Power Plant Efficiency: How to increase your revenues and save the World
What if I told you that it's possible to increase your CHP plant efficiency above 100 % and generate more than 20 % extra district heating power with the same fuel and reduce CO2 plus other emissions at the same time?
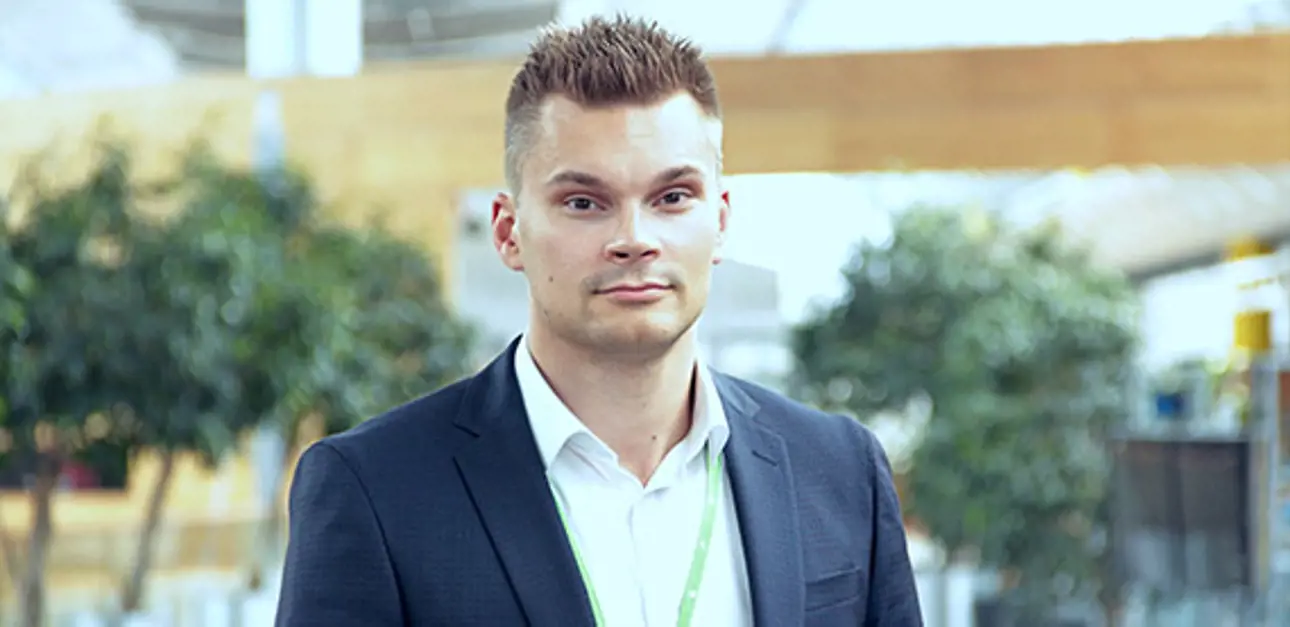
Everyone working in the energy sector has noticed the demise of electricity prices going on for a decade. In similar fashion, wind and solar power have been disruptive for conventional CHP plants complicating the operation of these plants. At the same time, the European Commission has tighten the emission limits forcing the power plants to invest.
District Heating In Europe, plenty of untapped potential
However, despite the challenges that power plant operators face today, there is plenty of untapped potential. Europe has 4400 district heating networks and more than 70 000 km on heating pipe in nearly 4000 cities enabling efficient heat production.
Source: Hamlstad & Aalborg Universities, NUTS Data
Increasing CHP plant efficiency
Flue gas contains plenty of heat (mainly latent heat) especially when the fuel moisture content is high. After combustion, fuel moisture is in vapor form in the flue gas with high enthalpy (kJ/kg). In normal combustion process this energy is not utilized and all that energy goes literally up in the smoke.
Let's look at the power plant heat balance and efficiency figure below.
Typically, the efficiency for CHP plant has been close to 90 %. The overall power plant efficiency is calculated by adjusting the calculation, i.e. the energy lost in flue gas moisture is not taken into consideration. Although it's a bit deceiving, since the fuel moisture has very significant effect, this efficiency calculation method has become the norm in energy industry.
