Flow control solutions for sustainable fuel production
The petroleum industry is looking for economical solutions to meet new regulatory specifications for producing environmentally clean fuels. This has led to an increased demand for high-performance C5 and C6 naphtha isomerization technology because of its ability to reduce the benzene concentration in the gasoline pool while maintaining or increasing the gasoline pool octane number. Isomerization is a process in which the atoms of a molecule remain the same but are rearranged to produce an isomer. Isomerization processes also saturate benzene into cyclohexane by hydrogenation, since benzene concentration in gasoline is legislated due to environmental concerns.
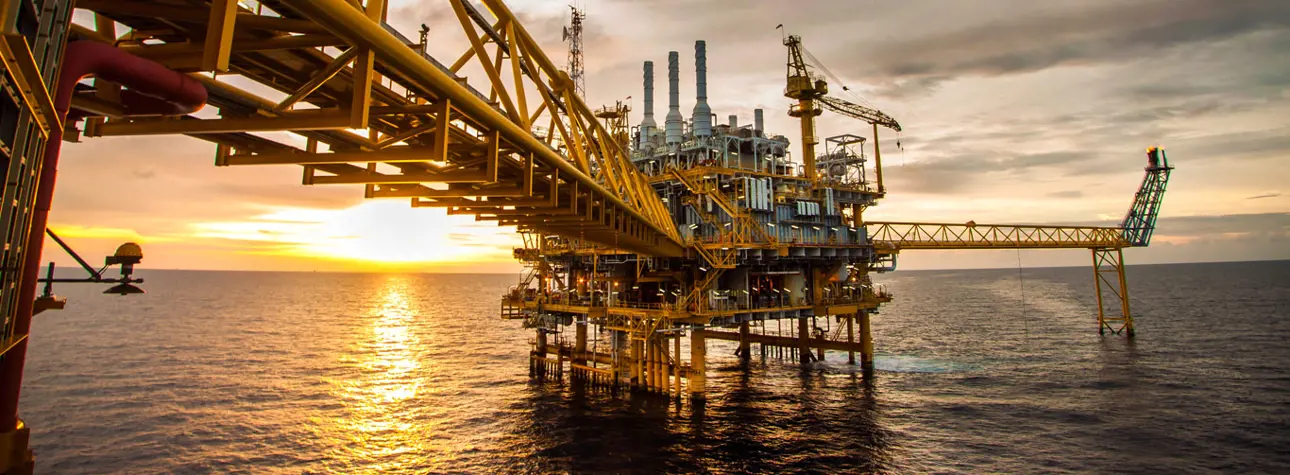
There are several isomerization process configurations available in the market that differ in terms of their operating costs, product revenue, investment costs and the isomerate product octane number. Using a simpler once-through process, research octane numbers (RON) can be improved from 70 to about 80–84. By further utilizing a recycling process for the unconverted hexane, octane numbers can further be improved to around 87–93.
The pentane/hexane and hydrogen feed usually enters the process through dryers, which are used to ensure that the feed is free of oxygen sources that could decrease catalyst activity. If the catalyst type used can tolerate water, dryers may not be necessary. After being mixed with make-up hydrogen, the feed is heat exchanged with the reactor effluent. The feed then enters a charge heater, or heat exchanger, before entering the reactors.
The reactors are kept at a temperature of about 100–200 °C (200–400 °F), as the equilibrium of the isomerization reaction is pushed towards the isomers at lower temperatures. The relatively low temperature slows down the reaction rate, requiring the use of a catalyst to make the reaction proceed at a reasonable rate.
To maintain high catalyst activity, some catalysts require the addition of small amounts of organic chlorides. Hydrogen quenches are used to maintain reactor temperature and catalyst activity. Some cracking also occurs in the reactors, and the light gas formed is removed in the stabilization column. The remaining part exits the stabilizer through the bottom. This stream then enters a deisohexanizer, where the unconverted hexane is separated and recycled.
Figure 1. Typical isomerization process
A typical isomerization process includes about 50 to 60 control valves and about 70 to 80 automated on-off and safety valves. Since pressure and temperature conditions are moderate, the valve pressure classes are normally ASME 300 and sometimes ASME 600. The valve sizes range between 1 and 10 inches. If chlorides are used in the process, Monel internals are typically required for the valves to ensure that the material is resistant to chlorides. Due to the presence of hydrogen and switching flows, bi-directional tightness may be required for some control and on-off valves.
The dryer switching applications represent perhaps the most crucial role for the valves in the isomerization process. This is due to the critical nature of the dryers in the process because they safeguard the reactors from moisture and impurities as well as the operating requirements for the valves that direct the flows between the dryer beds.
Feed and regenerant control valves
Light naphtha feed and make-up hydrogen are both charged in separate dryer vessels. The hydrogen amount is kept just slightly above the amount needed to saturate benzene in the hydrocarbon feed. The hydrogen-to-hydrocarbon ratio is kept at the minimum level required to prevent excessive catalyst coking in the reactors.
The dryers must be regenerated properly and frequently to remove the adsorbed water and other impurities from the molecular sieve beds. Reliable and accurate control is required to keep the hydrogen-to-hydrocarbon ratio at an optimal level. The seat leakage rate required for these control valves is typically class IV or V.
Rising stem valves are typically used for isomerization feed control applications. When combined with a third generation, intelligent controller, the desired control accuracy and reliability can be achieved. The best possible control accuracy is important to keep the feed ratio at the right level. A metal-seated valve with a rugged, one-piece body structure ensures long-lasting tightness and eliminates potential leak paths.
