Improving process safety and cutting costs with process ball valves
Jun 30, 2014
Ball valves are used in various process industry applications. The most typical solutions are in on-off and ESD applications, but high-performance ball valves are also widely used in control applications. In this article, the author explains by means of a hydrocracker example how challenging correct valve sizing and valve selection in control applications can be.
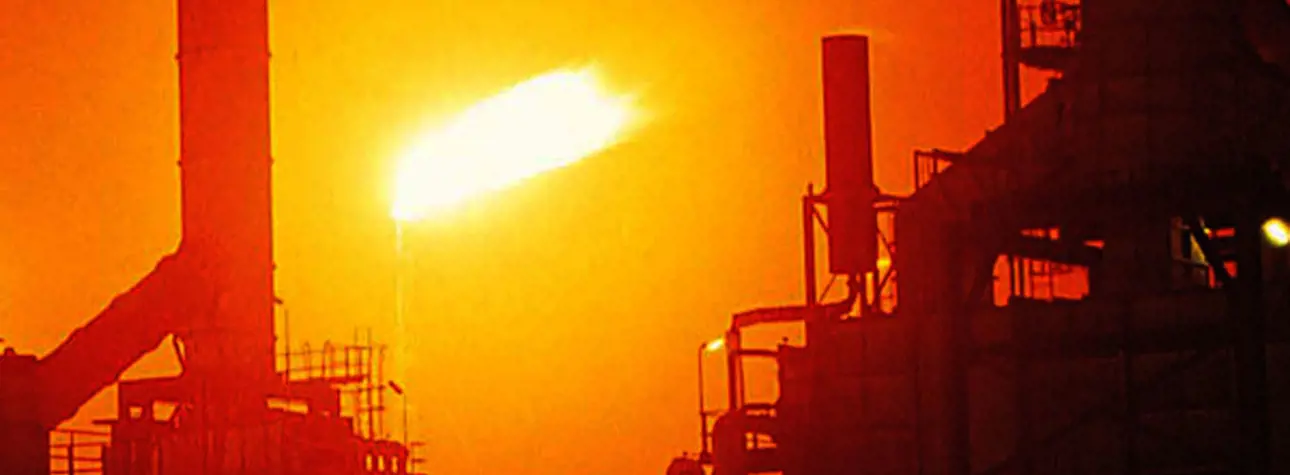
- In this article you will learn how a hydrocracking application has been able to gain greater advantages by using high performance process ball valves.
- The best solution can be achieved when all parts of the valve are selected according to the process conditions.
- High performance ball valves combine all safety aspects: good fugitive emission performance, worker safety, noise control and functional safety in case of an emergency.
- Proper valve design that fulfills all design standards is key to successful plant operations with minimized maintenance costs.
What makes a process ball valve?
There are multiple ball valve design standards. The ASME B 16.34 process valve design standard sets the basis for the design, yet it does not guarantee that the valve is designed for demanding process industry applications. Design requirements can be further raised with the use of additional standards. One of these standards is API 608, which contains extra design requirements as an extension of ASME B 16.34.
Although design standards set the basis for valve performance, there are still multiple points that must be considered when designing a process industry valve. All components must be developed with the capability of performing in demanding process environments. The most critical parts of a process ball valve are the bearing construction, seat construction and valve trim. The performance of a valve is only as good as its weakest link. By combining an advanced process ball valve design with various safety and plant performance expectations, the advantages of using true process valves are easy to recognize.
Operational costs can account for a major portion of the total valve cost. Using properly designed valves with the correct material selection can extend availability and reliability. Using valves with good fugitive emission performance can increase plant runtime and safety. Worker safety, too, can be increased by using a noise control solution. In addition, noise control can extend the valve lifetime by reducing the effects of cavitation and vibration. In case of emergency, fi re-safe and tested valves according to API 607, which also fulfill functional safety requirements, can be critical components in helping the plant to go to safe state.
The advantages of process ball valves can be easily shown through an example of a hydrocracking application.
