Q&A with expert: Juha Perttilä
Mar 21, 2018
Thorough and rigorous testing plays a key role in ensuring the quality of our products. We asked Juha Perttilä, Manager, Laboratory Engineering, to tell us more about everything our valves have to endure before they are ready to be shipped out to our customers.
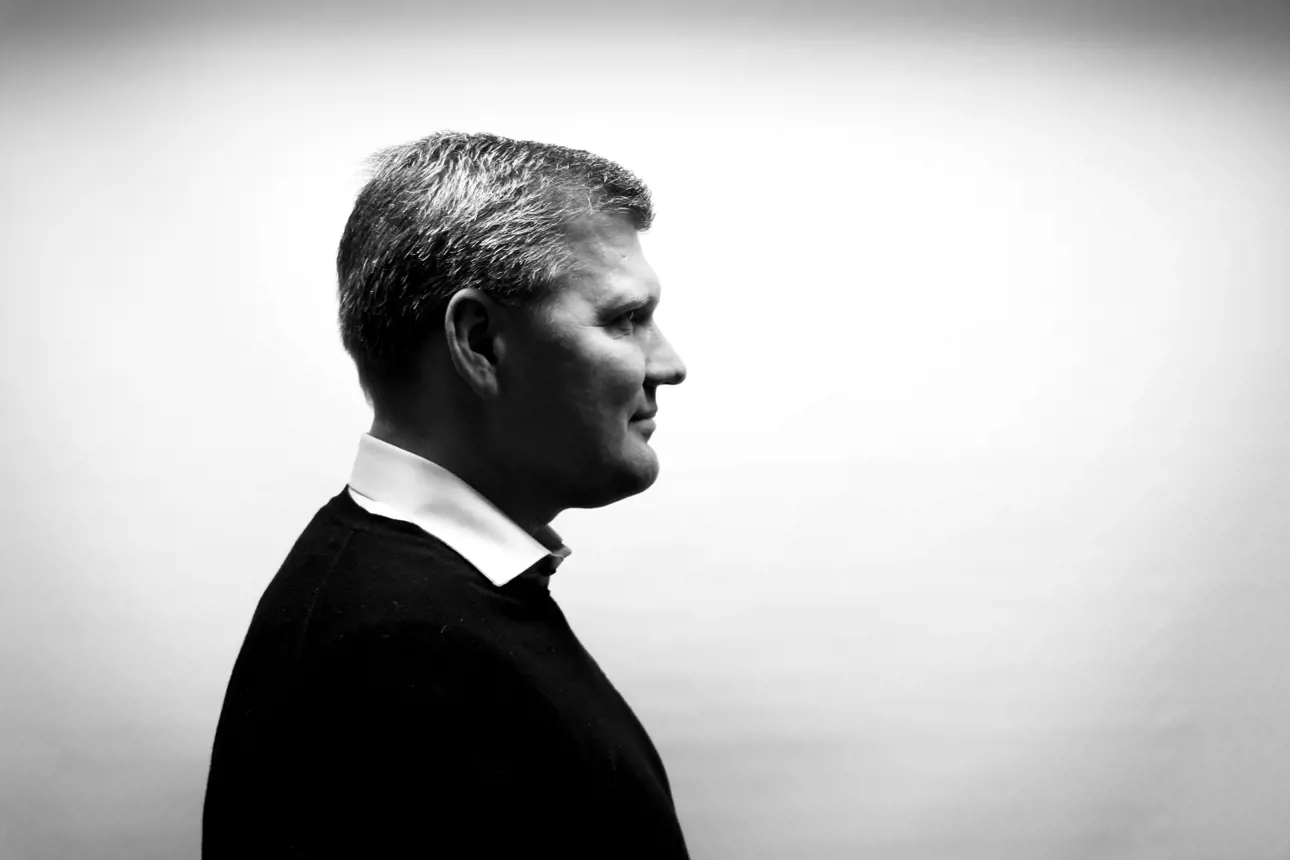
Valmet tests all of its valves before delivery. Where does this take place?
All delivered valves are inspected in the factory before delivery. Product development and performance verification testing along with product type and flow testing happens at our state-of-the-art valve technology centers located in Finland, USA, Germany, China and Korea. Each facility is a unique combination of R&D and technology laboratory. This is where we verify and validate our products and their performance.
Why is testing so important? Why do we do it?
Many of the requirements for our products come from international standards and from individual customer specifications. The standards and specifications usually require demanding tests and a deep understanding of related issues. The primary focus of these requirements are safety, the environment and operational performance. The design and set-up for all this testing requires the development of unique and specialized equipment, as well as deep knowledge of process automation and data acquisition.
Juha at his work station
What do you think is the primary importance of reliable, tested valves?
Even if the operational performance, reliability and accuracy of our valves is the reason to buy them, we never take any shortcuts when dealing with issues relating to human safety or environmental performance. Preventing catastrophic failure is often a matter of both ensuring continued plant availability and the safety of personnel working on-site.
How can we duplicate real operating environments in the lab?
We carry out comprehensive environmental testing to ensure our products perform reliably in even the most demanding and extreme operating environments and severe process conditions. Since our valves are used in such a wide variety of environments and process conditions, we must be able to duplicate these demanding conditions in order to test and verify product performance. Inside our environmental test chambers, we simulate different humidity conditions and temperatures from as low as -75˚C to over +800˚C. Salt spray chambers are used for accelerated corrosion testing to verify the performance of paints and other coatings, while vibration tables help test performance under severe process conditions and a wide range of frequencies.
