Meeting the demands of modern industry
Feb 11, 2025
Peristaltic pumps are a proven solution for industries striving to meet their operational and sustainability goals. In industries like mining and minerals processing, the handling of abrasive, viscous, or chemically aggressive media places significant demands on pumping systems.
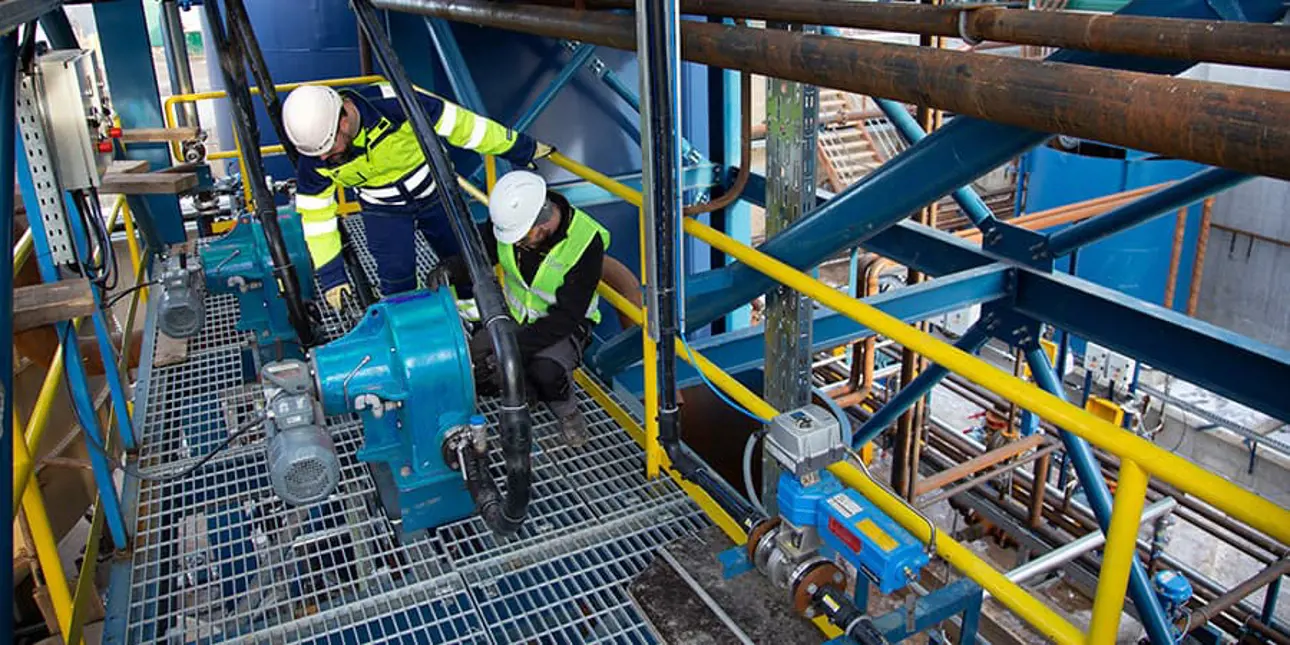
Equipment must operate reliably in industries like metals and mining, often in remote environments, where downtime or inefficiency can lead to considerable losses.
Among the solutions available, peristaltic pumps have carved out a niche, offering performance and reliability that excel under such conditions. Recent advancements in design and condition monitoring have further enhanced their appeal, making them a key choice for some of the most demanding applications.
Resource conservation
Another significant advantage of peristaltic pumps lies in their contribution to water conservation – a critical factor in industries like mining, where clean water is both scarce and valuable. Unlike pumps with shaft seals, peristaltic pumps do not require clean water for sealing, making them particularly well-suited for arid or resource-limited regions.
The ability to operate efficiently without dilution or added water also enhances process performance, especially when handling high-viscosity slurries or concentrated media. Combined with reduced lubricant consumption and extended component lifetimes, these factors underscore the role of peristaltic pumps in achieving sustainable industrial operations.
Single roller design
Traditional peristaltic pumps have long been known for their ability to handle thick slurries, abrasive fluids, and chemical media. However, many designs have limitations: overheating during continuous operation, excessive hose wear, and high lubricant consumption. Innovations in single roller design have addressed these challenges.
The single roller mechanism allows the pump to operate 24/7 at full speed without overheating. Unlike shoe-design peristaltic pumps, which require slower speeds or frequent cooling breaks, this system maintains performance even under prolonged, demanding workloads. As a result, industries benefit from uninterrupted operation, particularly in critical processes.
Additionally, the single roller design significantly reduces lubricant consumption,
requiring far less glycerin, which translates to lower maintenance costs and reduced waste. Another key advantage is the extended hose lifetime. The roller exerts less stress on the hose compared to shoe designs, slowing wear and minimizing replacement intervals. Over time, this results in lower operational costs and improved reliability.
Operating principles
Peristaltic pumps differ fundamentally from other pump technologies. Unlike centrifugal
pumps, they do not slip or cavitate when flow is restricted with a valve. Instead, restricting flow creates a significant pressure increase, which can damage the system if safety measures like pressure monitoring or torque tripping are not in place.
