Digging deeper for oil and gas with greater reliability
Today, when the extractable reserves of oil and gas are expended and natural resources can be obtained from more challenging locations, the industry has to deal with greater risks to keep production units safe for employees and the surrounding environment. Reliable valve performance plays a critical role in this challenge.
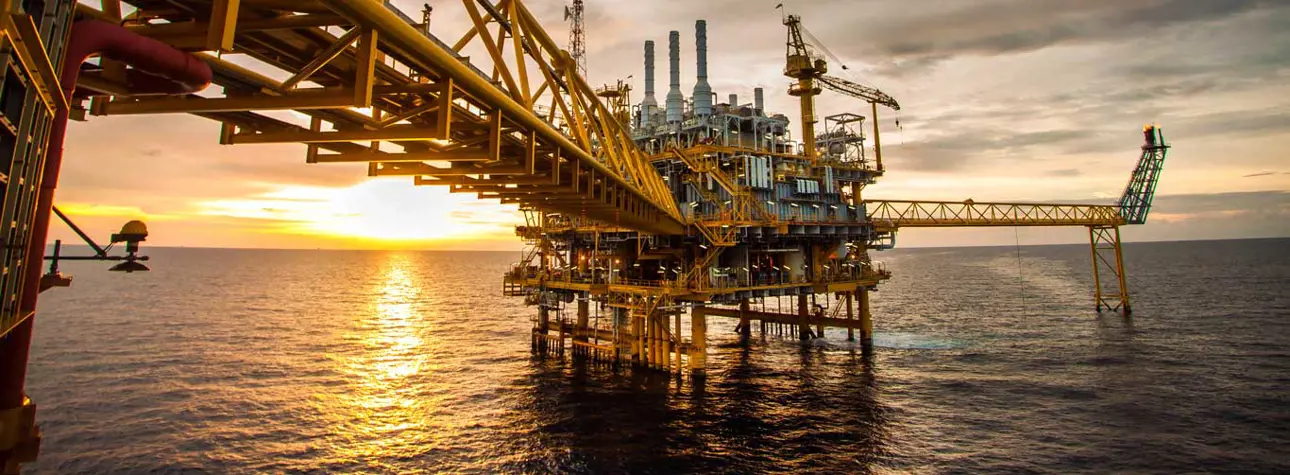
Customer challenge:
- Since the offshore oil and the gas industry is moving to more challenging environments, it calls for higher demands on the production units’ applications as well as experienced industry professionals.
Our solution:
- To match the needs of extreme conditions, Valmet offers solutions that include valves capable of withstanding higher pressures, nearly maintenance-free operation, and great size and weight optimization.
Key customer benefits:
- By having Valmet solutions in operation, oil and gas producers get the best total cost of ownership value, while keeping a tight control on quality and safety standards.
Oil and gas production involves great deal of risks that need to be addressed to perfection in order for production units to be safe for employees, surrounding population and vulnerable nature. This has been valid always, but even more today as easily extractable reserves are expended and oil is obtained from more challenging locations. In some cases this means extreme environmental conditions and adoption of new technologies as drilling goes deeper than before. These factors all increase risks related to the operation and companies need to keep tight control of quality and safety standards as a part of the operational culture.
Offshore production challenges
Offshore drilling is nothing new. It has been done for a long time, but now when the crude oil price has increased and more robust technological solutions have developed, activities to increase offshore production have as well increased. The best known locations for offshore production are the four big production areas of the North Sea, Mexican Gulf, Middle East and South East Asia. These areas are investing to new field developments all the time, but also ‘new’ development areas for offshore production have become very active in this game, mainly on the west coast of Africa and Brazil. In Brazil especially, new technology and higher oil prices have opened doors to start production plans for very deep pre-salt oil fields with extremely high expectations.
At the same time as off-shore oil and the gas industry is moving to new territories and more challenging environments, we are seeing experienced operating people retiring and in certain areas there seems to be a lack of young people entering the demanding off-shore profession. Additionally it is recognized by many in the business that there is miss-match between graduating students and industry demands. Also, there is no school education which compensates for experience, it comes only through hard work and when facing challenging situations during daily activities.