Dryer switching valves
Adsorptive dryers normally include three beds: two in the drying stage and the third one in regeneration with hot gas or in reactivation with cool gas. Switching from bed to bed takes place every two to six hours with a minimum of four to six switching valves required for each bed. The switching valves play an important role in directing the inlet and outlet gas streams into the adsorption bed columns, switching the columns from adsorption phase to regeneration phase or cooling phases in a pre-set sequence. These valves are also called dryer sequencing valves.
The valves must be able to resist hot regeneration gas (200–350 °C/400–660 °F) and temperature swings (25–350 °C/45–630 °F). They should maintain operability despite any particulates, like molecular dust, with an operating pressure up to 50–60 bar (730–870 psi). Tight shut-off is required, typically class V for feed dryer valves and class V or VI for hydrogen dryer valves.
Trunnion and seat-supported rotary ball valves are field-proven and licensor-approved solutions for isomerization and many other process dryer switching applications. The use of a rotating stem with live-loaded emission-proof packing ensures that the required, certified emission levels are met without the need for packing lubrication.
With trunnion design valves, the bearings above and below the ball and rotating concentric shaft make the bearing function simple and easily avoid excessive wear. Rotary ball valves resist particle build-up as the seat and ball are in continuous contact, effectively wiping the seat surface with every cycle. Durable two-way tightness is standard and with hard coatings a long-lasting tightness in demanding applications with variable temperature and other process conditions is ensured.
Rugged, pneumatic cylinder actuators provide a compact and easy way to install the rotary valve in any mounting position without any additional support needed, providing savings with piping and installation costs. The valves can be equipped with intelligent controllers, such as Neles SwitchGuard™, to give the possibility to set the on-off valve closing and opening stroke times and profiles according to the process needs with high pneumatics capacity. No additional accessories are needed, and online condition monitoring can be used with the diagnostic information saved to the device itself.
Hydrogen quench control
Hydrogen quenches are used to control the reactor temperature and to protect the catalyst beds from possible coke build-up. While the isomerization reactions are only mildly exothermic, benzene saturation releases significant heat that must be controlled to ensure a favorable equilibrium. Increased temperatures also promote catalyst deactivation. As the composition of the feed may vary, valve rangeability is required to adjust for the changing amount of heat released. Active catalysts are sensitive to temperature changes, making quick response a necessity for the valves.
Rising stem globe valves equipped with an intelligent valve controller ensure efficient and reliable reactor quenching. Keeping the variability under control reduces hydrogen consumption and makes certain that the required amount of hydrogen is available, especially with modern, efficient catalysts that require fast control response to stabilize the process conditions.
Reactor inlet shut-off
An emergency shutdown (ESD) valve is needed to isolate and protect the reactors and the catalyst in case of a process upset. These safety valves are normally open and are closed only in case of an upset. These valves are expected to be available and function reliably throughout the process runs when needed, even after longer periods of non-operation.
Rotary ball valves with an intelligent safety solenoid, such as Neles ValvGuard™, ensure that the valve will be operational when needed. A robust design is typically required for a long lifetime throughout the process run cycle. An anti-blowout valve shaft is particularly important for the safety of personnel and equipment in case of unexpected piping pressure, when the valve is pulled down for maintenance.
A high torque piston actuator, designed to overcome static friction, is an important feature for safety valves that are not operated frequently. Online partial stroke testing provides a way to ensure that the valve will be available when it is needed. Compliance up to SIL 3 by third-party certifications and HART or Foundation fieldbus communication compatibility is highly recommended. The advanced diagnostics capability of the intelligent safety solenoid helps the plant further comply with the demanding safety targets.
Column heat and product control
The reactor effluent is cooled before entering the product fractionation column. The column overhead vapors are caustic scrubbed to remove any hydrogen chloride (HCl) that has formed in the reactor. The hydrocarbon mixture is separated into the components according to the boiling points by fractionation in the column.
The reboilers control the heat input in the column and thereby also the efficiency of gas stripping from the isomerate. Reflux control is a balance between the gasoline separation and reboiler energy consumption. The lower the reflux rate, the more gasoline is lost with the gases, but less heat is required in reboiler. Reliable and accurate control performance is required from the valves to ensure efficient gas-liquid separation and isomerate product purity.
Summary and conclusions
Isomerization is a process that provides a solution for the petroleum industry to meet new regulatory specifications for producing environmentally clean and efficient fuels. It is important that the process is stable, flexible and constantly under control. Efficient and reliable valves help ensure that process productivity remains at the desired level and the process itself meets the strict environmental and safety requirements.
All dryers and switching valves involved play a particularly important role in the availability of the isomerization process as well as successful production. Intelligent valve controllers with online diagnostic capabilities provide the means for simple and reliable instrumentation with the transparency to control the performance of the on-off and safety valves while the process is running.
Text originally published in 2017, and slightly updated in April 2022, due to the company name change to Valmet.
TEXT: Sari Aronen
Published with permission of Valve World magazine, March 2017.
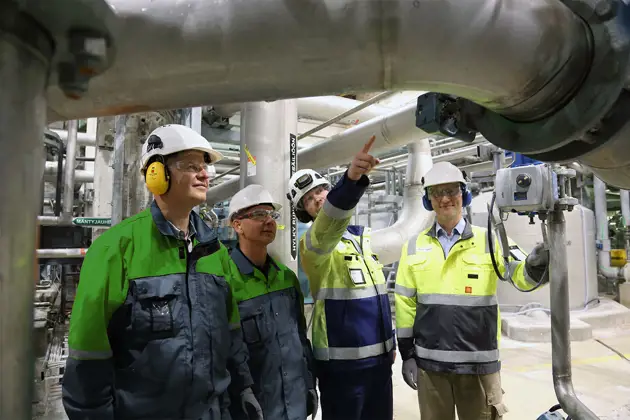
Subscribe to our newsletter
Subscribe now to flow control newsletter and receive the latest insights directly to your email.
SubscribeRead more about the topic