Always putting the customer first
Always putting the customer first
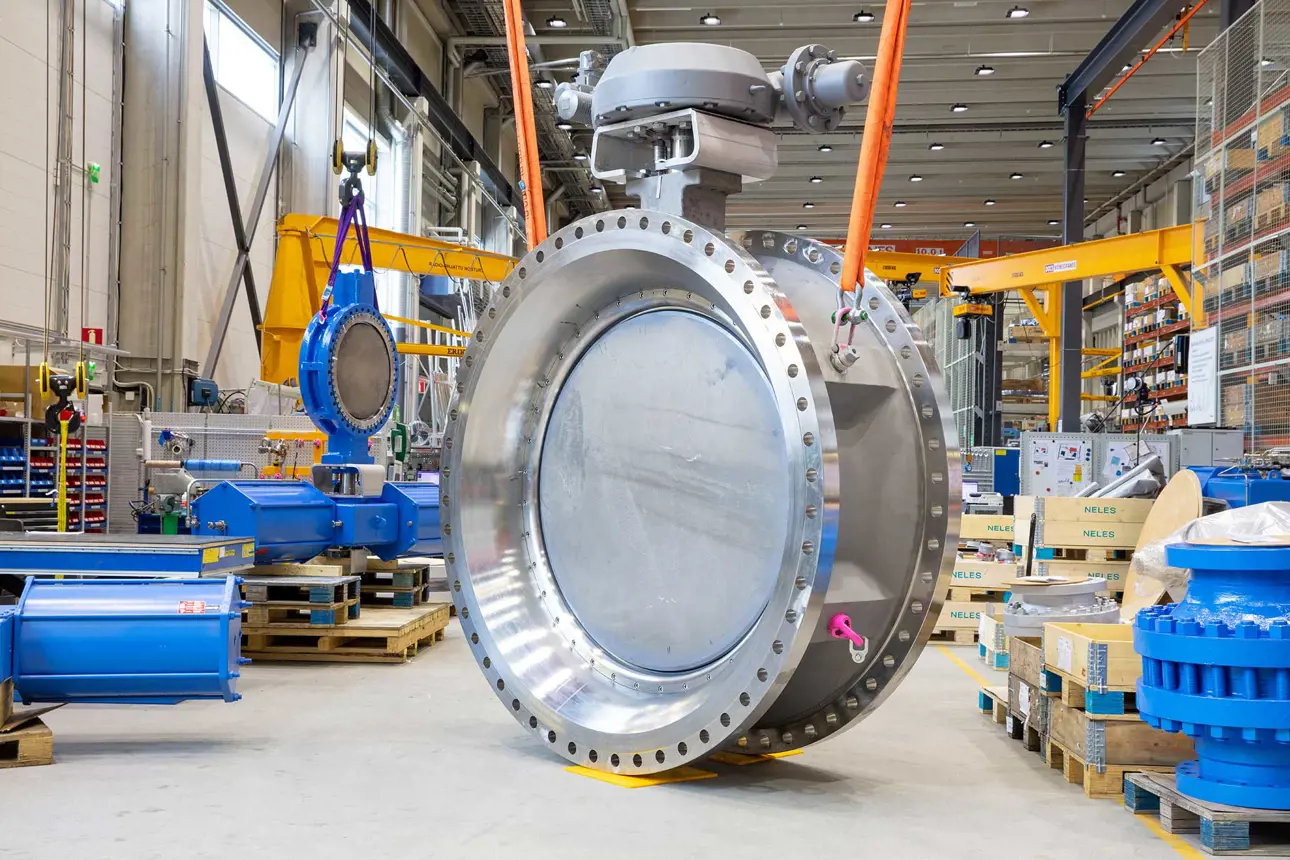
CHAPTER ONE An exciting journey
In July 2021, just a day after its first anniversary, Neles issued a joint statement with fellow Finnish company Valmet stating a merger has been agreed that will provide ‘enhanced growth opportunities and benefit from broader revenue and cost synergies’. This decision makes good business sense and should create exciting new opportunities and synergies for both companies. Whilst Valmet is focused on technologies, automation systems and services for the pulp, paper and energy industries, Neles offers flow control products such as valves used in all process industries.
