Keeping pace with growth in renewable fuels
The renewable share of the total energy use is predicted to rise up to 15% by 2040. Automation in renewable fuel production should be prepared to answer the needs of a growing industry, since the fact that the production processes require safe, reliable and accurate control valves is unquestioned.
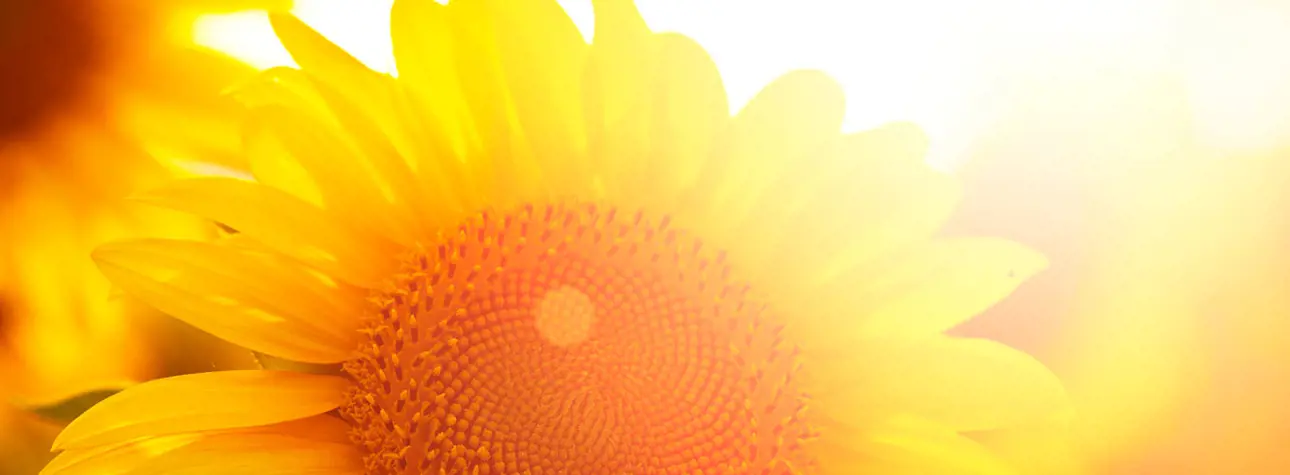
Renewable fuel production growth has been fast during the last decade. The energy markets are going through changes for various reasons. The discoveries and exploitation of shale gas, especially in the US, brings cheap gas into the market, which may displace investments to renewable fuel production. Still, the main drivers for renewable growth are climate change and the need to reduce the use and dependency on non-renewable raw materials, namely crude oil, natural gas and other associated hydrocarbons. How well the industry is prepared for these market changes and what the role of automation in renewable fuel production is may be questioned. The expectations are high; automation companies are expected to develop solutions and services that give renewable fuel producers business value over the life of their investments by improving productivity, energy and materials efficiency, optimising costs and enabling more effective risk control.
“The selection of best-in-class technologies can make an important contribution to valve performance while maintaining or even improving life-cycle costs for the investment.” Sari Aronen, Application Manager
Is there still a market for biofuels?
The International Energy Outlook 2013 projects that world energy consumption will grow by 56% between 2010 and 2040. The report does not incorporate prospective legislation or policies that might affect energy markets. Renewable energy and nuclear power are the world’s fastest growing energy sources, each increasing by 2.5% /y. Fossil fuels continue to supply almost 80% of world energy use through 2040. Natural gas is the fastest growing fossil fuel in the outlook and global natural gas consumption increases by 1.7% /y. Increasing supplies of tight gas, shale gas, and coalbed methane support growth in projected worldwide natural gas use. Coal use will grow faster than petroleum and other liquid fuel use until after 2030, mainly because of increases in China’s consumption of coal and tepid growth in liquids demand, attributed to slow growth in the OECD regions and high sustained oil prices. The renewable share of total energy use will rise from 11% in 2010 to 15% in 2040.
Highlights
· World energy consumption will grow by 56% between 2010 and 2040.
· The two main renewable products on the biofuel market are bioethanol and biodiesel.
· Modern biodiesel production tends to be more challenging for control valves than bioethanol production.
· The renewable share of total energy use will rise to 15% by 2040.
