The diverse role valves play in the chemical industry
Jul 7, 2022
The chemical industry is extremely diverse with more than 60,000 known products. Chemicals are typically split into basic categories including petrochemicals, agrochemicals, specialty chemicals, pharmaceuticals and bio-chemicals, and consumer products. Like all process industries, the chemical industry needs valves designed for safe, efficient and reliable process operation.
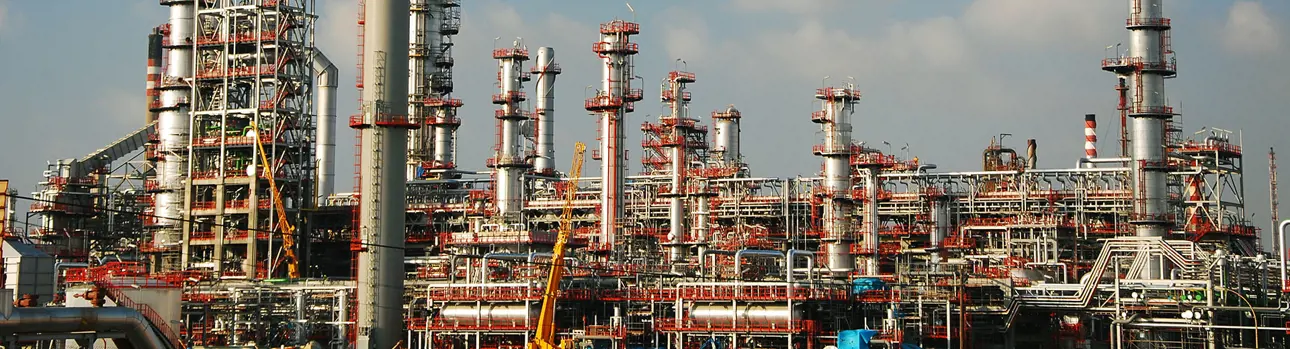
From a functional perspective, the industry has a need for control, emergency shutdown, manual/automated on/off, safety and pressure relief valves. Typical valve types used are gate (multiple variations), globe, check, plug, diaphragm, ball, butterfly, as well as other rotary control valves like segmented ball and eccentric plug valves.
From left: Sampling of valves used in chemicals processing: linear globe valve; modular trunnion mounted ball valve; and a butterfly valve pressure swing.
There are many ways chemical compounds can be extremely dangerous. They can be either extremely corrosive, abrasive, sticky, volatile or highly toxic substances. To ensure safety and reliability, it is important to take both the process conditions and the characteristics of the flow media into account when selecting valves. The chemical in question may affect the lining, material selection or even construction or design of the valve.
The diverse petrochemical and polymers sector
Within the chemical industry, petrochemicals are one of the largest segments including olefins (ethylene, propylene, butadiene) and aromatics (benzene, toluene, xylene) – then used for various applications to produce wide variety of products. For example, ethylene, produced typically by steam cracking process, is further utilized in the production of polyethylene by polymerization and other ethylene-based derivates.
In a steam cracker, the fuel gas valves need to handle various control loads, hence rangeability of valves can be a critical factor. On/off valves handling the fuel gas may need third-party approvals with compliance to EN161, Factory Mutual (FM) Global Class 7400 (fire safe class 7440), or CSA International Standards Specification Z21.21/CSA 6.5 Automated Valves for Gas Appliances.
Drying ethylene before it enters the cold zone area is typically done by using molecular sieve beds. Valves around these dryer beds are subject to various thermal conditions during adsorption and regeneration. Valves in the cold zone need to handle cryogenic temperatures and very high pressure drops. For fuel gas control, globe valves are typically the primary solution but when rangeability is a factor, segmented ball valves can be a viable option as well. In the cold area, where valves capable of handling cryogenic temperatures and high pressure drop applications are needed, globe valves with multistage trims help to eliminate noise and cavitation.
Globe valve Omega multi-stage anti-cavitation trim.