Commenting, Neles President and CEO, Mr. Olli Isotalo, says: “through our capabilities and know-how, we have positioned Neles for best in class growth and profitability and now look forward to accelerating this agenda as part of the combined company. We are delighted about the opportunities to continue to execute our growth in flow control across process industries from an even stronger base. The combination also creates attractive opportunities to digitalize our joint services to support customers’ efforts to achieve greater sustainability in their operations.”
Mr. Isotalo’s positive sentiments are mirrored by colleagues in India and the Middle East. For example, Paul Isaac, President, India Market Area comments that: “Neles and its predecessors have been operating in India for over 45 years. Neles is known for severe service valves and controls in various process industries. With the acquisition of India-based Rotex Manufacturers and Engineers Pvt. Ltd. in 2018, Neles footprint in India market was further strengthened with a full range of complete automated valve solutions. Since 2020, we have been strengthening our channel partner network in the region to offer more unique value-added solutions through this extended arm. Even during this difficult pandemic time, Neles’ three modern manufacturing plants and over 500 India based employees were fully focused on delivering products and services to meet both local and global customer needs.”
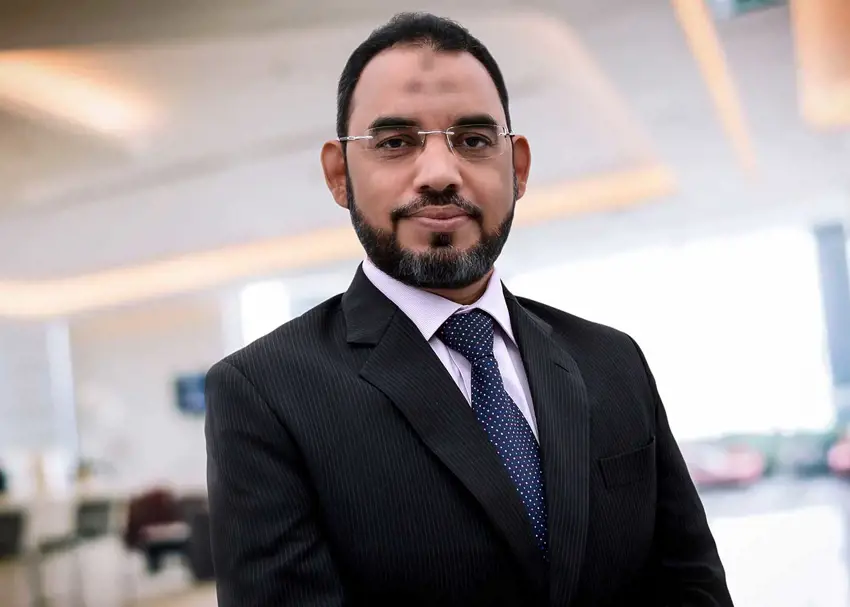
Haroon Azmi, Vice President, Middle East Market Area- Dubai- UAE is equally proud of what Neles has achieved. “Neles has a significant footprint in Middle East. We operate a manufacturing plant in Dammam, Saudi Arabia, and have a service/valve automation centre in Ras Laffan, Qatar. In addition to manufacturing, operations are focused on late customization, including a wide range of testing functions, application engineering services, and valve services and troubleshooting.”
CHAPTER TWO Comprehensive product offering
Industry sectors throughout India and the Middle East have ready access to Neles’ huge portfolio of products and services. “Customer groups in India include process industries such as chemicals, energy, gas processing, LNG, industrial gas, refining, fertilizers, pharmaceuticals, and of course, pulp and paper. Our preengineered product range also caters to industrial sectors like chemicals, pharmaceuticals, ONG, utilities, water etc,” states Mr. Isaac.
“As might be expected, Valmet products are in high demand throughout the broader hydrocarbons sector in the Middle East,” adds Mr. Azmi. “You will find our valves in areas such as oil & gas, refineries, petrochemical plants and industrial gas facilities, but also in mining, power, and pulp and paper.”