Ethanol’s challenges
Ethanol as an alternative fuel has some strong attributes, but it has its challenges as well. Commodity prices for corn are the most volatile piece of the puzzle. The increasing price for a bushel of corn is no different to the increasing price of a bbl of oil. Close to 50% of the total cost of goods sold needed to produce ethanol is directly tied to the price of corn. Transportation costs and logistics impact a producer’s ability to ship its product to an oil company’s blending facility. Currently, ethanol can only be transported by rail tank cars or tank truck. A method of transporting ethanol via a pipeline that does not contaminate the ethanol with moisture is yet to be developed. The cost of corn and other materials and the need for a relatively quick return on investment are driving the viability of future projects in question. Bioethanol production is based on a fermentation process using corn or sugar cane as the raw material. The basic conversion process consists of four main phases: mash preparation, fermentation, distillation and water removal. Prepared mash is transferred into fermenters, where the conversion of sugar to ethanol begins. The resulting liquid is then distilled, and water is removed with molecular sieving to form the finished end product. A major effort is underway to reduce the use of corn as the main feedstock in producing ethanol, due to its volatile price nature, which is similar to oil. Several companies are developing process technologies that will use agricultural waste, such as trees, grass, and municipal waste (biomass), as the main feedstock in ethanol production. Any material that contains cellulose can be broken down into a starch, which is then converted into a sugar and distilled. One of the other benefits to cellulosic ethanol technology is that greenhouse gas reduction is far greater with cellulosic ethanol than with corn ethanol.
Biodiesel: a clean alternative
Biodiesel, as was the case with ethanol, was developed at the grassroots farm level to reduce a farmer’s dependence on, and operating costs associated with, the price of diesel fuel needed to operate equipment. Since then, it has made inroads into automobile and other transportation fuels and can potentially be an alternative to home heating oil. The advantage that biodiesel has over traditional diesel fuel is that it burns cleaner and actually improves engine life. From an environmental standpoint, biodiesel has attractive qualities. It produces lower particulate matter emissions, eliminates acid rain, produces lower hydrocarbon exhaust emissions by 95% and reduces exhaust emissions of aromatic compounds by 75% to 90%. One of the biggest challenges with using biodiesel fuel is its lowered performance in cold weather environments. At lower ambient temperatures, it has a tendency to congeal. Its clouding or jelling point is approximately -16 °C higher than traditional diesel fuel. Biodiesel is traditionally produced by the transesterification of vegetable oils. More versatile, next generation biodiesel processes, such as Neste Oil’s NExBTL and syngas to liquid conversion by Fischer-Tropsch synthesis, have also recently appeared on the market and are gaining in both popularity and commercial viability. In contrast to bioethanol, biodiesel is used in engines without the need for any changes in the engine itself, and the next generation biodiesels are of excellent quality and can also be used at low temperatures.
Valves for renewable fuel production
The majority of valve applications in renewable fuel production involve low or moderate pressures and low temperatures. Modern biodiesel production tends to be more challenging for control valves than bioethanol production, due to the high pressures and temperatures that may be needed in the biodiesel conversion and product upgrade phases. However, both processes require safe, reliable and accurate control valves. There are many services in these plants where the selection of best in class technologies can make an important contribution to valve performance while maintaining or even improving lifecycle costs for the investment.
Soft and metal seated technology can be used for common control valve applications in renewable fuels. In dirty service, where flow media may contain impurities ranging from dust to dirt and debris, metal seated control valves are the more rugged and durable valve option. In applications where either clogging or erosion is known to be a risk, metal seated rotary valves have proven their reliability. In extreme cases, dustproof seats may be used to prevent flow media build up behind the seat area.
Flashing
When the downstream pressure of a control valve is less than the liquid vapour pressure, part of the liquid is vaporised and remains as vapour downstream from the valve. The flow downstream is partly liquid and partly vapour. This phenomenon is called flashing. It cannot be avoided with the valve design, but it has to be considered when selecting the valve type. Flashing flow may cause mechanical damage, such as erosion and vibration, if the velocity is too high. An eccentric plug valve has proven to be a reliable solution for flashing services, because it allows the trim to be positioned in the so called 'flow to close' direction that prevents the flow stream from hitting the valve body and downstream pipe wall.
Noise and cavitation
Noise and cavitation may pose a challenge for valves in which there is a high pressure differential. Cavitation is a two stage phenomenon that appears in the liquid flow through the control valve under certain conditions, where the liquid pressure decreases below vapour pressure and after the vapour bubbles collapse rapidly, creating pressure shocks when the pressure recovers to a level above the vapour pressure. Noise is generated mainly by turbulence and shock waves produced in chocked flow conditions. Such valves may be equipped with multi stage noise reduction and anti cavitation trims to reduce excessive noise and cavitation. Versatile Q-trim technology has been developed to widen rotary applications for noise and cavitation prone services.
