Finding the source of all that noise
Effective aerodynamic noise reduction in pipelines and control loops has become an important consideration for many industries as it directly affects a plant’s efficiency and productivity. Knowing the proper ways of controlling such noise can help in creating a safe working environment, protecting the plant, enabling stable process control, extending maintenance intervals and ensuring that legal requirements for noise are met.
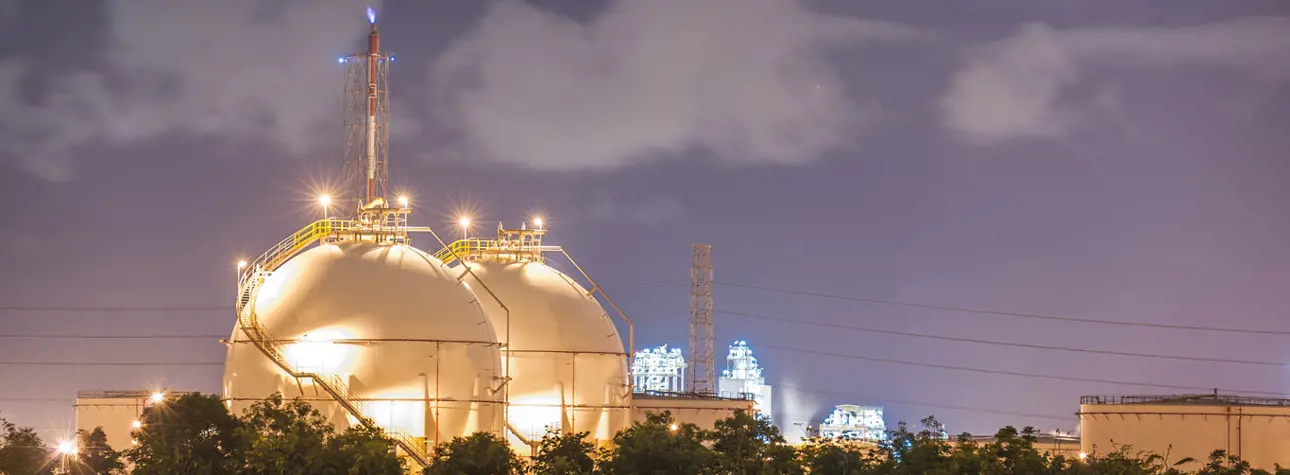
Customer challenge: Aerodynamic noise is not only annoying, it also presents a health threat and creates vibration that can damage the control valves, degrading their performance and shortening maintenance intervals.
Our solution: The most cost-effective approach is to limit the level of noise through meticulous valve sizing and piping configuration design.
Key customer benefits: By eliminating the reason for noise generation, customers get greater control reliability and process uptime, ensuring a safe working environment and achieving compliance with legal obligations.
Processing plants today do everything they can to increase efficiency and productivity. Frequently, that involves operating at higher temperatures, pressures and flow rates, which means higher pressure differentials across critical control valves as well other conditions that generate more noise.
While this noise has always been a problem, it is even more so in today’s high-throughput processing plants. When this cacophony is generated by air and other gases flowing through valves and piping systems, it is called “aerodynamic noise.” Aerodynamic noise is not only annoying, it also presents a health threat that may be subject to a variety of regulations. Most of those regulations limit maximum allowable noise levels to less than 85 decibels (dBA).
Even beyond the health and annoyance factors, aerodynamic noise causes problems. Such noise can generate substantial shock and vibration that can damage or alter the performance of control valves and instrumentation, degrading their performance and shortening maintenance intervals. This damage starts to occur at sound pressure levels in excess of 100 dBA.
Damage from acoustic shock and vibration can be minimized through the use of robustly designed valves, piping and instrumentation. But even these robust configurations should not be subjected to noise levels predicted to exceed 110 dBA.
In short, aerodynamic noise is a significant problem on many levels that need to be addressed. This can be accomplished by limiting the factors that generate the noise (called a source treatment), dampening the noise that has already been generated or a combination of those two solutions. The most cost-effective approach is to limit the level of noise through meticulous valve sizing and piping configuration design. However, that’s not always going to happen—valves are sometimes improperly sized, and unanticipated conditions arise that can result in surprising levels of noise. When the horse is already out of the barn and making a racket, it may be expedient to use path abatement procedures, rather than trying to redesign the system and replace most of the noise-generating components. If a great deal of noise is generated, however, the best approach might be to determine the most cost-effective combination of source abatement and path dampening. To do this requires finding a way to analyze control loops to accurately determine how much noise will be produced or abated by various source and path treatment options.