Never content to simply provide ‘off-theshelf’ products, Neles often engineers bespoke products to meet unique local conditions. “Clients in the Middle East have been early adopters of many of Neles’ advanced products, such as the Neles ValvGuard™ VG9000, the intelligent safety solenoid and partial stroke test devices for ESD valves. While many requirements in the Middle East will be similar to process industries elsewhere, customers in this region can have unique requirements. For example, they may request us to take into account high levels of hydrogen sulphide, or the desert conditions with high salinity in the air etc,” comments Mr. Azmi.
Mr. Isaac concurs. “Customers in India face pretty much the same challenges as everywhere else. However, there are quite some differences as regards legislations and standards. Moreover, in the current production climate, demands are high. Besides the economic parameters, there is also a heightened regulatory, environmental and safety pressure, for example, on fugitive emissions. Neles offers a range of high technology control and automation products and services for Indian markets, to meet our customer and process licensor needs. Our remote asset management and predictive diagnostic solutions for critical applications, gives us a distinct leverage in the digital flow control space and are widely accepted in the industry!”
Neles’ manufacturing units in India are also contributing to Neles’ global market range, continues Mr. Isaac. “Our well designed, topperforming products for the Indian market includes state-of-art pneumatic products, such as scotch-yoke, rack and pinion actuators, pneumatic cylinders etc. We can now serve a multitude of process industries with a wider range of high-quality flow control solutions and stronger local support in India. Also, the Easyflow by Neles™ range of pre-engineered products from Indian plants for mid-market applications are now available for global projects too. And our third-generation state-of-art valve controllers and positioners have long been included in the Neles basket of products.”

CHAPTER THREE Digitalization
In today’s world, change is a constant factor. This also applies to requests from Neles’ client base, states Mr. Isaac. “Customers increasingly request us to facilitate information streams on how their processes are performing. Highly relevant data can be collected through digital positioners which communicate with the DCS or similar systems. Take for example Neles’ analysing and diagnostic tools which can be used to prevent unplanned maintenance issues.”
Discussing how plants could upgrade their information flow, Mr. Isaac indicates that digitalization starts with a comprehensive inventory and rationalization of the installed base. “In many cases, installed base lists are not up-to-date which has knock-on effects on asset management and maintenance. We help customers streamline their lists thus enabling significant savings in manhours and inventory costs. This paves the way for more advanced maintenance concepts, such as predictive maintenance. Neles smart control valves hold condition and operations data that can be used to save on maintenance costs, prevent unplanned shutdowns and subsequently optimize output.”
CHAPTER FOUR Game changers
Throughout its 65 years in the flow control business, Neles has consistently set R&D benchmarks. For example, in 1973 a creative engineer called Antti Nelimarkka came up with a metallic seat ring which would improve valve reliability in exceptionally demanding conditions and applications. The result was the Neldisc, the first triple eccentric metal-seated butterfly valve in the world which was to become the norm in the industry.
Of late, Neles has been at the forefront of integrating additive manufacturing technology into the valve and actuator supply chain. “Additive manufacturing, or AM for short, has matured rapidly,” comments Mr. Azmi. “AM experts at Neles are currently working with others to develop guidelines which will provide quality assurance to end users.”
In some sectors AM is viewed as simply a handy tool for developing prototypes, but not so at Neles “We see real opportunities with AM for less standardised parts. Take our noise attenuation trims which with AM benefit from very complex internal flow paths,” Mr. Azmi states. “For the customer, AM therefore means having access to a superior valve trim with a longer life span and more reliable performance.”
Coming right up to date, Neles is also playing an influential role in using AM in the production of pressure-retaining components. In May this year Neles delivered its first valve with an AM body for field testing at a power plant in Finland. Comments Mr. Isaac: “as the valve body is a pressure-retaining component its material properties need to be well known. We therefore tested the valve body material extensively, to ensure it is safe and reliable in the process.”