The feasibility of flue gas condensing comes to life, when we calculate the efficiency with condensing flue gas scrubber or tube condenser. We get a 110 % efficiency that leaves some of us thinking whether we're generating energy out of thin air, but the defiance of thermodynamics is due to usage of lower heating value in the calculation.
Almost last drop of energy from the flue gas is released when the water vapor condensates into liquid form. Condensation occurs as the flue gas reaches the water dew point temperature, where the relative humidity is 100%. The higher the moisture content (the higher the dew point temperature) and the lower the district heating water return temperature, the greater the heat recovery. By adding combustion air humidifier into the mix with the condenser we can achieve even greater heat recovery. The flue gas temperature leaving the stack may even be reduced to 35 °C, which is roughly 100°C less heat lost into the air than in conventional process.
Flue gas condenser, the only flue gas cleaning method with a payback time
Now, let's discuss about the money-side of the matter. With CHP plant example above with 24.7 MW of heat recovery to district heating network we can plot the chart presented below.
The district heating demand fluctuates with the need for heating, i.e. the weather. Meaning that you cannot utilize the maximum potential the whole year. Thus, I have highlighted the most probable profit lines with green. However, if the district heating return temperature remains nearly constant the whole year, it might be possible to operate with of the two highest profit lines.
The figures presented are gross profit per year, but the overall operation costs are quite modest. Flue gas scrubber that is design for optimized emission reduction consumes around 160kW of electricity. If tube condenser is used for optimal heat recovery, then the consumption is around 30kW. The NaOH (sodium hydroxide) used to reduce emissions is economical reagent for this type of plants and the overall cost is marginal.
The matter of district heating prices is heavily depended on the power plant itself and district heating network it's supplying the heat to. The calculation can be done by either using cost of fuel (generating savings) or by using selling price (generating revenues). For example, in Finland, the price of biomass in power generation has been around 20€/MWh.
With using conservative estimate of 20€/MWh as district heating savings and 4000h operating hours, we achieve savings of roughly 2.5 million EUR per year or with 3000h operating hours more 2 million EUR. As said the outcome is plant depended and you should choose the unit values that have the fit for your plant.
Similarly, if you operate a smaller boiler, for example 100 MW. You can assume 20 MW heat recovery (20% of fuel power) and multiple the result according with (20/24.7).
Flue gas scrubber, saving the World by reducing emissions
Now that we have discussed the untapped potential in Europe and all ways interesting economics of flue gas condensing, we can move onto the Saving The World - part. By increasing CHP plant efficiency, you have already reduced your CO2 emissions and carbon footprint. However, with flue gas scrubber or tube condenser it's possible to reduce also other emissions.
The emission reduction with flue gas scrubber is extremely efficient and near zero level emissions are achievable. The SO2, HCl and NH3 removal rates are near 100 % reduction and for dust the reduction ranges between 50-90 % depending on the fuel and incoming dust. Even NOx can be reduced by oxidizing the nitrogen oxides to washable elements before the scrubber.
With every 1 MWh of heat recovery you gain approximately 1 m3/h condensate ready to be utilized in your operation. If you're using municipal water as raw water in you demineralized boiler water production, it's possible to generate savings and reduce water consumption, by using condensate instead. Depending on the cost of the raw water in your processes, this alone can generate saving and reduce your water footprint.
Typically reducing emission has always meant increasing costs. However, in today's low electricity price environment, generating district heating with flue gas condensing can help to improve your profits and reduce emission.
Save money, while saving the World
Lari-Matti Kuvaja
References:
stat, iea, heatroadmap.eu
![]() |
Lari-Matti Kuvaja works as a Product Sales Manager for Valmet's flue gas cleaning products. He has a Master of Science (Eng) degree in Energy Technology, Industrial Management from the Tampere University of Technology and a Master of Science (Economics and Business Administration) degree in Strategic Finance and Business Analytics from the Lappeenranta University of Technology. |
Related articles