Metal seated ball valves are an ideal solution for dryers in a steam cracking unit. These valves can handle wide temperature swings and frequent cycling. Rotary valves are easy to handle, compact and offer various orientation options compared to other valve designs.
The polymerization process needs to handle fluid medium with polymers, resins and catalyst residue. These fluid media are challenging as they can accumulate in the valve body cavity thereby affecting the availability of these valves. This may result in process interruptions with every minute the process is out of use causing considerable loss to the plant owners. Another challenge associated with this process is high cycling (up to 1.5 million cycles annually). Valves around the catalyst systems that handle dry catalysts typically face severe trim erosion. Fugitive emissions and seat leakage in valves also need to be tackled, given the importance of safety and a minimized environmental impact.
Once again, metal seated ball valves with solids-proof seats have excellent proven performance. The “polymer proof” seat helps to prevent the media from entering the seating area. Continuous contact of the ball and seat with a scraping seat design helps to remove any particle build-up on the ball. For polymer slurries, segmented ball valves are quite effective.
Ball valve with solids proof seats and live-loaded packing.
Aromatics units with dry flow media like p-xylene sticks to the trim surfaces, hence increasing the friction and wear. In certain separation processes, valves are subjected to high cycles, requiring precise control. Typical solutions include metal seated ball valves with scraping seat design, as well as segmented ball valves and eccentric rotary plug valves with specific coating material to handle the high friction. Triple offset butterfly valves can also be suitable solutions in the benzene and toluene extraction processes.
Fertilizers and the agrochemical segment
In the agrochemicals segment, nitrogenous fertilizers account for more than 50% of the market, with ammonia being a vital key component. Ammonia synthesis is used to produce ammonia from nitrogen and hydrogen. A mixture of hydrogen and nitrogen, usually originating from a steam reformer, is admitted to the synthesis loop and compressed in two stages into the synthesis pressure of 2200-4400 psi (150-300 bar). The ammonia conversion process is a compromise between temperature and pressure. For the catalyst to be efficient, a temperature of at least 750°F (400°C) is needed.
The high temperature, very high pressure presence of hydrogen and ammonia are challenging for any valve. Emissions control is important due to the toxicity of the media being handled. Triple-eccentric butterfly valves provide the optimal solution for ammonia synthesis loop isolation and control. The design reduces wear and facilitates an extended operational life through the wide pressure and temperature range, body and trim materials, with tight shutoff in some of the harshest conditions.
Solid metal seated options allow the highest possible flow velocities without damaging the seat. Additionally, seats are typically interchangeable without the need to disassemble the disc and shaft. Live-loaded stem seals are standard, and valves are fire tested and generally certified for emergency shutdown up to Safety Integrity Level (SIL) 3.
Neles™ Neldisc™ triple eccentric metal seated butterfly valve.
The rise of specialty chemicals
The drive toward solar energy has generated increased demand for photovoltaic panels in which polysilicon is a key raw material. Polysilicon has long been a raw material in semiconductor devices whether it be your mobile phone, laptop or personal vehicle.
A typical polysilicon process uses SiO2 (quartz sand) as raw material to produce metallurgical grade Si, also known as MG-Si. MG-Si is obtained in an arc furnace with the presence of carbon. During the process, raw material, intermediate products and by-products include Si powder, Cl2, H2, HCl, SiHCl3, SiH2Cl2 and SiCl4; therefore, the valve’s design must be able to deal with these media, especially the highly abrasive Si powder. H2 and SiHCl3 are easily combustible, HCl is extremely corrosive and SiHCl4 is a highly toxic substance. All these chemicals should be captured and recovered to decrease raw material consumption and increase overall process efficiency.
Rotary stem operation, live-loaded gland packings and an inherently fire safe design ensure that all the latest emission and fire safety standards can be applied. Soft-seated ball valves with polymeric flexible lip seal designs that use molecular enhanced PTFE as a seat material provide a long-term solution even with high cycle operation. Metal seated ball valves with dustproof seats have proven themselves well in silicon powder addition where the valve is typically subject to high erosion.