The role of valve and automation technologies
How can a valve company contribute to the challenges faced by the off-shore industry? The simple answer would be to tailor our offering to match the need of even more extreme conditions than our products face in the production units. Wellhead valves to withstand higher pressures, subsea valves with nearly maintenance free operation and generally, all valve components optimized for weight, which cannot be excessive. Remote location is an additional challenge as well. Maintenance optimization becomes more important since platforms are not designed to carry general spare parts for valve components. Only critical spare parts can be stored on a platform and maintenance staff visits need to be limited because of personnel capacity restrictions. Finally, products selected for the platform operation should be such that they provide best total cost of ownership value for the operator. This was discussed over a year ago in this magazine (please see Valve World June 2011). To be truly able to help the oil producers, the evolution of the valves must go beyond the self evident tweaking of valve designs, we need to focus not only on the closing element but also the surrounding automation. Automation can bring new possibilities related to valve operation and maintenance. When combining information from several sources, automation can provide information in the form that enables easier decision making and allows staff to concentrate to real process optimization rather than data mining from different information sources.
Enable intelligence to the valves
Valmet Flow Control has developed the perfect match to meet the off-shore industry demand for all kinds of automated valve controls. This means valve positioners and on/off valve controllers suitable to operate on top of any valve and capable of bringing intelligence to these valves. The intelligent control valve positioner, ND9000, offers extreme ruggedness with industry leading control performance and diagnostics to simplify maintenance decision making and make it easier with Valve Manager™, free-of-charge software.
To improve process safety for emergency shutdown valve (ESD) operation, we have introduced a second generation, intelligent safety solenoid valve (VG9000). Capable of fast safety action for the valve, operating performance diagnostics are achieved with partial stroke (PST) and internal pneumatics tests. These tests can be automated if allowed in the plant and all results are stored in the positioner memory, optimizing the communication between field devices and asset management system. This solution is designed according to IEC 61508 requirements and certified by TÜV Rheinland up to, and including, safety integrity level 3 (SIL3). All safety features are available with different safety and asset management systems and interoperability is guaranteed. The safety signal can be either a traditional digital output or 4 to 20mA analog output. Asset management connection can be made either using HART or Foundation fieldbus communication. For automated on/off valves, it’s becoming more common to combine solenoid valve and limit switches in one package. This makes the installation more robust and provides the capability to get more information about the on/off valve operation when using for example; Asi, HART or FF communication. Valmet provides two solutions for on/off valves. With valves that are not critical from the process availability point of view and where maintenance activities do not need to be planned, it is enough to combine solenoid valve and limit switches into the same package. Here, a product called Axiom gives cost efficient solution with high Cv capacity. For diagnostics in critical on/off applications, SwitchGuard SG9000 offers valve performance diagnostics and several operational advantages such as programmable opening and closing curves to reduce pressure shocks generated by the closing or opening valve.
How to analyze diagnostics
Valve performance measurement and basic analysis creates the baseline for information management, but in addition to this, information needs to be carried to the right persons in the correct format. When diagnostic information is included in an efficient asset management tool, such as the FieldCare, the enduser can manage automated valves throughout their life cycles, taking the specific needs of each phase into account. The benefits of control and on/off valve diagnostic information are particularly apparent in the planning of plant shutdown maintenance actions. Safety valve diagnostics information needs to be recorded for safety audits and most obviously ensures that all the safety valves are ready to take action in the rare case they are required.
Diagnostics information needs to be communicated to the user in a way that supports the effective delivery of information. FDT/DTM development began early in 2000 and this technology is readily available from most suppliers. By utilizing its full potential, the information can be delivered in easy to understand format at the correct time. The right information, delivered at the right time, to the right person will help you to:
- Provide real-time operational and maintenance data to onshore expert centers, thereby reducing the cost and risk of offshore staffingdentify deteriorated performance and provide guidance on how to resolve these issues
- Share that data with relevant parties, regardless of location
- Enable device optimization to ensure profitable operating
- Identify changes in equipment performance to proactively resolve problems and avoid process disturbances
- Monitor real-time asset health for predictive maintenance purposes, allowing prioritization and planning of maintenance trips offshore
- Provide targeted information to maintenance personnel on equipment problems, including suggestions for corrective actions
As the amount of data is increasing so rapidly, usability must be the driver for development not the quantity of the data. A common trend in the latest attempts to improve diagnostics is the desire to make diagnostics increasingly user friendly and also comparable from device to device. For example, the Namur NE107 standard defines how the most important status symbols should look like. The latest developments in valve diagnostics combine the different purely specialist oriented data to be further processed, easier to use and illustrative.
