsible for refurbishing the entire air supply system and replacing the valve controllers.
Valmet as general contractor for modernising the plant
As general contractor, Valmet in turn commissioned a sub-contractor to construct the new air supply system and installed approximately 150 intelligent valve controllers from the Neles™ ND9000 series on the valves of the refrigeration plant. Even though the linear and rotary valves have been in operation since the construction of the plant around 20 years ago, they are subjected to very little wear and tear since they are used with a gaseous element; there is little vibration and the site is very clean. “These are ideal operating conditions for valves, but with the system having been in operation for such a long time already we need a monitoring facility to ensure high plant availability,” says Torsten Böckmann. “With the valve controllers we can monitor the valves and identify and resolve potential problems at an early stage.”
150 ND9000 valve controllers provide optimal control and diagnosis functionality “We do not have the manpower to size and calculate all control cycles in advance and to set all relevant parameters. We rely on these processes taking place automatically and control parameters adapting to changing situations by themselves,” says Torsten Böckmann. The Neles™ ND9000 delivers on that front: it corrects itself during operation and adapts its parameters according to operating, process and environmental conditions. If several corrections need to be made with regard to the same issue, the ND9000 reports to the operator that a different solution is required for that particular problem. On this, Torsten Böckmann says, “the clever features of this controller are its diagnostic capabilities and the fact that sensor technology and diagnostics are fully integrated so that the sensors have a direct influence on valve control”.
FieldCare software with PROFIBUS monitors field devices
A further logical step by DESY was the decision to use the device and asset management software FieldCare to monitor all data from the approximately 150 Neles™ ND9000 in use at the plant. Torsten Böckmann calls this combination of intelligent valve controllers and automatic online monitoring system “a reliable, futureproof investment, especially since we no longer have redundancy built into the system. The system is well designed and we can perform a lot of tasks intuitively. We use this software as a bridge system for importing the data from the valve controllers into our own control system called EPICS. We use this basic system in combination with our own Java-based graphic interface CSS, which enables us to visualise all aspects of the control process. Unfortunately it is not possible to access the FDT/DTM technology with EPICS directly.”
However, Neles™ FieldCare is a FDT/ DTM-based software tool (FDT = field device tool) for configuring, diagnosing and monitoring field devices irrespective of their vendors. This system provides DESY as the refrigeration plant operator with all relevant information required for configuration, operation and maintenance of the connected field devices. All field devices can be managed using just this one tool, since the full functionality of the field devices is available via the relevant DTMs (device type managers). In addition, the integrated “Condition Monitoring System” ensures automatic output of all information in real time. Through a web-based interface it is even possible to access the data remotely. This online status monitoring system automatically collects all device and diagnostic data as well as warnings and error messages under real process conditions, sends the information to the operator and visualises and records it.
All measurements are stored as trends, so that the respective diagnostic parameters can later be traced back across the entire operational period and the data can be used for very precise forecasts. Thus, Neles™ FieldCare supports conditionoriented maintenance: based on the data collection, DESY can devise a precise maintenance schedule, which also allows for sufficient time to source spare parts. For Torsten Böckmann the biggest advantage is “that we can operate the refrigeration plant 24/7 throughout the year without failures. And that we are able to identify and resolve potential problems in advance, so that we will not suffer any system downtime. For the future we envisage an operator-less plant and the use of Neles FieldCare not only for the refrigeration plant, but also for the European XFEL accelerator directly”.
DESY in Hamburg is one of the world’s leading accelerator centres for research on matter. DESY develops, builds and operates accelerators and detectors for research with photons and particle physics. DESY is a publicly funded national research centre and member of the Helmholtz Association. DESY also has a location in Zeuthen. Image © DESY
With more than 50 years’ extensive experience in developing, building and operating accelerators, DESY is a global leader in photon science and particle physics. DESY’s collaboration with companies from various industries has led to important innovations in the fields of electronics, refrigeration, high-frequency and vacuum technology as well as the operation of complex superconducting systems.
Graphics © DESY
Text by Ursula Gehl
Article published in Results automation (2/2013) and Results valves (2/2013) as 'FLASH - cold, controlled and well monitored'.
Text originally published in 2013, and slightly updated in April 2022, due to the company name change to Valmet.
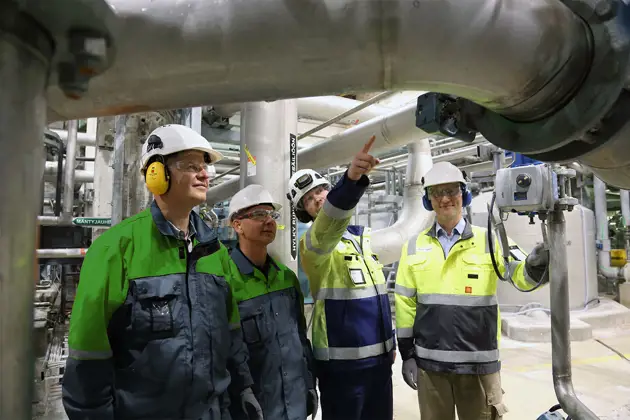
Subscribe to our newsletter
Subscribe now to flow control newsletter and receive the latest insights directly to your email.
SubscribeRead more customer success stories