He further notes that the field tests will yield valuable information on the feasibility of using AM to produce pressure-retaining parts with significantly quicker delivery times. “Moreover, AM enables more efficient use of materials as well as valves that have been optimized for customer-specific needs. This again keys into our constant endeavour to improve our customers’ and our own business in terms of reliability, performance, and material efficiency.”
Additive manufacturing
AM
enables more efficient use of materials as well as valves that have been optimized for customer-specific needs.
CHAPTER FIVE Continuous innovation
Of course, AM is just one of many initiatives underway at Neles. Another research project concerns MMCs, short for metal matrix composite materials.
Says Mr. Azmi: “MMCs are a very exciting new development within material science. These hybrid materials combine the superior hardness of ceramics and the toughness of metals to offer the best possible reliability and performance to end-users.”
The ceramic addition in MMCs promotes wear resistance, whilst the metal carries the mechanical load and improves impact resistance, adds Mr. Azmi. “We have built up expertise in technologies, such as advanced powder metallurgy, that are needed to integrate MMCs materials into products. These MMCs are then used as an inner layer in multi-material constructions where the outer layer is a standardized construction material. This combination ensures PED requirements for ductility are met.”
Asked for a reference, Mr. Azmi reveals how MMCs have been used in a Fluid Catalytic Cracking unit. Here, the original CrMo-material used for handling catalytic fines (at above 200 °C.) typically failed between one to three months of operation. “Neles’ solution - a 5-15 mm MMC armoring onto wear intensive surfaces - has extended the lifetime from three to 25 months. Furthermore, maintenance and HSE-activities were reduced by 90 per cent. This shows the value of investing in superior materials as MMCs can deliver a much better total cost of ownership.”
Metal matrix composite materials
MMCs
are a very exciting new development within material science.
CHAPTER SIX User friendly
Another recent development has been the launch of a versatile butterfly valve range, understood to combine ease-of-use with a higher degree of sustainability. States Mr. Isaac: “with its proven technology and state-of-the-art functionality, our latest butterfly valve range offers superior process efficiency with a minimized environmental footprint.”
According to Neles, this latest product platform offers reliable solutions for a wide range of applications, including a high-cycling valve to handle high-purity gases and valves for abrasive service or corrosive media. The crosscompatible components and standardized parts make it easy to upgrade valve performance without the need to replace the entire valve.
“Instead of focusing only on one maintenance interval, we considered the entire life cycle of the product. Along with high performance, the valves are also designed for easy maintenance. Serviceability increases the lifetime and safety of the valve and minimizes waste,” Mr. Isaac notes.
“Our goal was to simplify valve selection for all customers, irrespective of their industry or technical background,”. sums up Mr. Azmi. “Thanks to the new range, customers can easily select the features, functionalities, and materials they need to create a robust and reliable butterfly valve that meets their exact requirements. This exemplifies our approach to doing business: Neles’ focus isn’t so much about making valves; it’s about making life easier for our customers.”
This article was originally published in Valve World India & Middle East Journal, September 2021 issue.
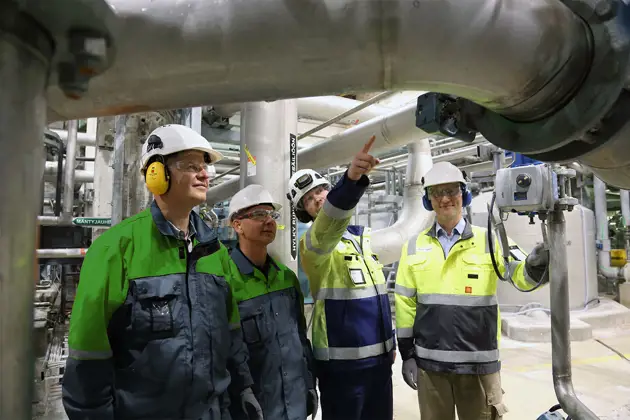
Subscribe to our newsletter
Subscribe now to flow control newsletter and receive the latest insights directly to your email.
SubscribeRead more about the topics