Enabling the energy transition with flow control solutions
Oct 30, 2024
As the power generation industry embraces the energy transition, Valmet is leveraging its extensive expertise with industrial gases to provide innovative flow control solutions. With a deep understanding of emerging technologies like green hydrogen production and carbon capture, utilisation and storage (CCUS), Valmet’s Flow Control business line is well-positioned to support the shift towards sustainable power generation practices.

Hydrogen is widely recognised as a crucial energy carrier for the storage and transportation of renewable energy. Its versatility and potential applications span a wide range of industries, from heating and electricity generation to powering vehicles and industrial processes. Recognising the growing importance of hydrogen, governments worldwide are actively planning the development of nationwide hydrogen pipeline networks to facilitate the integration of this innovative fuel into their energy systems.
Valmet’s Flow Control business line has a longstanding track record in handling industrial gases like hydrogen, oxygen and CO2, positioning the company as a trusted partner in the rapidly growing hydrogen economy.
Ville Kähkönen, Director of Renewable Energy and Gases at Valmet, highlights the company’s extensive portfolio, stating, “Our segment, butterfly, ball and other valve designs cover practically all valve needs in the energy transition, whether for hydrogen, oxygen or carbon dioxide service, withstanding high temperatures. Our valves have been proven in electrolysers, providing excellent control accuracy, safety and reliability.
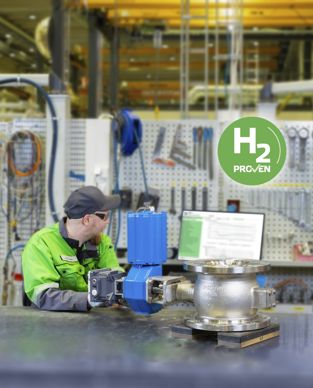
Addressing the challenges of hydrogen service
Handling hydrogen safely and effectively requires extensive expertise in material selection and testing. Valmet’s materials team has developed specialised knowledge in this area, designing and selecting appropriate test methods to generate data on how metallic and non-metallic materials respond in hydrogen environments. This data is invaluable for Valmet’s design engineers, allowing them to perform comprehensive engineering calculations to qualify material compatibility for hydrogen service.
While hydrogen presents unique challenges, Valmet’s decades of experience in handling industrial gases position the company well to address them. A key consideration is mitigating the risks associated with hydrogen’s small molecular size, which can make controlling internal tightness and fugitive emissions more challenging. Additionally, hydrogen has the potential to deteriorate certain material properties, reducing damage tolerance for components.
Liquid hydrogen service, commonly used for transport and short time storage, introduces further complexities due to the extremely low temperatures involved. “At these low temperatures, some metallic materials can become very brittle, and non-metallic materials can lose their properties, compromising valve tightness and safety,” explains Andreas Pischke, Global Industry Manager for Renewable Energy and Gas at Valmet. “Dimensional changes occurring during temperature transitions can also impact internal tightness and external sealing points.” Valmet’s comprehensive approach to material selection and testing, combined with its extensive knowledge in industrial gas applications, enables the company to develop valve solutions that can withstand the demanding conditions of hydrogen service in power generation facilities.
Enabling carbon capture solutions
As industries strive to reduce their carbon footprint, carbon capture, utilisation and storage (CCUS) technologies have emerged as critical components of decarbonisation efforts. Valmet is actively involved in the development of these technologies, participating in cutting-edge research projects like the Hydrogen UnderGround (HUG) initiative.
The HUG project, co-funded by Business Finland and part of Valmet’s Beyond Circularity R&D program, focuses on the underground storage of hydrogen, a key aspect of the green hydrogen value chain. Ville Kähkönen emphasises Valmet’s contribution, stating, “Our long experience and comprehensive portfolio cover most applications in the industrial use of hydrogen. Today, Valmet offers a wide range of segment, butterfly, ball and other valves for hydrogen applications, ranging from electrolysis to carbon recovery.”
In addition to hydrogen storage, Valmet’s expertise extends to carbon dioxide (CO2) applications, including handling risks associated with icing and phase changes. The company’s Flow Control business line offers valve solutions for various CO2 applications, from absorption and adsorption processes to cryogenic separation techniques.