The new Neles™ Valve Manager™ will take this approach to a new level. When the user opens the Neles™ Valve Manager, the first screen immediately tells the user how the control valve assembly is performing and describes the condition of its components. The opening screen shows the status of valve assembly components with symbols according to the Namur NE107 standard. In cases where something is wrong with the control valve, the user is provided with the most probable root causes analysis and solutions to fix the problem. The screen also includes a graphical presentation of setpoint and actual valve point and supply pressure as well as actuator channel pressures. However the sweetest fruit of the most recent development is the graphical presentation of five different indices describing; control performance, valve, actuator, positioner and external conditions.
The mathematics behind the indices is developed from Valmet’s large installed base and service experience. The models are verified against large databases of information from real conditions in various process industry branches. The algorithms behind the indices partially replace a specialist in the interpretation of available data, so less know-how is needed from the user. This has many advantages: the regular users are usually responsible for a large variety of field devices so the quality of information will be enhanced, wrong interpretations will diminish and the valuable time of specialists can be saved for matters that truly need their attention.
Information processing of the valve assembly
An intelligent control valve positioner, such as the Neles™ ND9000 or ValvGuard VG9000, gathers information on the valve performance throughout its life cycle. Modern valve controllers store all this data in the device’s own memory. This data can be accessed not only on site, but also remotely. Basically, there is no difference between processing the diagnostics data on-site or from thousands of kilometers away. While remote condition monitoring does not fully replace inspection “footwork” done on-site, it can focus and improve it. Depending on the application, valves should be regularly tested for tightness, condition of valve coatings, etc. These observation results can be stored in the same system together with the valve controller’s diagnostics data and subsequently the valve diagnostics can create a work order to the ERP for a maintenance check.
Valmet Flow Control business line has several years of experience in condition monitoring and predictive maintenance with customers in different branches of industry. This experience has proven that the amount of information from a site with hundreds of valves equipped with smart positioners can be huge, but it really becomes valuable when used in right way. One practical example comes from a safety valve audit on an off-shore platform. The platform had been in operation for only one year before the audit. Expectations of the audit result were that all safety
Once the immediate problems were corrected, training for the operating personnel was conducted and now safety valve diagnostics information is routinely followed, when there is need for corrective actions, they are carried out to ensure that safety system is in peak condition if needed. Processing this information is greatly improved, both in terms of quality and cost effectiveness, with the help of state-of-the-art condition monitoring algorithms developed at Valmet. By utilizing knowledge of control valve behavior, diagnostics gathered by the intelligent valve controllers and advanced mathematics, Neles™ Valve Manager ™ indicates those control valves whose performance has changed and suggests the most probable reasons for impaired operation.
Text by Sami Nousiainen
Published in Valve World magazine, September 2012 issue as 'Keep offshore production safe and available'.
Text originally published in 2012, and slightly updated in April 2022, due to the company name change to Valmet.
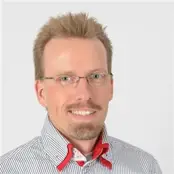
Sami Nousiainen
Vice President, Service and MRO Business unit
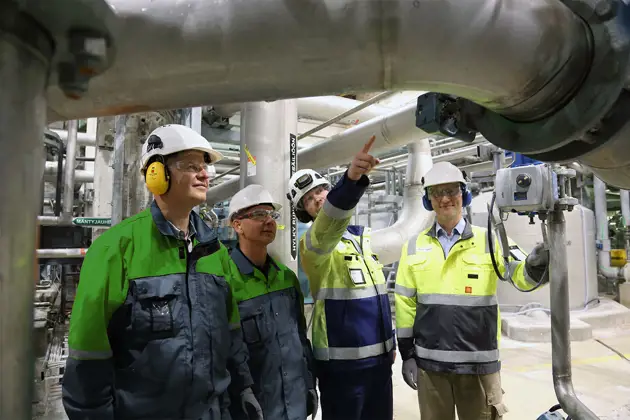
Subscribe to our newsletter
Subscribe now to flow control newsletter and receive the latest insights directly to your email.
Subscribe