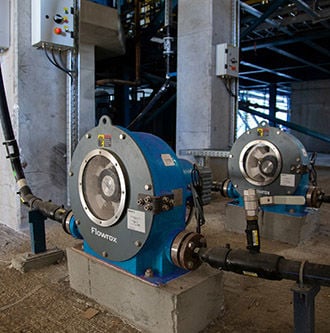
The rolling technology in Flowrox pumps allows for 100% utilization time at maximum speed, unlike shoe designs that require lower speeds or cooling breaks.
Because the pump curve is essentially linear, adjusting the pump speed is a far more effective way to control flow. Running the pump toward a closed valve will inevitably cause failure if proper safety mechanisms are not implemented. This operational characteristic sets peristaltic pumps apart, demanding a slightly different approach to system design and control.
Overcoming pumping challenges
In addition to their unique operational design, peristaltic pumps address common pumping challenges faced by other technologies. They are inherently immune to cavitation, a frequent issue in centrifugal pumps, ensuring smooth operation even under fluctuating suction conditions. Their ability to achieve full vacuum allows them to handle demanding suction scenarios without priming systems.
Peristaltic pumps are also capable of dry-run operation, as they are self-priming and do not require external lubrication to operate safely. This reliability is critical for processes with intermittent flow. Additionally, the gentle peristaltic action avoids shearing or breaking transported media, making these pumps ideal for handling high-viscosity slurries or biologically sensitive fluids.
Smart monitoring
Condition monitoring is becoming increasingly important for industries striving to reduce
maintenance costs and improve uptime. Advanced monitoring systems now enable realtime tracking of critical parameters, ensuring that pumps operate within optimal conditions.
The hose, as the core component of a peristaltic pump, dictates overall reliability. By analyzing vibration patterns, early signs of wear can be identified in both hoses and bearings. This allows for proactive replacements, minimizing unexpected downtime. Pressure monitoring further enhances safety, acting as a trigger for shutdowns when limits are exceeded and identifying anomalies like hose fatigue or flow interruptions.
In addition, monitoring VFD values such as power and torque provides valuable insight into process conditions. Changes in these parameters can reveal early signs of flow issues, hose wear, or increased resistance, offering operators a deeper understanding of system dynamics without intrusive inspections.
Unlike generic solutions, modern condition monitoring systems are tailored specifically for
the unique dynamics of peristaltic pumps. Their ability to capture high-frequency events, such as pressure peaks, ensures accurate and reliable performance monitoring, even in the most dynamic industrial environments.
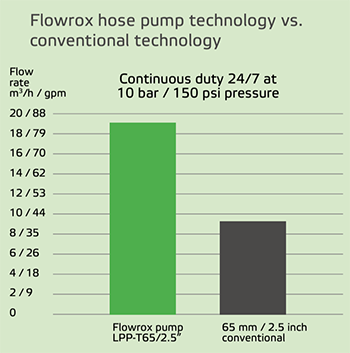
Flowrox hose pumps can handle up to 80% solids, and they do not require seal water at all. By pumping 80% versus 35% solids, there is a 45% reduction in make-up water to be reclaimed and cleaned for future reuse.
The path forward
In today’s industrial landscape, reliability, efficiency, and sustainability are essential for success. With advancements in single roller design and tailored condition monitoring systems, peristaltic pumps offer a robust solution to some of the most demanding pumping challenges. By reducing hose wear, lubricant consumption, and unplanned maintenance, these pumps help industries achieve operational efficiency and cost savings.
Understanding their unique operating principles – such as linear flow control and noncavitating performance – further enhances their value in critical applications. Combined with realtime monitoring capabilities, peristaltic pumps are paving the way for smarter, data-driven maintenance strategies.
In environments where every drop of water and every hour of uptime matter, peristaltic pumps are not just an alternative but a proven solution for industries striving to meet their operational and sustainability goals.
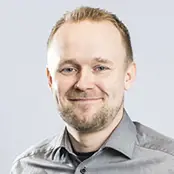
Simo Rounela
Automation Product Manager, Pumps
Certified Profinet Engineer
Valmet Flow Control P&S Flowrox Product Line
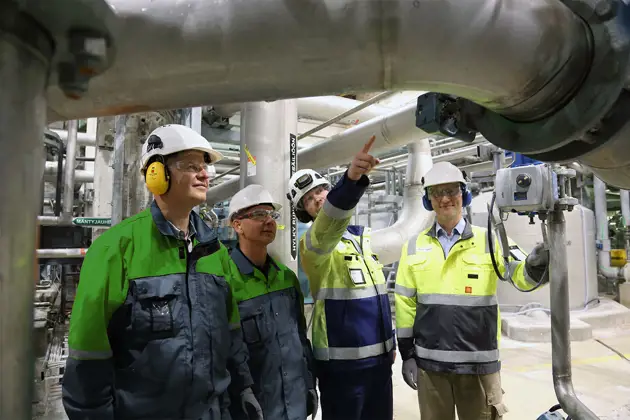
Subscribe to our newsletter
Subscribe now to flow control newsletter and receive the latest insights directly to your email.
Subscribe