Flashing and cavitation - Ask the flow control expert
Q: What are flashing and cavitation? Which valve type is most suitable for such conditions?
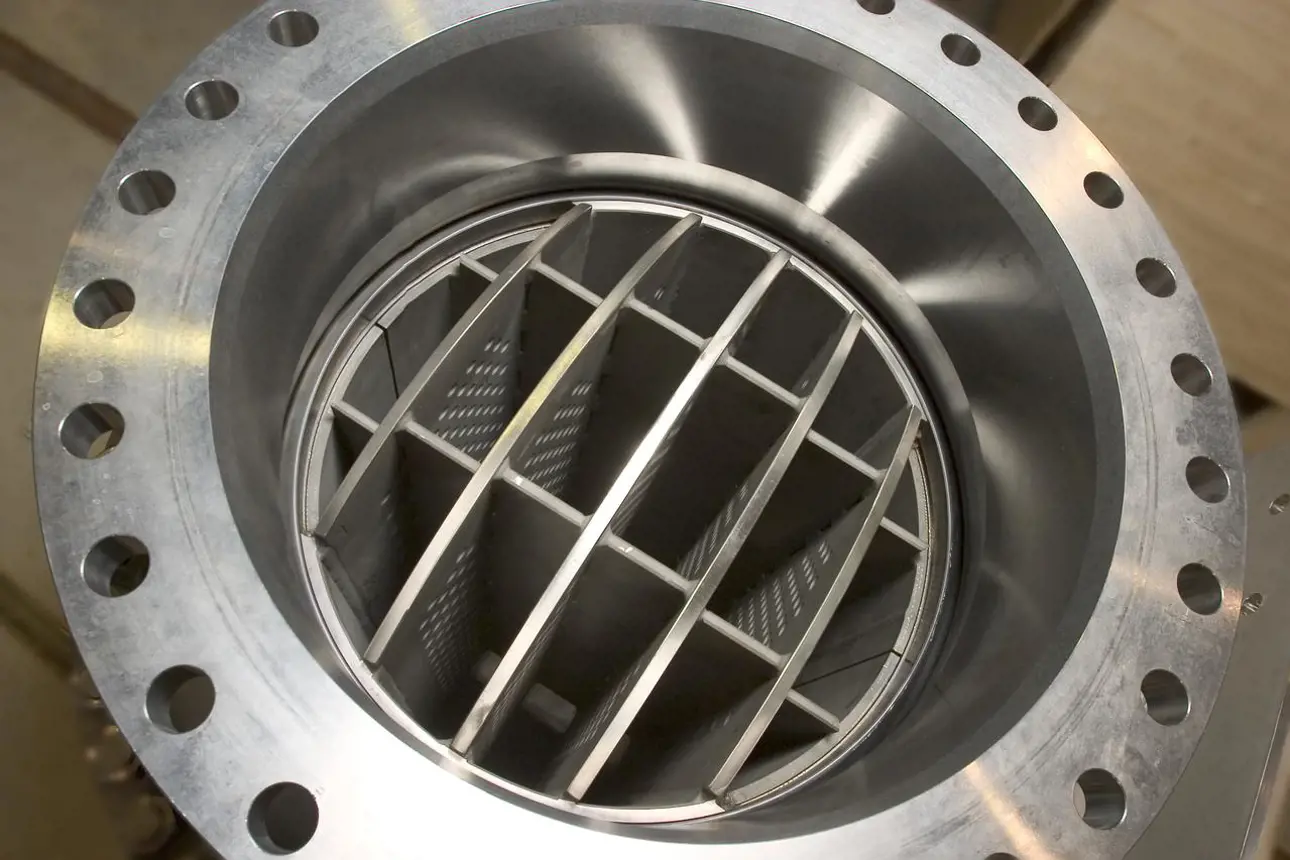
A: Cavitation and flashing are two-phase phenomena appearing in liquid flow through the control valve under certain conditions. The first stage of cavitation and flashing is similar; the liquid pressure decreases below vapor pressure creating vapor bubbles. This is identical the to well-known boiling phenomena. However, in control valves, boiling is accomplished by a pressure drop in the throttling process, not a temperature rise.
The second phases of flashing and cavitation differ from one another
The second stages of cavitation and flashing are different from one another. In cavitation, vapor bubbles collapse rapidly creating pressure shocks as pressure recovers above the vapor pressure. Pressure shocks may, at worst, cause mechanical damage to the valve. In flashing conditions, the pressure does not recover above vapor pressure, because the downstream pressure is below vapor pressure. Vapor bubbles do not collapse, therefore fluid on the valve outlet side is partly vapor and partly liquid.
Predicting cavitation damage depends on many factors
Predicting cavitation damage is complicated because it depends on many factors, e.g., pressure drop, flow medium, valve type and materials. The onset of cavitation is called incipient or partial cavitation, which should not be confused with incipient damage. Incipient cavitation can be used to predict cavitation noise but not to predict damage. Valmet’s cavitation criteria are based on noise limits and terminal pressure drop representing the pressure drop for choked flow. However, there are applications, typically low dp and small valve size, where even choked flow is not dangerous. Valmet’s Q-Trim technology has been applied to all rotary control valves to prevent cavitation and reduce noise. Q-Trim enhances rotary valve performance and is suitable for severe service.
Flashing can cause problems similar to erosion
Flashing flow may cause problems identical to erosion due to high outlet velocity. Unlike cavitation, flashing cannot be prevented by valve selection, because it results purely from process conditions. Hence Q valves are not normally utilized in flashing services. Standard Finetrol in the flow-to-close direction gives an economical solution instead of using line-size globe valves. Finetrol has been successfully utilized for flashing applications; case-hardened trim and seat ensure that the valve can handle even heavy flashing conditions. The streamlined plug and seat guide the flow in the middle of the pipe and an expander after the valve ensures enough space for two-phase flow.
Expert: Vesa Lempinen. Director, Control Valves Product Center.
Flow control expert
What would you like to learn?
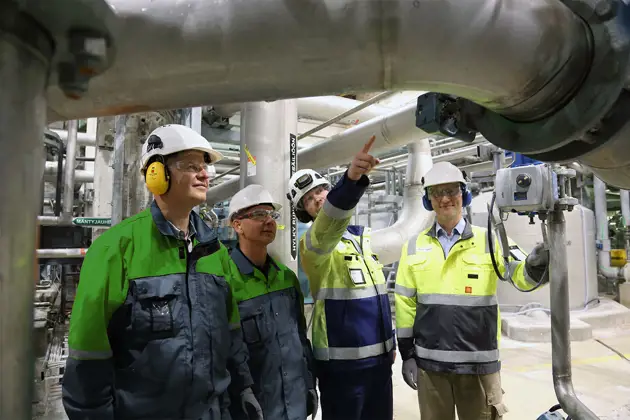
Subscribe to our newsletter
Subscribe now to flow control newsletter and receive the latest insights directly to your email.
SubscribeMore from the flow control expert