Molecular sieving
One special application in bioethanol production is molecular sieving, where dryers packed with molecular sieve material in several columns are used to remove the water in the biomass. There is a continuous switching between the columns, where the processing of wet streams during adsorption and regeneration is made possible by sequentially switching the valves between the columns. The valves must be able to maintain their bidirectional tightness during frequent cycling and temperature fluctuations. An additional challenge could be caused by particulates as molecular sieve dust coming from column beds. Metal seated butterfly or ball valves, and special soft seated butterfly valves, have been shown to provide good performance in such demanding conditions.
Online diagnostics
Online valve diagnostics make it possible to monitor valve performance while the process is running, indicate decreasing valve performance and warn the user before a failure becomes so bad as to cause excessive process variability or even an unexpected shutdown. The most efficient way to carry out predictive maintenance and online diagnostics is to utilise valve controllers that are capable of storing results in their memory or sending warnings and alarms based on stored performance limits. Today, online valve diagnostics can be used for all kinds of applications, from control to on/off and safety valves. Combining the utilisation of inherently reliable valves with intelligent devices can raise application reliability to a significantly higher level than before.
Transportation
An important and sometimes overlooked category of valves associated with renewable processing, regulates the loading and unloading of product into railcars and other forms of product transportation. Safety is a vital consideration for transportation valves, meaning tight shutoff and emission control from valve nstems are key issues. Another important consideration for renewable fuel transportation is the coefficient of flow (Cv), which determines how quickly a product can be loaded on and off of carriers, primarily railroad tank cars. A full port valve, such as Neles™ Jamesbury valve, is able to replace the existing standard port valve with no adapting hardware required. The substantially high capacity allows tank cars to load and unload considerably faster, so that the cars can make several more runs during the course of a year.
Conclusion
According to the international energy outlook 2013 of the US Energy Information Association, the renewable share of total energy use will rise to 15% by 2040. Bioethanol production is already considerable in the US and Brazil. Ethanol production is facing challenges to reduce transportation and feedstock costs and increase the rate of return on investments. Next generation biodiesels are getting more popular and commercially viable due to their versatility and excellent quality, also at low temperatures, without any need for changes in the car engine itself.
Modern biodiesel production tends to be more challenging for control valves than bioethanol production, due to the high pressures and temperatures that may be needed in the biodiesel conversion and product upgrade phases. Both processes require safe, reliable and accurate control valves. Versatile Q-trim technology has been developed to widen rotary applications for noise and cavitation prone services. Rotary valves provide a simple and maintenance free way to control fugitive emissions from valves. Metal seated valves and special soft seated butterfly valves have been shown to provide good performance in demanding conditions, such as continuous switching molecular sieve applications. Combining the utilisation of inherently reliable valves with intelligent devices can raise application reliability to a significantly higher level. The substantially high capacity of rotary valves allows tank cars to load and unload considerably faster, helping ethanol producers to cut transportation costs.
Text by Sari Aronen
Published in Hydrocarbon Engineering January 2014 as 'Fully qualified'
Text originally published in 2014, and slightly updated in April 2022, due to the company name change to Valmet.
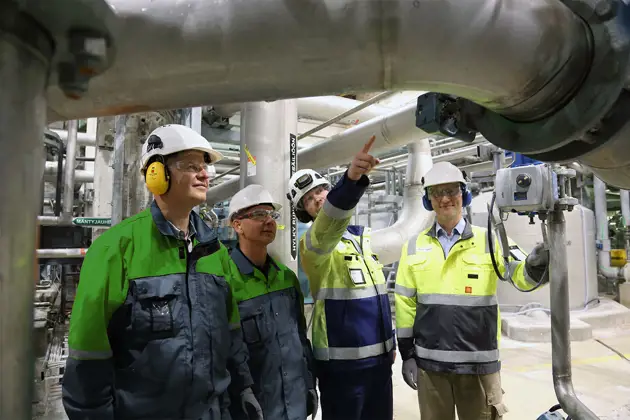
Subscribe to our newsletter
Subscribe now to flow control newsletter and receive the latest insights directly to your email.
Subscribe