Condition monitoring drives reliability and process improvement
Condition monitoring is the science and practice of monitoring key information to alarm, predict and prevent problems. In a way, condition monitoring is one of the original ‘big data’ applications in the industry.
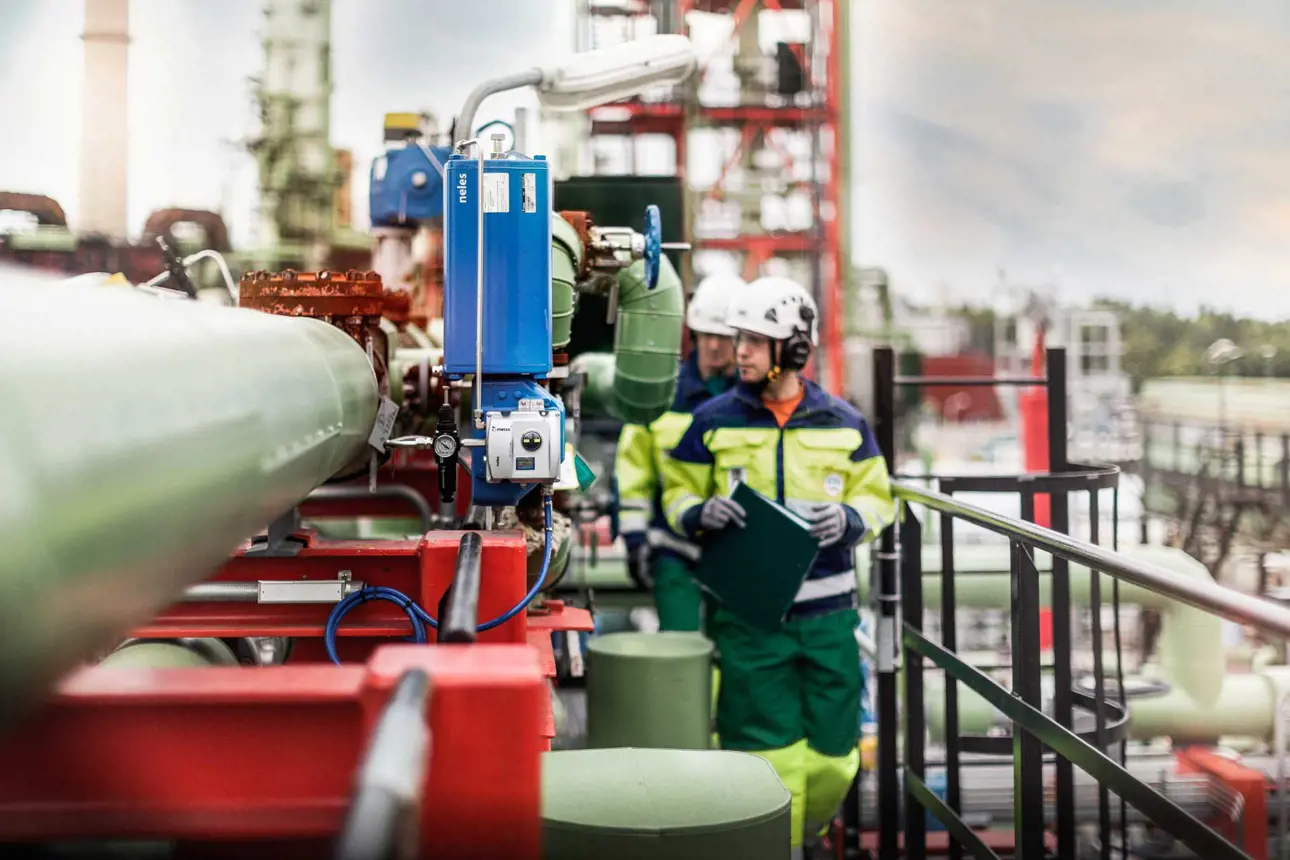
The principles and practices of condition monitoring can be applied broadly to many classes of equipment and processes. Smart instruments and smart valve positioners provide condition information throughout the plant. Even 'dumb' instruments can be effectively analysed by software tools using real time data from the plant's control system or data historian.
Traditional condition monitoring approaches consider, for example, vibration data from rotating equipment. This information can then be automatically analysed to alarm upon excessive vibration. Detailed analysis of the vibration frequencies can also be used to predict specific upcoming failures, such as a worn bearing. Other information, such as motor winding temperatures, can be used preventively to address bad operating conditions early and make adjustments to operation or equipment maintenance practices.
This article takes a broader view by describing how condition monitoring serves to drive specific, targeted actions to improve the reliability and performance of controls, equipment, and, ultimately, the process. The goals go beyond reliability alone, and address all of the plant's key performance metrics, including safety, environment, reliability, quality and production.
Condition monitoring practices
Instrumentation and controls are the starting point for condition monitoring.They are the senses and the 'central nervous system' of the plant. One must have reliable, accurate information as the basis for any monitoring effort, as, if measurements are inaccurate, noisy, or failed, then these efforts will be unsuccessful. Similarly, if the base regulatory controls are performing poorly, or unstably, then it becomes difficult, or impossible, to monitor the equipment and the process. Somewhat surprisingly, most plants suffer from significant issues with the base layer of instrumentation and controls.
