Klabin stabilizes its pulp mill production
Apr 21, 2020
The Valmet PlantTriage software helped stabilize the operation and achieve chemical savings.
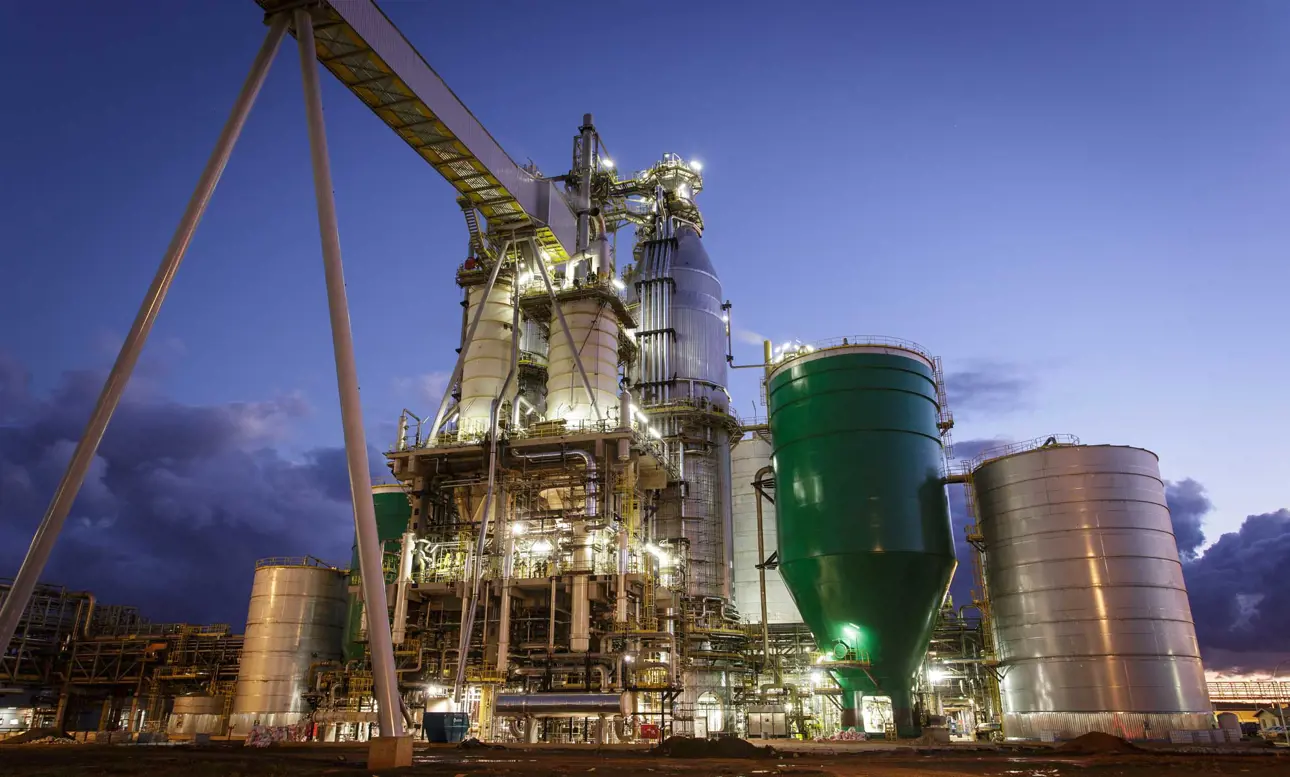
Klabin’s Ortigueira mill is a large, complex industrial plant. It is the only factory in Brazil that simultaneously produces short-fiber pulp (eucalyptus), long-fiber pulp (pine) and fluff pulp (the basis for diapers and absorbents). Known as the Puma plant, it is located in Paraná, Ortigueira, and has been operating since 2016, with a capacity of 1.5 million tons/year. Puma is one of the 18 mills of the Brazilian multinational company, Klabin.