Performance under extreme temperature conditions is tested in Neles’ cryolab
Can we also prepare for when something goes potentially wrong?
Yes. We also take precautions to ensure valve safety in situations when things do go wrong. We carry out fire testing to simulate a fire in a plant or factory. The tests are carried out in accordance with international industry or customer standards. We want to make sure that internal or external leakages won’t contribute to expanding the fire. This is done by exposing the valve to high-temperature flames for 30 minutes before rapidly cooling it with cold water to simulate extinguishing efforts. We design all our valves to be able to withstand such a severe thermal shock.
Minimizing fugitive emissions is also a priority. Can you tell us about that?
Fugitive emissions from valves are generally gaseous substances, which can be hazardous or lethal to people, or are damaging to the environment, such as severe greenhouse gases. Dangerous leakages should be avoided at all costs. Fugitive emissions from industrial processes are regulated and monitored closely by governments all around the world, and demands for tighter limits continue to be applied. High-quality testing plays a vital role in developing new and better sealing technologies, minimizing fugitive emissions.
Testing for fugitive emissions is difficult and demanding. Internationally recognized testing standards are used to verify and classify fugitive emissions performance. Each Neles valve is tested by pressurizing it, normally with helium or methane gas, up to its maximum design pressure, which can be as high as 250 bars. Any leaking test gas is then detected from outside the valve with a highly sensitive mass spectrometer, gathering every atom of gas. The test temperature cycles between the minimum to maximum rating and can vary from -196 to over 400 degrees Celsius. During a fugitive emissions test, we operate the valve tens or even hundreds of thousands of times.
But testing is also about ensuring the performance of our valve solutions, right?
Exactly. As important as safety and environmental performance may be, one of the most fundamental requirements for valve technology is performance. All valves must be pressure tested to ensure they withstand their defined ratings. Valve sealing tests are carried out to ensure tightness under all possible process conditions. To ensure valve endurance, they are often subjected to more than 5 million cycles to ensure sustained performance over time. Actuator performance is also tested, both on its own and together with valves. For overall performance in some of the hottest and coldest environments in the world, actuators must also be verified to perform for millions of uninterrupted cycles. Equally stringent testing must be carried out on all actuators leaving the Neles factory.
Flow testing is a critical operation. Can you give us a crash course?
Sure. Making sure your media flows through our valves as they are meant to is possibly the most critical aspect that we must test. The correct flow coefficients are essential to be able to select the correct valves for your process applications, and they yield better process efficiency, longer life expectancy, as well as lower investment and usage costs. The main control valve sizing coefficients measured in our flow laboratories are the valve flow characteristics, flow coefficient (Cv), valve pressure recovery factor (FL), differential pressure ratio of incipient cavitation noise (xFz), and pressure differential ratio factor at choked flow (xT). Also valve hydrodynamic and aerodynamic noise levels are measured for determining noise coefficients.
Juha explains the Q-Trim noise and cavitation attenuating technology: "With this element in the valves, we can decrease the pressure in the pipe and inside the valve in smaller steps."
Q9. How else can we ensure performance?
We have to remember that valve performance is not just a matter of design, but equally a matter of selecting the correct construction materials and coatings for every specific process and media. Material testing starts with metallographic testing for chemical composition and heat treatment. Just as we measure the microstructure of used metals under a high-power microscope to evaluate and verify effective heat treatment and check coating morphology, we also regularly test new materials and coatings in conjunction with new technology projects. Neles also performs extensive and complex analyses of polymers such as PTFE. Tribology testing, or wear testing, is used to evaluate materials and coatings used for valve trim, seats, and bearings. Coated surfaces are pressed together and cycled under specified forces for a defined number of cycles. Test specimens are evaluated and measured for changes in surface roughness after the test. After testing new coating materials, the best candidates are then tested in valves for tightness and endurance.
Any final thoughts for our readers?
With accurate and reliable performance verification of all our valve products, we are able to give you, our customer, first-hand information about actual performance levels, quality and safety of the entire valve assemblies. This way, all of our customers can depend on safe valve products while maximizing the productivity of their operations.
Fire testing ensures valves don’t fail catastrophically in case of a fire
Text originally published in 2018, and slightly updated in April 2022, due to the company name change to Valmet.
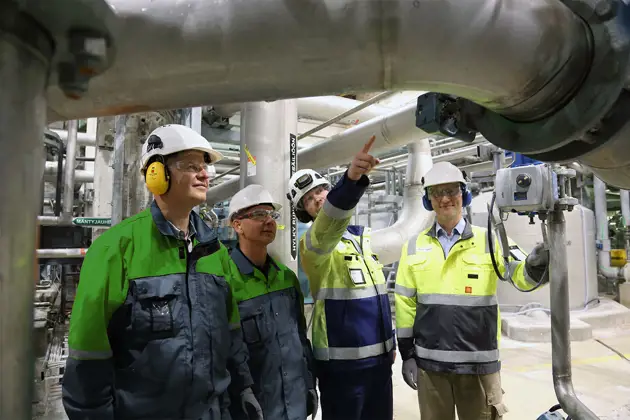
Subscribe to our newsletter
Subscribe now to flow control newsletter and receive the latest insights directly to your email.
SubscribeRead other Q&A's