“Processing plants today do everything they can to increase efficiency and productivity. Frequently, that involves operating at higher temperatures, pressures and flow rates, which means higher pressure differentials across critical control valves as well other conditions that generate more noise.” Steven Hocurscak, Business Manager and Kyle Rayhill, Global Business Manager
Science of predicting noise level
Because source reduction is the best way to avoid excessive noise, this article will consider that subject shortly. But first, the issue of how to know if a noise problem will occur in a system must be addressed. The place to start is experience: Professional plant operations personnel know that certain control valve and piping configurations are inherently noisy. Valves in these services need to be sized very carefully with noise attenuation in mind. Beyond experience, however, is developing an understanding of conditions most likely to generate noise. At low-pressure ratios, for example, the cause of aerodynamic noise is turbulence. At high-pressure ratios, the turbulent interactions of the shock waves become the major source of noise. A very potent determinant of noise is flow velocity because dBA levels increase geometrically (to the fourth, sixth and even eighth power) as flow velocities increase.
While this terse summary provides a simplistic explanation of where noise comes from, predicting noise generation in air and gasses is actually a very complex challenge. For example, scientists study noise at subsonic and supersonic velocities, and for subsonic sources, the noises in processing could be monopole, dipole or quadrapole (measurements of how sound waves radiate), with each of these levels adding more complexity to the equation. Also, noise created by the interplay of shock waves and turbulence can be influenced by the presence and geometry of physical boundaries in the vicinity of these interactions. Shock waves that are perpendicular to a free jet stream are called normal or direct shocks. A shock wave can also be oblique if the flow passes a wedge or sharp object or if supersonic flow is forced to change direction by a solid boundary. Shock waves can be reflected from solid boundaries and can penetrate one another. A control valve outlet flow stream can create an oscillating chain of compression shock waves with declining cycles and intensity—a very powerful noise source. With computational fluid dynamics, shock waves can be simulated in different geometries. Normally, super computers with substantial memory and processing power are used because the calculations required are long and complex. The results that these state-of the-art computer programs produce are used in the design of low-noise trims and attenuators.
Expert simulation and sizing
The scientific study of what creates noise in process lines is ongoing. However, after decades of research, much has been learned that can translate into equations to predict, with high levels of accuracy, the noise-generating potential for most piping and control valve configurations. These equations are available to process engineers within the International Electrotechnical Commission and the German Engineering Federation (VDMA) standards. Control valve vendors have specialists who understand these variables and can work with processors to predict and modify the noise-generating characteristics of process loops. Some even have expert software developed to simulate line conditions for making realistic predictions of flow and noise generation.
This expert software allows an experienced user to swap valves, trim and other components until the most favorable combination of noise attenuation and process performance has been achieved. If a control valve vendor can simulate control loops with expert sizing software, it is likely that vendor can detect potential noise generation problems in advance and minimize those noises using cost-effective source treatment approaches. In such cases, high levels of mechanical vibration, which are always associated with noise, can be minimized or eliminated at the outset to ensure greater control reliability and process uptime.
Source treatment
A variety of methods exist that can minimize the potential for noise generation. The most common are acoustic control, velocity control, location control and diffusion. Recently, trim has been defined specifically to address these types of aerodynamic noise.
Increasing the number of flow passages by making them smaller also affects noise frequency distribution— the smaller the passage, the higher the noise frequency. The pipe wall easily attenuates high-frequency noise. High frequencies are also less of a problem because they extend beyond the capabilities of the human ear.
Modifying the acoustic field directs the flow path in such a way that the peak noise field is broken up into a more diffused space.
Velocity control: Controlling the maximum fluid velocity inside a control valve trim is an effective way of controlling noise at subsonic flow velocities because the acoustic intensity of a jet is proportional to the sixth power of the flow velocity in a system with solid boundaries, such as valve trim or a pipe. The control valve trim velocity can be controlled most effectively by using a multistage pressure drop and by increasing the valve trim outlet area in a manner in which the flow velocity and pressure at the valve outlet are minimized and gas volume is maximized. The successive stages are spaced so that gas pressure is allowed to recover to an intermediate level and velocity before the next throttling stage. This intermediate recovery of pressure and the resulting velocity reduction prevents the fluid from reaching the velocity of a single-stage pressure drop system.
Location control: Two major sources of noise are turbulence that forms in the mixing region between where the jet exits from an orifice and the gas flows at the outlet region and attachment, and the interaction of shock waves. The piping system should be designed following documented best piping practices. Such practices specify factors such as the distance from transition pieces to valves for the purpose of delivering flow in as laminar a condition as possible (thereby limiting turbulence).