About the project:
- The PUMA project has achieved a simultaneous output of 1.1 million tonnes/year of bleached hardwood pulp and 400 thousand tonnes/year of bleached softwood and fluff pulp.
- The facility was designed to produce 270 MW of electricity, consuming 120 MW internally and exporting up to 150 MW to the Brazilian national grid, using 100% renewable fuels based on wood, tree bark and lignin. Klabin is self-sufficient in power generation.
Another way to measure the plant’s complexity is through its automation. This plant has 38 distributed control systems (DCS), with 15,000 physical access points (I/O) and about 2,900 devices interconnected into a Profibus network. The current phase of the factory has 2,000 automatic valves and 2,700 instruments for measuring temperature, pressure, flow and level. This great army of devices has a huge task to do and needs to work together for a simple reason: the operation must be as stable as possible. And to make stability possible, Klabin uses tools for the online monitoring of its control loops.
Average Absolute Error reduced from 30% to 1.5% in just over two years
“The tuning of control loops is essential for stabilizing the plant and reducing control errors. On the factory start-up, we had room for adjustments and that is what we did. In less than a year, we reduced the Average Absolute Error from the variable average of 25-30% to a level of 15%. Two years after starting, we reached the current average of 1.5%,” summarizes Pablo Cadaval Santos, Industrial manager of the Puma unit in Klabin. One of the examples mentioned by him is the fiber line, which operates today with a minor rate of errors. Figure 1 shows the dramatic improvement that comes from these levels of variability reduction.
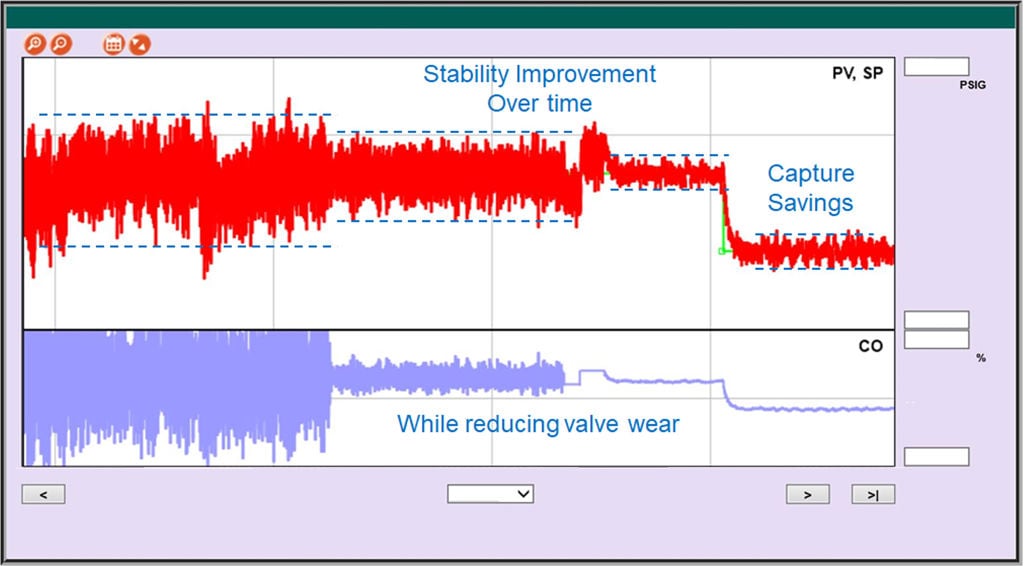
Translated into the factory’s day-to-day reality, the lower control error rates mean a plant with a stable industrial process: variability is low, therefore high quality standards are maintained. In addition, variable costs remain controlled throughout the year. If the process parameters vary within the specified control error limit, the production can be stabilized with little consumption of chemical additives. What’s more, fine-tuned control loops create a track record of who operates and who maintains the factory.
The added stability directly impacted the operator’s workload as well by drastically reducing the alarm rate, allowing the operator to focus more on process optimization.