Integrated automation solutions
Recognising the importance of automation and control systems in complex processes like hydrogen storage and handling, Valmet has invested in the development of its DNAe Distributed Control System. Anna Sydänmaa, Business Manager, Alternative Fuels, in Valmet’s Automation Systems business line, highlights the system’s key features, stating,
“The Valmet DNAe Distributed Control System has been engineered for demanding process control, emphasising performance and availability. The system architecture is cybersecure by design, and it’s been developed with a design philosophy to empower people to perform and collaborate better across the organisation.”
User experience and usability are paramount in ensuring the safe and efficient operation of these critical systems. Valmet’s longstanding focus on these aspects is now being extended to the HUG project, with plans to collaborate with the SEEDForest COACH project, led by the VTT Technical Research Centre of Finland, to adapt new technologies to users’ work environments.
Proven reliability and performance
In the energy transition, proven valve solutions that deliver long-lasting reliability and performance are critical. Companies like Valmet, with extensive expertise in handling industrial gases and advanced automation capabilities, are well-positioned to develop safe and effective solutions for demanding applications such as hydrogen service components and carbon capture systems.
Suppliers in this space must provide comprehensive support throughout the entire product lifecycle, from initial design and engineering to ongoing maintenance and service. A deep understanding of the unique challenges posed by different industrial gases and processes is essential for qualifying material compatibility and mitigating risks like fugitive emissions, hydrogen embrittlement and temperature extremes.
Valmet’s longstanding experience in the industrial gas sector, combined with its knowledge-based engineering approach, allows the company to address these challenges and develop reliable valve solutions for the energy transition. Continuous investment in research and development, as well as close collaboration with industry partners, is necessary to meet the evolving needs of emerging sustainable technologies across various industries.

Sustainable innovation across industries
The push towards sustainability and environmental responsibility is driving innovation across various sectors. Companies are developing solutions for emerging applications that support decarbonisation efforts, such as waste-to-energy systems, low-emission cement production and sustainable concrete manufacturing. This trend presents opportunities for valve manufacturers to adapt their products to meet the evolving needs of these industries while minimising environmental impact.
“We are seeing new, exciting applications where carbon capture plays an important role,” states Ville Kähkönen. “Industries such as the concrete and cement industries are starting to absorb CO2 from their plants, and biomass and waste-to-energy powerplants are popping up in conjunction with carbon capture units. All these new processes, when executed responsibly using reliable and proven technologies from recognised vendors, hold the keys to the first successful steps in decarbonising industry and paving the way for the green transition.”
This text was originally published in Valve World magazine, October 2024 issue.
Text by Melonie Dodaro, Editor, KCI Publishing.
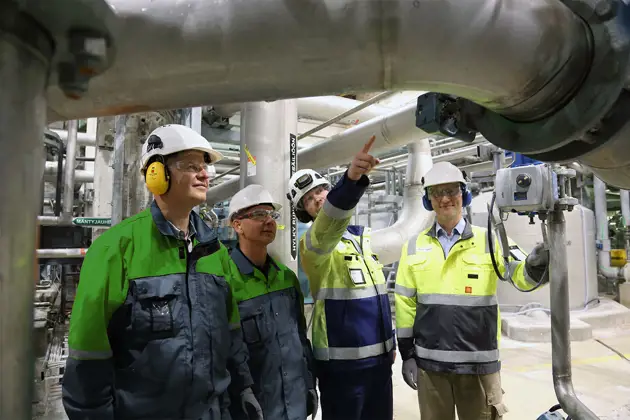
Subscribe to our newsletter
Subscribe now to flow control newsletter and receive the latest insights directly to your email.
Subscribe