Example application – hydrocracker
Typical hydrocracking feedstocks include heavy atmospheric and vacuum gas oils, and catalytically or thermally cracked gas oils. These products are converted to lower molecular weight products, primarily naphtha or distillates. Sulphur, nitrogen and oxygen removal and olefi n saturation occur simultaneously with the hydrocracking reaction. Typical reactor operating conditions require temperatures of 280 – 475°C and reactor circuit pressures of 35 – 215 bar, depending on the feedstock and fi nal products desired. The reactions consume hydrogen and are highly exothermic. The key to hydrotreating and hydrocracking reactions is applying bi-functional catalysts that contain an acid function and a metal function. A hydrocracker sets demanding requirements on valves through plant runtime, emissions, fi re-safe and functional safety. These are directly related to valve design and testing.
Cost control with high-performance design
Valve sizing in on-off cases is quite simple, but valve selection requires expertise. The best solution can be achieved when all parts of the valve are selected according to the process conditions. In high performance ball on-off and ESD valves, the critical areas are the material selection and actuator sizing. When selecting a control valve, the correct valve sizing is the most important aspect.
A high-performance ball valve that is designed to have a long cycle life will offer operational and service cost savings when compared with poor-performance designs. If all parts of the valve are designed to have a high cycle life, the total number of service and failures are low compared with a design that is meant to last only a few cycles.
In a hydrocracker
Poorly performing valves in the process must be serviced because they will have a direct impact on the efficiency of the process. The cost of unscheduled maintenance will be quite high, up to 70% of the cost of a new valve in some applications. When adding this to the cost of removing the valve from the line and disrupting the process, the total cost will be much higher. Typical hydrocracking plant runtime is 2 to 4 years, which requires reliable equipment and process control, before the catalyst will need regeneration of its deposits.
All aspects of safety combined with high-performance process ball valves
Rotary stem type valves are considered to be less sensitive to packing wear and have greater performance compared with rising stem valves. In demanding control, on-off and ESD service applications, the fugitive emission performance can become a critical factor for achieving longer plant runtime.
Valves with low fugitive emission levels benefit end users in many ways. First, valves with very low fugitive emissions help end users fulfill current environmental rules and regulations, which must be adhered to if the plant is to continue its operations and avoid heavy fines. These can be far more costly than FE-certified valves. Secondly, the minimization of fugitive emissions can also help avoid other costs that occur when product is lost via leaking valves. Lost flow medium results in both lost raw material and lower end product yields. The more complex and processed the flow media is the higher price it has per mass unit. The loss of flow medium also means lost energy, as the pumps or compressors must do extra work to compensate for the leakage. Plus, minimizing fugitive emissions can save a considerable amount of money. FE-certified valves improve safety. A leaking packing can represent an enormous safety issue in a process plant. For example, a hydrogen leak can auto-ignite and cause flames that are nearly impossible to detect. Such flames will burn surroundings and compromise safety. Health issues, too, can be minimized by reducing fugitive emissions. A healthier environment protects people and makes them more productive. For example, reducing H2S content in the air allows employees to work for longer time periods. By asking valve suppliers to require FE testing according to the most comprehensive standard available (currently ISO15848-1), end users can introduce significant health, safety and environmental benefits at their process plants, while simultaneously improving their operating costs.
Hydrogen itself is a perfect example of the importance of emissions control. If the packing is not properly designed for the application, it will lead to emissions. With hydrogen in particular, those leakages can be critical. Emissions testing according to ISO 15848-1 will not only test the valve shaft packing, but also the body joint leakage so that all aspects of emissions can be controlled. With live-loaded packing, the lifetime-to-emissions level can be maintained longer.
Noise control with self-cleaning solution
High noise levels not only constitute a health risk to personnel, but can also cause damage to equipment. In many countries, strict noise abatement laws require the reduction of noise levels to acceptable levels. Health and safety legislation typically restricts the maximum noise level to be less than 85 dB(A). In residential areas in particular, such strict limits cannot be exceeded, and the limits may be even lower. Using source treatment, such as Q-trim technology in high-performance process ball valves, the noise levels can be kept at an acceptable level. Combining a noise control solution with impurities handling capability, an optimal solution can be achieved. A quarter-turn valve with a self flushing capable trim design offers longer plant runtime and reduced maintenance costs. Also, the latest developments offer high noise- reduction solutions.