Demanding inorganic chemical processes
Titanium dioxide (TiO2) is another application that is demanding for valves. The material is commonly used as a white pigment in paint manufacturing, paper, plastics, rubber, ceramics and fabrics. TiO2 is generally produced from its ore, which is either ilmenite or natural or synthetic rutile. Ilmenite-based raw materials are typically used for the wet sulphuric acid process, while rutile is the used in the high-temperature chloride process.
The production process exposes valves to high temperatures, abrasive slurries and corrosion. Metal seated ball valves with carbide coatings and bellow seats are the most suitable for isolation at high temperatures. Pinch valves are often preferred in the handling of abrasive slurries. They provide a full and true bore in the open position with no restrictions. Heavy-duty pinch valves with superior elastomer technology are ideal for both shut-off and control applications. Controllability can be further improved with conical sleeves and intelligent positioners. The rubber sleeve is the only wearing part, which helps extend service intervals and significantly reduce maintenance costs.
The chlor-alkali segment also presents many challenges for valves. Chlorine passes through liquefaction for storage and transportation and vaporisation for processing. Liquefaction is performed in stages and valve sizes typically range from 3 inches to 20 inches and ANSI Class 150.316SS is the typical material of construction due to low temperatures. With liquid chlorine, valves with CS bodies and Monel trims are recommended. Double-eccentric butterfly valves with live loaded packing to contain fugitive emissions are commonly used.
Flowrox™ pinch valve.
The process of turning Cl2 liquid into vapor requires the application of heat under controlled conditions. Hot water or steam is modulated to maintain the vapor-producing temperature of the vaporizer section. Rotary control ball valves are used for modulation, while the numerous drain and isolation valves used are almost exclusively threaded end ball valves. PFA-lined ball and butterfly valves as well as diaphragm valves find extensive use in brine preparation and caustic soda production for corrosion protection.
Interior view of pinch valve.
Technology improves safety in all chemical processes
Intelligent controllers combined with reliable valves and actuators have ushered in an era of enhanced safety and availability. SIL 3-approved intelligent solenoid valves with partial stroke testing ensure that plant emergency shutdown valves will always perform when needed. Advanced intelligent on/off and modulating controllers ensure high positioning accuracy and fast responses. Modern valve selection and sizing programs can ensure the best valve performance and process control.
Neles NDX™ valve controller.
Open FDT/DTM based technologies allow seamless interfacing between the controllers and device management and condition monitoring systems. Valve performance trend data is collected and easily analyzed, facilitating predictive maintenance and reduced unscheduled downtime.
Comprehensive device diagnostics.
Like all other industries, the chemical industry is also in a race to achieve net zero emission targets set out at the last COP26 summit. Energy optimization, the use of alternative forms of energy and decarbonization are under active pursuit and will offer new opportunities and challenges to valve manufacturers in the coming years.
This article has been originally published in VALVE Magazine Summer 2022. Link to the original article.
Authors and Valmet experts
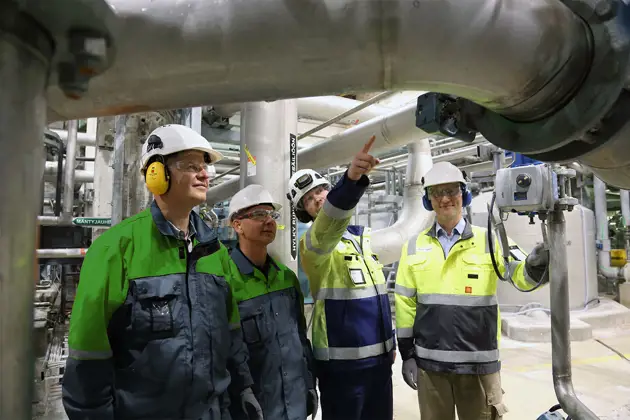
Subscribe to our newsletter
Subscribe now to flow control newsletter and receive the latest insights directly to your email.
Subscribe