Location control is employed to make sure the jet streams within and departing from the trim are located and shaped to minimize the potential for noise generation. One way to do this is to smooth the velocity profile of the jet by introducing a lower velocity gas stream alongside the jet.
Diffusers: Diffusers have fixed area flow resistances and are custom-made for a particular flow condition. Dividing the pressure drop between a control valve and a downstream diffuser provides an effective way to further increase the noise attenuation in cases where the control valve has a constant, high-pressure drop, and the flow rate is relatively constant.
Aerodynamically specific trim: Typically, source treatment approaches applied within and around the control valve can solve most noise generation issues. Valve manufacturers have been studying and refining approaches to noise and anti-cavitation trim for decades now. As a result, combinations of all of the commonly used source treatment approaches can be applied to noise attenuation within a single device.
Path treatment
The path treatment for noise, i.e. suppressing the transmission of excessive noise levels along the path, can be performed by using at least three different tools: silencers, insulation and heavier pipe schedule. While less than ideal, path treatment is an approach that can be considered when vibration levels are not high enough to damage or inhibit the performance of the control loop or if source treatment alone could not bring noise generation down to acceptable levels.
Silencers: Silencers are mufflers used inline or at an outlet leading to the atmosphere to dampen the noise produced. Reactive silencers create frequency interactions to dampen noise; whereas dissipative silencers use sound-absorbing materials such as glass-fiber to dampen the noise. The main use for silencers is on outlets for gas or steam. Typically, a combination of reactive and dissipative methods is used in atmospheric vent silencers.
Insulation: Pipe insulation may be used to dampen noise in gas and steam lines, particularly in steam lines, where there is already thermal lagging. Thermal insulation can dampen noise 1-2 dBA per 10 millimeters (mm) of insulation thickness (3 to 5 dBA per inch). The maximum is about 12 dBA because of leaks and acoustic bridges. Special acoustic insulation reduces noise up to 4 dBA per 10 mm of insulation thickness (10 dBA per inch). The maximum attenuation for acoustic insulation is 20-25 dBA.
Heavy downstream pipe schedule: A heavier downstream pipe schedule can be used to dampen noise because vibrating pipe wall generates part of that noise. The heavier the pipe wall (the bigger the schedule), the less that wall will vibrate. Note that the noise level inside the pipe does not decrease with a heavier wall pipe. Because of this, the heavier wall pipe should be used for the whole downstream piping to avoid recurrence of the high noise level further down the line, which can be very costly in the case of long pipe runs.
Conclusion
Effective aerodynamic noise reduction in pipelines and control loops has become an important consideration for many industries. This is because control of such noise ensures a safe working environment, protects process and plant surroundings, enables stable process control, extends maintenance intervals and ensures legal obligations are met.
While noise can be suppressed after it is generated through path treatment, a generally more effective and less expensive alternative is source treatment. Much progress has been made recently in developing expert software technology for predicting noise generation under actual line conditions and for designing specific valve trim attenuation for aerodynamic noise. Processors who deal with air and gas control applications that have a tendency to generate noise should seek the assistance of control valve vendors that understand and can suggest these technologies.
Text by Steven Hocurscak and Kyle Rayhill
For additional information, please contact fred.porth@valmet.com
Published in VALVE MAGAZINE • Spring 2013
The text has been updated in April 2022, due to the company name change to Valmet.
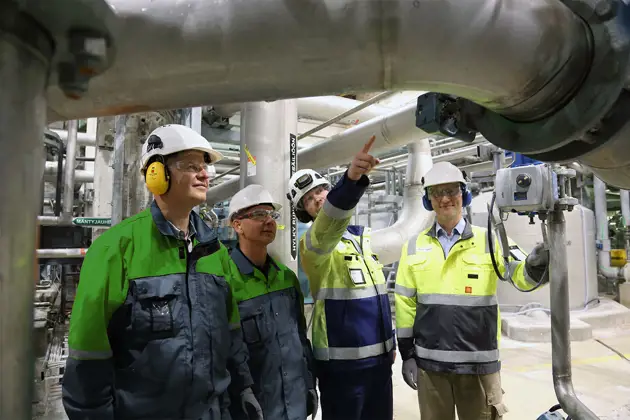
Subscribe to our newsletter
Subscribe now to flow control newsletter and receive the latest insights directly to your email.
SubscribeRead more about noise reduction