ESD valve – part of a safety instrumented system
A high-performance process ball valve is the perfect solution for ESD service. The partial stroke test capability, tight shutoff and lowest possible pressure drop in full bore valves offer an easy-to-use ESD solution with online testing capability. By selecting the proper process valve, the design will fulfill the process requirements with functional safety capability and complies to the requirements of the safety instrumented system as a layer of protection. A very good example can also be illustrated in the hydrocracker, where depressurizing noise can be a problem and demanding functional safety requirements are common.
"By asking valve suppliers to require FE testing according to the most comprehensive standard available (currently ISO15848-1), end users can introduce significant health, safety and environmental benefits at their process plants, while simultaneously improving their operating costs." Ville Kähkönen, Neles
Depressurising
When it comes to a reactor’s depressurizing challenge, many refineries are looking for a safety instrumented function for emergency depressurizing of their hydrocracking process unit upon detecting thermal runaway. Many hydrocrackers are equipped with two different means of depressurizing: a slow system and a fast one. In an emergency scenario, an operator will first attempt to bring the process under control using slow depressurizing. The fast depressurizing system is only used if the first option is not capable of stopping the runaway reaction from continuing. The process can be brought back to a safe state by either manual or automatic depressurizing. To minimize the negative impact on the process equipment, slow depressurizing is always used first. Valve performance can be one of the weakest links in the safety system, where the failure mode may become stuck. The only way to test for this condition is to stroke the valve regularly. Still, closing the valve completely is not desirable when the unit is operating. In many refineries, the hydrocracker reactor can be a SIL 3 application. As part of a safety instrumented system, a high-performance process ball valve with fire-safe and tested construction according to API 607 and online valve diagnostics ensure reliable and safe valve operation so that the process can be brought back to a safe condition. Along with the functional safety calculations for the PFD value and SIL level, the most important safety aspect is the basic valve selection. If a valve is incorrectly selected, none of the PFD calculations are valid. A good example of this is an improper seat selection.
The catalyst can damage and jam an incorrectly selected seat. When the seat is not selected correctly and the valve is not suitable to the application, the PFD value and SIL levels are not valid. It is important to select a seat that can resist impurities and take advantage of the functional safety calculation.
Summary
Proper valve design that fulfills all design standards is key to successful plant operations with minimized maintenance costs. Simply fulfilling the standards is not enough, however, as all aspects that affect the application suitability must be checked. The valve itself must be selected so that it is suitable for the process to take advantage of all life cycle and safety targets. All parts of the valve must be designed according to the process requirements, even if this means exceeding the given standards.
Published in June 2014 Valve World Magazine
Text by Ville Kähkönen
Text originally published in 2014, and slightly updated in April 2022, due to the company name change to Valmet.
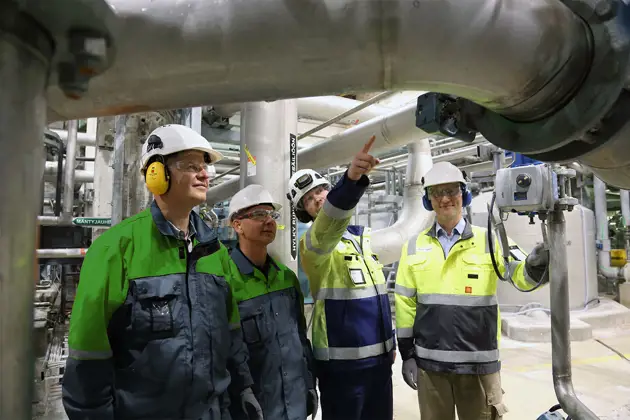
Subscribe to our newsletter
Subscribe now to flow control newsletter and receive the latest insights directly to your email.
SubscribeRead more about ball valves