Application roadmap and technical visit defined Klabin’s choice
Santos reinforces that the platform operates on autopilot, monitoring the performance of the approximately 600 control loops of the plant according to the KPIs established by Klabin. The current process, which has been refined over the course of more than two years, was the result of the partnership between the pulp manufacturer and Valmet. The relationship history already included the use of valves in other units, but in the case of Valmet PlantTriage, the team expanded to include technical visits in another customer’s plant that already uses the platform in Brazil. “The technical assistance in Brazil and a defined roadmap for the tool also count, along with the global market share,” he summarizes.
Cristian Moraes, Performance Solutions Manager at Valmet, highlights the sharing of experiences as the key to the success of Valmet PlantTriage at the Puma plant. He points out that massive data analysis allows it to be a predictive tool with real-time corrections. It was the case of the adjustment of the weight of cellulose bales, which must be standardized in their weight as a final product. “The lack of tuning between the moisture and the steam control loops was a challenge, and adjustments were being made manually. With Valmet PlantTriage, the plant definitely solved the problem. Now every bale is consistently produced,” he says.
Customized globe valve reflects partnership in the Ortigueira plant
The same alignment that occurred for the adoption of Valmet PlantTriage was also involved in the delivery of a globe valve for the Ortigueira unit’s boiler. The equipment replaced the original device that had been installed, but was preceded by an engineering study that simulated the operating conditions of the valve with actual data and customization of the equipment.
Because it is crucial equipment for the operation, the new valve also has an intelligent positioner that performs the remote diagnosis and anticipates valve failures. The customization made by the valve experts included the alloys for the construction of the valve body and the most suitable specification of the internal materials.
“The development was not limited to the standard technical specifications; it considered the variations of pressure, flow and the high mechanical stress that the piece undergoes in the field,” explains Santos. The solution presented by the experts was considered the one with the best technical and economic results and scored highly for engineering that met the demanding specifications. “It is equipment that operates under severe conditions, subject to high pressure, in some cases up to 100 bar; it gave stability to the operation and does not present premature degradation due to the correct application,” he adds.
The prompt and specific supplies in the first phase of the Puma I plant in Ortigueira also involved the application of Neles™ ND9000 positioners for a total of 120 valves, and the supply of 12-inch Neles™ ball valves at the outlet of the mass tanks. These valves replaced the knife gate-type devices originally provided in the project.
With the expansion of the plant, the Puma II project, Valmet's flow control business line's participation has grown considerably as the company has become the leading supplier of valves and positioners for the new paper mill, with a total of 1800 valves, all equipped with smart control valve positioners (also called valve controllers), Neles™ ND9000 or on-off valve monitors. The Puma II project will also have the application of the PlantTriage platform for control loops monitoring and tuning.
Sami Nousiainen, VP Valves Services at Valmet's flow control, says, “We are committed to partnering with our clients to improve reliability. We are helping our customers to achieve big improvements by combining our expertise with their application knowledge in a practical way. This applies across the entire lifecycle: from equipment design, to installation, operation, monitoring, lifecycle planning and maintenance.”
The text has been updated in April 2022 & July 2023, due to the company & product name changes.
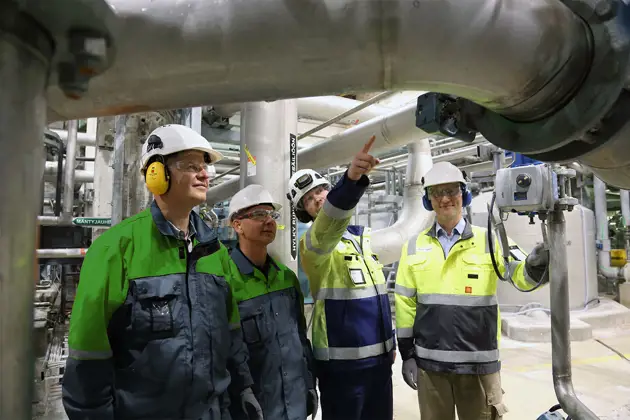
Subscribe to our newsletter
Subscribe now to flow control newsletter and receive the latest insights directly to your email.
SubscribeRead more pulp and paper stories