Condition monitoring should not be a pure function of the maintenance department. A number of personnel can, and should, be affected by the actions resulting from condition monitoring analysis. While mechanics may need to investigate a motor, instrument technicians repair valves, control engineers perform loop tuning, operators adjust the process and process engineers make changes to the operating procedures.
Condition monitoring for instrumentation and controls
T
Many plants are operating with more than 20% of their controls in the manual operation, with up to 5% of instruments showing signs of failure and as many as 30% of valves with significant mechanical faults. While plants are able to keep running in these conditions, it is obviously sub-optimal, and the corrective action of these faults can lead to big business gains.
Condition monitoring identified a sticking valve. The process calls for flow to be set according to a pre-determined set of values, however, the valve is 'sticking'. So the valve controls keep trying to push the valve open or closed. This clearly upsets the process with an unsteady flow and wears down the valve with excessive movement. A simple inspection identified the problem as low air supply pressure to the valve. The corrective action, adjusting the air supply regulator, could be accomplished in just a few minutes, with only a small investment of time. Simple repairs that prevent unplanned shutdowns represent the highest return on investment for the entire operation.
Equipment condition monitoring
Aside from the rotating equipment mentioned above, there are many other forms of equipment monitoring in use. Each type of equipment may need a specific type of monitoring; however, there are some common themes:
- Monitoring hours of operation.
- Monitoring against design capacity.
- Monitoring of the environmental conditions, such as temperature and humidity.
- Monitoring of vibration.
In addition to these common metrics, each specialised piece of equipment may have its own form of monitoring:
- Heat exchangers can monitor pressure drops and fouling rates.
- Infrared thermography techniques can detect loose wiring connections as well as problems with bearings or couplings.
- Analysis of lubrication fluids can detect component wear.
- Ultrasound methods can detect issues with mechanical systems or fluid flows.
Process condition monitoring
The operating process is usually monitored closely by operations. Key performance metrics, such as production rate, quality and uptime, are tracked, trended and reviewed on a daily basis. More detailed condition monitoring is now becoming the norm in the process industries. Tracking of operating 'windows' or 'envelopes' provides better insight into areas for process improvement. Traditionally, this is in the realm of process engineers.
The latest advances are tools and techniques to understand interactions between process, equipment and controls. After all, many process problems originate with equipment or instrument and controls issues. The challenge has been that process, equipment and controls monitoring are carried out separately, by different departments, and without good methods to compare information.
One example of how this is changing is the root cause analysis tools, such as the process interaction map. This, and other big data analysis tools, have entered the arena of condition monitoring, allowing plants to leverage historical data to develop greater insight and understanding. Furthermore, these tools help to streamline problem solving by clearly determining whether a root cause is related to equipment, process or controls. This ensures that the correct personnel are called upon to perform the proper corrective actions in a timely manner, avoiding the trial and error, waste, or re-work that often follows problem solving efforts.
How to get started
Chances are, a plant is already running at least some condition monitoring. Smart instruments and smart valve positioners are performing the monitoring, and even some of the analysis, but is all the condition monitoring information being used effectively? The following methods can be used to achieve the best gains from condition monitoring:
- Prioritise: choose the process operations with the highest business impact.
- Leverage: make good use of what is already there.
- Consolidate: put in place systems to consolidate and share data with personnel in different roles.
- Routine monitoring: data is of no use unless somebody is using it. Put in place business practices to make good use of the information.
- Prioritise again: with the key information to hand, actions/action plans should be prioritised again.
Conclusion
Today, condition monitoring offers plants much more than just checking the health and performance of individual instruments, equipment and processes. If used properly, condition monitoring improves a plant's intelligence and increases both reliability and performance. In the best case, when all data from the controls, equipment and process is synchronized, a plant can take full advantage of condition monitoring to enhance many of its other key performance metrics, including safety, environment, reliability, quality and production.
Text originally published in 2017, and slightly updated in April 2022, due to the company name change to Valmet.
Published in Hydrocarbon Engineering magazine July 2016 as 'The Drive to Success'
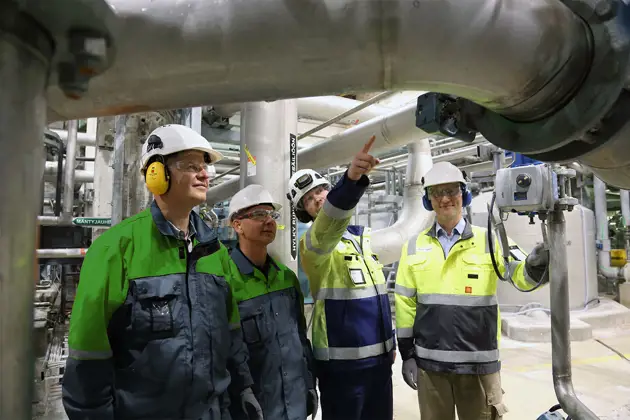
Subscribe to our newsletter
Subscribe now to flow control newsletter and receive the latest insights directly to your email.
SubscribeRead more about condition monitoring